High temperature iron powders refer to specialized metallic iron powders designed to operate at elevated temperatures beyond 700°C without rapidly oxidizing or losing strength. These advanced materials expand the usable temperature range of iron while retaining magnetic properties, making them critical for modern applications including electromagnetic devices like motors, actuators, sensors and transformers.
Overview of High Temperature Iron Powder
High temperature iron powders are produced by thermally stable insulative coatings on iron particles, alloying additions, or other proprietary methods to impart oxidation and corrosion resistance for sustained performance in warmer environments.
These powders retain high saturation induction and low core losses at 400-700°C, unlike conventional iron which suffers from rapid deterioration of magnetic properties beyond 300°C. Their thermal endurance allows miniaturized electromagnetic components to handle higher power densities.
Types of High Temperature Iron Powder
Several distinct material technologies exist for imparting thermal stability:
Type | Description |
---|---|
Silicon coated iron | Iron particles encapsulated by thin silica layer |
Alloyed iron powder | Small additions of Al, Si, Cr increase temperature resistance |
Annealed carbonyl iron | Improved insulation minimizes eddy current losses |
High purity iron | 99.5%+ iron content raises operating ceiling |
Silicon coated, alloyed and high purity iron powders dominate the landscape of commercially available high temperature grades. Each approach has relative advantages and limitations.

Composition of High Temperature Iron
While the base composition is >90% iron for most high temperature grades, various alloying additions or coatings are used to curb oxidation around 500-600°C. Some typical compositions are:
Material | Composition |
---|---|
Silicon coated iron | 96-98% Fe, 2-4% SiO2 coating |
Alloyed iron | Up to ~3% Cr, 2% Al, 1% Si |
High purity iron | 99.5%+ iron, 0.01% C, low oxygen |
Maintaining high iron content is vital for enabling elevated Curie temperatures while additions protect powders against rapid air oxidation. Balancing magnetic performance and temperature resistance is key.
Properties of High Temperature Iron Powder
Key properties of high temperature iron powders are:
Property | Typical Value |
---|---|
Saturation induction | 1.7-2.1 Tesla up to 500°C |
Resistivity | ~1.0-1.4 x 10<sup>-7</sup> Ωm |
Curie temperature | 750 – 1050°C |
Thermal conductivity | 25-35 W/mK |
Density | 7.1 – 7.4 g/cm3 |
Exceptional saturation magnetization persistence versus temperature paired with electrical resistivity form the foundation for high efficiency in motors, transformers, inductors etc.
Characteristics of High Temp Iron Powders
Critical characteristics differentiating commercially available high temperature iron powders include:
Characteristic | Significance |
---|---|
Temperature resistance | Oxidation protection determines upper limit |
Saturation induction | Magnetic strength heavily influences efficiency |
Resistivity | Higher is better for minimizing eddy current losses |
Particle size distribution | Affects powder pressing and sintered density |
Compactability | High green/sintered density improves properties |
Flowability | Impacts ease of powder handling during processing |
Balancing thermal stability and magnetic performance defines the quality and value proposition of these premium powders.
Applications of High Temperature Iron
The unique properties of high temperature iron powders make them ideally suited for:
High Temperature Iron Applications
Category | Applications |
---|---|
Automotive | Ignition coils, traction motors, sensors |
Aerospace | generators, actuators, relays |
Power | Grounding transformers, reactors, energy meters |
Electronics | Magnetic amplifier cores, inductor cores |
Chemical | Reactors vessels, high temperature reactors |
Equipment | Wind turbines, heavy electrical systems |
Exceptional thermal persistence of magnetic flux density combined with design flexibility using powder metallurgy enables next generation electric machine designs across transportation, energy and industrial systems.
Specifications of High Temperature Iron Powder
High temperature iron powders must meet exacting standards concerning properties and powder characteristics:
Parameter | Typical Specification | Test Standard |
---|---|---|
Apparent density | 2.7 – 4 g/cm3 | ASTM B243 |
Tap density | 3.6 – 5 g/cm3 | ASTM B527 |
Compacted density | 6.8 – 7.4 g/cm3 | MPIF 42 |
Induction (500°C) | > 1.4 Tesla | ASTM A773 |
Resistivity (500°C) | > 7×10<sup>-6</sup> Ωm | ASTM B43 |
International testing standards help qualify magnetic performance, densification response and electrical properties following exposure to elevated operating temperatures around 500°C.
-
CM247LC Powder | Nickel Alloy Powder
-
0# Pure Nickel powder
-
NiCoCrAlY alloys powders
-
Rene 142 alloy-Rene Powder
-
Haynes 25 Haynes Powder
-
Best Hastelloy C-22 Powder-High temperature alloy Powder for 3D Printing
-
Best Hastelloy C-276 Powder-High temperature alloy Powder for 3D Printing
-
Best Hastelloy N Powder-High temperature alloy Powder for 3D Printing
-
Best Hastelloy B Powder丨High temperature alloy Powder for 3D Printing
Grades of High Temperature Iron Powder
Grades are differentiated based on:
Grade | Definitions |
---|---|
Temperature index | Maximum operating temperature in °C |
Permeability grade | Indication of flux density and losses |
Alloy designations | Defines composition (A, AS, ASC etc) |
Manufacturing method | Water atomized, carbonyl process etc |
Common commercial grades rated for 500-600°C use include HS, HF, ASR and ASC – signifying high silicon, high flux, alloyed silicon-resistant and alloyed silicon-coated respectively. Custom grades optimize magnetic saturation, permeability, core losses and temperature performance.
Global Standards for High Temp Iron Powder
Globally accepted quality standards include:
Standard | Scope |
---|---|
ISO 4491 | Metallic powders – Determination of oxygen content by reduction methods |
ISO 4829-1 | Iron powders for sintered products — Part 1: Specifications and test methods |
MPIF Standard 35 | Materials Standards for Magnetic Properties of High Flux Iron Powders |
ASTM A877M | Standard Test Method for Iron Powders and Powder Metallurgy Products By Direct Current Magnetic Methods |
These composition, testing and analysis standards ensure batch-to-batch consistency and provide quality metrics for high temperature powder assessment across geographies.
Suppliers of High Temperature Iron Powder
Leading global manufacturers of thermally stable iron powders include:
Company | Brand Names | |
---|---|---|
Höganäs | North America | ASC, ANCORSTEEL |
Rio Tinto | UK | STARLITE |
JFE Steel | Japan | JIP |
BASF | Germany | CIP |
Sandvik Osprey | UK | ATOMET |
Several specialty brands andgrades optimize magnetic properties, resistivity and oxidation resistance for 500-700°C operational environments. Both global suppliers and regional distributors offer these materials.
Pricing
Due to extensive R&D and proprietary methods for enhancing thermal persistence, high temperature iron powders demand significant pricing premiums over conventional iron:
Powder Grade | Estimated Price Range |
---|---|
High silicon iron | $5 – $8 per kg |
Alloyed iron | $7 – $12 per kg |
High purity iron | $10 – $15 per kg |
Prices vary based on precise chemistry, powder characteristics, customization, order volumes, production method and supplier relationships. Contact manufacturers directly for quotes.
Comparative Analysis of High Temperature Iron Powder
Tradeoffs exist between different material options:
Metric | Silicon Coated | Alloyed | High Purity |
---|---|---|---|
Max. temp | 600°C | 700°C | 750°C |
Saturation | Excellent | Very good | Good |
Resistivity | Very good | Good | Excellent |
Cost | $ | $$ | $$$ |
Environmental | Poor | Good | Excellent |
While silicon coated iron offers the lowest cost option to 500-600°C, high purity powders extend the ceiling further. Performance balancing with pricing and manufacturing sustainability helps guide material selection.
Advantages of High Temperature Iron
Key benefits include:
- Operates efficiently at 400-700°C unlike conventional iron at 300°C
- Retains magnetic properties like saturation, low losses
- Achieves improved power density and miniaturization
- Enables electric designs for aerospace, automotive etc.
- Powder-based manufacturing enables net-shape parts
Ability to shrink electromagnetic component sizes while raising temperature and power handling unlocks superior system performance.
Limitations of High Temperature Iron
The main restrictions are:
- Cost – Significant pricing premiums over standard iron grades
- Embrittlement – Some alloying additions negatively impact ductility
- Recyclability – Composite alloys have lower reuse potential
- Oxidation – Only moderate chemical resistance in acidic environments
Understanding compromises around budget, durability, reuse and chemical compatibility aids selection of optimum high temperature iron variant.
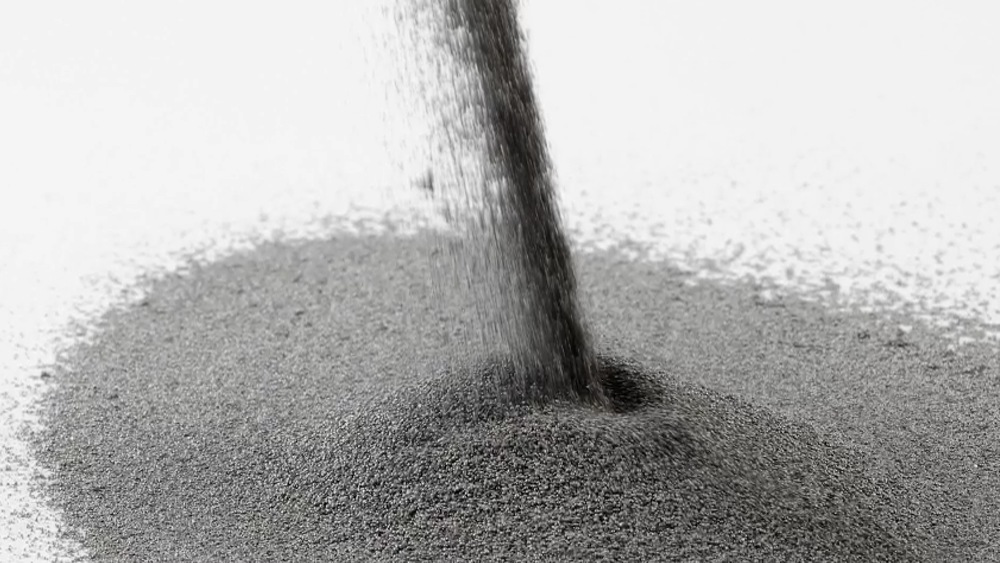
Frequently Asked Questions
FAQs
Question | Answer |
---|---|
How is high temperature iron powder made? | Specialized production techniques like inert gas atomization, surface enrichment and proprietary coatings impart thermal stability. Post-processing like annealing or oxidizing enhances insulation. |
What are typical alloying elements in iron powder? | Silicon, aluminum, chromium aid formation of surface oxide barriers up to ~500-700°C. Minimal additions curb oxidation without excessively impacting magnetics. |
Why can’t standard iron operate at high temperatures? | Iron rapidly oxidizes when heated in air above ~300°C, causing powder particles to deteriorate and lose magnetic strength very quickly. Unprotected iron simply does not have requisite thermal persistence. |
What is high temperature iron powder used for? | Enables miniaturized motors, transformers, inductors etc. to function efficiently at 400-700°C in applications ranging from automotive traction to aerospace electrical systems, generators etc |
Is high temperature iron powder expensive? | Yes, high purity grades and specialized proprietary production to enhance thermal endurance with tightly controlled characteristics results in costs exceeding standard iron by 5-10x. But enhanced performance justifies premium prices for critical applications. |