Overview
AlSi12 powder is an aluminum alloy powder containing approximately 12% silicon. It is commonly used as a powder feedstock in additive manufacturing processes like selective laser melting (SLM) and electron beam melting (EBM) to produce metal parts.
Some key properties and characteristics of AlSi12 powder:
- Aluminum alloy with 11-13% silicon content
- Flowable spherical powder ideal for powder bed fusion
- High fluidity allows smooth powder spreading
- Good thermal conductivity
- Low coefficient of thermal expansion
- High build rates and low porosity in printed parts
- Excellent corrosion resistance
- High strength-to-weight ratio
- Widely used in aerospace, automotive and industrial applications
AlSi12 Powder Types
Type | Description | Characteristics |
---|---|---|
Gas atomized | Made by inert gas atomization process | Spherical shape, good flowability, optimized particle size distribution |
Plasma atomized | Made by plasma atomization process | More spherical, smoother surface, better flowability than gas atomized |
Recycled | Reused powder from prior prints | Irregular shapes, satellite particles, contamination |
Blended | Mixture of virgin and reused powder | Controlled particle size distribution |
AlSi12 Powder Characteristics
Parameter | Typical Value |
---|---|
Silicon content | 11-13 wt% |
Particle shape | Spherical |
Particle size | 15-45 μm |
Apparent density | 1.8-2.5 g/cc |
Tap density | 2.2-3.0 g/cc |
Flowability | Excellent |
Residual oxygen content | <0.2 wt% |
Residual nitrogen content | <0.04 wt% |
AlSi12 Powder Applications
Industry | Uses |
---|---|
Aerospace | Engine components, structural parts, brackets |
Automotive | Pistons, connecting rods, turbochargers |
Industrial | Heat exchangers, tooling, fixtures |
Medical | Orthopedic implants, prosthetics |
Defense | Lightweight armor, conduits |
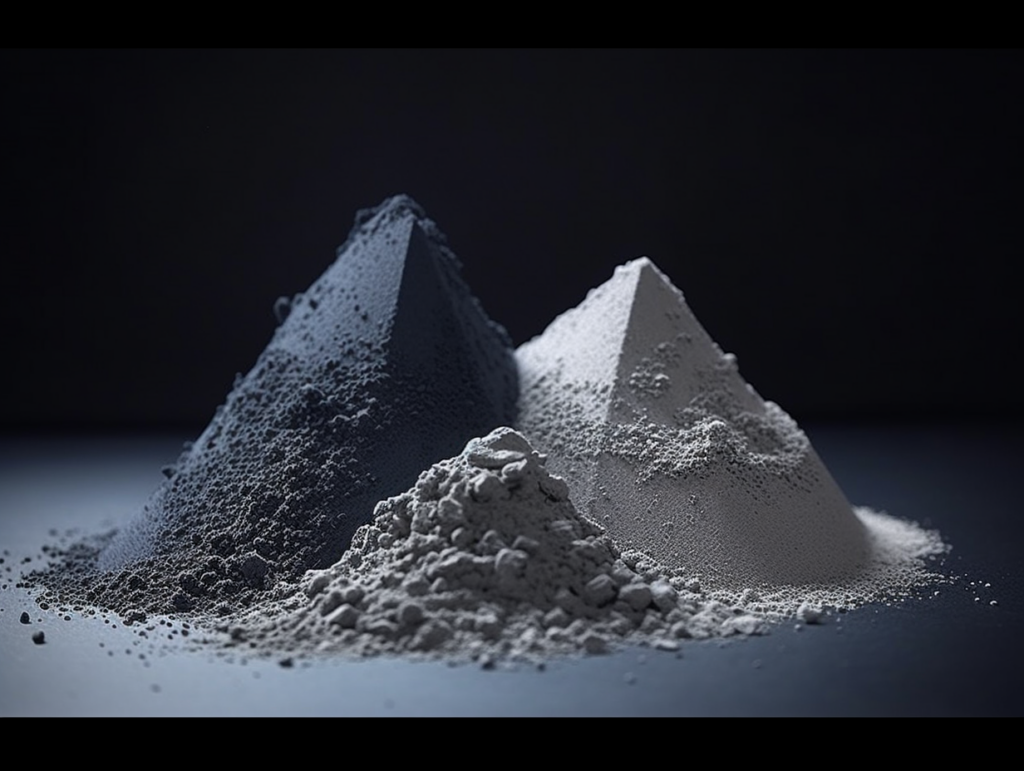
How to Choose AlSi12 Powder
Several factors need to be considered when selecting AlSi12 powder for additive manufacturing:
Powder Type
- Virgin gas atomized and plasma atomized powders provide optimal properties
- Recycled and blended powders are more economical
- Plasma atomized powder is preferred for critical applications requiring superior properties
Particle Size Range
- A typical range is 15-45 μm
- Size distribution affects packing density, porosity, surface finish
- Finer particles below 10 μm can cause dust issues
- Coarser particles above 45 μm reduce resolution
Apparent Density
- Higher density above 2.0 g/cc improves powder bed density
- Lower density below 1.5 g/cc causes powder spreading issues
Flow Characteristics
- Flow rates of 18-23 s/50 g preferred using Hall flowmeter
- Lower flowability can interrupt uniform powder spreading
Composition
- Aluminum content over 85 wt%
- Silicon 11-13 wt% for precipitation hardening
- Low oxygen and nitrogen content critical for mechanical properties
Manufacturer Reputation
- Source powder from established, reputable manufacturers
- Ensure strict quality control and consistency between batches
Where to Buy AlSi12 Powder
AlSi12 powder can be purchased from the following major suppliers:
Powder Manufacturers
Company | Description |
---|---|
AP&C | Leading producer of titanium, aluminum and nickel alloys |
Carpenter Additive | Offers gas atomized AlSi12 powder |
ECKA Granules | Global metal powders supplier based in Germany |
Erasteel | Producer of spherical gas atomized AlSi12 |
LPW Technology | Supplies customized aluminum alloy powders |
Praxair | Gas and plasma atomization, wide alloy offerings |
Sandvik Osprey | Global powder supplier, including AlSi12 |
Powder Distributors
Company | Location |
---|---|
3DXtech | Grand Rapids, MI, USA |
Advanced Powders & Coatings | Quebec, Canada |
CNPC Powder Group | Shanghai, China |
Höganäs | Sweden |
LPW Technology | Cheshire, UK |
Material Technology Innovations | Singapore |
Sigma Aldrich | Global locations |
AlSi12 Powder Pricing
Powder Type | Price Range |
---|---|
Virgin gas atomized | $60-100 per kg |
Virgin plasma atomized | $80-150 per kg |
Recycled | $30-60 per kg |
Blended | $40-80 per kg |
Pricing varies based on order volume, location, manufacturer, and purchase through distributors or directly. Plasma atomized powder commands higher prices over gas atomized.
How to Install and Operate AlSi12 Powder Feedstock
Using AlSi12 powder feedstock for additive manufacturing requires proper storage, handling, loading, and sieving:
Powder Storage
- Store unopened containers in a dry, cool environment
- Avoid temperature swings and moisture which can cause caking
- Limit exposure to oxygen by using a sealed container
- Use original packaging or inert gas purged containers
Powder Handling
- Wear nitrile gloves to prevent skin contact and contamination
- Pour powder slowly to minimize dust generation
- Use antistatic tools and vacuum aspiration for spills
Machine Loading
- Level the powder bed and spread evenly using the recoater mechanism
- Adjust the spreader speed, blade gap, and powder layer thickness
- Ensure uniform deposition for consistent melt pools
Powder Sieving
- Sieve powder between prints to break up agglomerates
- Use mesh size around 40 μm for effective sieving
- Collect sieved powder separately from unsieved quantities
Environment Control
- Maintain ambient temperatures 15-25°C and humidity 20-50%
- Use inert gas purge systems to prevent oxidation
- Install pollution control and venting systems
Safety Equipment
- Use appropriate respirators, dust masks, and protective clothing
- Powder quantities over 2 lbs may require grounded equipment
- Follow all safety handling procedures from OSHA and SDS
AlSi12 Printing Parameters
Optimized print parameters are critical for high quality AlSi12 parts:
Laser Powder Bed Fusion Parameters
Parameter | Typical Value |
---|---|
Layer thickness | 20-50 μm |
Hatch spacing | 100-150 μm |
Scan speed | 700-1100 mm/s |
Laser power | 190-350 W |
Beam diameter | 50-100 μm |
Powder bed temp | 100-220°C |
Electron Beam Melting Parameters
Parameter | Typical Value |
---|---|
Layer thickness | 50-100 μm |
Line offset | >50 μm |
Scan speed | 1000-3000 mm/s |
Beam power | 3-7 kW |
Beam size | 100-300 μm |
Powder bed temp | 650-1100°C |
Key Printing Guidelines
- Maintain consistent temperature across the powder bed
- Use higher temperatures for better powder sintering
- Adjust parameters to avoid balling, porosity, cracking
- Optimize scan patterns and support structures
- Scale parameters based on part size and geometry
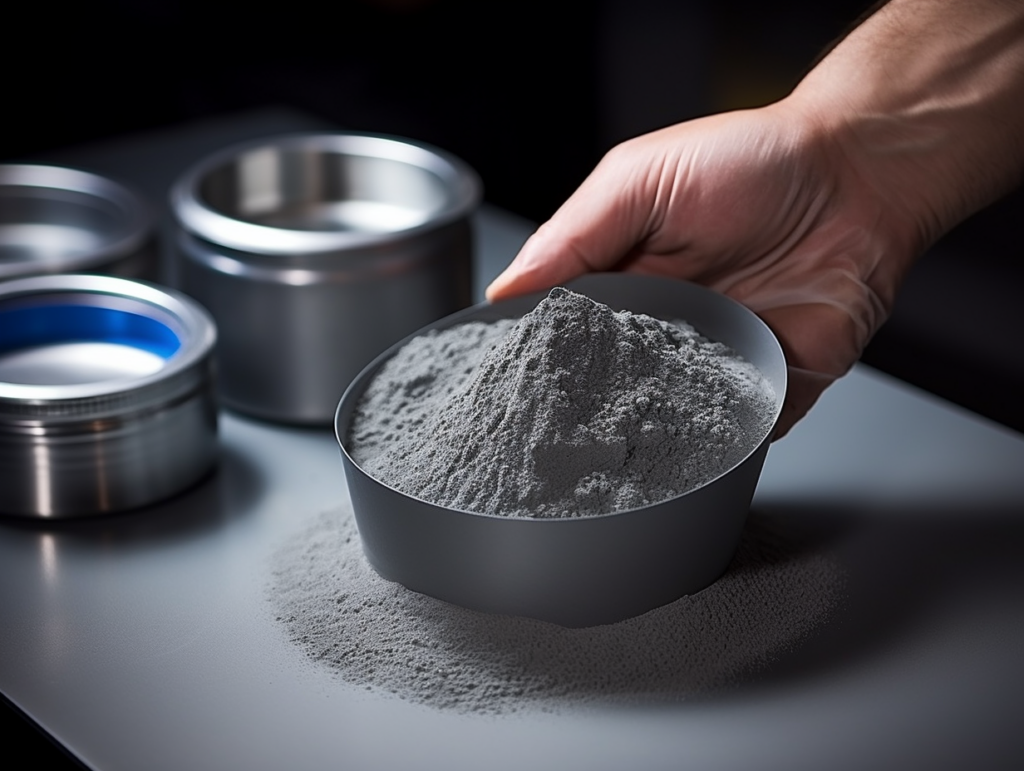
AlSi12 Post Processing
Common post processing methods for AlSi12 printed parts include:
- Powder removal – Use brushing, compressed air, or vibration to remove loose powder
- Stress relieving – Heat treatment at 300°C for 2 hours to relieve residual stresses
- Hot isostatic pressing – Apply high temperature and pressure to close internal voids and porosity
- Surface machining – CNC milling, turning, drilling to improve surface finish and tolerances
- Lapping and polishing – Smoothen surfaces using abrasives and polishing compounds
- Plating – Apply metallic coatings like nickel or copper to enhance aesthetics and conductivity
- Painting and coating – Use dye penetrants, primers, paints for color and corrosion protection
Proper post processing is essential for improving the functional performance of additively manufactured AlSi12 components. The methods used depend on the application requirements, cost, lead time, and properties desired.
AlSi12 Material Properties
AlSi12 demonstrates the following mechanical, physical and chemical properties:
Mechanical Properties
Property | As-printed | Wrought AlSi12 |
---|---|---|
Density | 2.66-2.72 g/cc | 2.66-2.68 g/cc |
Hardness | 110-150 HB | 85-105 HB |
Tensile strength | 400-480 MPa | 220-300 MPa |
Yield strength | 250-350 MPa | 140-240 MPa |
Elongation at break | 1-5% | 8-10% |
Modulus of elasticity | 80-90 GPa | 72-77 GPa |
Physical Properties
Property | Typical Value |
---|---|
Melting point | ~600°C |
Thermal conductivity | 130-160 W/m-K |
Electrical resistivity | 4-8 μΩ-cm |
CTE | 20-23 x10<sup>-6</sup> °C<sup>-1</sup> |
Chemical Properties
- Excellent corrosion resistance in various environments
- Good chemical stability for industrial applications
- Prone to galvanic corrosion if contacted with dissimilar alloys
Applications of AlSi12 Parts
Key applications of additively manufactured AlSi12 components include:
Aerospace Applications
- Engine brackets, mounts, housings, ducts
- Structural frameworks, airframes, wings, fins
- Lightweight satellite and drone components
- Rotor blades, engine blades and impellers
Automotive Applications
- Turbocharger wheels and housings
- Pistons, brake discs, powertrain parts
- Lightweight chassis, transmission and drivetrain components
- Heat exchangers, oil tanks, pumps
Industrial Applications
- Press tools, jigs, fixtures, gauges
- Robotics, UAVs, drone parts
- Heat sinks, enclosures, hydraulic manifolds
- Customized grippers, levers, housings
With properties like high strength, lightweight, thermal conductivity and corrosion resistance, AlSi12 is suitable for robust functional components across automotive, aerospace, industrial, and consumer product sectors.
Pros and Cons of AlSi12 Powder
AlSi12 powder offers several benefits along with some limitations:
Advantages
- High strength-to-weight ratio
- Excellent thermal conductivity
- Good corrosion resistance
- High build rates and resolutions
- Near fully dense printed parts
- Cost effective compared to other aluminum alloys
- Recyclability of unused powder
Limitations
- Low ductility and elongation
- Difficulty fabricating large overhangs
- High residual stresses in as-printed condition
- Requires hot isostatic pressing for stress relieving
- Lower machinability than wrought AlSi12 alloy
- Limited availability of plasma atomized powder
Overall, AlSi12 provides a balanced material option for automotive, aerospace and industrial additive manufacturing applications needing high strength, lightweight and thermal performance.
How to Choose Between AlSi12 vs AlSi10Mg vs Scalmalloy®
AlSi12, AlSi10Mg and Scalmalloy® are popular aluminum alloys for laser powder bed fusion. Here is a comparison between their properties and applications:
Parameter | AlSi12 | AlSi10Mg | Scalmalloy® |
---|---|---|---|
Composition | Al-11-13Si | Al-9-11Si | Al-6.2Mg-0.5Sc-0.4Zr |
Key features | High strength, thermal conductivity | Excellent strength and ductility | Highest strength, hardness |
Density | 2.7 g/cc | 2.7 g/cc | 2.67 g/cc |
Tensile strength | 400-480 MPa | 450-500 MPa | 500-520 MPa |
Elongation | 1-5% | 7-10% | 10-13% |
Application fit | High temperature functional parts | Ductile structural components | Aerospace fittings, brackets |
AlSi12 is preferred for high temperature stability and thermal conductivity. It works for industrial tooling, aerospace engine parts, automotive components.
AlSi10Mg provides the best all-round properties. It is suitable for lightweight structural parts across aviation, defense and automotive sectors.
Scalmalloy® is chosen where maximum strength and hardness is needed. It is ideal for thin-wall brackets, aviation fittings, components needing high yield strength.
Maintaining AlSi12 Powder Feedstock
To ensure optimal performance from AlSi12 powder:
- Store sealed powder containers properly in cool, dry areas to prevent contamination. Keep away from temperature fluctuations.
- Monitor the powder for changes in flowability, density or composition over time. Test older powders before use.
- Sieve powder with 40-63 μm mesh periodically to break up agglomerates. Discard extremely fine particles below 10 μm.
- Mix small ratios of new powder to replenish reused older powder after 5-10 reuse cycles.
- Do not top off existing powder quantities in machine hoppers. Use fresh pre-sieved batches for consistent spreading.
- Consider use of humidity control, inert gas gloveboxes and sealed containers to minimize oxidation during storage and handling.
- Follow all safety procedures listed in the safety data sheet. Use appropriate PPE during handling and machine loading.
Proper maintenance ensures AlSi12 powder remains free-flowing and buildable, leading to higher quality printed components with expected material properties.
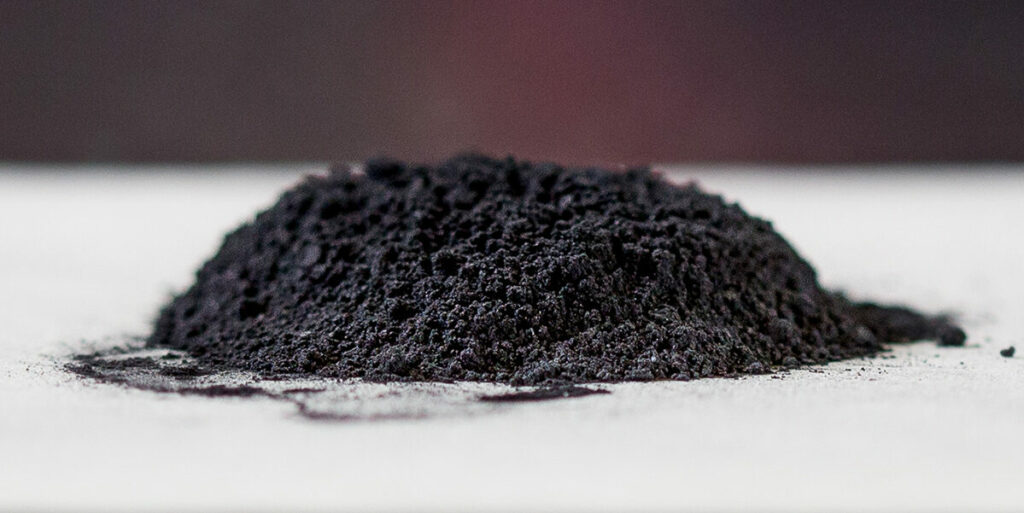
FAQs
What is AlSi12 powder used for?
AlSi12 is commonly used to additively manufacture high-strength, thermally conductive parts for aerospace, automotive and industrial applications like engine components, brackets, turbomachinery, and heat exchangers.
Does AlSi12 powder require heat treatment?
In the as-printed state, AlSi12 components have high residual stresses. Heat treatment like stress relieving at 300°C for 2 hours or hot isostatic pressing helps reduce internal stresses and improve ductility.
How is AlSi12 powder made?
AlSi12 is produced using inert gas atomization or plasma atomization to generate spherical powder suitable for additive manufacturing. The powder particles solidify rapidly from molten material with the desired alloy composition.
Is AlSi12 stronger than aluminum?
Yes, AlSi12 is significantly stronger than pure aluminum alloys due to precipitation hardening from the silicon content. AlSi12 powder has an ultimate tensile strength of 400-480 MPa versus just 90-200 MPa for aluminum.
What is the density of AlSi12?
The density of AlSi12 powder ranges from 2.66-2.72 g/cc in the as-printed condition. This is over 20% lower density than steel allowing lighter weight components to be built.
Can you weld AlSi12?
Yes, AlSi12 can be welded using processes like metal inert gas (MIG) welding and tungsten inert gas (TIG) welding. Welding AlSi12 requires controlled heat input to minimize hot cracking and joint weaknesses.
What is the strongest aluminum alloy?
Among cast aluminum alloys, A206 has the highest strength with a tensile strength over 500 MPa. For wrought alloys, 7075 aluminum is the strongest with over 570 MPa tensile strength. For additive manufacturing, Scalmalloy® offers over 520 MPa strength.
Is AlSi12 corrosion resistant?
AlSi12 demonstrates excellent corrosion resistance due to the passive oxide layer forming on its surface. It provides good corrosion protection in various environments and applications without needing protective coatings.
What is the difference between AlSi10Mg and AlSi12?
The key difference is their silicon content. AlSi10Mg has 9-11% Si whereas AlSi12 contains 11-13% Si. The higher silicon provides better wear resistance and tensile strength in AlSi12 powder.