Overview of 4140 Equivalent Powder
If you’re delving into the world of metallurgy and manufacturing, you’ve likely come across the term “4140 equivalent powder.” But what exactly is it, and why is it so significant? To put it simply, 4140 equivalent powder is a type of alloy steel powder that mimics the properties of AISI 4140 steel—a versatile, chromium-molybdenum alloy steel. This powder is widely used in various industries due to its excellent mechanical properties, including high strength, good toughness, and wear resistance.
Why Does 4140 Equivalent Powder Matter?
When it comes to manufacturing components that demand high-performance characteristics, the choice of material is crucial. 4140 equivalent powder provides the flexibility and reliability needed for producing high-quality parts, particularly in automotive, aerospace, and heavy machinery applications. Its ability to be used in powder metallurgy processes makes it an indispensable resource for industries that rely on precision and durability.
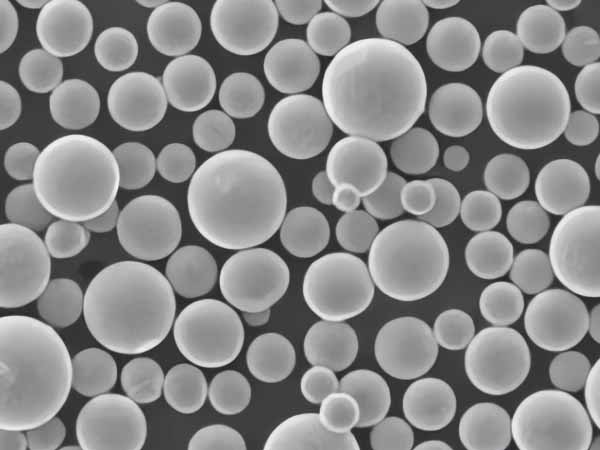
Composition of 4140 Equivalent Powder
Understanding the composition of 4140 equivalent powder is essential for grasping its properties and applications. The primary elements include chromium, molybdenum, carbon, and manganese. However, the exact composition may vary slightly depending on the specific powder model.
Key Elements in 4140 Equivalent Powder
Element | Percentage (%) | Role in Alloy |
---|---|---|
Carbon | 0.38-0.43 | Provides hardness and strength |
Chromium | 0.80-1.10 | Enhances corrosion resistance and hardness |
Molybdenum | 0.15-0.25 | Increases toughness and wear resistance |
Manganese | 0.75-1.00 | Improves hardenability and strength |
Silicon | 0.15-0.30 | Enhances strength and elasticity |
Phosphorus | ≤ 0.035 | (Minimal) Affects machinability negatively |
Sulfur | ≤ 0.040 | Improves machinability |
These elements combine to create a material that’s robust, durable, and capable of withstanding harsh conditions, making 4140 equivalent powder a versatile choice for many engineering applications.
Characteristics of 4140 Equivalent Powder
The characteristics of 4140 equivalent powder make it a standout material in the world of alloy steels. These characteristics not only determine its suitability for various applications but also its performance under different conditions.
Notable Characteristics
- High Strength: One of the most prominent features of 4140 equivalent powder is its impressive tensile and yield strength, making it suitable for components that need to bear heavy loads.
- Good Toughness: The material’s toughness ensures that it can absorb energy and resist fracture, which is crucial in dynamic or impact-heavy environments.
- Wear Resistance: Thanks to its composition, 4140 equivalent powder offers excellent wear resistance, making it ideal for parts subjected to friction and wear.
- Corrosion Resistance: Although not as high as stainless steels, the chromium content provides decent corrosion resistance, which is sufficient for many industrial applications.
- Heat Treatability: The alloy can be heat treated to achieve various hardness levels, allowing for customization based on the specific application needs.
Comparing Characteristics: 4140 Powder vs. 4340 Powder
Property | 4140 Equivalent Powder | 4340 Powder |
---|---|---|
Strength | High | Slightly higher |
Toughness | Good | Superior |
Wear Resistance | Excellent | Excellent |
Corrosion Resistance | Moderate | Slightly better due to higher chromium |
Heat Treatability | High | Higher |
Applications | Automotive, aerospace | Aerospace, heavy machinery |
Advantages of 4140 Equivalent Powder
When choosing a material for manufacturing, it’s crucial to weigh the pros and cons. Let’s dive into the advantages of using 4140 equivalent powder.
Why Choose 4140 Equivalent Powder?
- Versatility: 4140 equivalent powder is used across a wide range of industries, from automotive to aerospace, because it offers a balanced combination of strength, toughness, and wear resistance.
- Customization: This powder can be heat treated and alloyed in various ways to meet specific performance requirements, offering flexibility to engineers and manufacturers.
- Cost-Effectiveness: Compared to some high-end alloys, 4140 equivalent powder provides a cost-effective solution without compromising on performance, making it a popular choice for budget-conscious projects.
- Availability: 4140 equivalent powder is widely available from numerous suppliers, ensuring that it can be sourced with relative ease, which is a significant advantage for industries operating on tight timelines.
Comparing Costs: 4140 Equivalent Powder vs. Other Alloys
Alloy | Cost | Performance |
---|---|---|
4140 Equivalent Powder | Moderate | High |
4340 Powder | Higher | Superior toughness |
Stainless Steel Powders | High | Excellent corrosion resistance |
Titanium Powders | Very High | Exceptional strength-to-weight |
Applications of 4140 Equivalent Powder
4140 equivalent powder finds its way into various industries due to its excellent mechanical properties. Here, we’ll explore some of the most common applications.
Where Is 4140 Equivalent Powder Used?
Industry | Application | Benefits of 4140 Equivalent Powder |
---|---|---|
Automotive | Gears, shafts, and axles | High strength, wear resistance |
Aerospace | Landing gear components | Good toughness, high fatigue resistance |
Heavy Machinery | Drill bits, cutting tools | Excellent hardenability, durability |
Oil & Gas | Valves, fittings, couplings | Corrosion resistance, high pressure tolerance |
Tool & Die | Molds, punches | High hardness, machinability |
Power Generation | Turbine components, fasteners | Heat resistance, fatigue strength |
Construction Equipment | Hydraulic cylinders, crane components | Toughness, load-bearing capacity |
Defense | Armored vehicles, weapon components | High impact resistance, durability |
Specific 4140 Equivalent Powder Models
There are several models of 4140 equivalent powder, each designed for specific applications or manufacturing processes. Below is a detailed look at ten popular models and their unique features.
Detailed Descriptions of 4140 Equivalent Powder Models
- Powder Model A: Designed for additive manufacturing, this model offers high precision and excellent surface finish, making it ideal for producing complex geometries in the aerospace industry.
- Powder Model B: Known for its exceptional wear resistance, this model is widely used in the production of gears and other automotive components that require high durability.
- Powder Model C: This model is optimized for cold forging applications, offering a combination of high ductility and strength, perfect for the production of fasteners and fittings.
- Powder Model D: Engineered for high-performance cutting tools, this powder provides excellent hardness and edge retention, making it a go-to choice for the tool and die industry.
- Powder Model E: With a focus on corrosion resistance, this powder is commonly used in the oil and gas industry for components exposed to harsh environments.
- Powder Model F: This model is tailored for powder metallurgy, offering a fine particle size that ensures uniformity and high density in sintered parts.
- Powder Model G: A general-purpose 4140 equivalent powder, this model is versatile and cost-effective, making it suitable for a wide range of applications including machinery and construction equipment.
- Powder Model H: Designed for high-temperature applications, this powder maintains its mechanical properties even at elevated temperatures, ideal for power generation and turbine components.
- Powder Model I: This model offers improved machinability, reducing tool wear and increasing productivity in manufacturing processes where precision and speed are critical.
- Powder Model J: Specifically developed for defense applications, this powder provides superior impact resistance and durability, essential for military-grade components.
Specifications and Standards for 4140 Equivalent Powder
To ensure consistency and reliability, 4140 equivalent powders must meet specific industry standards and specifications. Here, we’ll outline the key specifications and standards that these powders adhere to.
Specifications and Standards Overview
Specification | Description | Common Standards |
---|---|---|
Particle Size | The size of powder particles, typically measured in microns | ASTM B214, ISO 4497 |
Composition | The elemental makeup of the powder | ASTM A829, ISO 3755 |
Mechanical Properties | Strength, hardness, and toughness parameters | ASTM E8/E8M, ISO 6892 |
Sintering Temperature | Temperature range for sintering processes | ASTM B925, ISO 13099 |
Density | Powder density, both bulk and tap | ASTM B527, ISO 3923-1 |
Flow Rate | The flowability of the powder | ASTM B213, ISO 4490 |
Purity | Levels of impurities like phosphorus and sulfur | ASTM E1019, ISO 10714 |
Certification | Compliance with industry regulations and certifications | AMS 2301, MIL-STD-3021 |
Suppliers and Pricing Details for 4140 Equivalent Powder
Finding the right supplier for 4140 equivalent powder is crucial, especially when balancing quality and cost. Below, we’ll provide details on several prominent suppliers and the associated pricing.
Comparing Suppliers and Pricing
Supplier | Region | Product Range | Pricing | Lead Time |
---|---|---|---|---|
Supplier A | North America | Full range of 4140 powders | $$ – $$$ | 2-4 weeks |
Supplier B | Europe | Specialty powders for aerospace | $$$ – $$$$ | 4-6 weeks |
Supplier C | Asia | Economical options, large volumes | $ – $$ | 6-8 weeks |
Supplier D | Global | Custom powders, technical support | $$ – $$$ | 3-5 weeks |
Supplier E | North America | High-purity powders, certified | $$$ | 4-6 weeks |
Pros and Cons of 4140 Equivalent Powder
Like any material, 4140 equivalent powder comes with its own set of advantages and limitations. Let’s break down the pros and cons to help you decide if this material is right for your needs.
Advantages
- High Strength and Toughness: Ideal for heavy-duty applications where durability is critical.
- Versatile Applications: Can be used across various industries, from automotive to aerospace.
- Customizable Properties: Easily tailored through heat treatment and alloying.
- Cost-Effective: Offers a good balance of performance and price compared to other alloys.
Disadvantages
- Moderate Corrosion Resistance: Not suitable for environments with extreme corrosion risks.
- Requires Heat Treatment: To achieve the desired properties, heat treatment is often necessary, which adds to processing time and cost.
- Not the Best for All Applications: In some cases, other materials like stainless steel or titanium may be a better choice.
Pros and Cons Compared to Other Alloys
Feature | 4140 Equivalent Powder | 4340 Powder | Stainless Steel Powder | Titanium Powder |
---|---|---|---|---|
Strength | High | Very High | Moderate | Very High |
Toughness | Good | Excellent | Moderate | High |
Corrosion Resistance | Moderate | Moderate | Excellent | Excellent |
Cost | Moderate | Higher | High | Very High |
Heat Treatability | High | Very High | Limited | Limited |
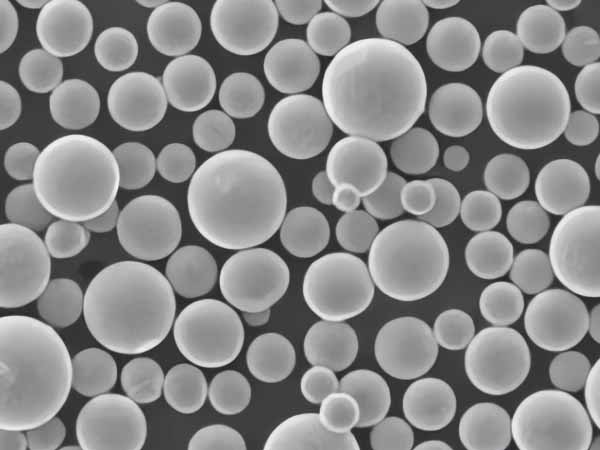
FAQ
Let’s address some common questions that often arise when discussing 4140 equivalent powder.
Question | Answer |
---|---|
What is 4140 equivalent powder used for? | It is used in the production of high-strength, wear-resistant components in industries such as automotive, aerospace, and heavy machinery. |
How does 4140 powder compare to 4340 powder? | 4340 powder offers slightly better toughness and fatigue resistance, but at a higher cost. Both are suitable for demanding applications. |
Can 4140 equivalent powder be heat treated? | Yes, heat treatment is commonly used to enhance its mechanical properties such as hardness and strength. |
Is 4140 equivalent powder corrosion resistant? | While it offers moderate corrosion resistance, it is not as resistant as stainless steel powders. |
What are the alternatives to 4140 equivalent powder? | Alternatives include 4340 powder, stainless steel powders, and titanium powders, depending on the specific application requirements. |
Where can I buy 4140 equivalent powder? | It can be purchased from various suppliers globally, with options ranging from standard grades to custom formulations. |
What standards must 4140 equivalent powder comply with? | It must comply with industry standards such as ASTM B214, ISO 3755, and AMS 2301, among others. |
Is 4140 equivalent powder suitable for 3D printing? | Yes, certain models are specifically designed for additive manufacturing, offering precision and a good surface finish. |
What is the cost of 4140 equivalent powder? | The cost varies depending on the supplier, quality, and specific requirements, but generally falls in the moderate range. |
Can 4140 equivalent powder be customized? | Yes, it can be alloyed or heat treated to meet specific performance needs, offering great flexibility for different applications. |
Conclusion
Choosing the right material for your manufacturing needs can be challenging, but 4140 equivalent powder offers a compelling mix of strength, toughness, wear resistance, and versatility. Whether you’re working in automotive, aerospace, or heavy machinery, this powder provides the reliability and performance that modern industries demand. By understanding its composition, characteristics, and applications, you can make an informed decision that ensures the success of your project.
So, the next time you’re in the market for a high-performance alloy, consider the many benefits that 4140 equivalent powder has to offer.