Overview
FeCoNiCrAl powder, also known as High Entropy Alloy (HEA) powder, refers to a new class of advanced metallic materials that contain multiple principal elements in equimolar or near-equimolar ratios. Unlike traditional alloys that are based on one major element, HEAs utilize 4 or more elements in substantial quantities to produce alloys with superior properties compared to conventional alloys.
Some key properties of FeCoNiCrAl powder include:
- Excellent strength-to-weight ratio
- Enhanced corrosion and oxidation resistance
- High hardness and wear resistance
- High thermal stability
- Good machinability
- Tunable magnetic properties
With its unique cocktail of properties, FeCoNiCrAl has shown promising performance for applications such as tooling, biomedical implants, aerospace components, coatings, and more. This guide provides a comprehensive overview of FeCoNiCrAl powder, its manufacturing methods, properties, applications, and suppliers.
Types of FeCoNiCrAl Powder
FeCoNiCrAl powder can be categorized into the following main types depending on composition and processing technique:
Type | Composition | Characteristics |
---|---|---|
Equiatomic | 25at.% of each element | Excellent strength, ductility, toughness |
Off-equiatomic | Varying ratios of elements | Tunable properties by adjusting ratios |
Pre-alloyed | Alloyed using casting/melting | Uniform composition, stable properties |
Mechanically alloyed | Alloyed by ball milling | Fine microstructure, metastable phases |
The equiatomic composition with 25% of each element Fe, Co, Ni, Cr, and Al is considered the baseline HEA composition. However, tuning the ratios of the different elements allows properties like strength, corrosion resistance, magnetism etc. to be adjusted as per application requirements.
Pre-alloyed powders are fabricated using conventional melting and casting processes to homogenize the alloy composition before atomizing into powder form. Mechanically alloyed powders are produced by high-energy ball milling of elemental or pre-alloyed powders to obtain metastable nanostructures.
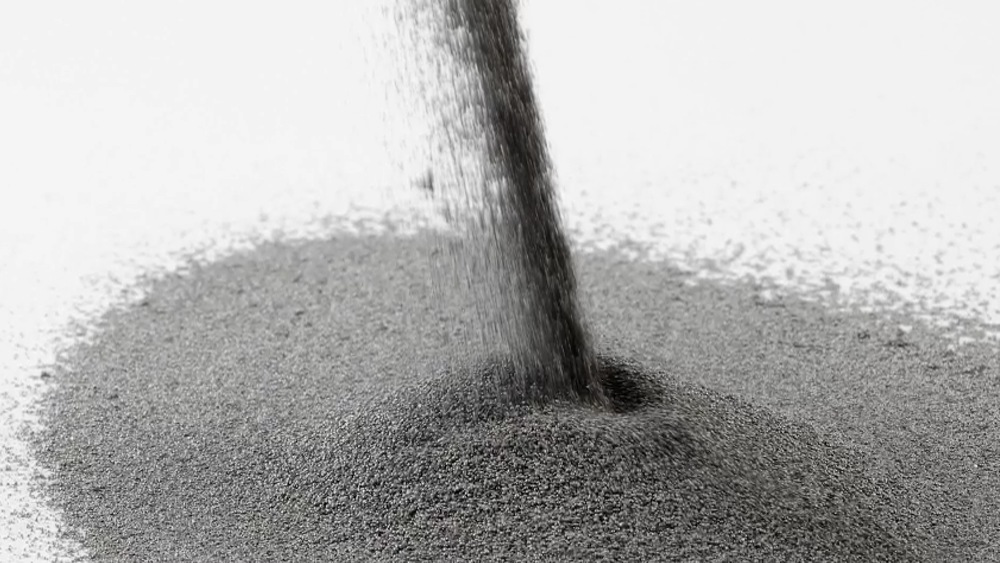
Characteristics and Properties
Some of the notable characteristics and properties of FeCoNiCrAl powder include:
High strength
- Yield strength > 500 MPa
- Tensile strength > 700 MPa
- Originates from lattice distortion effect and dislocation strengthening
Good ductility and toughness
- Elongation > 15%
- Absorbed energy up to 30 J
- Averts brittle failure
Excellent corrosion resistance
- Better passivation behavior than 304 stainless steel
- Resists pitting and crevice corrosion
- High resistance to acids, bases, and salts
Oxidation resistance
- Forms protective Al2O3 oxide layer
- Retains strength in oxidizing environments up to 700°C
High hardness
- Vickers hardness around 200-450 HV
- Grinding, machining capable
Thermal stability
- Service temperature from -196 to 700°C
- Slow coarsening rate up to 0.5Tm
Tunable magnetic properties
- Controlled with Fe, Co, Ni ratios
- Ferromagnetic to paramagnetic range
Applications of FeCoNiCrAl Powder
The excellent combination of strength, ductility, and environmental resistance makes FeCoNiCrAl suitable for the following applications:
Cutting tools and dies
- Replacements for WC-Co tools
- improved wear resistance and toughness
Biomedical implants
- Joint replacements, fixation devices
- Biocompatible, non-toxic alloy
Aerospace and automotive
- Engine components, landing gear
- Withstand high temperatures and stresses
Corrosion resistant coatings
- Protection for pipelines, vessels, tanks
- Replaces stainless steel, Ni alloys
Permanent magnets
- Energy-related applications
- Alternative to rare earth magnets
High-entropy alloys
- Alloying element for other HEAs
- Imparts strength and environmental resistance
3D printing
- Direct metal laser sintering
- Creates complex, dense parts
Manufacturing Processes
FeCoNiCrAl powder can be produced via the following methods:
Gas atomization
- Melts alloy and atomizes with inert gas
- Yields fine spherical powder 10 – 150 μm
- Compositionally uniform, high purity
Water atomization
- Melts alloy and sprays into water
- Irregular powder shapes 2 – 300 μm
- Higher oxygen pick-up
Plasma rotating electrode process (PREP)
- Centrifugal disintegration of molten metal
- Powder size 5 – 25 μm
- Lower oxygen content
Mechanical alloying
- High energy ball milling
- Elemental/pre-alloyed blended powders
- Particle size 10 – 50 μm
- Meta-stable nanostructures
Gas atomization and PREP are preferred for pre-alloyed powder production to minimize oxygen contamination. Mechanical alloying creates composite and nanostructured powders suitable for consolidation into bulk alloys.
Specifications
Typical specifications for FeCoNiCrAl powder are:
Parameter | Specification |
---|---|
Alloy composition | Equiatomic or off-equiatomic ratios |
Particle shape | Spherical, irregular, composite |
Particle size | 10 – 150 μm |
Oxygen content | < 300 ppm |
Carbon content | < 100 ppm |
Apparent density | 2 – 4 g/cc |
Tap density | 4 – 6 g/cc |
Flow rate | 15 – 25 s/50g |
Specific surface area | 0.05 – 0.5 m2/g |
Composition is application-specific. Smaller powder sizes (<20 μm) are preferred for additive manufacturing. Lower oxygen and carbon contents improve alloy properties. Good powder flow aids in die filling and spreading during AM.
Design and Standards
Key design factors and relevant standards for FeCoNiCrAl powder include:
Alloy ratios: Adjusted to meet required properties like strength, corrosion resistance, magnetism etc.
Powder characteristics: Particle size distribution, morphology, purity etc. tailored based on production method.
Consolidation method: Depends on application – metal injection molding, HIP, welding, or AM processes.
Microstructure control: Solution annealing, aging, and thermo-mechanical processing used to tailor grain size, precipitates, phases.
ASTM B939: Standard specification for pre-alloyed powder for HEAs. Defines allowable limits for composition, particle size distribution, impurity levels etc.
ASTM E1405: Guide for discussing HEA material properties using a minimum dataset. Promotes consistency in reporting data.
ASTM E3159: Standard terminology for HEA compositions, processing, microstructures, properties, and performance. Provides definitions of key HEA terms.
Following standard specifications and characterization frameworks ensures quality control and enables data comparisons across different HEA studies.
Suppliers and Pricing
Some of the major suppliers offering FeCoNiCrAl powder include:
Supplier | Location | Price Range |
---|---|---|
Sandvik | Sweden | $100 – $500/kg |
Praxair | USA | $80 – $450/kg |
Hoganas | Sweden | $150 – $600/kg |
CNPC Powder | China | $50 – $250/kg |
Metal Powder Company | India | $70 – $350/kg |
Prices vary based on composition, production method, powder characteristics, order quantity and purity requirements. Small R&D quantities are relatively expensive while bulk orders for commercial use tend to cost much less per kg.
Installation, Storage and Handling
To ensure optimal performance from FeCoNiCrAl powder, proper installation, storage and handling procedures must be followed:
- Store in cool, dry environment away from moisture, heat, sparks or flames
- Use inert gas sealing or vacuum packing for long-term storage
- Limit exposure to air to prevent oxidation and contamination
- Handle powder gently to avoid segregation, attrition and contamination
- Install dust collection system and ground equipment to prevent dust explosions
- Wear PPE like respirators, gloves, eye protection when handling powder
- Follow local regulatory codes for combustible metal powder storage and handling
Proper installation of equipment like sieving stations, mixing vessels and dust collection systems creates a safe environment for workers to process the powders for different applications.
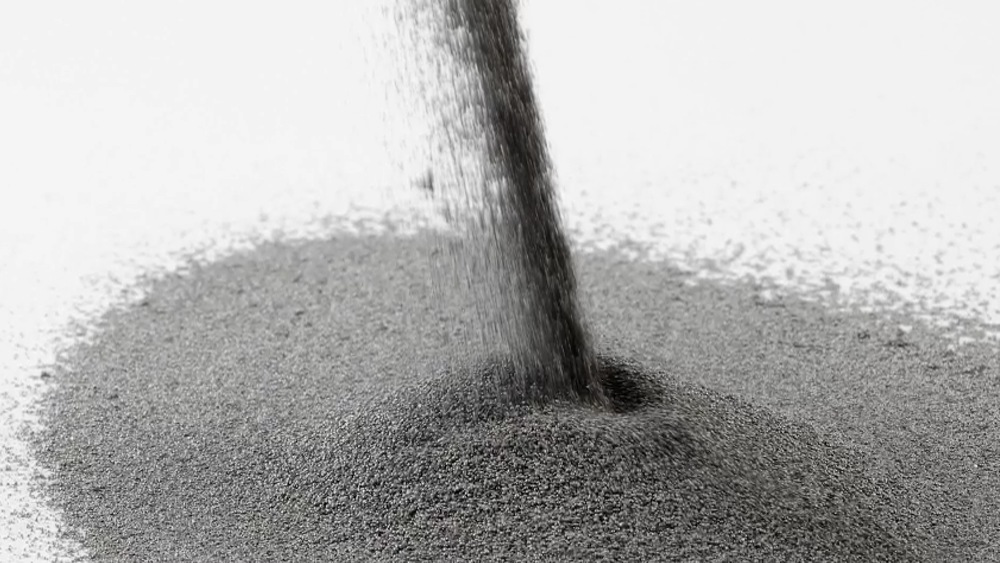
Operation and Maintenance
Key operation and maintenance practices for equipment handling FeCoNiCrAl powder:
Sieving:
- Clean sieves regularly to prevent mesh clogging
- Check sieve integrity before use
- Control amplitude and time to limit particle attrition
Mixing:
- Use intensifier bars for effective blending
- Do not overmix to limit powder oxidation
Hopper/feeder:
- Inspect wedge, wheel, and orifice for damage
- Remove powder buildup to ensure uniform flow
Cold compaction:
- Monitor press capacity and stopping position
- Use adequate lubricant for high density and low wear
- Periodic replacement of punches and dies
Sintering furnace:
- Control atmosphere to prevent oxidation
- Calibrate temperature uniformity
- Maintain insulation and heating elements
Safety:
- Ground all powder handling equipment
- Strictly control spark/flame sources
- Store powder properly in sealed containers
Proper maintenance optimizes equipment performance, achieves consistent powder flow and avoids contamination. This leads to higher quality finished HEA parts.
How to Select FeCoNiCrAl Powder Suppliers
When selecting a supplier for FeCoNiCrAl powder, buyers should consider the following:
Production capability
- Capacity to produce required alloy compositions
- Powder quantity and lead times
- Customization of size distribution, shape etc.
Quality systems
- ISO 9001 and ISO 13485 certification
- Stringent quality control standards
- Consistency in powder characteristics
Technical expertise
- Knowledge of HEA compositions and properties
- Capability to tailor alloys and processes
- Support for part design and manufacturing
Testing services
- Chemical analysis, particle size analysis
- Crystal structure, microstructure characterization
- Powder property evaluation
Reputation and references
- Good customer reviews and feedback
- Experience supplying to similar applications
Price and value
- Reasonable prices for capacity and quality
- Provision of sampling, small batches
- Flexible pricing for large orders
A capable supplier with a track record of quality and customer service ensures a smooth procurement experience and contributes to the success of the final application.
Pros and Cons of FeCoNiCrAl Powder
Advantages
- Excellent strength-to-weight ratio
- Better corrosion resistance than stainless steel
- High hardness and wear resistance
- Good thermal stability up to 700°C
- Tunable magnetic properties
- Biocompatible composition
- Works well for metal AM processes
Disadvantages
- Relatively more expensive than common alloys
- Processing can be challenging due to high alloying
- Limited data available compared to conventional materials
- Requires special storage/handling considerations
- Certain compositions may lack ductility
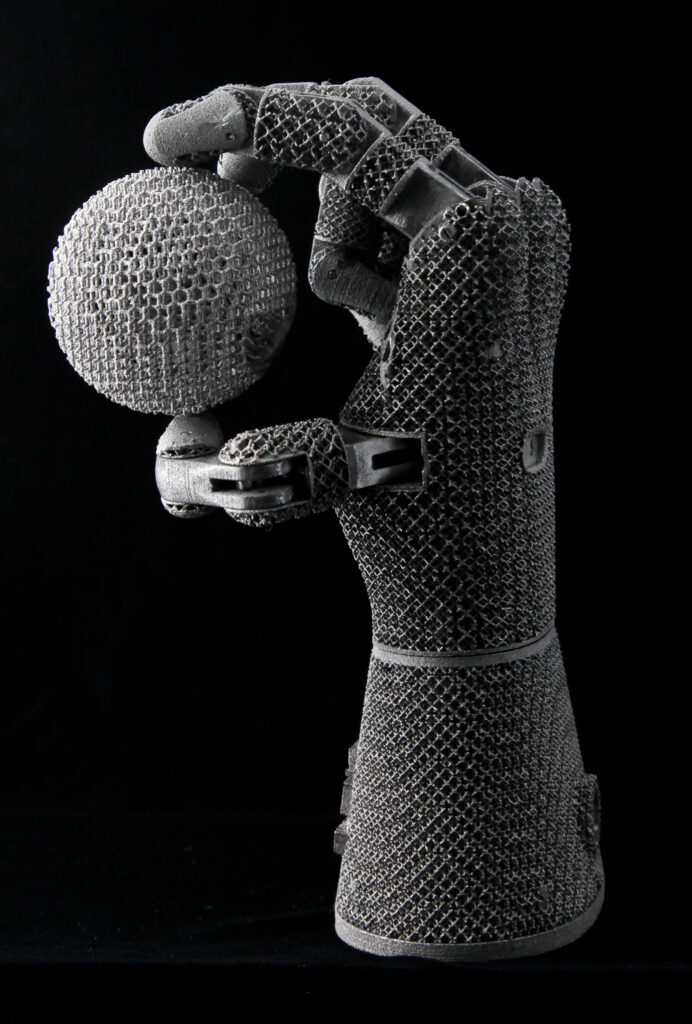
FAQs
What are the typical applications of FeCoNiCrAl alloy powder?
Some of the main application areas taking advantage of the properties of this high entropy alloy powder include cutting tools, biomedical implants, aerospace components, corrosion resistant coatings, permanent magnets, and metal additive manufacturing.
What particle size range is recommended for AM with FeCoNiCrAl?
For powder bed fusion AM processes like selective laser melting and electron beam melting, the ideal particle size range is 15-45 μm. Finer powders promote higher density while larger sizes Above 50 μm can negatively impact flow and spreading.
How is corrosion resistance of FeCoNiCrAl powder enhanced?
Corrosion resistance is improved by increasing the Al and Cr content in the alloy composition. The Al forms a protective oxide layer while the Cr provides passivation. Tuning the ratios to between 5-35% Al and 10-40% Cr results in excellent corrosion resistance.
What is the difference between gas atomized and water atomized FeCoNiCrAl powder?
Gas atomization yields finer spherical powder particles with lower oxygen pickup compared to water atomization. However, water atomized powder is cheaper though less ideal for critical applications. Gas atomized powder flows better and produces higher quality AM or sintered parts.
How should FeCoNiCrAl powder be stored for maximum shelf life?
Proper storage in a cool, dry, inert environment sealed from atmosphere prevents oxidation and contamination. Vacuum packaging or sealing under argon are recommended. Limit moisture to below 10 ppm and oxygen to under 100 ppm for stable long-term storage over months.
Conclusion
With its tantalizing mix of high strength, toughness, hardness, and environmental resistance, FeCoNiCrAl has emerged as a promising multi-principal element alloy system. Though relatively new, continued research and development efforts to explore composition-processing-property relationships can help tap the full potential of this high entropy alloy. Selection of the optimal powder composition, production method, characteristics, consolidation process and parameters is key to fabricating high-performance FeCoNiCrAl components cost-effectively.