Titanium and aluminum TA7 powder is an advanced composite material with applications across aerospace, automotive, and other industries. This guide provides a detailed overview of TA7 powder metallurgy, manufacturing, properties, applications, and considerations for optimal utilization.
Overview of Titanium And Aluminum TA7 Powder
Titanium and aluminum TA7 powder consists of a homogeneous blend of titanium and aluminum particles that can be consolidated into lightweight high-strength components.
Key properties:
- Lightweight yet strong
- Heat treatable
- Excellent corrosion resistance
- High thermal stability
- Low density
TA7 powder offers an excellent balance of strength, ductility, and low density. Here is a quick reference table summarizing key details:
Parameter | Details |
---|---|
Composition | 60-70% Ti, 30-40% Al |
Density | 3.7-4.1 g/cc |
Particle Size | 15-45 microns |
Melting Point | >1000°C |
Strength | Up to 1000 MPa |
Key Properties | Lightweight, strong, heat treatable |
Main Applications | Aerospace, automotive, marine |
With its versatile properties, TA7 powder is enabling lighter and stronger parts across demanding applications.
Manufacturing Process
TA7 powder is manufactured through the following steps:
Blending – Titanium and aluminum powders are blended in the right proportions to achieve homogenous mixing.
Milling – The powder blend is mechanically milled to break up agglomerates and evenly distribute the metals.
Annealing – The milled powder is annealed to relieve stresses induced during milling.
Screening – Final powder is screened to obtain the desired particle size distribution.
QC Testing – Rigorous quality control testing validates powder characteristics meet specifications.
Proper processing controls during powder manufacture ensure optimal quality and performance in the final application.
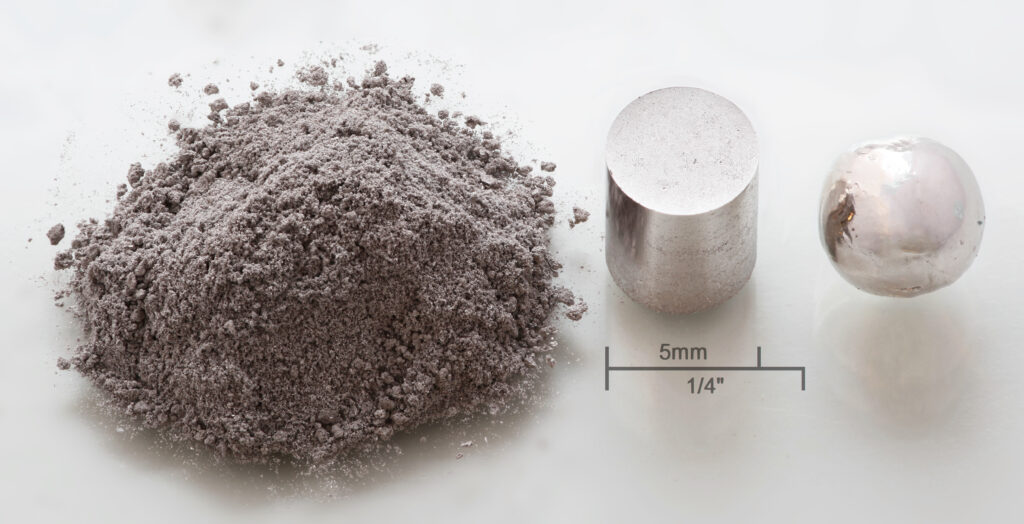
Properties of TA7 Powder
The outstanding properties of TA7 powder stem from the synergistic effects between titanium and aluminum:
Lightweight – 20-40% lower density than titanium alloys. Enables weight savings.
Strength – Heat treated strength up to 1000 MPa, higher than aluminum alloys.
Stiffness – Excellent specific stiffness close to titanium alloys.
Hardness – Heat treatable to high hardness levels up to 450 HV.
Thermal Stability – Maintains strength up to 300°C. Higher than aluminum alloys.
Corrosion Resistance – Resists corrosion in harsh environments.
Wear Resistance – Good erosion and abrasion resistance.
Manufacturability – Easy to process using powder metallurgy techniques.
The balanced properties of TA7 make it suitable for structural and dynamic applications needing lightweight strength.
Applications of TA7 Powder
Key application areas of TA7 powder include:
Aerospace
- Structural airframe components
- Jet engine parts
- Airframe fasteners
- Rotor hubs
Automotive
- Valve train components
- Pistons
- Gears
- Drive shafts
Industrial
- Robotics components
- Turbine blades
- Pump housings
- Mine screens
Biomedical
- Orthopedic implants
- Dental implants
- Surgical tools
TA7 allows creating lighter and efficient components for performance-critical applications across sectors.
Global Suppliers
Some of the major global suppliers of TA7 powder include:
Company | Location |
---|---|
GKN Sinter Metals | Germany, USA |
Rio Tinto Metal Powders | Canada |
AMETEK Specialty Metal Products | USA |
CNPC Powder Group | China |
TLS Technik | Germany |
These companies can provide custom-engineered TA7 powder suited for particular component requirements in terms of composition, particle size, shape, and powder characteristics.
Cost Analysis
TA7 powder is more expensive than standalone titanium or aluminum powders. Cost depends on:
- Purity levels
- Particle size distribution
- Purchase quantity
- Supplier
Some typical price ranges:
Powder Grade | Price Range |
---|---|
Research/Lab Quantities | $200-500/kg |
Industrial Quantities | $100-200/kg |
Contact suppliers directly for exact price quotes based on your specific powder requirements. Buying in bulk quantities can help lower costs.
Processing TA7 Powder into Components
TA7 powder can be processed into end-use components using:
Additive Manufacturing – Selective laser melting, electron beam melting to build complex 3D shapes.
Metal Injection Molding – Mixing powder with binders, molding, and sintering. Enables complex geometries and net-shape capability.
Press and Sinter – Compacting powder and sintering to full density. Lower costs but shape limitations.
Hot Isostatic Pressing – Consolidating encapsulated powder under heat and pressure. Eliminates porosity.
Process | Benefits | Limitations |
---|---|---|
Additive Manufacturing | Design freedom, customization | Size limits, higher cost |
Metal Injection Molding | Net-shape, automation | Multi-step process |
Press and Sinter | Lower equipment costs | Shape constraints |
Hot Isostatic Pressing | Fully dense parts | Requires encapsulation |
The process selection depends on part shape, size, quantity, properties, and cost targets.
Post-Processing
Common post-processing steps include:
- Heat Treatment – Solution treatment, aging to enhance strength and ductility through precipitation hardening.
- Machining – Finish machining to meet dimensional tolerances and surface finish requirements.
- Surface Treatment – Anodizing, powder coating for corrosion protection, wear resistance, aesthetics.
- Joining – Welding, mechanical fastening to assemble components.
- Testing – Mechanical testing, non-destructive evaluation to ensure component meets design specifications.
Proper post-processing is key to realizing the full performance potential of TA7 parts.
Installation and Maintenance
To ensure optimal performance from TA7 parts:
- Follow manufacturer’s installation guidelines for proper fitment and load bearing.
- Conduct scheduled inspections and testing to identify potential defects early.
- Check for signs of corrosion and early fatigue damage.
- Replace worn or damaged components before failure.
- Service with compatible lubricants to prevent wear and galling.
- Maintain proper clearance between moving parts.
- Keep within designed operating parameters like temperature, load, rpm etc.
- Protect against chemical exposure that can degrade properties.
Proactive maintenance combined with good installation practices help maximize the working life of components.
Choosing a TA7 Powder Supplier
Here are key considerations when selecting a TA7 powder supplier:
- Experience handling titanium and aluminum powder blends
- Technical expertise in manufacturing customized powders
- Quality certifications (ISO, AS9100 etc.)
- R&D capabilities for process innovation
- Customer focus with responsive technical support
- Material characterization testing capabilities
- Logistics infrastructure for timely delivery
- Pricing competitiveness
- Willingness to partner on application development
Choosing an established supplier with strong technical experience ensures a consistent supply of high-quality TA7 powder tailored to the application.
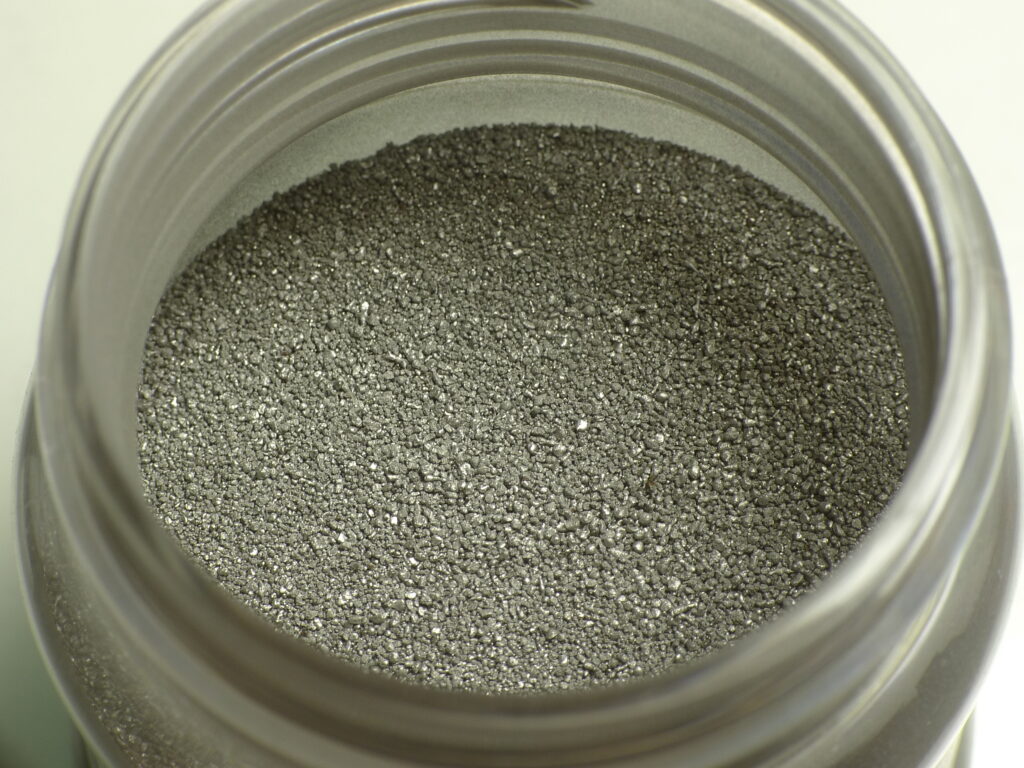
Pros and Cons of TA7 Powder
Pros
- Lightweight alternative to steels and titanium alloys
- Heat treatable to high strength levels
- Outstanding specific stiffness
- Excellent corrosion resistance
- Good wear resistance
- Fabricatable into net shape components
Cons
- More expensive than aluminum or titanium alone
- Not weldable using conventional fusion welding
- Subject to galvanic corrosion if copper or graphite are present
- Requires controlled atmosphere processing and heat treatment
For applications where lightweight structural performance is critical, TA7 provides significant benefits.
FAQs
Q: What is TA7 powder used for?
A: TA7 is used mainly in aerospace and automotive components like airframes, valves, pistons, gears, shafts requiring high strength along with low density.
Q: Is TA7 powder flammable?
A: Yes, titanium and aluminum powders are flammable. TA7 powder requires cautious handling and inert gas storage to prevent fire risks.
Q: What is the difference between TA7 and TA11 titanium aluminum powder?
A: TA11 has 11% aluminum while TA7 has 30-40% aluminum resulting in higher strength levels. TA11 offers better ductility.
Q: Does TA7 powder require special sintering equipment?
A: Yes, vacuum or inert gas sintering is essential to prevent oxidation issues during consolidation to full density.
Q: What are typical applications of hot isostatic pressing of TA7 parts?
A: HIP is commonly used to eliminate internal porosity in critical components like aerospace turbine blades and medical implants.
Conclusion
With its excellent strength-to-weight ratio and fabricability, TA7 powder enables lighter and efficient component designs across performance-intensive applications. Continued powder quality refinements and processing innovations will further expand the utilization of TA7 as a versatile advanced material across industries.