Overview of the Lifecycle of Metal Powder
Metal powder is a fundamental material in various industries, playing a crucial role in manufacturing processes like additive manufacturing (3D printing), powder metallurgy, and surface coating. Understanding the lifecycle of metal powder involves delving into its creation, applications, and eventual recycling or disposal. In this extensive guide, we will explore every facet of metal powder’s lifecycle, from production methods to specific models, applications, and beyond. We’ll also delve into the characteristics that make different types of metal powders unique, and the advantages and disadvantages of using them in different contexts.
Key Details:
- Production Methods: Atomization, chemical reduction, electrolysis, mechanical alloying
- Applications: Additive manufacturing, powder metallurgy, surface coatings, sintering
- Types of Metal Powders: Iron, steel, aluminum, titanium, cobalt-chromium, tungsten, nickel, copper, magnesium, stainless steel
- Lifecycle Stages: Production, usage, recycling, disposal
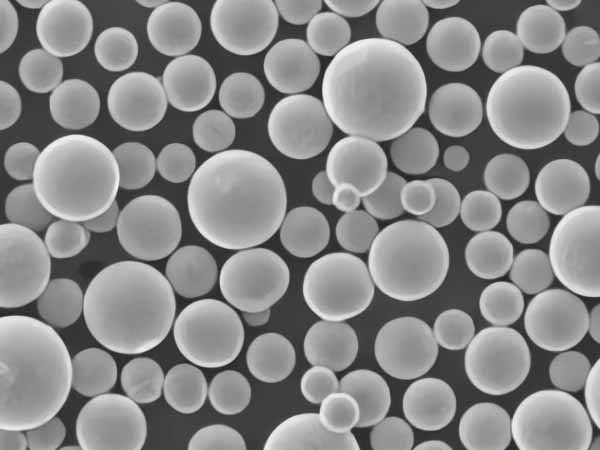
Types, Composition, and Properties of Metal Powder
Different types of metal powders have unique compositions and properties that make them suitable for specific applications. Below is a detailed table presenting various types of metal powders along with their composition, properties, and characteristics.
Table: Types, Composition, and Properties of Metal Powders
Metal Powder | Composition | Properties | Characteristics |
---|---|---|---|
Iron Powder | Pure iron or iron-carbon alloys | High magnetic permeability, high density | Common in powder metallurgy, cost-effective |
Steel Powder | Iron with carbon, manganese, chromium | High strength, wear resistance | Used in automotive and structural applications |
Aluminum Powder | Pure aluminum or aluminum alloys | Lightweight, high corrosion resistance | Key in aerospace, automotive industries |
Titanium Powder | Pure titanium or titanium alloys | High strength-to-weight ratio, biocompatible | Critical in aerospace, medical implants |
Cobalt-Chromium Powder | Cobalt, chromium, molybdenum | High wear resistance, biocompatible | Dental, orthopedic implants |
Tungsten Powder | Pure tungsten or tungsten carbide | High density, high melting point | Used in heavy-duty applications, radiation shielding |
Nickel Powder | Pure nickel or nickel alloys | Corrosion resistance, good mechanical properties | Aerospace, electronics, batteries |
Copper Powder | Pure copper or copper alloys | High electrical and thermal conductivity | Electronics, conductive inks |
Magnesium Powder | Pure magnesium or magnesium alloys | Lightweight, high strength | Automotive, aerospace for weight reduction |
Stainless Steel Powder | Iron, chromium, nickel | Corrosion resistance, durability | Widely used in medical, food processing industries |
Applications of Metal Powder
Metal powders are utilized across a diverse range of industries and applications. The following table highlights the primary uses of various metal powders in different sectors.
Table: Applications of Metal Powders
Industry | Metal Powder | Applications |
---|---|---|
Automotive | Steel, aluminum, iron | Gears, bearings, structural components |
Aerospace | Titanium, aluminum, nickel | Engine components, structural parts |
Medical | Cobalt-chromium, titanium, stainless steel | Implants, surgical instruments |
Electronics | Copper, nickel, silver | Conductive inks, electronic components |
Additive Manufacturing | Stainless steel, titanium, aluminum | Prototyping, complex parts |
Energy | Nickel, tungsten, iron | Battery components, nuclear shielding |
Consumer Goods | Aluminum, stainless steel, copper | Appliances, decorative items |
Construction | Iron, steel, aluminum | Structural elements, tools |
Defense | Tungsten, titanium, steel | Armor, ammunition, aerospace components |
Industrial Machinery | Iron, steel, tungsten | Wear parts, tools, machinery components |
Specifications, Sizes, Grades, and Standards of Metal Powder
Each type of metal powder comes in different specifications, sizes, grades, and adheres to various standards to meet industry requirements. Below is a table summarizing these details.
Table: Specifications, Sizes, Grades, and Standards of Metal Powders
Metal Powder | Specifications | Sizes | Grades | Standards |
---|---|---|---|---|
Iron Powder | ASTM B1, MPIF 01 | 1-200 μm | 1000, 2000 | ISO 4497 |
Steel Powder | ASTM B783, MPIF 35 | 10-500 μm | AISI 316L, 434L | ISO 4499 |
Aluminum Powder | ASTM B928, AA 10 | 5-150 μm | 6061, 7075 | AMS 4217 |
Titanium Powder | ASTM B348, AMS 4998 | 10-300 μm | Grade 1, Grade 5 | ISO 5832 |
Cobalt-Chromium Powder | ASTM F75, ISO 5832-4 | 15-250 μm | CoCrMo | ASTM F799 |
Tungsten Powder | ASTM B777, AMS 7725 | 1-100 μm | WC, W2C | ISO 4488 |
Nickel Powder | ASTM B561, ISO 9001 | 5-200 μm | Nickel 200, Inconel 625 | AMS 5666 |
Copper Powder | ASTM B216, ISO 4521 | 1-100 μm | C11000, C18200 | ASTM B848 |
Magnesium Powder | ASTM B92, AMS 4377 | 10-150 μm | AZ31B, AZ91D | ISO 3116 |
Stainless Steel Powder | ASTM B243, MPIF SS | 10-500 μm | 316L, 17-4PH | ISO 45001 |
-
0# Pure Nickel powder
-
NiCoCrAlY alloys powders
-
Rene 142 alloy-Rene Powder
-
Haynes 25 Haynes Powder
-
FGH95 Ni-base Alloy Powder | Nickel Alloy Powder
-
CMSX-4 Nickel Alloy Powder | Nickel Alloy Powder
-
Ni-Fe-Mo Soft Magnetic Powder | Nickel Alloy Powder
-
Ni-Cr-Mo Alloy Powder | Nickel Alloy Powder
-
Nickel Titanium Alloy Powder | Nickel Alloy Powder
Suppliers and Pricing Details of Metal Powder
Understanding where to source metal powders and their pricing is crucial for budgeting and procurement. Here’s a table detailing some prominent suppliers along with indicative pricing.
Table: Suppliers and Pricing Details of Metal Powders
Metal Powder | Supplier | Price (per kg) | Notes |
---|---|---|---|
Iron Powder | Höganäs AB | $5 – $10 | High purity, various grades |
Steel Powder | GKN Powder Metallurgy | $15 – $25 | Custom blends available |
Aluminum Powder | Alcoa Inc. | $20 – $35 | Aerospace grades |
Titanium Powder | ATI Powder Metals | $200 – $300 | Medical and aerospace grades |
Cobalt-Chromium Powder | Carpenter Technology | $250 – $400 | Medical implants |
Tungsten Powder | Buffalo Tungsten Inc. | $50 – $75 | High density applications |
Nickel Powder | Vale S.A. | $50 – $80 | Battery applications |
Copper Powder | Belmont Metals | $30 – $50 | Conductive applications |
Magnesium Powder | Magnesium Elektron | $60 – $90 | Lightweight applications |
Stainless Steel Powder | Sandvik Materials | $25 – $40 | Multiple industries |
Pros and Cons, Advantages and Limitations of Metal Powder
Metal powders offer various advantages and limitations depending on their type and application. Below is a comparison table illustrating these aspects.
Table: Pros and Cons, Advantages and Limitations of Metal Powders
Metal Powder | Advantages | Disadvantages |
---|---|---|
Iron Powder | Cost-effective, magnetic properties | Lower corrosion resistance |
Steel Powder | High strength, wear resistance | Heavier than other metals |
Aluminum Powder | Lightweight, corrosion-resistant | Lower strength compared to steel |
Titanium Powder | High strength-to-weight ratio, biocompatible | Expensive, difficult to process |
Cobalt-Chromium Powder | High wear resistance, biocompatible | Very expensive |
Tungsten Powder | Extremely high density, high melting point | Brittle, difficult to machine |
Nickel Powder | Excellent corrosion resistance, high-temperature stability | Expensive |
Copper Powder | High electrical conductivity, easy to process | Prone to oxidation |
Magnesium Powder | Lightweight, good strength | Highly reactive, flammable |
Stainless Steel Powder | Corrosion resistance, durable | Expensive compared to plain steel |
Characteristics of the Lifecycle of Metal Powder
The lifecycle of metal powder encompasses several stages, each with its unique characteristics and processes.
- Production: The creation of metal powder typically involves atomization (gas, water, or plasma), chemical reduction, electrolysis, and mechanical alloying. Each method produces powders with distinct properties suitable for various applications.
- Usage: Metal powders are employed in additive manufacturing, powder metallurgy, surface coatings, and sintering. The choice of powder depends on the specific requirements of the application, such as strength, corrosion resistance, or thermal properties.
- Recycling: The recycling of metal powder is a crucial aspect, especially in industries like aerospace and automotive, where sustainability is key. Recycled metal powders can often be reused in the same or different applications, reducing waste and environmental impact.
- Disposal: Proper disposal of metal powder, especially hazardous materials like magnesium and tungsten, is essential. Disposal methods must adhere to environmental regulations to prevent contamination and ensure safety.
Advantages of the Lifecycle of Metal Powder
The lifecycle of metal powder offers several benefits, particularly in modern manufacturing and engineering applications.
- Efficiency: Metal powders enable efficient manufacturing processes like 3D printing and powder metallurgy, reducing material wastage.
- Customization: Powders can be engineered with specific properties, allowing for tailored solutions in critical applications.
- Sustainability: Recycling metal powders helps in conserving resources and reducing environmental impact.
- Innovation: Advances in powder production and processing technologies drive innovation in various fields, from aerospace to medical implants.
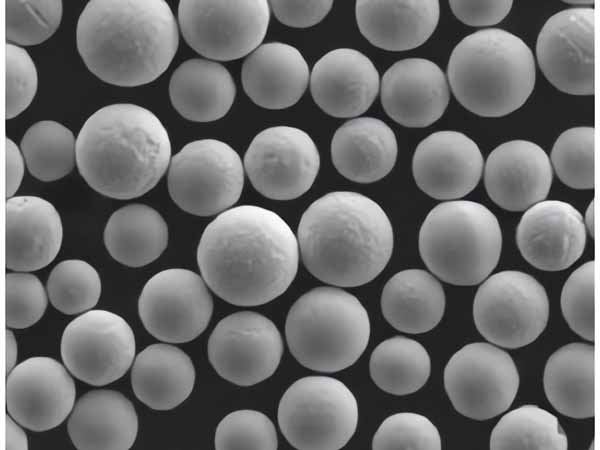
FAQ
Question | Answer |
---|---|
What are the primary methods of producing metal powders? | Atomization, chemical reduction, electrolysis, and mechanical alloying are the primary methods. |
Why are metal powders important in additive manufacturing? | They allow for precise and complex part creation with minimal material waste. |
How are metal powders recycled? | Metal powders are collected, purified, and reprocessed to be used again in similar or different applications. |
What are the environmental concerns related to metal powder disposal? | Improper disposal can lead to environmental contamination and health hazards. Adhering to regulations is essential. |
Can metal powders be customized for specific applications? | Yes, powders can be engineered to have specific properties such as strength, corrosion resistance, and thermal conductivity. |
In conclusion, the lifecycle of metal powder is a comprehensive process that spans production, usage, recycling, and disposal. Each stage has its unique characteristics and implications, especially in industries where precision, efficiency, and sustainability are paramount. Understanding these facets not only helps in better material selection and application but also promotes innovation and environmental responsibility. Whether you’re involved in aerospace, medical, automotive, or any other industry, mastering the nuances of metal powder can significantly enhance your manufacturing processes and product quality.