FeCoNiCrTi powder, also known as high entropy alloy (HEA) powder, refers to a multi-principal element alloy powder containing iron, cobalt, nickel, chromium and titanium. This advanced material offers exceptional properties from the synergistic effects of its composite composition.
This guide provides a comprehensive overview of FeCoNiCrTi powder, including:
Introduction to FeCoNiCrTi Powder
FeCoNiCrTi powder belongs to a new class of materials called high entropy alloys (HEAs) which contain multiple principal alloying elements in equiatomic or near-equiatomic ratios.
Key advantages of FeCoNiCrTi powder:
- Excellent strength-ductility combination
- Outstanding fracture toughness
- Good corrosion and wear resistance
- High hardness and stiffness
- Retains strength at elevated temperatures
- Isotropic and homogenous properties
Production methods:
- Gas atomization of alloy melt
- Mechanical alloying of elemental powders
Particle sizes:
- 10 to 45 microns for AM powders
- Up to 150 microns for other applications
The unique properties of FeCoNiCrTi powder make it suitable for advanced applications across aerospace, automotive, tooling, and more.
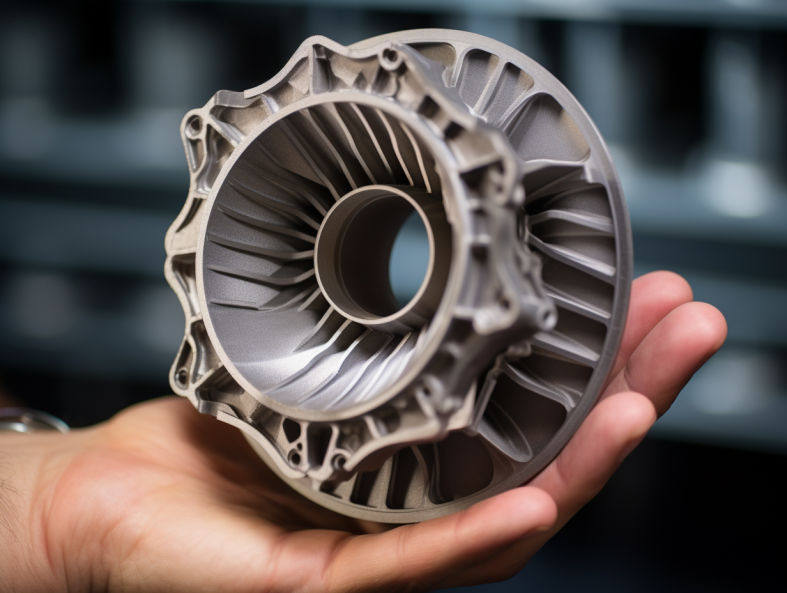
Composition of FeCoNiCrTi Powder
FeCoNiCrTi powder contains iron, cobalt, nickel, chromium and titanium in equiatomic or near-equiatomic ratios:
Element | Weight % |
---|---|
Iron (Fe) | 18-24% |
Cobalt (Co) | 18-24% |
Nickel (Ni) | 18-24% |
Chromium (Cr) | 18-24% |
Titanium (Ti) | 18-24% |
Equiatomic ratios provide the maximum configurational entropy and optimal properties. However, composition can be tailored as per application needs.
Properties of FeCoNiCrTi Powder
FeCoNiCrTi powder possesses a unique combination of mechanical properties:
Property | Function |
---|---|
High strength | Resists permanent deformation under load |
Ductility | Ability to deform plastically before fracturing |
Toughness | Absorbs impact and fracture energy |
Hardness | Resistance to surface indentation and wear |
Fatigue strength | Withstands cyclic stresses without cracking |
Creep resistance | Retains shape and strength under sustained loads |
Corrosion resistance | Resists material degradation in environments |
Thermal stability | Maintains strength and structure at elevated temperatures |
These properties make FeCoNiCrTi suitable for demanding applications across industries.
Applications of FeCoNiCrTi Powder
The high performance properties of FeCoNiCrTi powder make it ideal for:
Industry | Applications |
---|---|
Aerospace | Turbine components, thrust chambers, airframe parts |
Automotive | Gears, valves, turbocharger parts |
Industrial | Extruder screws, tooling, fabrication equipment |
Oil & Gas | Seals, valves, downhole tools |
Biomedical | Implants, surgical instruments |
Other niche applications include:
- Cutting tools and dies
- Wear parts and tooling
- Ballistic armor
- Sporting goods
The unique properties of high entropy alloy powders enable their adoption in critical applications.
Specifications of FeCoNiCrTi Powder
FeCoNiCrTi powder can be customized to meet application requirements:
Parameter | Options |
---|---|
Composition | Equiatomic, custom ratios |
Particle size | 10-45 μm, up to 150 μm |
Morphology | Spherical, irregular |
Production method | Gas atomization, mechanical alloying |
Apparent density | Up to 98% theoretical |
Flowability | Good flow characteristics |
Impurities | Minimized oxygen/nitrogen |
The powder can be optimized by tuning size, shape, density, and composition based on end-use performance needs.
Processing of FeCoNiCrTi Powder
FeCoNiCrTi powder can be processed into parts using:
- Additive manufacturing – Selective laser melting, electron beam melting
- Metal injection molding – Mixing with binder, molding, debinding, sintering
- Hot isostatic pressing – Encapsulating in can, high pressure, high temperature
- Cold/hot compaction – Pressing powder into a mold
- Extrusion – Forcing powder through a die
Each process requires tailored powder characteristics and process parameters.
Standards for FeCoNiCrTi Powder
Key standards for quality control include:
- ASTM E2926 – Standard specification for HEA powder for AM
- ASTM E3050 – Guide for characterizing HEA powder
- ASTM E3160 – Standard test method for HEA powder analysis
- ISO/ASTM 52904 – Requirements for AM metal powder
- ASTM F3056 – Specification for additive metals
- ASTM B833 – Specification for HEA powders for MIM
Compliance ensures powder quality and part performance meet application needs.
Suppliers of FeCoNiCrTi Powder
Reputable suppliers of gas atomized FeCoNiCrTi powder include:
Supplier | Location | Description | Pricing |
---|---|---|---|
Sandvik | Germany | Broadest HEA powder sizes and grades | $xxx/kg |
Praxair | US | High quality spherical HEA powders | $xxx/kg |
Carpenter | US | Custom HEA compositions and atomization | $xxx/kg |
Erasteel | Sweden | Specialist producer of niche alloys | $xxx/kg |
Prices range from $100/kg for developmental grades and small quantities to over $500/kg for specialized compositions.
Factors that affect pricing include order volume, powder morphology, custom alloy development, and certifications required.
How to Select a FeCoNiCrTi Powder Supplier
Important factors when selecting an FeCoNiCrTi powder supplier:
- Experience with high entropy alloy powder manufacturing
- Quality management system and testing capabilities
- Flexibility to tailor composition and particle characteristics
- Technical expertise in HEA powder metallurgy
- Range of available powder sizes and morphologies
- Reasonable pricing for required order volumes
- Responsiveness for custom orders and compositions
- Compliance with industry standards and certifications
Work with a supplier focused on consistently meeting your application requirements.
Pros and Cons of FeCoNiCrTi Powder
Advantages:
- Excellent strength-ductility combination
- High fracture toughness
- Good high temperature strength
- Resistant to fatigue, wear and corrosion
- Isotropic and homogenous properties
- High hardness and stiffness
Disadvantages:
- Relatively high material cost
- Limited commercial availability currently
- Processing can require advanced techniques
- Composition and microstructure sensitivities
- Oxidation resistance limitations at very high temperatures
Properties can be tuned by adjusting composition and processing to maximize benefits and minimize limitations.
Comparison to Stainless Steel Powder
FeCoNiCrTi | Stainless Steel |
---|---|
Higher strength | Moderate strength |
Superior toughness | Brittle, prone to cracking |
Better high temperature strength | Loses strength above 600°C |
More thermally stable | Sensitive to thermal fluctuations |
Lower density | Higher density |
More corrosion resistant | Prone to pitting and crevice corrosion |
Harder | Softer and more ductile |
More expensive | Lower cost |
FeCoNiCrTi HEA powder outperforms stainless steel for critical applications despite higher cost.
Comparison to Tool Steel Powder
FeCoNiCrTi | Tool Steel Higher hardness | Moderate hardness Superior toughness | Prone to brittle fracture Better creep resistance | Softens at high temperatures
More corrosion resistant | Sensitive to corrosion in certain environments Thermally stable | Loses hardness above 600°C More refractory | Dimensional changes at high temperatures Higher raw material costs | Less expensive More challenging to process | Easier to machine and process
HEA powder is preferred for high temperature tooling, dies, molds despite being more difficult to machine after processing.
Future Outlook
The future looks bright for FeCoNiCrTi and other HEA powders:
- Expanding adoption in aerospace, automotive and industrial sectors
- Developments in alloy compositions and processing techniques
- Declining costs as production scales up
- Growth in high performance niches like motorsports
- New players entering the HEA powder supply chain
- Increased R&D on microstructure and property optimization
- Recycling initiatives to recover scrap powder
HEA powder offers a promising material platform for next-generation advanced components and processes across critical industries.
FAQs
Q: What are high entropy alloys?
A: HEAs contain multiple principal elements in high entropy compositions that enhance properties through elemental interactions.
Q: What industries use FeCoNiCrTi powder?
A: Primarily aerospace, automotive, tooling, oil and gas, sporting goods. The medical field is also evaluating these alloys.
Q: What particle size is best for AM of FeCoNiCrTi?
A: 10-45 microns is optimal. Finer particles offer better resolution but can impact flow and density.
Q: Does FeCoNiCrTi require heat treatment?
A: Yes, heat treatment can adjust hardness, strength and ductility. Solution annealing followed by aging is common.
Q: Is FeCoNiCrTi powder expensive?
A: Prices range from $100-500/kg. Cost is higher than steels but reasonable for a high performance alloy.
Q: Is FeCoNiCrTi hard to machine?
A: Yes, it requires diamond tooling. Machinability can be improved through composition adjustments.
Q: Can you 3D print FeCoNiCrTi?
A: Yes, selective laser melting and electron beam melting offer excellent results with FeCoNiCrTi powder.
Q: Is FeCoNiCrTi powder toxic?
A: Elemental powders require handling precautions against risks like inhalation. Proper PPE should be worn.
Q: Does FeCoNiCrTi work harden rapidly?
A: No, its ability to deform without strain hardening is beneficial for formability and machinability.
Q: Is FeCoNiCrTi resistant to sea water corrosion?
A: Yes, it demonstrates excellent corrosion resistance to marine and many other aggressive environments.