Haynes Alloy 188 Powder is an oxidation resistant nickel-chromium-cobalt-tungsten alloy powder designed for high temperature service up to 2200°F. This guide covers Haynes 188 powder compositions, properties, manufacturing methods, applications, specifications, pricing, comparisons, and frequently asked questions when considering this superalloy material.
Typical Composition of Haynes Alloy 188 Powder
Element | Weight % |
---|---|
Nickel | Balance |
Chromium | 22% |
Tungsten | 14% |
Cobalt | 10% |
Iron | 3% |
Manganese | 1.25% max |
Silicon | 0.35% max |
Carbon | 0.1% max |
Nickel gives ductility and chromium provides oxidation resistance. Tungsten and molybdenum for solid solution strengthening. Low carbon minimizes carbide precipitation during long exposures above 1000°F.
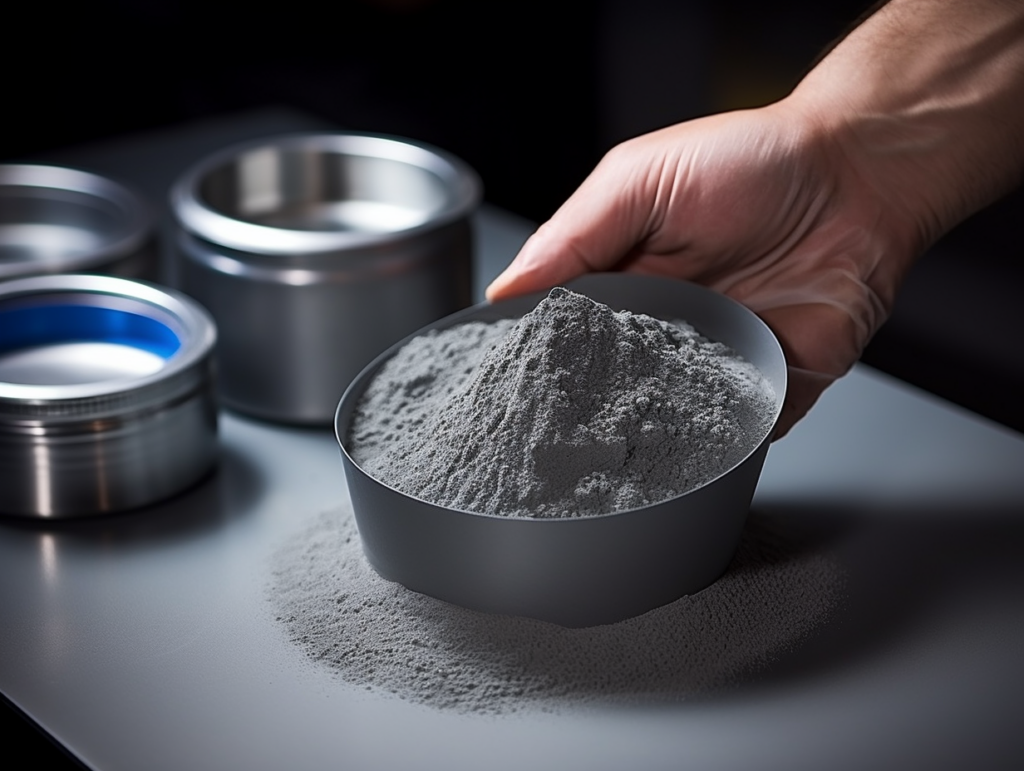
Key Properties and Characteristics
Haynes Alloy 188 Powder delivers an optimal balance of properties:
- Excellent oxidation resistance and thermal stability up to 2200°F from high levels of Cr and W
- Less tendency to sigma phase embrittlement than Haynes 617 alloy
- Retains strength and resists creep deformation at high operating temperatures
- More fabricable than high tungsten Rhenium alloys
- Available as gas atomized powder for additive manufacturing or powder metallurgy
Typical Applications of Haynes Alloy 188 Powder
Industry | Common Uses |
---|---|
Aerospace | Afterburner components, combustion liners |
Gas Turbines | Transition ducts, seals, cases |
Automotive | Turbocharger housings, exhaust manifolds |
Petrochemical | Heat treating fixtures, reformer tubes |
Thermal spray | Wear and corrosion resistant coatings |
Haynes 188 resists oxidation in extreme thermal cycling environments, making it suitable for the hottest section components across diverse industries.
Haynes Alloy 188 Powder Specifications
Product Form | Standards |
---|---|
Wrought sheet/plate | AMS 5759, AMS 5997 |
Wrought bar | AMS 5759 |
Welding wire | AWS A5.14 ERNiCrCoW |
Powder feedstock | – |
No existing specifications for 188 alloy powder since most usage is in research contexts. Peroformance expectations align with wrought equivalents. Application determines acceptance criteria.
-
CM247LC Powder | Nickel Alloy Powder
-
0# Pure Nickel powder
-
NiCoCrAlY alloys powders
-
Rene 142 alloy-Rene Powder
-
Haynes 25 Haynes Powder
-
Best Hastelloy C-22 Powder-High temperature alloy Powder for 3D Printing
-
Best Hastelloy C-276 Powder-High temperature alloy Powder for 3D Printing
-
Best Hastelloy N Powder-High temperature alloy Powder for 3D Printing
-
Best Hastelloy B Powder丨High temperature alloy Powder for 3D Printing
Suppliers and Pricing
Vendor | Lead Time | Price/kg |
---|---|---|
Sandvik Osprey | 12 weeks | $170 |
Atlantic Equipment | 16 weeks | $200 |
TLS Technik | 16 weeks | $210 |
Special Metals Corp | 12 weeks | $160 |
Pricing indicative for 100 kg batch. Significant volume discounts from 500 kg upwards.
Comparative Analysis
Attribute | Haynes 188 | Haynes 617 | Waspaloy |
---|---|---|---|
Max temperature | 2200°F | 2100°F | 1800°F |
Oxidation resistance | Excellent | Very Good | Moderate |
Cost | Moderate | High | Low |
Fabrication | Good | Challenging | Excellent |
Among Ni superalloys, Haynes 188 provides the best combination of temperature capability, oxidation resistance and fabricability. Preferred over 617 when extreme thermal stability not needed.
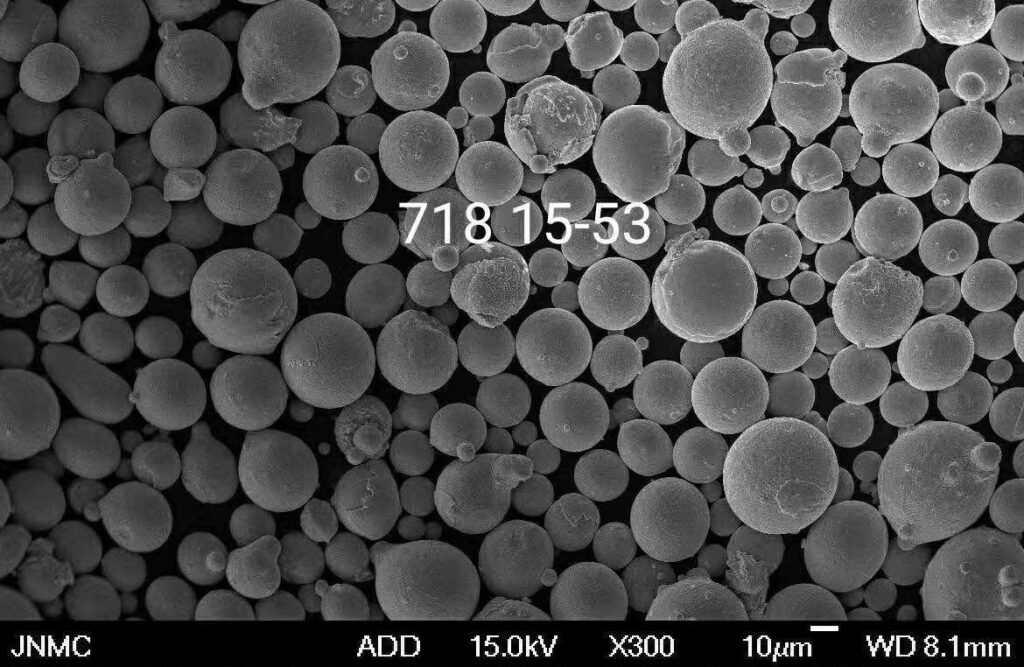
FAQ
What particle size range is used for laser powder bed fusion?
Around 15-45 microns for most printers. Larger particles hurt density and surface finish. Too fine powders can be safety hazards.
Does Haynes 188 powder require hot isostatic pressing (HIP) post printing?
Yes, HIP helps close internal voids improving fatigue resistance. 2165°F at 15 ksi for 4 hours typical post treatment. Eliminates need for internal supports.
What environments cause Haynes 188 degradation?
Sulfidation and salt corrosion attack protective Cr2O3 scale. Long exposures above 1800°F leads to incipient melting and alloy changes. Cyclic heating into bright red heat shortens life.
Why is Haynes 188 powder expensive relative to nickel alloys?
Complex multicomponent composition with 14% tungsten significantly raises alloy costs. Manufacturing meticulous requiring vacuum or inert gas atomization, additional powder classification steps etc also adds cost.
What are common defects when printing Haynes 188 parts?
Lack of fusion defects from poor energy density or scan strategies. Residual internal stresses distorting finer features. unused alloy powder trapped inside closed volumes. Incomplete HIP diffusion hardening.
Conclusion
Haynes 188 powder combines excellent high temperature properties and oxidation resistance pivotal for additive manufacturing and powder metallurgy processing of critical components facing extreme environments. Harnessing the design freedoms of emerging manufacturing methods allows expanding usage of Haynes 188 into new applications.