Electron Beam Additive Manufacturing (EBAM) is revolutionizing the world of metal fabrication. Imagine a process where you can build metal parts layer by layer, using an electron beam to fuse metal powders or wire. Sounds futuristic, right? Well, it’s not just the stuff of science fiction anymore. It’s happening right now, and it’s changing how we think about manufacturing.
Overview of Electron Beam Additive Manufacturing (EBAM)
EBAM is an advanced manufacturing technique that uses a high-energy electron beam to melt and fuse metal powders or wires layer by layer to create complex metal parts. This process offers numerous advantages, including the ability to create parts with intricate geometries, reduced material waste, and shorter production times compared to traditional manufacturing methods. But that’s just scratching the surface.
Key Details of EBAM
- Technique: Utilizes an electron beam to melt and fuse metal powders or wire.
- Materials: Primarily used with various metal powders and wires.
- Applications: Aerospace, automotive, medical implants, and more.
- Benefits: High precision, reduced waste, faster production times.
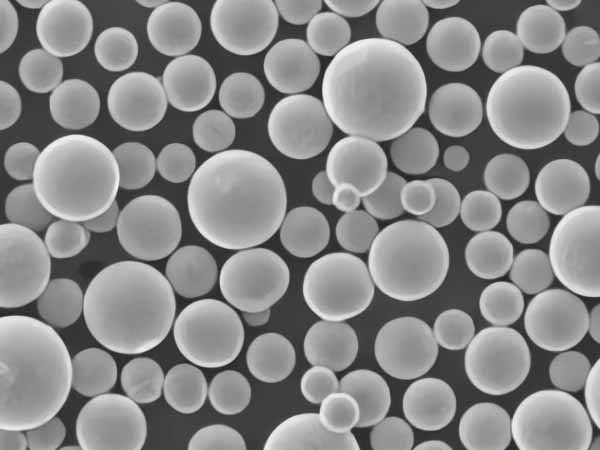
Types of Metal Powders Used in EBAM
Different types of metal powders are used in EBAM, each with unique properties and applications. Here are ten specific models:
Metal Powder | Composition | Properties | Applications |
---|---|---|---|
Ti-6Al-4V | Titanium alloy with 6% Al and 4% V | High strength, corrosion resistance | Aerospace, medical implants |
Inconel 718 | Nickel-chromium alloy | High temperature resistance | Turbine blades, aerospace components |
Stainless Steel 316L | Iron alloy with 16-18% Cr and 10-14% Ni | Corrosion resistance, durability | Medical devices, food processing equipment |
AlSi10Mg | Aluminum alloy with 10% Si and 0.3% Mg | Lightweight, good thermal conductivity | Automotive parts, heat exchangers |
Copper (Cu) | Pure copper | Excellent electrical conductivity | Electrical components, heat sinks |
Hastelloy X | Nickel-based superalloy | Oxidation resistance at high temps | Gas turbines, chemical processing |
Maraging Steel (18Ni300) | Iron-nickel alloy with 18% Ni and 8-12% Co | High strength, hardness | Tooling, aerospace components |
CoCrMo | Cobalt-chromium-molybdenum alloy | Wear resistance, biocompatibility | Medical implants, dental applications |
Ti-6Al-2Sn-4Zr-6Mo | Titanium alloy with 6% Al, 2% Sn, 4% Zr, 6% Mo | High strength, fatigue resistance | Aerospace components, high-stress parts |
Aluminum 6061 | Aluminum alloy with Mg and Si | Lightweight, versatile | Structural components, marine applications |
Composition of EBAM Metal Powders
Understanding the composition of the metal powders used in EBAM is crucial. These powders are meticulously engineered to ensure they meet the specific requirements of the manufacturing process.
Metal Powder | Major Elements | Minor Elements |
---|---|---|
Ti-6Al-4V | Titanium, Aluminum, Vanadium | Oxygen, Nitrogen, Carbon |
Inconel 718 | Nickel, Chromium, Iron | Molybdenum, Niobium, Aluminum, Titanium |
Stainless Steel 316L | Iron, Chromium, Nickel | Molybdenum, Manganese, Silicon |
AlSi10Mg | Aluminum, Silicon, Magnesium | Iron, Copper, Manganese |
Copper (Cu) | Copper | Oxygen, Phosphorus |
Hastelloy X | Nickel, Chromium, Iron | Molybdenum, Cobalt, Tungsten |
Maraging Steel (18Ni300) | Iron, Nickel, Cobalt | Molybdenum, Titanium, Aluminum |
CoCrMo | Cobalt, Chromium, Molybdenum | Nickel, Iron, Carbon |
Ti-6Al-2Sn-4Zr-6Mo | Titanium, Aluminum, Tin, Zirconium, Molybdenum | Oxygen, Iron, Silicon |
Aluminum 6061 | Aluminum, Magnesium, Silicon | Iron, Copper, Zinc |
Characteristics of EBAM Metal Powders
The characteristics of the metal powders used in EBAM are just as important as their composition. These characteristics determine how the material will behave during the manufacturing process and in the final product.
Characteristic | Description |
---|---|
Particle Size | Typically ranges from 15 to 150 microns |
Flowability | Essential for consistent powder distribution |
Purity | High purity levels to ensure material integrity |
Density | Affects the melting and solidification process |
Oxidation Resistance | Important for maintaining material properties |
Applications of Electron Beam Additive Manufacturing (EBAM)
EBAM is used in a wide range of applications, from aerospace components to medical implants. The ability to create complex geometries and use high-performance materials makes it ideal for industries where precision and performance are critical.
Industry | Applications |
---|---|
Aerospace | Turbine blades, structural components, engine parts |
Automotive | Lightweight parts, prototypes, custom components |
Medical | Implants, prosthetics, surgical tools |
Energy | Turbine components, heat exchangers, fuel cells |
Tooling | Custom molds, dies, and jigs |
Defense | Armor, weapon components, specialized equipment |
Electronics | Heat sinks, connectors, casings |
Specifications, Sizes, Grades, and Standards in EBAM
When working with EBAM, it’s essential to adhere to specific standards and specifications to ensure the quality and performance of the final product.
Metal Powder | Sizes | Grades | Standards |
---|---|---|---|
Ti-6Al-4V | 15-45 µm, 45-90 µm | Grade 5 | ASTM F2924, AMS 4998 |
Inconel 718 | 15-45 µm, 45-106 µm | AMS 5662, AMS 5663 | ASTM B637 |
Stainless Steel 316L | 15-45 µm, 45-90 µm | 316L | ASTM A276, ASTM F138 |
AlSi10Mg | 15-45 µm, 45-106 µm | – | ASTM B928, EN 1706 |
Copper (Cu) | 15-45 µm, 45-106 µm | C11000 | ASTM B170 |
Hastelloy X | 15-45 µm, 45-90 µm | AMS 5754 | ASTM B619 |
Maraging Steel (18Ni300) | 15-45 µm, 45-90 µm | – | ASTM A538 |
CoCrMo | 15-45 µm, 45-90 µm | ASTM F75 | ISO 5832-4 |
Ti-6Al-2Sn-4Zr-6Mo | 15-45 µm, 45-106 µm | – | AMS 4919 |
Aluminum 6061 | 15-45 µm, 45-90 µm | 6061-T6 | ASTM B209, ASTM B221 |
Suppliers and Pricing Details for EBAM Metal Powders
Finding reliable suppliers and understanding pricing is crucial for those looking to utilize EBAM in their manufacturing processes.
Supplier | Metal Powders | Price Range (per kg) |
---|---|---|
EOS GmbH | Ti-6Al-4V, Inconel 718, Stainless Steel 316L | $300 – $500 |
Carpenter Technology | AlSi10Mg, Copper, Hastelloy X | $250 – $600 |
Höganäs AB | Maraging Steel, CoCrMo, Ti-6Al-2Sn-4Zr-6Mo | $200 – $700 |
GKN Additive | Aluminum 6061, Inconel 718, Stainless Steel 316L | $300 – $550 |
AP&C (Arcam) | Ti-6Al-4V, Inconel718, AlSi10Mg 718, AlSi10Mg | $350 – $650 |
LPW Technology | Copper, Hastelloy X, Maraging Steel | $250 – $600 |
Sandvik | Ti-6Al-2Sn-4Zr-6Mo, CoCrMo, Stainless Steel 316L | $200 – $700 |
Praxair | Inconel 718, Aluminum 6061, Ti-6Al-4V | $300 – $600 |
Metalysis | Ti-6Al-4V, Hastelloy X, AlSi10Mg | $250 – $650 |
ATI Metals | Stainless Steel 316L, Copper, Inconel 718 | $300 – $550 |
Comparing Pros and Cons of EBAM
When considering EBAM, it’s important to weigh its advantages and limitations compared to other manufacturing methods.
Aspect | Advantages | Limitations |
---|---|---|
Precision | High precision, able to create complex geometries | Requires meticulous calibration and control |
Material Efficiency | Minimal waste compared to subtractive methods | Powder handling and recycling can be challenging |
Speed | Faster production times for certain parts | Initial setup and calibration can be time-consuming |
Material Properties | Excellent mechanical properties, high strength | Limited to materials that can be processed by electron beam |
Cost | Cost-effective for small batch and custom parts | High initial investment in equipment and materials |
Flexibility | Can create custom and one-off parts easily | Not as well-suited for mass production compared to traditional methods |
Post-Processing | Often minimal post-processing required | Some parts may require additional finishing depending on application |
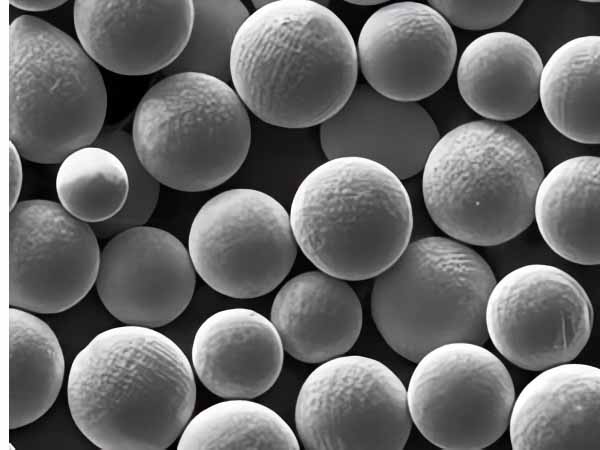
FAQ
Here are some frequently asked questions about EBAM to help you better understand this innovative technology.
Question | Answer |
---|---|
What is EBAM? | EBAM stands for Electron Beam Additive Manufacturing, a process that uses an electron beam to melt and fuse metal powders or wire to create parts layer by layer. |
What materials can be used in EBAM? | A wide range of metal powders and wires, including titanium alloys, nickel alloys, stainless steels, aluminum alloys, and more. |
What are the advantages of EBAM? | High precision, reduced material waste, faster production times, and the ability to create complex geometries. |
What are the limitations of EBAM? | High initial investment, requires meticulous calibration, and is limited to materials that can be processed by an electron beam. |
What industries use EBAM? | Aerospace, automotive, medical, energy, tooling, defense, and electronics. |
How does EBAM compare to other 3D printing methods? | EBAM offers superior mechanical properties and is suitable for high-performance applications, but it can be more expensive and complex to set up. |
What are some common metal powders used in EBAM? | Ti-6Al-4V, Inconel 718, Stainless Steel 316L, AlSi10Mg, Copper, Hastelloy X, Maraging Steel, CoCrMo, Ti-6Al-2Sn-4Zr-6Mo, and Aluminum 6061. |
Is post-processing required for EBAM parts? | While EBAM parts often require minimal post-processing, some applications may need additional finishing. |
How does the electron beam work in EBAM? | The electron beam generates heat to melt and fuse metal powders or wire, layer by layer, to build the part. |
What is the future of EBAM? | The future of EBAM looks promising, with ongoing advancements in materials, process optimization, and expanded applications in various industries. |
Conclusion
Electron Beam Additive Manufacturing (EBAM) is a groundbreaking technology that is transforming the way we think about manufacturing. By utilizing high-energy electron beams to melt and fuse metal powders or wire, EBAM can create complex, high-performance parts with minimal waste and faster production times. Whether you’re in aerospace, automotive, medical, or any other industry that demands precision and performance, EBAM offers a compelling solution. So, why not explore the possibilities of EBAM and see how it can revolutionize your manufacturing process?