Laser Metal Deposition (LMD) is a groundbreaking technology in the realm of manufacturing and material science. This sophisticated process has revolutionized how we repair, coat, and manufacture metal parts. Let’s dive into the intricacies of LMD, exploring its types, composition, applications, and much more. Ready? Let’s get started.
Overview of Laser Metal Deposition (LMD)
Laser Metal Deposition (LMD) is an advanced additive manufacturing technique. It uses a high-power laser to melt metal powders, which are then deposited layer by layer to create a three-dimensional object. This method is incredibly versatile, allowing for precise control over the material properties and the geometry of the final product.
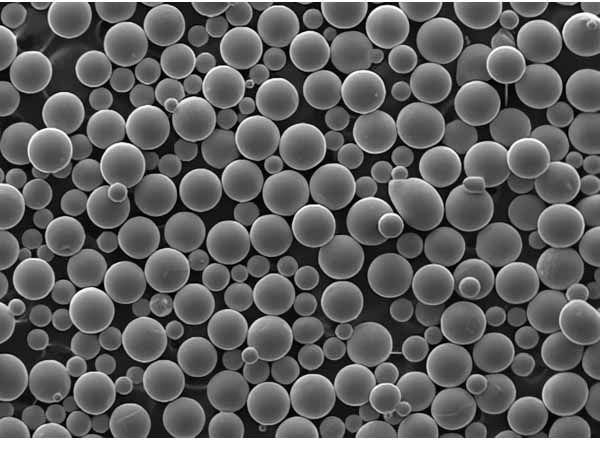
Types of Metal Powders for LMD
There is a variety of metal powders used in LMD, each with specific characteristics tailored for different applications. Here’s a detailed look at some of the most popular ones:
Metal Powder | Description |
---|---|
316L Stainless Steel | Known for its excellent corrosion resistance and mechanical properties. Ideal for medical devices and food processing equipment. |
Inconel 625 | A nickel-based superalloy with high strength and resistance to oxidation and corrosion. Used in aerospace and marine applications. |
Titanium Ti-6Al-4V | A high-strength alloy with excellent corrosion resistance. Commonly used in the aerospace, medical, and automotive industries. |
Aluminum AlSi10Mg | Lightweight with good mechanical properties and thermal conductivity. Used in automotive and aerospace applications. |
Cobalt-Chrome (CoCr) | Highly wear-resistant and biocompatible, making it ideal for dental and orthopedic implants. |
Tool Steel H13 | Known for its high hardness and resistance to thermal fatigue. Used in tooling and die applications. |
Copper Cu | Excellent thermal and electrical conductivity. Used in electrical components and heat exchangers. |
Nickel Alloy 718 | High strength and oxidation resistance at elevated temperatures. Used in gas turbines and other high-temperature applications. |
Stellite 6 | A cobalt-chromium alloy with excellent wear and corrosion resistance. Used in valve seats and bearings. |
Maraging Steel | Ultra-high strength with good toughness and weldability. Used in aerospace and tooling applications. |
Composition of Laser Metal Deposition (LMD)
The composition of the metal powders used in LMD plays a crucial role in determining the properties and performance of the final product. Here’s a closer look at the typical compositions:
Metal Powder | Composition |
---|---|
316L Stainless Steel | Fe balance, Cr 16-18%, Ni 10-14%, Mo 2-3% |
Inconel 625 | Ni 58%, Cr 20-23%, Mo 8-10%, Nb 3.15-4.15% |
Titanium Ti-6Al-4V | Ti balance, Al 5.5-6.75%, V 3.5-4.5% |
Aluminum AlSi10Mg | Al balance, Si 9-11%, Mg 0.2-0.45% |
Cobalt-Chrome (CoCr) | Co balance, Cr 26-30%, Mo 5-7%, W 5% |
Tool Steel H13 | Fe balance, Cr 4.75-5.5%, Mo 1.1-1.75%, V 0.8-1.2%, C 0.32-0.45% |
Copper Cu | Cu balance, with trace amounts of O2 and other impurities |
Nickel Alloy 718 | Ni 50-55%, Cr 17-21%, Fe balance, Nb 4.75-5.5%, Mo 2.8-3.3%, Ti 0.65-1.15%, Al 0.2-0.8% |
Stellite 6 | Co balance, Cr 27-32%, W 3.5-5.5%, C 0.9-1.4%, Ni 2.5% |
Maraging Steel | Fe balance, Ni 18-19%, Co 8.5-9.5%, Mo 4.6-5.2%, Ti 0.15-0.25%, Al 0.05-0.15% |
Characteristics of Laser Metal Deposition (LMD)
Laser Metal Deposition boasts several key characteristics that make it a preferred choice in many industries:
- High Precision: LMD allows for exact control over the dimensions and properties of the deposited material.
- Versatility: Capable of working with a wide range of metals and alloys.
- Minimal Waste: Additive nature means material is only used where needed, reducing waste.
- Customization: Easy to create custom parts and complex geometries.
- Strength and Durability: Parts produced are typically very strong and durable.
Applications of Laser Metal Deposition (LMD)
LMD is used in a diverse array of industries and applications. Here’s a breakdown of some of its primary uses:
Application | Description |
---|---|
Aerospace | Used for repairing and manufacturing high-performance components such as turbine blades and engine parts. |
Medical Devices | Ideal for creating customized implants and surgical instruments due to its precision and material flexibility. |
Automotive | Used for producing lightweight and high-strength parts, as well as for repair and maintenance. |
Tooling | Manufacture of molds, dies, and other tools with high durability and precision. |
Energy Sector | Repair and production of components for power plants, including turbine blades and heat exchangers. |
Oil and Gas | Used for coating and repairing parts exposed to harsh environments, such as valves and pipes. |
Marine | Manufacture and repair of ship components and offshore equipment, focusing on corrosion resistance. |
Defense | Production of high-strength, lightweight parts for military equipment and vehicles. |
Electronics | Fabrication of components requiring high thermal and electrical conductivity, like heat sinks. |
Jewelry | Creation of intricate designs and custom pieces with high precision. |
Specifications, Sizes, Grades, and Standards for LMD
When it comes to specifications, sizes, grades, and standards, LMD technology adheres to stringent requirements to ensure quality and performance. Here are some examples:
Specification | Description |
---|---|
ASTM F3001 | Standard specification for additive manufacturing titanium alloys. |
ISO 17296-2 | Additive manufacturing – General principles – Part 2: Overview of process categories and feedstock. |
AMS 4999 | Aerospace material specification for nickel alloy powders used in LMD. |
DIN EN 17068 | Requirements for qualification of operators of additive manufacturing machines. |
Grade 1 | Pure Titanium – Used for medical implants and aerospace components. |
Grade 23 | Titanium alloy with improved strength and toughness, used in high-stress applications. |
Type 316L | Stainless steel with high corrosion resistance, used in medical and food industry applications. |
Alloy 625 | High-strength, corrosion-resistant nickel alloy used in marine and aerospace. |
H13 Tool Steel | High-hardness tool steel used for molds and dies. |
AlSi10Mg | Aluminum alloy used for lightweight and high-strength applications in automotive and aerospace. |
Suppliers and Pricing Details for Metal Powders
Here’s a look at some of the leading suppliers of metal powders for LMD and their pricing details:
Supplier | Metal Powder | Price per kg (USD) |
---|---|---|
Höganäs | 316L Stainless Steel | $60-$80 |
Carpenter Technology | Inconel 625 | $90-$110 |
LPW Technology | Titanium Ti-6Al-4V | $250-$300 |
ECKART | Aluminum AlSi10Mg | $50-$70 |
Oerlikon Metco | Cobalt-Chrome (CoCr) | $180-$220 |
Sandvik | Tool Steel H13 | $40-$60 |
American Elements | Copper Cu | $20-$30 |
ATI | Nickel Alloy 718 | $100-$130 |
Kennametal Stellite | Stellite 6 | $150-$200 |
Arcam AB | Maraging Steel | $120-$150 |
Pros and Cons of Laser Metal Deposition (LMD)
LMD, like any technology, has its advantages and limitations. Let’s compare:
Pros | Cons |
---|---|
High Precision | Cost: LMD equipment and materials can be expensive. |
Material Efficiency: Minimal waste production. | Speed: Slower than some traditional manufacturing methods. |
Versatility: Can use a wide range of materials. | Complexity: Requires skilled operators and precise control. |
Customization: Ideal for custom and complex parts. | Equipment Maintenance: High maintenance requirements. |
Strength and Durability: Produces strong, durable parts. | Initial Setup: High initial investment cost. |
Detailed Characteristics of Specific Metal Powders
Here’s a deeper dive into the characteristics of some popular metal powders used in LMD:
316L Stainless Steel
- Corrosion Resistance: Excellent, especially in chloride environments.
- Mechanical Properties: High strength and toughness.
- Applications: Medical devices, food processing equipment, marine environments.
Inconel 625
- Oxidation Resistance: Outstanding at high temperatures.
- Mechanical Properties: High tensile, creep, and rupture strength.
- Applications: Aerospace, marine, chemical processing industries.
Titanium Ti-6Al-4V
- Strength-to-Weight Ratio: High, making it ideal for aerospace.
- Biocompatibility: Suitable for medical implants.
- Applications: Aerospace, medical, automotive industries.
Aluminum AlSi10Mg
- Lightweight: Ideal for weight-sensitive applications.
- Thermal Conductivity: Excellent, suitable for heat exchangers.
- Applications: Automotive, aerospace, electronics.
Cobalt-Chrome (CoCr)
- Wear Resistance: Extremely high, ensuring longevity.
- Biocompatibility: Perfect for dental and orthopedic implants.
- Applications: Medical implants, aerospace, turbine components.
Comparative Analysis: LMD versus Traditional Manufacturing
How does Laser Metal Deposition stack up against traditional manufacturing methods?
Parameter | Laser Metal Deposition | Traditional Manufacturing |
---|---|---|
Precision | Higher precision and detail | Lower precision, especially for complex shapes |
Material Efficiency | Minimal waste | Higher material waste |
Customization | Easy to customize parts | Difficult and expensive to customize |
Cost | Higher initial cost | Lower initial cost |
Speed | Slower for large parts | Faster for bulk production |
Maintenance | High maintenance | Lower maintenance |
Complexity Handling | Excels in handling complex geometries | Struggles with complex designs |
Insightful Examples of LMD Applications
Aerospace Industry
In the aerospace industry, LMD is used to repair and manufacture high-performance components such as turbine blades and engine parts. The ability to add material precisely where needed helps in repairing worn-out parts, extending their service life, and reducing costs.
Medical Sector
For medical devices, LMD’s precision and flexibility in materials are crucial. Custom implants, such as dental and orthopedic implants, can be manufactured to fit individual patients perfectly, improving outcomes and comfort.
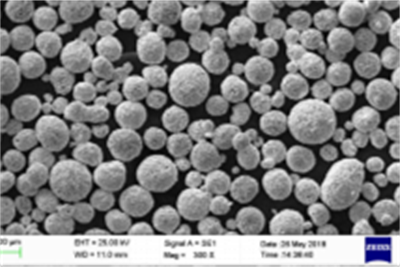
FAQ
Question | Answer |
---|---|
What is Laser Metal Deposition (LMD)? | LMD is an additive manufacturing process that uses a laser to melt and deposit metal powders layer by layer. |
What are the advantages of LMD over traditional manufacturing methods? | LMD offers higher precision, minimal waste, greater customization, and stronger, more durable parts. |
Which industries benefit most from LMD? | Aerospace, medical, automotive, energy, and defense industries benefit significantly from LMD. |
What types of metals can be used in LMD? | Various metals including stainless steel, titanium, aluminum, cobalt-chrome, and nickel alloys can be used. |
Is LMD cost-effective? | While the initial costs are high, LMD can be cost-effective in the long run due to reduced waste and improved part longevity. |
How does LMD contribute to sustainability? | LMD minimizes material waste and can extend the life of existing parts through precise repairs, contributing to sustainability. |
What are the typical applications of LMD? | Applications include manufacturing and repairing aerospace components, medical implants, automotive parts, and tooling. |
Can LMD be used for large-scale production? | LMD is generally slower than traditional methods for large-scale production but excels in custom and complex parts. |
How does the choice of metal powder affect the final product? | The choice of metal powder determines the mechanical properties, corrosion resistance, and suitability for specific applications. |
What are the maintenance requirements for LMD equipment? | LMD equipment requires regular maintenance and skilled operators to ensure precise and reliable operation. |