With the continuous development of 3D printing technology, the market share of 3D printing powder metal materials also continues to be high.
This article mainly introduces the latest progress of aerosolization technology, the current process of preparing metal powder for 3D printing, and analyzes the current status of 3D printing metal powder preparation technology.
The current status of 3D printing metal powder preparation technology
3D printing technology is a new type of printing technology, its outstanding advantage is that without mechanical processing or any mold, it can directly generate any shape of parts from computer graphics data, thus greatly reducing the product development cycle, improving productivity and reducing production costs.
3D printing metal powder as the most important raw material for 3D printing of metal parts, its preparation method has attracted a lot of attention, 3D printing Metal powder as the most important part of the metal parts 3D printing industry chain, but also the greatest value.
The world’s leading experts in the 3D printing industry have a clear definition of 3D printing metal powder, which refers to a group of metal particles with a size of less than 1mm. This includes single metal powder, alloy powder and certain refractory compound powder with metallic properties.
At present, 3D printing metal powder materials include cobalt-chromium alloy, stainless steel, industrial steel, bronze alloy, titanium alloy and nickel-aluminum alloy. However, in addition to good plasticity, 3D printed metal powders must also meet the requirements of fine particle size, narrow particle size distribution, high sphericity, good flowability and high bulk density.
Making Process of Metal Powder
At present, the powder preparation method according to the preparation process can be divided into: reduction method, electrolysis method, carbonyl decomposition method, grinding method, atomization method, etc.
Among them, it is more common to use the powder produced by reduction, electrolysis and atomization methods as raw materials for the powder metallurgy industry. However, electrolytic and reduction methods are limited to the production of single metal powders, while for alloy powders these methods are not applicable.
The latest progress of aerosolization technology
The atomization method can be used for the production of alloy powders, and the modern atomization process can also control the shape of the powder, and the evolving atomization chamber structure has significantly improved the atomization efficiency, which makes the atomization method gradually developed into the main powder production method.
Atomization method meets the special requirements of 3D printing consumables metal powder. Atomization method refers to the mechanical method to crush the molten metal into particles of size less than about 150μm.
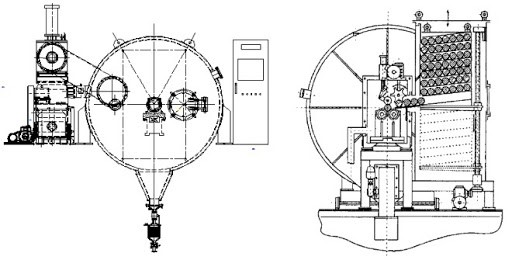
Aerosolization is one of the main methods of producing metal and alloy powders. The basic principle of aerosolization is the process of breaking the liquid metal stream into small droplets and solidifying them into powder by high speed airflow. Due to the advantages of high purity, low oxygen content, controllable powder size, low production cost and high sphericity, it has become the main development direction of high performance and special alloy powder preparation technology. However, the gas atomization method also has shortcomings.
The energy of high-pressure air flow is much smaller than that of high-pressure water flow, so the braking efficiency of gas atomization on metal melt is lower than that of water atomization, which makes the atomization efficiency of gas atomized powder lower, thus increasing the preparation cost of atomized powder.