Imagine being able to fabricate intricate, high-performance components with exceptional strength, heat resistance, and corrosion defiance – all from a metal powder just a fraction of a millimeter wide. That’s the magic of IN718 powder, a revolutionary material pushing the boundaries of 3D printing in demanding industrial applications. Buckle up, as we delve into the world of this remarkable material, exploring its characteristics, applications, and the intricate details that make it a game-changer in the realm of additive manufacturing.
Characteristics of IN718 powder
IN718 powder, also known as Inconel 718 powder, is a nickel-chromium-based superalloy specifically engineered for 3D printing processes. It boasts a unique blend of properties that make it a favorite for creating parts that need to withstand extreme conditions:
- Exceptional Strength: Imagine a material that can rival the strength of steel even at elevated temperatures. IN718 powder delivers just that, offering outstanding tensile strength, creep resistance, and fatigue resistance, making it ideal for applications like aerospace components, turbine blades, and downhole tools.
- Superior Heat Resistance: Think of withstanding scorching temperatures that would melt most metals. IN718 powder possesses phenomenal heat resistance, able to maintain its strength and structural integrity even at temperatures exceeding 1200°C (2200°F). This makes it perfect for parts exposed to intense heat, like jet engine components and combustion chambers.
- Outstanding Corrosion Resistance: Picture a material that remains unfazed by harsh environments. IN718 powder shines in its resistance to corrosion and oxidation, even in demanding environments like saltwater, high-pressure steam, and acidic solutions. This characteristic makes it ideal for marine applications, chemical processing equipment, and parts exposed to harsh chemicals.
- Excellent Formability: Imagine the flexibility to create intricate shapes with exceptional precision. IN718 powder exhibits good ductility and formability, allowing for the creation of complex geometries with smooth surface finishes. This property makes it suitable for intricate components requiring tight tolerances and precise functionality.
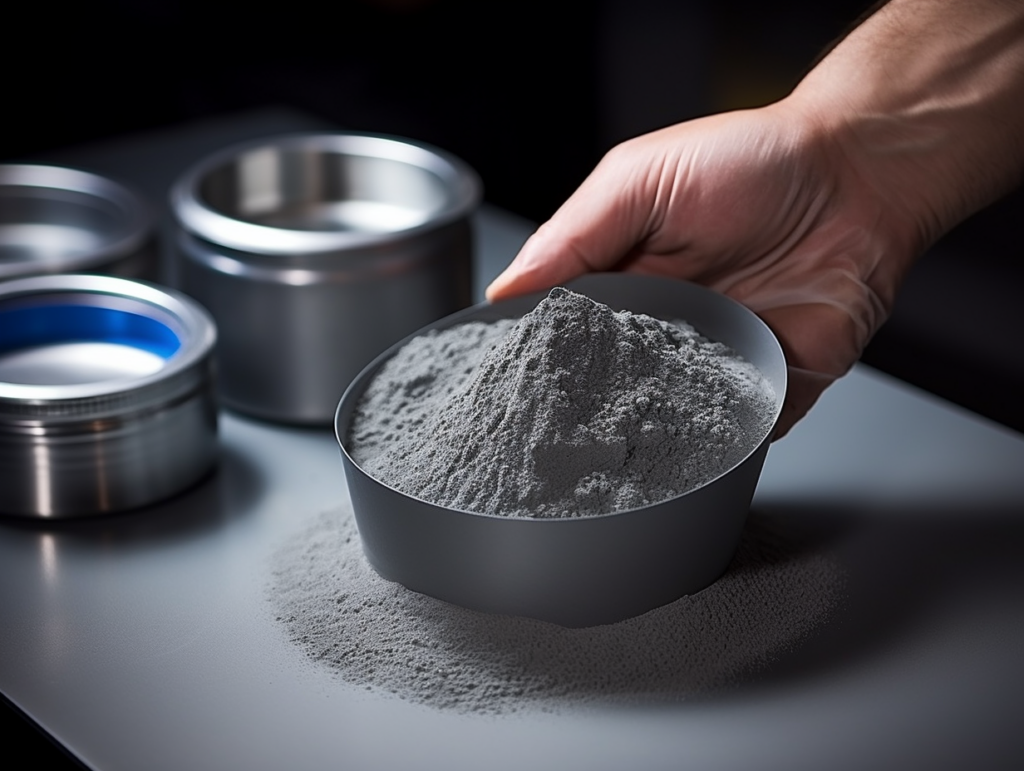
Composition of IN718 powder
Element | Weight % |
---|---|
Nickel (Ni) | Bal. |
Chromium (Cr) | 17-21 |
Iron (Fe) | Bal. |
Niobium (Nb) | 2.8-3.3 |
Molybdenum (Mo) | 2.8-3.3 |
Manganese (Mn) | 0.75-1.25 |
Silicon (Si) | 0.35-0.75 |
Others (C, S, P) | Max 0.15 |
Key benefits of IN718 powder
- High-performance capabilities: Delivers exceptional strength, heat resistance, and corrosion resistance.
- Design freedom: Enables the creation of complex geometries with intricate features.
- Material efficiency: Minimizes waste compared to traditional manufacturing methods.
- Lightweighting potential: Can create lighter components compared to traditional alloys, improving fuel efficiency in applications like aerospace.
Limitations of IN718 powder
- High cost: Compared to other metal powders, IN718 powder can be more expensive due to its complex manufacturing process and high-performance properties.
- Process complexity: Requires specialized 3D printing equipment and expertise to handle the material effectively.
- Post-processing: May require additional post-processing steps like heat treatment to achieve optimal mechanical properties.
IN718 powder is used to manufacture various high-performance components
Industry | Applications |
---|---|
Aerospace | Turbine blades, combustor liners, landing gear components, rocket engine parts |
Oil & Gas | Downhole tools, wellhead components, valves, pumps |
Chemical Processing | Heat exchangers, reactors, vessels, piping |
Marine | Impellers, propellers, rudders, shafts |
Power Generation | Gas turbine components, heat exchangers, steam turbine blades |
Medical | Implants, prosthetics, surgical instruments |
This list is not exhaustive, and IN718 powder’s versatility allows it to be explored in various other demanding applications where exceptional performance is crucial.
IN718 powder is processed using PBF, DED, and AM processes
- Powder Bed Fusion (PBF): This popular technique utilizes a laser beam to selectively melt and fuse layers of IN718 powder, building the desired component layer by layer. PBF offers high accuracy and resolution, making it ideal for intricate geometries.
Metal Powder Models for Unleashing IN718’s Potential
While IN718 powder offers remarkable properties, its specific characteristics can vary depending on the manufacturer and the processing methods employed. Here’s a glimpse into some of the leading metal powder models available:
Model: EOS Nickel Alloy IN718
- Description: This gas-atomized powder from EOS is known for its excellent flowability and packing density, leading to consistent builds and high-quality components. It’s optimized for laser PBF processes and caters to various demanding applications in aerospace, oil & gas, and power generation.
- Applications: Turbine blades, downhole tools, heat exchangers, and other high-performance components.
Model: LPW IN718
- Description: LPW’s IN718 powder is renowned for its tight chemical control and consistent particle size distribution, ensuring reliable printability and predictable mechanical properties. It’s suitable for a broad range of PBF 3D printing systems and caters to applications in the aerospace, automotive, and medical industries.
- Applications: Turbine blades, engine components, prosthetics, and other high-strength parts.
Model: SLM Solutions IN718
- Description: This gas-atomized powder from SLM Solutions boasts exceptional purity and flowability, enabling the creation of near-net-shape components with minimal post-processing requirements. It’s tailored for laser and electron beam PBF processes and finds applications in aerospace, energy, and medical sectors.
- Applications: Rocket engine parts, gas turbine components, and complex surgical instruments.
Model: IN718 AM Powder by Höganäs
- Description: Höganäs offers IN718 powder specifically designed for Additive Manufacturing (AM) processes. This atomized powder features a spherical morphology and controlled particle size distribution, promoting optimal flowability and printability. It caters to various AM technologies, including PBF, DED, and binder jetting.
- Applications: Aerospace components, downhole tools, heat exchangers, and other parts requiring intricate geometries.
Model: Carpenter Additive IN718
- Description: Carpenter Additive’s IN718 powder is produced using a proprietary argon gas atomization process, resulting in a powder with superior flowability and packing density. This powder is optimized for PBF processes and caters to demanding applications in aerospace, oil & gas, and power generation.
- Applications: Turbine blades, downhole tools, heat exchangers, and other high-performance components.
Model: ALD IN718
- Description: Produced by Aubert & Duval, ALD IN718 powder is known for its exceptional chemical homogeneity and tight particle size distribution. This powder is suitable for various PBF systems and caters to applications in the aerospace, defense, and energy sectors.
- Applications: Turbine blades, rocket engine parts, and other high-strength, high-temperature components.
Model: IN718 Powder by Sandvik
- Description: Sandvik’s IN718 powder is gas-atomized and nitrogen-treated, offering excellent flowability and printability. It’s tailored for PBF processes and finds applications in demanding environments like aerospace, oil & gas, and chemical processing.
- Applications: Turbine blades, downhole tools, heat exchangers, and other components requiring superior corrosion resistance.
Model: IN718 by ExOne
- Description: ExOne offers IN718 powder specifically formulated for binder jet 3D printing processes. This powder features a spherical morphology and controlled particle size distribution, enabling efficient printing and high-quality component production.
- Applications: Complex heat exchangers, lightweight components for aerospace applications, and intricate parts with internal channels.
Model: IN718 by 3D Matter
- Description: 3D Matter’s IN718 powder is produced using a water atomization process, resulting in a cost-effective option for various 3D printing applications. This powder is suitable for PBF and DED processes and caters to industries like automotive, oil & gas, and power generation.
- Applications: Prototypes, functional components requiring good mechanical properties, and parts where cost is a crucial factor.
Remember: This list is not exhaustive, and numerous other metal powder models are available from various manufacturers. It’s essential to consider factors like your specific application, desired properties, printing process compatibility, and budget when selecting the most suitable IN718 powder for your needs.
choosing an IN718 powder model
- Particle size distribution: The size and distribution of powder particles significantly impact flowability, printability, and final component properties.
- Sphericity: Spherical particles generally offer better flowability and packing density compared to irregularly shaped particles.
- Chemical composition: Slight variations in chemical composition can influence the mechanical properties and performance of the final component.
- Flowability: Powders with good flowability enable smooth and consistent feeding into the 3D printing system, ensuring consistent layer formation and high-quality builds.
- Moisture content: Excessive moisture can negatively impact powder flowability and lead to processing issues.
- Certification: Consider powders that meet relevant industry standards or certifications for specific applications, like aerospace or medical implants.
Applications of IN718 powder
IN718 powder’s unique blend of properties unlocks its potential in various industries, pushing the boundaries of what’s possible:
Aerospace:
- Turbine blades: IN718 powder is a popular choice for manufacturing high-performance turbine blades due to its exceptional strength, heat resistance, and creep resistance at elevated temperatures. These blades are crucial for efficient jet engine operation.
- Combustor liners: Exposed to extreme heat and pressure, IN718 powder finds application in combustor liners, which contain the combustion process within jet engines.
- Landing gear components: Landing gear components require a combination of strength, lightweight design, and corrosion resistance. IN718 powder fulfills these needs, making it suitable for manufacturing landing gear components.
- Rocket engine parts: IN718 powder’s ability to withstand high temperatures and pressure makes it valuable for manufacturing certain rocket engine parts, contributing to the success of space exploration endeavors.
Oil & Gas:
- Downhole tools: Downhole tools used in oil and gas exploration and production require immense strength and corrosion resistance to operate in harsh downhole environments. IN718 powder’s properties make it an ideal material for these tools.
- Wellhead components: Wellhead components are critical for controlling and managing pressure during oil and gas extraction. IN718 powder’s strength and corrosion resistance make it suitable for these applications.
- Valves and pumps: Valves and pumps play a vital role in oil and gas operations, and IN718 powder’s properties ensure they can withstand demanding conditions and high pressures.
Chemical Processing:
- Heat exchangers: Heat exchangers transfer heat between fluids in various industrial processes. IN718 powder’s excellent heat resistance and corrosion resistance make it suitable for manufacturing heat exchangers used in harsh chemical environments.
- Reactors: Chemical reactors are vessels where chemical reactions take place. IN718 powder’s ability to withstand high temperatures and corrosive chemicals makes it suitable for specific reactor applications.
- Vessels and piping: Vessels and piping are used to store and transport various chemicals in the process industry. IN718 powder’s corrosion resistance makes it a valuable material for these components.
Marine:
- Impellers and propellers: Impellers and propellers are essential components for marine vessels, and IN718 powder’s strength and corrosion resistance make it suitable for their manufacture.
- Rudder components: Rudders enable steering of marine vessels, and IN718 powder’s properties contribute to the creation of robust and reliable rudders.
- Shafts: Shafts transmit power in various marine applications, and IN718 powder’s strength makes it a suitable material for these components.
Other Industries:
- Power generation: IN718 powder finds application in gas turbine components, heat exchangers, and steam turbine blades within the power generation industry due to its ability to handle high temperatures and pressures.
- Medical: While strictly regulated, IN718 powder shows promise in creating specific medical implants and prosthetics due to its biocompatible properties and high strength. However, thorough testing and certification are necessary before widespread adoption in the medical field.
The potential applications of IN718 powder continue to expand as research and development efforts delve deeper into its capabilities. As 3D printing technology matures, we can expect even more innovative applications to emerge, revolutionizing various industries.
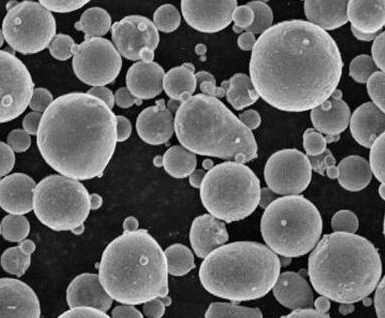
FAQ
Q: What are the different types of IN718 powder available?
A: Several manufacturers offer IN718 powder, and the specific types can vary in terms of particle size distribution, sphericity, chemical composition, and flowability. It’s crucial to consult with the manufacturer and consider your specific application requirements when choosing the most suitable type.
Q: What are the advantages of using IN718 powder compared to traditional manufacturing methods?
A: IN718 powder offers several advantages over traditional manufacturing methods, including:
- Design freedom: Enables the creation of complex geometries with intricate features that might be challenging or impossible to produce using conventional techniques.
- Material efficiency: Minimizes waste compared to subtractive manufacturing methods, where material is removed to create the desired shape.
- Lightweighting potential: Allows for the creation of lighter components compared to traditional alloys, leading to potential benefits like improved fuel efficiency in aerospace applications.
- Rapid prototyping: Enables the rapid creation of prototypes for faster design iteration and testing cycles.
Q: What are the limitations of using IN718 powder?
A: While offering numerous advantages, IN718 powder also has limitations to consider:
- High cost: Compared to other metal powders, IN718 powder can be more expensive due to its complex manufacturing process and high-performance properties.
- Process complexity: Requires specialized 3D printing equipment and expertise to handle the material effectively, potentially increasing upfront investment and operational costs.
- Post-processing: May require additional post-processing steps like heat treatment to achieve optimal mechanical properties, adding to the overall processing time and complexity.
Q: What are the safety considerations when working with IN718 powder?
A: IN718 powder, like other metal powders, can pose certain health and safety risks. It’s crucial to follow proper safety protocols when handling this material, including:
- Wearing appropriate personal protective equipment (PPE): This may include safety glasses, gloves, respirators, and protective clothing to prevent inhalation, skin contact, and eye irritation.
- Working in a well-ventilated environment: Ensure adequate ventilation to minimize exposure to airborne dust particles.
- Proper handling and storage: Follow the manufacturer’s recommendations for safe handling and storage of the powder to prevent contamination and maintain its quality.