Highly spherical powders are critical in various high-tech applications ranging from additive manufacturing to aerospace engineering. Their unique shape and properties make them a favorite among engineers and manufacturers. This guide delves into the nitty-gritty of highly spherical powders, covering everything from types and compositions to applications and suppliers. So, buckle up and get ready to dive deep into the fascinating world of highly spherical powders!
Overview of Highly Spherical Powder
Highly spherical powders are characterized by their near-perfect spherical shape, which provides numerous advantages in terms of flowability, packing density, and uniformity. These powders are used in various industries, including aerospace, automotive, biomedical, and electronics, due to their superior performance characteristics.
Key Benefits of Highly Spherical Powder
- Improved Flowability: The spherical shape allows the powder to flow more easily and consistently.
- Higher Packing Density: Spherical particles can be packed more tightly, leading to higher density in finished products.
- Enhanced Mechanical Properties: Uniform particle size and shape contribute to better mechanical properties in manufactured components.
- Reduced Wear and Tear: Lower friction between spherical particles results in less wear and tear on equipment during processing.
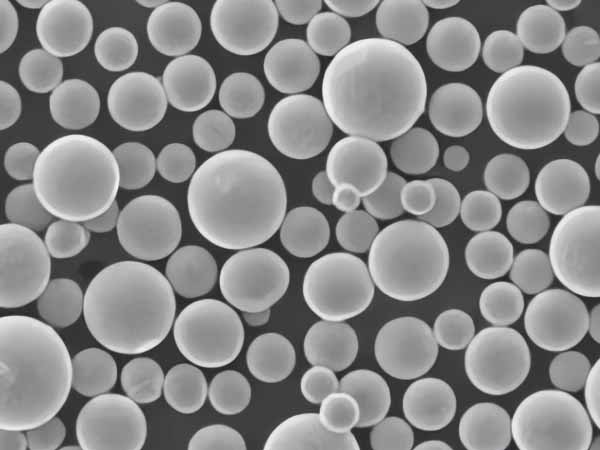
Types of Highly Spherical Powder
Highly spherical powders come in various compositions and grades, each tailored for specific applications. Let’s explore some of the most common types:
Table: Types and Compositions of Highly Spherical Powder
Type | Composition | Properties | Applications |
---|---|---|---|
Aluminum Powder | Pure Al or Al alloys | Lightweight, high conductivity | Aerospace, automotive, electronics |
Titanium Powder | Pure Ti or Ti alloys | High strength, corrosion resistance | Biomedical implants, aerospace components |
Nickel Powder | Pure Ni or Ni alloys | High temperature stability, corrosion resistance | Gas turbines, batteries, aerospace |
Copper Powder | Pure Cu or Cu alloys | High conductivity, thermal properties | Electrical components, heat sinks |
Stainless Steel Powder | Fe-Cr-Ni alloys | Corrosion resistance, mechanical strength | Medical devices, automotive, construction |
Cobalt Powder | Pure Co or Co alloys | High wear resistance, magnetic properties | Hard facing, magnets, aerospace |
Iron Powder | Pure Fe or Fe alloys | High strength, magnetic properties | Automotive, machinery, electronics |
Tungsten Powder | Pure W or W alloys | High density, high melting point | Radiation shielding, aerospace, military |
Chromium Powder | Pure Cr or Cr alloys | Corrosion resistance, hardness | Surface coatings, alloying |
Zinc Powder | Pure Zn or Zn alloys | Corrosion resistance, low melting point | Galvanizing, battery electrodes |
Characteristics of Highly Spherical Powder
The unique characteristics of highly spherical powders make them indispensable in various high-precision applications. Here are some key characteristics:
- Particle Size Distribution: Highly spherical powders often have a narrow particle size distribution, which ensures uniformity in the end product.
- Surface Area: The spherical shape reduces the surface area compared to irregularly shaped powders, enhancing flowability and reducing oxidation.
- Purity: High purity levels are essential for specific applications, especially in the aerospace and biomedical fields.
- Density: The packing density of spherical powders is typically higher, which is crucial for applications requiring high material density.
Table: Properties and Characteristics of Highly Spherical Powder
Property | Description |
---|---|
Shape | Spherical |
Particle Size Distribution | Narrow, uniform |
Surface Area | Lower compared to irregular powders |
Density | High packing density |
Purity | High, essential for critical applications |
Flowability | Excellent due to spherical shape |
Applications of Highly Spherical Powder
Highly spherical powders are used in various applications due to their unique properties. Here are some of the key applications:
Table: Applications and Uses of Highly Spherical Powder
Application | Description |
---|---|
Additive Manufacturing | Used in 3D printing for creating complex geometries with high precision |
Aerospace Engineering | Critical for manufacturing lightweight, high-strength components |
Biomedical Implants | Used in making implants due to biocompatibility and mechanical properties |
Electronics | Essential for creating high-conductivity components |
Automotive Industry | Used in making lightweight, durable parts |
Energy Sector | Utilized in batteries, fuel cells, and other energy storage devices |
Surface Coatings | Applied for enhancing corrosion resistance and wear resistance |
Grades and Specifications of Highly Spherical Powder
Different grades and specifications of highly spherical powders are available to meet the diverse requirements of various applications. These specifications include particle size, purity, and composition.
Table: Specifications, Sizes, Grades, and Standards of Highly Spherical Powder
Specification | Description |
---|---|
Particle Size | Varies from nano to micron size, depending on application |
Purity | Typically >99% |
Composition | Pure metals or alloys |
Standards | ASTM, ISO, AMS |
Grades | Multiple grades available based on specific requirements |
Suppliers and Pricing Details of Highly Spherical Powder
Finding the right supplier for highly spherical powder is crucial to ensure quality and consistency. Here are some leading suppliers and their pricing details:
Table: Suppliers and Pricing Details of Highly Spherical Powder
Supplier | Location | Product Range | Pricing (per kg) |
---|---|---|---|
Sandvik | Sweden | Metal powders for AM | $200 – $500 |
Carpenter Technology | USA | High-performance alloys | $300 – $700 |
GKN Powder Metallurgy | Germany | Various metal powders | $250 – $600 |
AP&C (GE Additive) | Canada | Titanium and other metal powders | $350 – $800 |
Höganäs AB | Sweden | Iron and steel powders | $150 – $400 |
ECKART | Germany | Aluminum powders | $100 – $300 |
Valimet | USA | Aluminum and titanium powders | $250 – $600 |
Tekna | Canada | Spherical powders for AM | $400 – $900 |
Praxair Surface Technologies | USA | Nickel and cobalt-based powders | $300 – $700 |
LPW Technology | UK | Metal powders for AM | $350 – $800 |
Pros and Cons of Highly Spherical Powder
While highly spherical powders offer numerous advantages, there are also some limitations to consider. Here’s a detailed comparison of their pros and cons:
Table: Advantages and Limitations of Highly Spherical Powder
Aspect | Advantages | Limitations |
---|---|---|
Flowability | Excellent due to spherical shape | Can be expensive due to manufacturing process |
Packing Density | High, leading to denser materials | Limited availability for some specific alloys |
Mechanical Properties | Enhanced due to uniform particle size | Higher cost compared to irregular powders |
Purity | High purity levels | Processing challenges for certain applications |
Applications | Suitable for high-tech applications | Requires precise handling and storage conditions |
Top 10 Metal Powder Models
Now, let’s dive into some specific metal powder models that are highly regarded in the industry for their performance and reliability:
- Aluminum Alloy Powder (AlSi10Mg)
- Description: A widely used aluminum alloy powder in additive manufacturing, known for its excellent mechanical properties and lightweight.
- Applications: Aerospace, automotive, and consumer electronics.
- Characteristics: High strength, good thermal conductivity, and corrosion resistance.
- Titanium Alloy Powder (Ti6Al4V)
- Description: A high-strength titanium alloy powder commonly used in aerospace and biomedical applications.
- Applications: Aircraft components, medical implants, and high-performance automotive parts.
- Characteristics: Superior strength-to-weight ratio, excellent biocompatibility.
- Nickel Alloy Powder (Inconel 718)
- Description: A nickel-chromium alloy powder known for its high temperature and corrosion resistance.
- Applications: Gas turbines, aerospace engines, and nuclear reactors.
- Characteristics: High strength, resistance to oxidation and corrosion at high temperatures.
- Copper Alloy Powder (CuCr1Zr)
- Description: A copper alloy powder with high electrical and thermal conductivity, used in electronics and heat exchangers.
- Applications: Electrical connectors, heat sinks, and welding electrodes.
- Characteristics: Excellent conductivity, good mechanical properties, and wear resistance.
- Stainless Steel Powder (316L)
- Description: A widely used stainless steel powder known for its corrosion resistance and mechanical properties.
- Applications: Medical devices, food processing equipment, and automotive parts.
- Characteristics: High corrosion resistance, good mechanical properties, and biocompatibility.
- Cobalt Alloy Powder (CoCrMo)
- Description: A cobalt-chromium-molybdenum alloy powder used in biomedical implants and high-wear applications.
- Applications: Orthopedic implants, dental devices, and aerospace components.
- Characteristics: High wear resistance, excellent biocompatibility, and strength.
- Iron Alloy Powder (Fe-Ni)
- Description: An iron-nickel alloy powder with high magnetic properties, used in electronic and automotive industries.
- Applications: Transformers, inductors, and electric motors.
- Characteristics: High magnetic permeability, good mechanical strength.
- Tungsten Alloy Powder (W-Ni-Fe)
- Description: A tungsten alloy powder with high density and excellent mechanical properties, used in aerospace and military applications.
- Applications: Radiation shielding, kinetic energy penetrators, and aerospace components.
- Characteristics: High density, excellent strength, and corrosion resistance.
- Chromium Alloy Powder (Cr-Co)
- Description: A chromium-cobalt alloy powder used in surface coatings and high-wear applications.
- Applications: Hard-facing, surface coatings, and industrial machinery.
- Characteristics: High hardness, excellent wear and corrosion resistance.
- Zinc Alloy Powder (Zn-Al)
- Description: A zinc-aluminum alloy powder used in galvanizing and battery applications.
- Applications: Galvanized coatings, battery electrodes, and sacrificial anodes.
- Characteristics: Good corrosion resistance, low melting point, and good electrical conductivity.
Comparing Highly Spherical Powder Models
When choosing the right highly spherical powder for your application, it’s essential to compare their properties and performance. Here’s a comparison of the top metal powder models:
Table: Comparison of Highly Spherical Powder Models
Model | Composition | Applications | Characteristics | Pricing |
---|---|---|---|---|
AlSi10Mg | Al-Si-Mg | Aerospace, automotive, electronics | Lightweight, high strength | $200 – $400 |
Ti6Al4V | Ti-Al-V | Aerospace, biomedical | High strength, biocompatibility | $400 – $800 |
Inconel 718 | Ni-Cr | Gas turbines, aerospace, nuclear | High temperature resistance | $600 – $1000 |
CuCr1Zr | Cu-Cr-Zr | Electronics, heat exchangers | High conductivity | $250 – $500 |
316L | Fe-Cr-Ni-Mo | Medical, food processing, automotive | Corrosion resistance | $150 – $350 |
CoCrMo | Co-Cr-Mo | Biomedical, high-wear applications | Wear resistance, biocompatibility | $500 – $900 |
Fe-Ni | Fe-Ni | Electronics, automotive | High magnetic properties | $100 – $300 |
W-Ni-Fe | W-Ni-Fe | Aerospace, military | High density, strength | $700 – $1200 |
Cr-Co | Cr-Co | Surface coatings, machinery | Hardness, wear resistance | $200 – $500 |
Zn-Al | Zn-Al | Galvanizing, batteries | Corrosion resistance, conductivity | $100 – $300 |
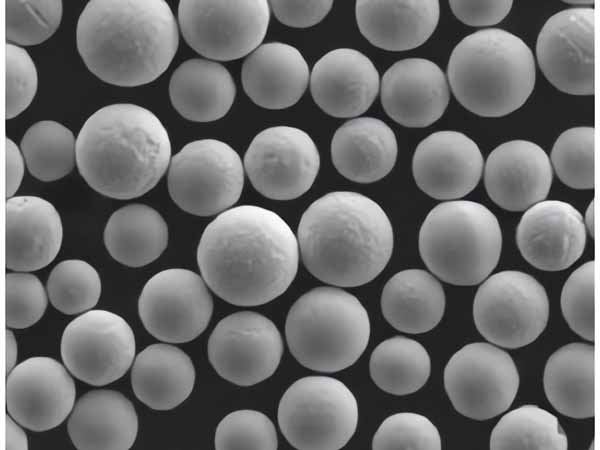
FAQ
Table: FAQ on Highly Spherical Powder
Question | Answer |
---|---|
What are highly spherical powders used for? | They are used in additive manufacturing, aerospace, biomedical implants, electronics, and more. |
Why are spherical powders preferred? | Their shape enhances flowability, packing density, and mechanical properties. |
How are highly spherical powders made? | Techniques include gas atomization, plasma atomization, and centrifugal atomization. |
What is the importance of particle size distribution? | A narrow distribution ensures uniformity and consistent properties in the final product. |
Are highly spherical powders expensive? | They can be more costly due to the manufacturing processes involved but offer superior performance. |
Which industries benefit most from these powders? | Aerospace, automotive, medical, and electronics industries benefit significantly. |
Can spherical powders be used in traditional manufacturing? | Yes, but they are particularly advantageous in advanced manufacturing like 3D printing. |
What are some common alloys used in spherical powders? | Aluminum, titanium, nickel, copper, stainless steel, cobalt, and iron alloys are common. |
How do I choose the right spherical powder for my application? | Consider factors like composition, particle size, purity, and specific application requirements. |
Where can I buy highly spherical powders? | Leading suppliers include Sandvik, Carpenter Technology, GKN Powder Metallurgy, AP&C, and Höganäs AB. |
Conclusion
Highly spherical powders are a game-changer in various high-tech applications due to their unique properties and advantages. From aerospace to biomedical implants, these powders play a crucial role in enhancing performance and efficiency. By understanding the types, characteristics, and applications of highly spherical powders, you can make informed decisions for your specific needs.
Whether you’re a manufacturer looking to optimize your production processes or an engineer seeking the best materials for your projects, highly spherical powders offer unparalleled benefits. Explore the options, compare the models, and choose the best powder that meets your requirements.