Overview of Spherical Powder
Spherical powders are becoming increasingly essential in various industries due to their unique properties and versatile applications. But what exactly makes spherical powder so special? Picture tiny, perfectly round grains of metal, like microscopic beads of uniform perfection. This precision is what allows spherical powders to excel in applications ranging from 3D printing to advanced aerospace components. In this comprehensive guide, we’ll dive deep into the world of spherical powders, exploring their types, compositions, properties, applications, and more. Let’s get started!
What is Spherical Powder?
Spherical powder refers to finely divided metal particles that are nearly perfectly spherical in shape. These powders are produced using various atomization processes, which result in their distinctive shape and uniformity. The benefits of spherical powders include improved flowability, higher packing density, and better performance in applications requiring precision and consistency.
Types and Composition of Spherical Powder
To give you a clearer picture of spherical powders, here’s a table summarizing the key types and their compositions:
Type | Composition | Characteristics |
---|---|---|
Stainless Steel Powder | Iron, Chromium, Nickel | Corrosion-resistant, durable |
Aluminum Powder | Pure Aluminum or Aluminum Alloys | Lightweight, excellent conductivity |
Titanium Powder | Pure Titanium or Titanium Alloys | High strength-to-weight ratio, biocompatible |
Nickel Powder | Pure Nickel or Nickel Alloys | Corrosion-resistant, high melting point |
Copper Powder | Pure Copper | Excellent electrical and thermal conductivity |
Cobalt-Chromium Powder | Cobalt, Chromium | High wear resistance, biocompatible |
Iron Powder | Pure Iron or Iron Alloys | Magnetic properties, good machinability |
Tungsten Powder | Pure Tungsten | High density, high melting point |
Bronze Powder | Copper, Tin | Good corrosion resistance, excellent machinability |
Inconel Powder | Nickel, Chromium, Molybdenum, Niobium | High temperature resistance, excellent strength |
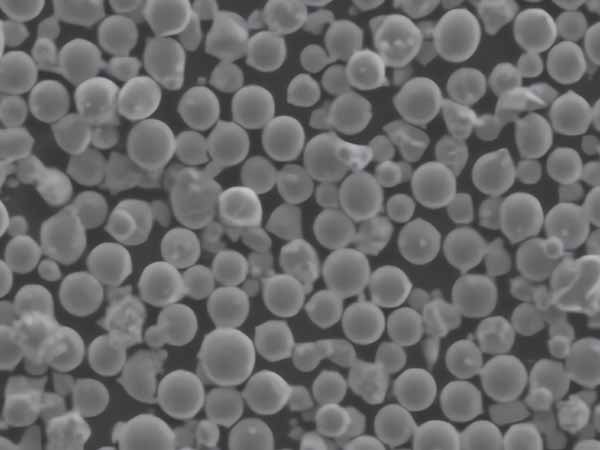
Characteristics of Spherical Powder
What sets spherical powder apart from other types of powders? Let’s delve into some of their unique characteristics:
- Flowability: Spherical powders flow more easily compared to irregularly shaped powders, making them ideal for processes like additive manufacturing and powder metallurgy.
- Packing Density: Due to their shape, spherical powders pack more densely, which is beneficial for producing high-density components.
- Uniformity: The consistent shape and size of spherical powders result in uniform properties across the produced parts.
- Surface Area: Spherical powders have a lower surface area-to-volume ratio, which can influence their reactivity and sintering behavior.
Applications of Spherical Powder
Spherical powders find applications in various industries due to their unique properties. Here’s a detailed look at some of their common uses:
Application | Description |
---|---|
Additive Manufacturing | Used in 3D printing for producing complex, high-precision parts |
Powder Metallurgy | Employed to create high-density metal components |
Thermal Spraying | Used for coating surfaces to improve wear and corrosion resistance |
Electronics | Utilized in the production of conductive pastes and components |
Aerospace | Essential for manufacturing lightweight, high-strength components |
Medical Devices | Used in implants and prosthetics due to biocompatibility |
Chemical Catalysts | Act as catalysts in various chemical reactions |
Sintering | Employed in the sintering process to create dense, uniform parts |
Automotive | Used in the production of high-performance automotive parts |
Energy Storage | Utilized in batteries and fuel cells for improved performance |
Grades of Spherical Powder
Different applications require different grades of spherical powder. Here’s a table outlining some common grades and their specifications:
Grade | Material | Particle Size | Purity | Standards |
---|---|---|---|---|
SS316L | Stainless Steel | 15-45 µm | >99.5% | ASTM B243 |
AlSi10Mg | Aluminum Alloy | 20-60 µm | >99.7% | ISO 20902-1 |
Ti64 | Titanium Alloy | 10-45 µm | >99.9% | ASTM F2924 |
Ni625 | Nickel Alloy | 15-53 µm | >99.5% | AMS 5666 |
Cu | Copper | 20-50 µm | >99.8% | ASTM B216 |
WC-Co | Tungsten Carbide | 10-45 µm | >99.5% | ISO 3878 |
In718 | Nickel Alloy | 15-53 µm | >99.5% | AMS 5662 |
Fe | Iron | 20-60 µm | >99.5% | ISO 4497 |
CoCr | Cobalt-Chromium | 15-45 µm | >99.7% | ASTM F75 |
Bronze | Copper-Tin | 20-50 µm | >99.8% | ISO 11714-2 |
Suppliers and Pricing Details of Spherical Powder
Finding the right supplier is crucial for obtaining high-quality spherical powders. Here’s a table with some notable suppliers and their pricing details:
Supplier | Materials Offered | Pricing (per kg) | Location | Website |
---|---|---|---|---|
Höganäs | Iron, Stainless Steel, Copper | $30 – $100 | Sweden | www.hoganas.com |
Carpenter Additive | Nickel, Titanium, Aluminum | $150 – $500 | USA | www.carpenteradditive.com |
LPW Technology | Nickel, Stainless Steel, Aluminum | $100 – $400 | UK | www.lpwtechnology.com |
Sandvik | Stainless Steel, Titanium | $50 – $300 | Sweden | www.materials.sandvik |
GKN Hoeganaes | Iron, Nickel, Copper | $40 – $200 | USA | www.gknpm.com |
EOS | Stainless Steel, Titanium, Aluminum | $120 – $450 | Germany | www.eos.info |
AP&C | Titanium, Aluminum | $200 – $600 | Canada | www.advancedpowders.com |
Praxair | Nickel, Stainless Steel, Aluminum | $100 – $400 | USA | www.praxairsurfacetechnologies.com |
Arcam AB | Titanium, Nickel | $150 – $500 | Sweden | www.arcam.com |
Aubert & Duval | Nickel, Titanium, Stainless Steel | $120 – $450 | France | www.aubertduval.com |
Advantages and Limitations of Spherical Powder
Like any material, spherical powders have their pros and cons. Here’s a comparative look:
Aspect | Advantages | Limitations |
---|---|---|
Flowability | Excellent due to spherical shape | None significant |
Packing Density | Higher packing density compared to irregular powders | Limited by particle size distribution |
Uniformity | Consistent properties across parts | May require precise production controls |
Surface Area | Lower surface area-to-volume ratio | May affect reactivity in some applications |
Cost | Generally higher due to production complexity | Higher upfront investment |
Application Range | Versatile in many industries | Specific grades may be needed for certain uses |
Comparison of Spherical Powder Models
When it comes to choosing the right spherical powder for your needs, understanding the differences between various models is crucial. Let’s compare some popular models:
Stainless Steel Powder vs. Aluminum Powder
- Composition: Stainless steel powders are typically made from iron, chromium, and nickel, while aluminum powders are made from pure aluminum or aluminum alloys.
- Characteristics: Stainless steel is corrosion-resistant and durable, whereas aluminum is lightweight and offers excellent conductivity.
- Applications: Stainless steel powders are ideal for applications requiring durability and corrosion resistance, such as in aerospace and medical devices. Aluminum powders are preferred in applications where weight reduction is critical, such as in automotive and aerospace components.
Titanium Powder vs. Nickel Powder
- Composition: Titanium powders are made from pure titanium or titanium alloys, while nickel powders are made from pure nickel or nickel alloys.
- Characteristics: Titanium offers a high strength-to-weight ratio and biocompatibility, making it suitable for medical implants and aerospace parts. Nickel is known for its high melting point and corrosion resistance, ideal for high-temperature applications.
- Applications: Titanium powders are used in the medical and aerospace industries, while nickel powders are prominent in thermal spraying and chemical catalysts.
FAQ
Here are some frequently asked questions about spherical powders:
Question | Answer |
---|---|
What is spherical powder used for? | Spherical powder is used in additive manufacturing, powder metallurgy, thermal spraying, and more. |
Why is spherical powder preferred in 3D printing? | Its excellent flowability and uniformity make it ideal for creating precise and high-quality parts. |
How is spherical powder made? | It is typically produced through atomization processes, such as gas or water atomization. |
What are the benefits of using spherical powder? | Improved flowability, higher packing density, and consistent properties across produced parts. |
Can spherical powder be recycled? | Yes, many spherical powders can be recycled, especially in additive manufacturing processes. |
What are the common materials for spherical powder? | Stainless steel, aluminum, titanium, nickel, copper, cobalt-chromium, iron, tungsten, and bronze. |
How do you store spherical powder? | It should be stored in a dry, cool place to prevent oxidation and contamination. |
What industries use spherical powder? | Aerospace, medical, automotive, electronics, and energy storage are some of the key industries. |
Is spherical powder expensive? | It can be more expensive than irregular powders due to the complexity of production. |
What are the limitations of spherical powder? | High cost and the need for precise production controls are some limitations. |
Conclusion
Spherical powders are a cornerstone of modern manufacturing, offering unparalleled advantages in terms of flowability, packing density, and uniformity. By understanding the different types, compositions, properties, and applications, you can make informed decisions about which spherical powder is best suited for your needs. Whether you’re in aerospace, medical devices, or any other industry, spherical powders can provide the performance and reliability you require. Happy manufacturing!