Overview of Bonded Powder
Bonded powder, a key material in various industrial applications, is produced by bonding fine metal particles together, often using a binder or through mechanical means. This process results in powders that exhibit enhanced flowability, stability, and performance characteristics compared to traditional, non-bonded powders. Whether you’re delving into additive manufacturing, powder metallurgy, or surface coating, bonded powders offer unique advantages that can significantly impact your project’s success.
Why Choose Bonded Powder?
Bonded powders are known for their consistent particle size distribution and improved handling properties, which are crucial in high-precision industries. Their enhanced flowability makes them ideal for processes like 3D printing and metal injection molding, where uniform material deposition is critical.
Types and Composition of Bonded Powder
Different bonded powders are tailored for specific applications, each with unique compositions and characteristics. Here’s a detailed look at some common types of bonded metal powders:
Metal Powder Model | Composition | Properties | Applications |
---|---|---|---|
316L Stainless Steel | Iron, Chromium, Nickel, Molybdenum | Corrosion resistance, high strength | Medical implants, food processing equipment |
CuSn10 (Phosphor Bronze) | Copper, Tin, Phosphorus | High wear resistance, low friction | Bearings, bushings |
AlSi10Mg (Aluminum Alloy) | Aluminum, Silicon, Magnesium | Lightweight, good thermal conductivity | Aerospace parts, automotive components |
Ti-6Al-4V (Titanium Alloy) | Titanium, Aluminum, Vanadium | High strength-to-weight ratio, biocompatibility | Aerospace, medical devices |
Inconel 718 | Nickel, Chromium, Iron, Molybdenum | High temperature resistance, corrosion resistance | Turbine blades, jet engines |
FeNiCo (Kovar) | Iron, Nickel, Cobalt | Low thermal expansion, high strength | Electronic packaging, glass-to-metal seals |
WC-Co (Tungsten Carbide-Cobalt) | Tungsten, Cobalt | High hardness, wear resistance | Cutting tools, mining equipment |
316L SS/Ni (Stainless Steel/Nickel) | Stainless Steel, Nickel | Enhanced corrosion resistance, improved ductility | Oil & gas, marine environments |
CuNi2Si (Copper-Nickel-Silicon) | Copper, Nickel, Silicon | High strength, electrical conductivity | Electrical contacts, connectors |
FeNiCr (Nickel-Chrome Steel) | Iron, Nickel, Chromium | High strength, oxidation resistance | Industrial machinery, automotive parts |
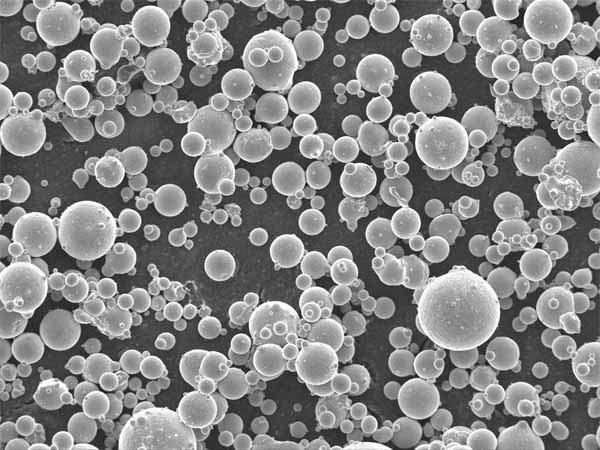
Characteristics of Bonded Powder
Enhanced Flowability
Bonded powders exhibit superior flowability compared to non-bonded counterparts. This property is critical in processes like powder metallurgy and additive manufacturing, where consistent material deposition is essential.
Uniform Particle Size Distribution
The bonding process ensures a more uniform particle size distribution, which contributes to better packing density and reduced porosity in the final product. This results in higher mechanical properties and better surface finishes.
Improved Stability and Handling
Bonded powders are less prone to segregation and dusting, making them safer and easier to handle. This is particularly important in industries where precise material control is necessary.
Optimal Performance in High-Precision Applications
From 3D printing to metal injection molding, bonded powders deliver the consistency and reliability required for high-precision applications. Their properties can be fine-tuned to meet specific performance criteria, ensuring optimal results.
Applications of Bonded Powder
Bonded powders are utilized across a wide range of industries. Here’s a breakdown of their applications:
Application | Description | Commonly Used Powders |
---|---|---|
Additive Manufacturing | Used in 3D printing for creating complex, high-precision parts | 316L Stainless Steel, Ti-6Al-4V, Inconel 718 |
Powder Metallurgy | Employed in the production of metal parts through compaction and sintering | CuSn10, AlSi10Mg, WC-Co |
Metal Injection Molding | Combines the benefits of plastic injection molding with powder metallurgy | FeNiCo, CuNi2Si, FeNiCr |
Surface Coating | Enhances surface properties such as wear resistance and corrosion resistance | 316L SS/Ni, WC-Co, Inconel 718 |
Medical Devices | Used in the manufacturing of biocompatible implants and instruments | Ti-6Al-4V, 316L Stainless Steel |
Aerospace Components | Critical for producing lightweight, high-strength parts | AlSi10Mg, Ti-6Al-4V, Inconel 718 |
Automotive Parts | Improves performance and durability of components | FeNiCr, AlSi10Mg, CuNi2Si |
Specifications, Sizes, and Grades
Bonded powders come in various specifications, sizes, and grades to meet diverse industry needs. Here’s an overview:
Powder Model | Particle Size Range (µm) | Grade | Standard |
---|---|---|---|
316L Stainless Steel | 15-45, 45-106 | Grade A, Grade B | ASTM F138, ISO 5832-1 |
CuSn10 (Phosphor Bronze) | 20-63 | Grade 1, Grade 2 | ASTM B505, ISO 1338 |
AlSi10Mg (Aluminum Alloy) | 20-60 | Grade A | ASTM B209, ISO 3522 |
Ti-6Al-4V (Titanium Alloy) | 15-45, 45-106 | Grade 5 | ASTM F136, ISO 5832-3 |
Inconel 718 | 15-53 | Grade A | ASTM B637, ISO 15156-3 |
FeNiCo (Kovar) | 20-60 | Grade A | ASTM F15, ISO 10027 |
WC-Co (Tungsten Carbide-Cobalt) | 10-40 | Grade A | ASTM B777, ISO 1302 |
316L SS/Ni (Stainless Steel/Nickel) | 15-45 | Grade A | ASTM B927, ISO 5832-1 |
CuNi2Si (Copper-Nickel-Silicon) | 20-63 | Grade A | ASTM B422, ISO 1338 |
FeNiCr (Nickel-Chrome Steel) | 15-45 | Grade A | ASTM B700, ISO 15156-3 |
Suppliers and Pricing Details
Here’s a table summarizing suppliers and indicative pricing for different bonded powders:
Supplier | Powder Model | Price per kg (USD) | Location |
---|---|---|---|
Höganäs AB | 316L Stainless Steel | $50 | Sweden |
GKN Hoeganaes | CuSn10 (Phosphor Bronze) | $60 | USA |
LPW Technology | AlSi10Mg (Aluminum Alloy) | $45 | UK |
Carpenter Technology | Ti-6Al-4V (Titanium Alloy) | $150 | USA |
Sandvik | Inconel 718 | $200 | Sweden |
Advanced Powders & Coatings (AP&C) | FeNiCo (Kovar) | $80 | Canada |
HC Starck | WC-Co (Tungsten Carbide-Cobalt) | $100 | Germany |
Oerlikon Metco | 316L SS/Ni (Stainless Steel/Nickel) | $70 | Switzerland |
Metal Powder and Process Ltd | CuNi2Si (Copper-Nickel-Silicon) | $55 | UK |
Arcam AB | FeNiCr (Nickel-Chrome Steel) | $65 | Sweden |
Advantages and Limitations of Bonded Powder
When selecting bonded powders, it’s essential to understand their advantages and limitations:
Aspect | Advantages | Limitations |
---|---|---|
Flowability | Enhanced flowability | May require specific handling conditions |
Uniformity | Consistent particle size distribution | Potential for higher cost |
Stability | Improved handling and reduced dusting | Limited to specific applications |
Performance | Better mechanical properties and surface finish | May require special equipment for processing |
Safety | Safer to handle due to reduced dust | Not suitable for all environments |
Key Considerations When Choosing Bonded Powder
Performance Requirements
Consider the mechanical properties and performance characteristics needed for your application. For example, aerospace components demand high strength and low weight, making materials like Ti-6Al-4V ideal.
Processing Methods
Ensure compatibility with your processing methods. Additive manufacturing may require different powder characteristics compared to traditional powder metallurgy.
Cost and Availability
Factor in the cost and availability of the powder. While high-performance powders like Inconel 718 offer excellent properties, they may come at a premium price.
Supplier Reliability
Choose suppliers known for their quality and reliability. Consistent supply and adherence to standards are crucial for maintaining production quality.
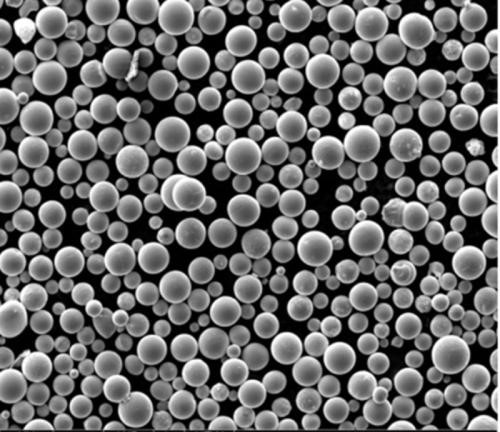
FAQ
What is bonded powder?
Bonded powder is a type of metal powder where fine particles are bonded together, often using a binder, to enhance flowability and performance.
What are the benefits of using bonded powder?
Bonded powders offer enhanced flowability, uniform particle size distribution, improved stability, and better performance in high-precision applications.
Which industries use bonded powder?
Industries such as aerospace, automotive, medical devices, additive manufacturing, powder metallurgy, and surface coating commonly use bonded powders.
How is bonded powder made?
Bonded powder is made by mechanically bonding fine metal particles together, often using a binder or through mechanical means.
What should I consider when selecting a bonded powder?
Consider the performance requirements, compatibility with processing methods, cost and availability, and supplier reliability.
Are bonded powders more expensive than non-bonded powders?
Generally, bonded powders can be more expensive due to their enhanced properties and processing methods. However, their benefits often justify the cost in high-precision applications.
Can bonded powder be used in 3D printing?
Yes, bonded powders are ideal for 3D printing due to their enhanced flowability and consistent particle size distribution.
What are some common types of bonded powder?
Common types include 316L Stainless Steel, CuSn10 (Phosphor Bronze), AlSi10Mg (Aluminum Alloy), Ti-6Al-4V (Titanium Alloy), and Inconel 718.
What is the difference between bonded and non-bonded powder?
Bonded powder has enhanced flowability, stability, and uniformity compared to non-bonded powder, making it more suitable for high-precision applications.
Where can I buy bonded powder?
Bonded powders can be purchased from specialized suppliers such as Höganäs AB, GKN Hoeganaes, LPW Technology, Carpenter Technology, and Sandvik.
Conclusion
Bonded powders are a versatile and high-performance solution for various industrial applications. Their unique properties, such as enhanced flowability, uniform particle size distribution, and improved stability, make them indispensable in fields like additive manufacturing, powder metallurgy, and surface coating. By understanding the types, characteristics, and applications of bonded powders, you can make informed decisions that optimize your project’s outcomes. Whether you’re developing aerospace components, medical devices, or automotive parts, bonded powders offer the consistency and reliability you need for success.
Remember, the key to leveraging the full potential of bonded powders lies in selecting the right type and working with reputable suppliers to ensure quality and reliability.