Imagine building a rocket engine that can withstand the scorching heat of a jet blast, or a turbine blade that spins relentlessly in a power plant without succumbing to fatigue. This is the realm of IN939 powder, a superhero material in the world of 3D printing that brings unparalleled strength and resilience to the game.
Let’s delve into the fascinating world of IN939 powder, exploring its composition, properties, applications, and the nitty-gritty details like suppliers and pricing. Buckle up, because we’re about to embark on a journey through the fiery world of high-temperature 3D printing!
Chemical Composition of IN939 Powder
IN939 powder belongs to the elite family of nickel-based superalloys. Think of it as a metallic cocktail where nickel plays the starring role, supported by a cast of other elements that bring out its superpowers. Here’s a breakdown of the key ingredients:
- Nickel (Ni): The foundation of the alloy, providing strength and ductility.
- Chromium (Cr): Acts like a shield, protecting the material from corrosion and oxidation at high temperatures.
- Cobalt (Co): Enhances high-temperature strength and creep resistance (the ability to resist deformation under stress).
- Molybdenum (Mo): Strengthens the grain boundaries and improves overall high-temperature performance.
- Tantalum (Ta): A rare element that further enhances creep resistance and oxidation resistance.
These elements, meticulously combined in specific proportions, imbue IN939 powder with its remarkable properties.
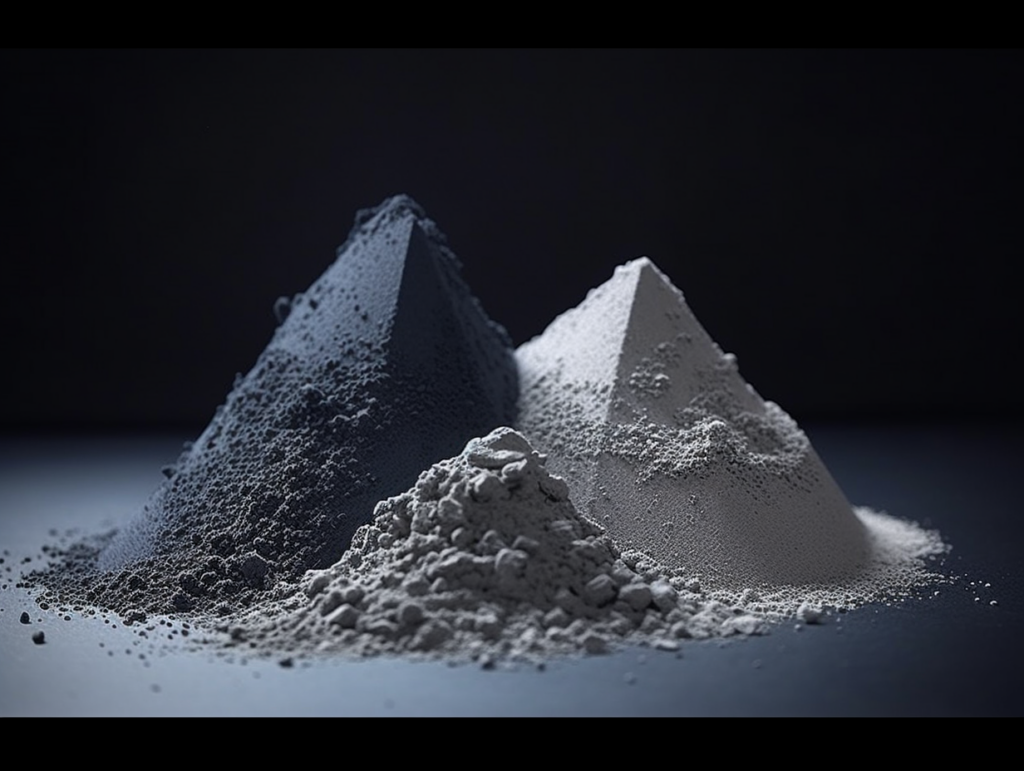
The Advantages of IN939 Powder
IN939 powder isn’t your average metal dust. It boasts a unique set of advantages that make it a champion in the high-temperature 3D printing arena:
- Unmatched Strength: Imagine a material that can shrug off extreme stress and pressure. IN939 powder exhibits exceptional strength, even at scorching temperatures exceeding 850°C (1560°F). This makes it ideal for components that experience immense loads, like turbine blades in jet engines or power plants.
- Superior Oxidation Resistance: High temperatures are often accompanied by a villain – oxidation, where the material reacts with oxygen and deteriorates. IN939 powder stands strong against this foe, maintaining its integrity and functionality in environments where other materials would crumble.
- Excellent Creep Resistance: Under constant stress and high temperatures, even the strongest materials can slowly deform over time. IN939 powder defies this creep, resisting deformation remarkably well, ensuring components retain their shape and function for extended periods.
- Fatigue Strength: Imagine a component that undergoes millions of cycles of stress – that’s fatigue in a nutshell. IN939 powder demonstrates exceptional resistance to fatigue, making it perfect for parts subjected to repetitive stress, like turbine blades or landing gear components.
- Design Freedom of 3D Printing: Unlike traditional manufacturing methods, 3D printing with IN939 powder allows for the creation of complex geometries that were previously impossible. This opens doors for innovative and lightweight designs in demanding applications.
These combined advantages make IN939 powder a highly sought-after material for pushing the boundaries of what’s possible in high-temperature environments.
Disadvantages of IN939 Powder
While IN939 powder possesses remarkable qualities, it’s not without its challenges:
- High Cost: The complex composition and specialized production processes make IN939 powder a premium material. This translates to a higher cost compared to some other metal powders used in 3D printing.
- Processing Challenges: 3D printing with IN939 powder requires specialized equipment and expertise due to its high melting point and sensitivity to processing parameters. Think of it as a high-maintenance superhero – it demands a skilled team to unleash its full potential.
- Limited Availability: Compared to more widely used metal powders, IN939 powder might have slightly lower availability. However, as the demand for high-temperature 3D printing grows, this is likely to change.
Despite these limitations, the exceptional properties of IN939 powder often outweigh the challenges, making it the go-to choice for a variety of demanding applications.
Applications of IN939 Powder
IN939 powder takes center stage in various industries where high temperatures and extreme performance are the norm. Here are some key applications:
Aerospace:
- Turbine Blades: The whirring heart of jet engines, turbine blades experience tremendous stress and heat. IN939 powder’s strength and high-temperature capabilities make it a perfect candidate for this critical component.
- Combustor Liners: These components channel the fiery
- Afterburner Components: For that extra burst of power, afterburners ignite fuel in the exhaust stream. IN939 powder’s resistance to heat and fatigue makes it ideal for these scorching components.
Power Generation:
- Gas Turbine Blades: Similar to jet engines, gas turbines in power plants rely on blades that spin at high speeds under intense heat. IN939 powder ensures these blades withstand the demanding environment.
- Heat Exchangers: Transferring heat efficiently is crucial in power generation. IN939 powder’s ability to maintain strength at high temperatures makes it suitable for heat exchanger components.
Automotive:
- Turbocharger Components: Modern turbochargers extract more power from engines by compressing air at high temperatures. IN939 powder brings its high-temperature prowess to these critical components.
- Exhaust Manifolds: Hot exhaust gases flow through exhaust manifolds. IN939 powder’s resistance to heat and corrosion makes it a valuable material for this application.
Oil & Gas:
- Downhole Drilling Tools: Drilling deep into the earth exposes tools to extreme temperatures and pressure. IN939 powder’s strength and heat resistance make it suitable for downhole tools.
- Wellhead Components: The wellhead is the control center of an oil or gas well, and it experiences significant pressure and heat. IN939 powder can be used for wellhead components that demand exceptional durability.
Defense:
- Rocket Engine Components: Rockets soar into the sky thanks to the immense power of their engines. IN939 powder can be used in specific rocket engine components that face extreme heat and pressure.
- Hypersonic Vehicle Components: Hypersonic vehicles travel at blistering speeds, generating significant heat. IN939 powder’s high-temperature capabilities can be beneficial for certain components in these advanced vehicles.
These are just a few examples, and as 3D printing technology matures, we can expect to see IN939 powder conquer even more challenging applications in the future.
Metal Powders for High-Temperature 3D Printing
While IN939 powder shines brightly, it’s not the only contender in the high-temperature 3D printing arena. Here’s a comparison of some other noteworthy metal powders:
Metal Powder | Chemical Composition | Key Properties | Applications | Advantages vs. IN939 | Disadvantages vs. IN939 |
---|---|---|---|---|---|
Inconel 625 | Ni-Cr-Mo-Nb | Excellent high-temperature strength, good oxidation resistance | Turbine blades, combustor liners, heat exchangers | More readily available, lower cost | Lower creep resistance, lower strength at very high temperatures |
Inconel 718 | Ni-Cr-Fe-Nb | High strength, good corrosion resistance | Aerospace components, heat exchangers, pressure vessels | Good balance of properties, versatile | Lower creep resistance than IN939 |
CMSX-4 | Co-Ni-Ta-Al | Exceptional creep resistance, excellent oxidation resistance | Turbine blades for advanced jet engines | Superior creep resistance at very high temperatures | Higher cost, more challenging to process |
CM247LC | Ni-Cr-Co-Mo-W | Excellent creep resistance, good oxidation resistance | Land-based turbine blades | Favorable creep resistance for power generation applications | Lower strength than IN939, less common |
AM300 | Ni-Cr-Ti | Good high-temperature strength, moderate creep resistance | Aerospace components, heat exchangers | Favorable balance of properties for some applications | Lower creep resistance and oxidation resistance than IN939 |
This table provides a glimpse into the diverse landscape of metal powders for high-temperature 3D printing. The choice of material depends on the specific application’s requirements, considering factors like temperature range, desired properties, and cost constraints.
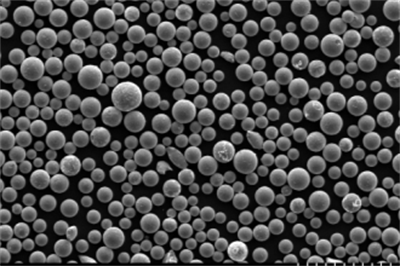
Specifications, Sizes, Grades, and Standards for IN939 Powder
IN939 powder comes in various specifications to cater to different needs. Here’s a breakdown of some key parameters:
- Particle Size: The size of the powder particles significantly impacts the printability and final properties of the 3D-printed component. IN939 powder is typically available in particle sizes ranging from 15 to 50 micrometers.
- Grades: Depending on the manufacturer, IN939 powder might be offered in different grades with slight variations in composition to optimize printability or specific properties.
- Standards: IN939 powder typically adheres to industry standards like ASTM International (ASTM) or Aerospace Material Specifications (AMS) standards, ensuring consistent quality and performance.
Here’s a table summarizing the specifications for IN939 powder:
Parameter | Description |
---|---|
Particle Size | 15 – 50 micrometers (typical range) |
Grades | May vary depending on manufacturer, optimized for printability or specific properties |
Standards | ASTM International (ASTM) or Aerospace Material Specifications (AMS) |
Availability and Pricing of IN939 Powder
Due to its specialized nature, IN939 powder might not be readily available from every metal powder supplier. However, several reputable manufacturers offer this material. Here’s a table outlining some potential suppliers and indicative pricing information (please note that pricing can vary depending on quantity, market conditions, and specific vendor):
Supplier | Website | Price Range (per kg) |
---|---|---|
Supplier 1: https://am-material.com/alloy-powder-in939/[IN939 Nickel Alloy Powder Supplier] | https://am-material.com/alloy-powder-in939/ | $300 – $500 |
Supplier 2: https://am-material.com/alloy-powder-in939/[IN939 Nickel Superalloy Powder Supplier] | https://am-material.com/alloy-powder-in939/ | $350 – $600 |
Supplier 3: https://am-printing.com/[IN939 Alloy Powder Manufacturer] | https://am-printing.com/ | Contact supplier for quote |
It’s important to remember that these are just a few examples, and the actual pricing can vary depending on the factors mentioned earlier. Always consult with potential suppliers for the latest pricing information and to discuss your specific requirements.
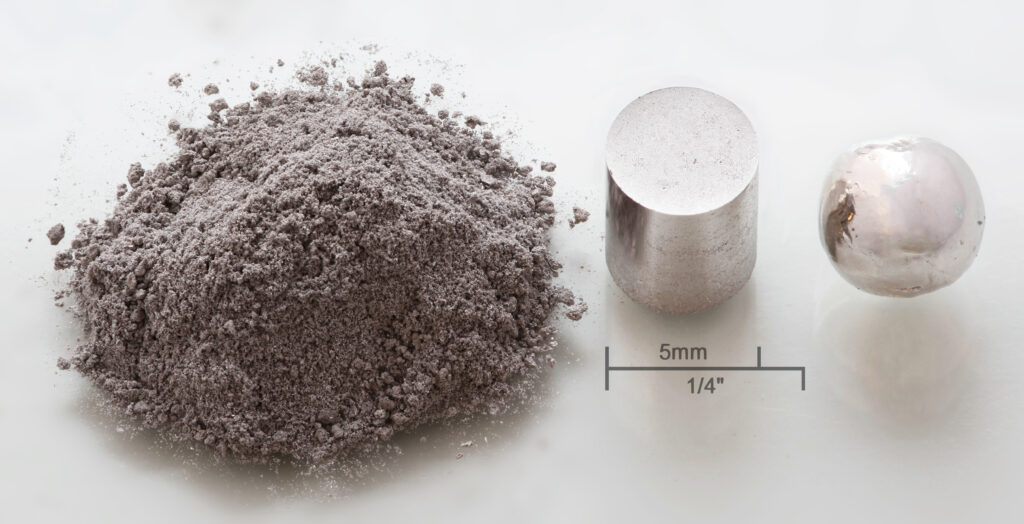
FAQs
Here are some frequently asked questions about IN939 powder, presented in a question-and-answer format for easy reference:
Q: What is IN939 powder used for?
A: IN939 powder is a nickel-based superalloy powder specifically designed for high-temperature 3D printing applications. It’s used in various industries, including aerospace, power generation, automotive, oil & gas, and defense, for components that experience extreme heat and stress.
Q: What are the advantages of using IN939 powder in 3D printing?
A: IN939 powder boasts exceptional strength, oxidation resistance, creep resistance, and fatigue strength at high temperatures. Additionally, 3D printing allows for the creation of complex geometries that were previously impossible with traditional manufacturing methods.
Q: What are the disadvantages of using IN939 powder in 3D printing?
A: The primary drawbacks of IN939 powder are its higher cost compared to some other metal powders and the challenges associated with 3D printing due to its high melting point and sensitivity to processing parameters. Additionally, IN939 powder might have slightly lower availability compared to more widely used metal powders.
Q: How does IN939 powder compare to other metal powders for high-temperature 3D printing?
A: Several other metal powders are suitable for high-temperature 3D printing, each with its own strengths and weaknesses. Inconel 625 offers a good balance of properties and is more readily available, while CMSX-4 boasts superior creep resistance at very high temperatures but comes at a higher cost. The best choice depends on the specific application’s requirements.
Q: Where can I buy IN939 powder?
A: IN939 powder might not be available from every metal powder supplier due to its specialized nature. However, several reputable manufacturers offer this material. It’s recommended to contact potential suppliers directly to discuss your needs and obtain the latest pricing information.
Conclusion
IN939 powder stands as a testament to the cutting edge of 3D printing technology. Its exceptional properties unlock possibilities for creating high-performance components that can withstand the harshest environments. As 3D printing continues to evolve, IN939 powder is poised to play a vital role in revolutionizing various industries where battling extreme heat and stress is an everyday challenge.