Introduction
Definition of Metal Powder
Metal powder is a crucial component in the field of 3D printing, particularly in the production of metal parts. It refers to finely ground particles of metal that are used as the raw material for additive manufacturing processes. The quality and characteristics of the metal powder play a significant role in determining the final properties and performance of the printed metal parts. The use of metal powder in 3D printing allows for the creation of complex and intricate designs that would be difficult or impossible to achieve using traditional manufacturing methods. As the field of 3D printing continues to advance, the future of metal powder holds great potential for revolutionizing various industries, including aerospace, automotive, and healthcare.
Overview of 3D Printing
3D printing, also known as additive manufacturing, is a revolutionary technology that has transformed various industries. It allows for the creation of three-dimensional objects by layering materials on top of each other, based on a digital design. The process starts with a 3D model, which is then sliced into thin layers. These layers are then printed one by one, gradually building up the final object. 3D printing has gained significant popularity due to its ability to produce complex shapes and structures that traditional manufacturing methods cannot achieve. It offers numerous advantages such as reduced waste, faster production times, and the ability to customize products. As the technology continues to advance, the future of 3D printing looks promising, especially in the field of metal powder. Metal powder is increasingly being used in 3D printing to create strong and durable metal parts, with applications ranging from aerospace to healthcare. With ongoing research and development, the use of metal powder in 3D printing is expected to grow, opening up new possibilities and revolutionizing the manufacturing industry.
Importance of Metal Powder in 3D Printing
The importance of metal powder in 3D printing cannot be overstated. Metal powder serves as the raw material for creating complex and intricate metal objects through additive manufacturing. It is the foundation upon which the entire 3D printing process relies. Without high-quality metal powder, the final printed objects may lack the desired strength, durability, and precision. Metal powder allows for the production of customized and lightweight metal parts, making it a crucial component in various industries such as aerospace, automotive, and healthcare. As 3D printing technology continues to advance, the demand for high-quality metal powder will only grow, paving the way for innovative and groundbreaking applications in the future.
Advancements in Metal Powder
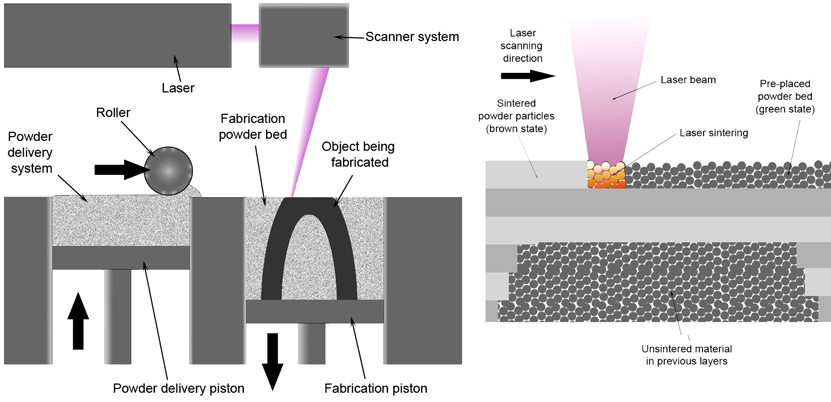
Improved Powder Quality
Improved powder quality plays a crucial role in the future of metal powder in 3D printing. As the demand for high-quality 3D printed metal parts continues to grow, manufacturers are focusing on enhancing the quality of the powders used in the printing process. Higher quality powders result in improved print accuracy, reduced defects, and enhanced mechanical properties of the final products. This not only ensures better performance but also opens up new possibilities for complex and intricate designs that were previously unachievable. With advancements in powder production techniques and rigorous quality control measures, the future of metal powder in 3D printing looks promising and holds immense potential for revolutionizing various industries.
Enhanced Powder Properties
Enhanced Powder Properties play a crucial role in the future of metal powder in 3D printing. As the demand for high-quality and complex metal parts continues to grow, the need for powders with enhanced properties becomes paramount. These enhanced powder properties include improved flowability, particle size distribution, and chemical composition control. By optimizing these properties, manufacturers can achieve better printability, higher part density, and improved mechanical properties in the final 3D-printed metal components. Furthermore, enhanced powder properties enable the production of intricate geometries and intricate designs, pushing the boundaries of what is possible in metal 3D printing. With ongoing research and development, the future holds great promise for further advancements in enhancing powder properties, opening up new opportunities for innovation and application in various industries.
New Metal Powder Alloys
Metal powder alloys are constantly evolving in the field of 3D printing, paving the way for exciting advancements in the industry. With each passing year, researchers and engineers are discovering new combinations of metals that offer improved properties and performance. These new alloys are revolutionizing the capabilities of 3D printed metal objects, allowing for greater strength, durability, and precision. From titanium-based alloys to aluminum alloys, the possibilities are endless. As the demand for high-quality metal 3D printed parts continues to grow, so does the need for innovative metal powder alloys. The future of metal powder in 3D printing is bright, as it holds the promise of unlocking new possibilities in manufacturing and design.
Applications of Metal Powder in 3D Printing
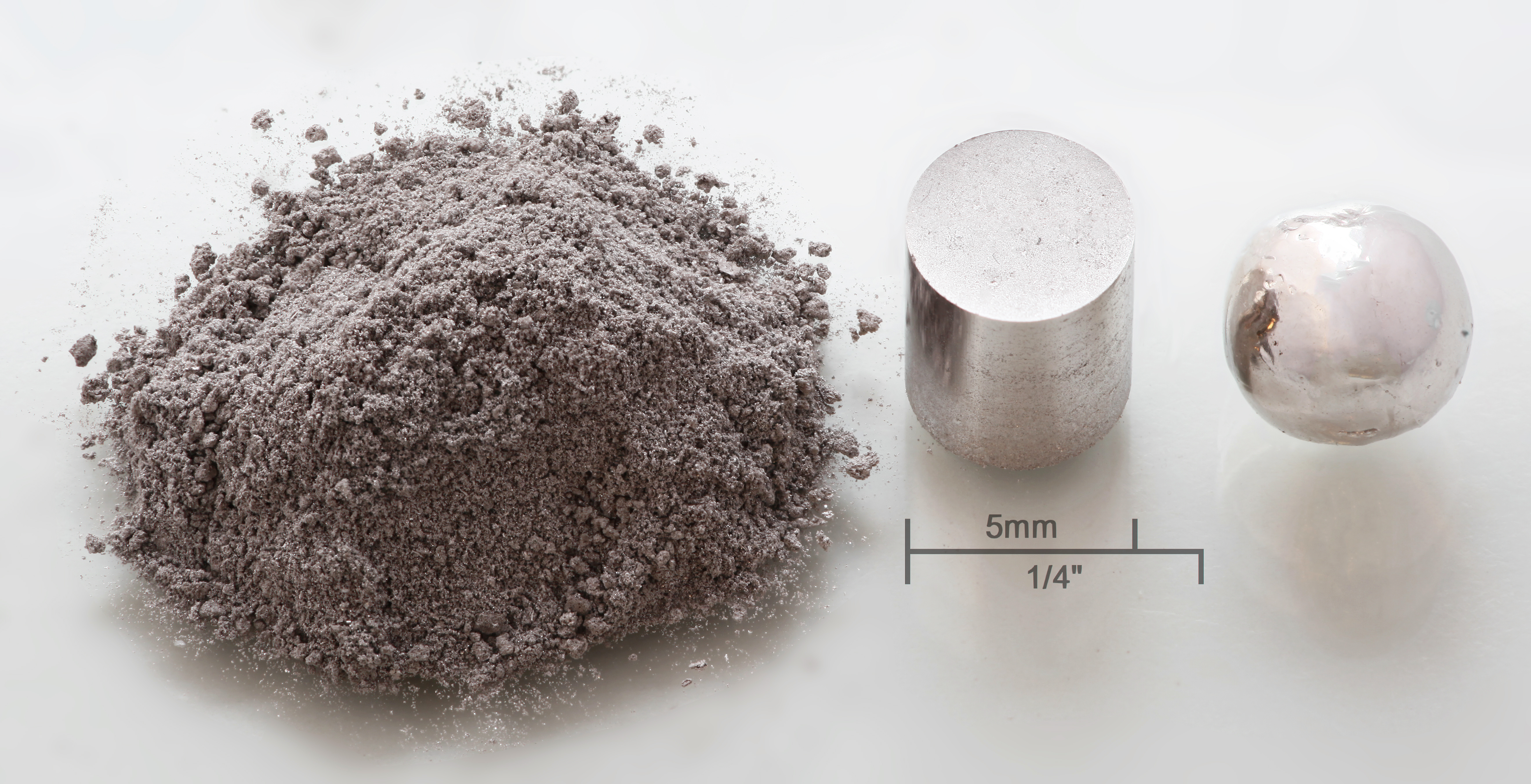
Aerospace Industry
The aerospace industry has been one of the key adopters of metal powder in 3D printing technology. With its ability to produce complex geometries and lightweight structures, metal powder 3D printing has revolutionized the manufacturing process in aerospace. From engine components to aircraft parts, this innovative technology has enabled faster production, reduced costs, and improved performance. As the demand for more efficient and sustainable aircraft continues to grow, the aerospace industry will increasingly rely on metal powder 3D printing to meet these challenges and push the boundaries of what is possible in aircraft design and production.
Medical Field
In the medical field, the use of metal powder in 3D printing has the potential to revolutionize healthcare. With the ability to create intricate and customized medical implants, such as prosthetics and dental implants, 3D printing offers a new level of precision and personalization. This technology allows for the production of implants that perfectly fit the unique anatomy of each patient, resulting in improved functionality and comfort. Additionally, metal powder 3D printing enables the creation of complex internal structures, such as porous implants, which can promote better integration with surrounding tissues and enhance the healing process. As the technology continues to advance, we can expect to see even more innovative applications in the medical field, ultimately improving patient outcomes and transforming the way healthcare is delivered.
Automotive Sector
The automotive sector is one of the key industries that can greatly benefit from the use of metal powder in 3D printing. With the advancements in additive manufacturing technology, automotive manufacturers are able to produce complex and lightweight components that were previously impossible to manufacture using traditional methods. Metal powder 3D printing allows for the creation of parts with intricate designs and precise geometries, resulting in improved performance and fuel efficiency. Additionally, the use of metal powder in 3D printing enables the production of customized parts on-demand, reducing the need for inventory and storage space. As the automotive industry continues to embrace additive manufacturing, the future of metal powder in 3D printing looks promising, with the potential to revolutionize the way vehicles are designed, manufactured, and maintained.
Challenges and Limitations
Powder Contamination
Powder contamination is a critical issue in the world of 3D printing. As metal powders are used as the raw material for printing, any impurities or foreign particles can have a significant impact on the quality and integrity of the final printed object. Contaminants such as dust, moisture, or even tiny metal fragments can lead to defects, reduced strength, and compromised structural integrity. Therefore, it is crucial to have strict quality control measures in place to minimize powder contamination and ensure the production of high-quality 3D printed metal objects.
High Cost of Metal Powder
The high cost of metal powder is one of the main challenges in the field of 3D printing. Metal powders used in 3D printing are often expensive due to the specialized manufacturing processes involved. The production of high-quality metal powders requires advanced technologies and precise control over various parameters. Additionally, the limited availability of certain metals further contributes to the high cost. As a result, the cost of metal powder can significantly impact the overall cost of 3D printed metal parts. However, ongoing research and development efforts are focused on finding cost-effective alternatives and optimizing the manufacturing processes to reduce the cost of metal powder in 3D printing.
Post-Processing Requirements
Post-processing requirements play a crucial role in the success of metal powder 3D printing. After the printing process, the metal parts often require additional steps to achieve the desired final properties. These post-processing steps can include heat treatment, surface finishing, and removal of support structures. Heat treatment is commonly used to improve the mechanical properties and remove residual stresses in the printed parts. Surface finishing processes such as polishing or sandblasting are necessary to enhance the aesthetic appeal and smoothness of the final product. Additionally, the removal of support structures is essential to ensure the dimensional accuracy and functionality of the printed metal parts. Overall, post-processing requirements are essential to optimize the performance and appearance of metal powder 3D printed objects.
Future Trends in Metal Powder 3D Printing
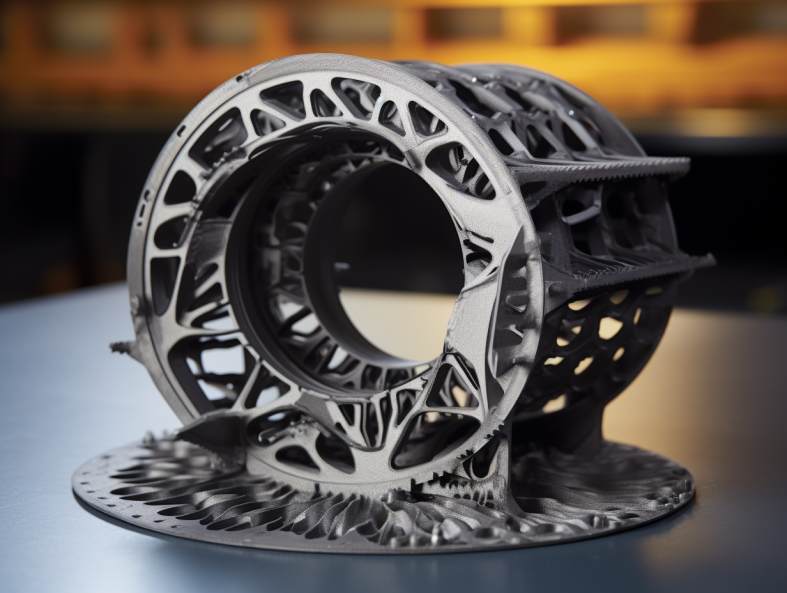
Increased Material Options
With the advancements in metal powder technology, 3D printing has opened up a whole new world of possibilities in terms of material options. Traditional manufacturing methods often limit the types of materials that can be used, but with metal powder 3D printing, a wide range of metals and alloys can be utilized. This means that manufacturers can now create complex and intricate designs using materials such as stainless steel, titanium, aluminum, and even precious metals like gold and silver. This increased material options not only enhances the versatility of 3D printing but also allows for the production of stronger and more durable parts. From aerospace components to medical implants, the future of metal powder in 3D printing is set to revolutionize various industries.
Improved Printing Speeds
Improved printing speeds are a key factor in the future of metal powder in 3D printing. As technology continues to advance, the ability to print metal objects at faster speeds opens up new possibilities for various industries. With improved printing speeds, manufacturers can increase production rates and reduce lead times, resulting in more efficient and cost-effective manufacturing processes. Additionally, faster printing speeds enable the creation of complex and intricate metal designs with precision and accuracy. This not only enhances the quality of the final products but also expands the range of applications for metal 3D printing. As a result, the future of metal powder in 3D printing looks promising, with improved printing speeds driving innovation and growth in the industry.
Integration of AI and Machine Learning
The integration of AI and machine learning has revolutionized various industries, and the field of metal powder in 3D printing is no exception. With the power of AI algorithms and machine learning models, manufacturers can now optimize the entire process of metal powder production, from material selection to powder bed preparation. AI algorithms can analyze vast amounts of data to identify the ideal combination of metal powders for specific applications, taking into account factors such as strength, durability, and cost-effectiveness. Machine learning models can then predict the optimal parameters for the 3D printing process, ensuring high-quality and precise metal parts. This integration of AI and machine learning not only enhances the efficiency and accuracy of metal powder 3D printing but also opens up new possibilities for innovation and customization in the manufacturing industry.
Conclusion
Summary of Key Points
The future of metal powder in 3D printing is promising and holds great potential for various industries. Metal powder is a crucial component in additive manufacturing, enabling the creation of complex and intricate designs with high strength and durability. One of the key points to consider is the continuous advancements in metal powder technology, leading to improved print quality, reduced costs, and increased material options. Additionally, the ability to customize metal powders for specific applications opens up new possibilities in the fields of aerospace, automotive, healthcare, and more. As the demand for metal 3D printing continues to grow, the future of metal powder in this industry looks bright.
Potential Impact on Industries
The potential impact of metal powder in 3D printing on industries is immense. With the advancements in additive manufacturing technology, metal powder has become a game-changer in various sectors. One of the key areas where it has the potential to revolutionize is the manufacturing industry. Metal powder allows for the production of complex and intricate designs that were previously impossible with traditional manufacturing methods. This opens up new possibilities for creating lightweight and high-performance parts, leading to improved efficiency and cost-effectiveness. Additionally, the use of metal powder in 3D printing has the potential to disrupt the supply chain by reducing the need for raw materials and minimizing waste. This not only has environmental benefits but also offers significant cost savings. Overall, the integration of metal powder in 3D printing has the potential to transform industries by enabling faster, more efficient, and sustainable manufacturing processes.
Future Outlook
The future outlook for metal powder in 3D printing is promising. As the technology continues to advance, metal powders are becoming more refined and specialized, allowing for greater precision and quality in printed metal objects. Additionally, the demand for 3D printed metal products is expected to grow significantly in industries such as aerospace, automotive, and healthcare. This increased demand will drive the development of new metal powders with enhanced properties, such as improved strength, durability, and heat resistance. As a result, the future of metal powder in 3D printing looks bright, with endless possibilities for innovation and advancement.