Welding is an intricate dance of heat, precision, and materials science. One key player in this dance is metal powder. If you’re diving into the world of metal powders for welding, you’ve come to the right place. Let’s unpack this topic in detail, keeping it engaging, informative, and thoroughly SEO-optimized.
Overview of Metal Powder for Welding
Metal powder is a crucial component in various welding techniques, providing enhanced performance, efficiency, and quality. These powders come in different types and compositions, each tailored for specific welding applications. The choice of metal powder can significantly impact the weld quality, strength, and overall durability.
Types of Metal Powders for Welding
Metal Powder | Composition | Properties | Characteristics |
---|---|---|---|
Iron Powder | Pure iron or iron alloy | High tensile strength, magnetic properties | Common in MIG and TIG welding |
Aluminum Powder | Pure aluminum or aluminum alloy | Lightweight, corrosion-resistant | Used in lightweight structures |
Nickel Powder | Pure nickel or nickel alloy | High corrosion resistance, high melting point | Ideal for high-temperature applications |
Copper Powder | Pure copper or copper alloy | Excellent electrical conductivity | Used in electrical welding |
Titanium Powder | Pure titanium or titanium alloy | High strength-to-weight ratio, corrosion-resistant | Aerospace and medical applications |
Cobalt Powder | Pure cobalt or cobalt alloy | High wear resistance, thermal stability | Used in high-wear applications |
Zinc Powder | Pure zinc or zinc alloy | Good corrosion resistance | Galvanizing applications |
Tungsten Powder | Pure tungsten or tungsten alloy | High melting point, hardness | Used in high-temperature welding |
Magnesium Powder | Pure magnesium or magnesium alloy | Lightweight, good strength | Aerospace applications |
Stainless Steel Powder | Alloy of iron, chromium, nickel | Corrosion-resistant, durable | Widely used in various welding applications |
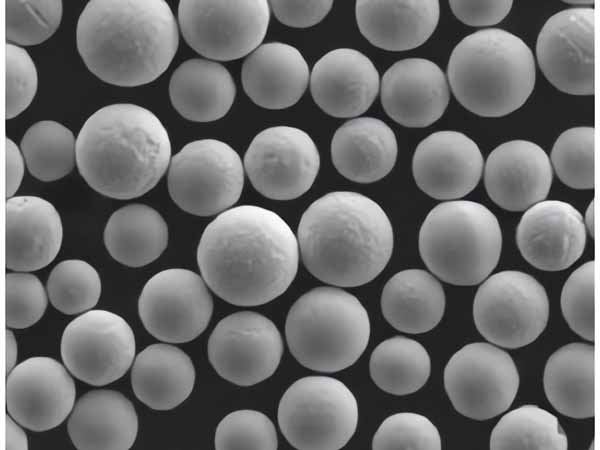
Applications of Metal Powder for Welding
Application | Metal Powder Type | Description |
---|---|---|
Automotive | Iron, Aluminum, Copper | Used for structural and electrical components |
Aerospace | Titanium, Magnesium | Lightweight and strong components |
Construction | Iron, Stainless Steel | Structural integrity and durability |
Medical Devices | Titanium, Stainless Steel | Biocompatibility and strength |
Electronics | Copper, Silver | High electrical conductivity |
Oil and Gas | Nickel, Cobalt | High-temperature and corrosive environments |
Marine | Aluminum, Zinc | Corrosion resistance in marine environments |
Renewable Energy | Copper, Aluminum | Electrical components in solar and wind energy systems |
Specifications, Sizes, Grades, Standards
Metal Powder | Specification | Size (microns) | Grades | Standards |
---|---|---|---|---|
Iron Powder | FE 100.29 | 45-150 | High purity | ASTM A95 |
Aluminum Powder | AL 1100 | 20-200 | Various grades | ASTM B928 |
Nickel Powder | NI 123 | 10-100 | High purity | ASTM B330 |
Copper Powder | CU 101 | 15-200 | Electrolytic, atomized | ASTM B216 |
Titanium Powder | TI 6-4 | 5-100 | Grade 5 | ASTM F1580 |
Cobalt Powder | CO 6 | 10-150 | Various grades | ASTM F75 |
Zinc Powder | ZN 99 | 20-200 | High purity | ASTM B6 |
Tungsten Powder | W 1 | 1-50 | High purity | ASTM B777 |
Magnesium Powder | MG 99 | 15-150 | Various grades | ASTM B90 |
Stainless Steel Powder | SS 316 | 10-150 | 304, 316 | ASTM A276 |
Suppliers and Pricing Details
Supplier | Metal Powder | Price (per kg) | Location | Website |
---|---|---|---|---|
Höganäs | Iron, Stainless Steel | $20-$50 | Sweden | hoganas.com |
Valimet | Aluminum | $30-$60 | USA | valimet.com |
JFE Steel | Iron, Nickel | $40-$80 | Japan | jfe-steel.co.jp |
Sandvik | Stainless Steel, Titanium | $50-$100 | Sweden | home.sandvik |
Kennametal | Cobalt, Tungsten | $80-$150 | USA | kennametal.com |
American Elements | Various | $25-$70 | USA | americanelements.com |
Tekna | Aluminum, Titanium | $45-$90 | Canada | tekna.com |
Praxair Surface Technologies | Various | $35-$85 | USA | praxairsurfacetechnologies.com |
GKN Hoeganaes | Iron, Stainless Steel | $30-$75 | USA | gknpm.com |
Makin Metal Powders | Copper, Zinc | $20-$60 | UK | makin-metals.com |
Comparing Pros and Cons of Metal Powders for Welding
Metal Powder | Advantages | Disadvantages |
---|---|---|
Iron Powder | High strength, widely available, cost-effective | Heavier than alternatives, rusts easily |
Aluminum Powder | Lightweight, corrosion-resistant, good conductivity | Lower strength than steel, more expensive |
Nickel Powder | High corrosion resistance, high melting point | Expensive, hard to machine |
Copper Powder | Excellent conductivity, easy to weld | Expensive, prone to oxidation |
Titanium Powder | High strength-to-weight ratio, corrosion-resistant | Very expensive, difficult to weld |
Cobalt Powder | High wear resistance, thermal stability | Very expensive, limited availability |
Zinc Powder | Good corrosion resistance, cost-effective | Lower strength, not suitable for high-temperature applications |
Tungsten Powder | Extremely high melting point, hardness | Very heavy, difficult to process |
Magnesium Powder | Lightweight, good strength | Flammable, lower corrosion resistance |
Stainless Steel Powder | Corrosion-resistant, durable | More expensive than regular steel, heavier |
Detailed Descriptions of Specific Metal Powder Models
- FE 100.29 Iron Powder
- Composition: Pure iron
- Properties: High tensile strength, magnetic
- Uses: MIG, TIG welding in automotive and construction
- AL 1100 Aluminum Powder
- Composition: Pure aluminum
- Properties: Lightweight, corrosion-resistant
- Uses: Aerospace, automotive, electronics
- NI 123 Nickel Powder
- Composition: Pure nickel
- Properties: High corrosion resistance, high melting point
- Uses: Oil and gas, high-temperature welding
- CU 101 Copper Powder
- Composition: Pure copper
- Properties: Excellent electrical conductivity
- Uses: Electrical welding, electronics
- TI 6-4 Titanium Powder
- Composition: Titanium alloy (Grade 5)
- Properties: High strength-to-weight ratio, corrosion-resistant
- Uses: Aerospace, medical devices
- CO 6 Cobalt Powder
- Composition: Pure cobalt
- Properties: High wear resistance, thermal stability
- Uses: High-wear applications, tooling
- ZN 99 Zinc Powder
- Composition: Pure zinc
- Properties: Good corrosion resistance
- Uses: Galvanizing, marine applications
- W 1 Tungsten Powder
- Composition: Pure tungsten
- Properties: High melting point, hardness
- Uses: High-temperature welding, aerospace
- MG 99 Magnesium Powder
- Composition: Pure magnesium
- Properties: Lightweight, good strength
- Uses: Aerospace, automotive
- SS 316 Stainless Steel Powder
- Composition: Iron, chromium, nickel alloy
- Properties: Corrosion-resistant, durable
- Uses: Construction, medical devices
Characteristics of Metal Powder for Welding
The characteristics of metal powders are pivotal to their performance in welding applications. Understanding these characteristics helps in selecting the right powder for the job.
- Particle Size: Affects flowability, packing density, and surface area.
- Purity: High purity ensures consistent performance and fewer contaminants.
- Density: Influences the mechanical properties and melting behavior.
- Flowability: Important for processes like additive manufacturing and powder metallurgy.
- Morphology: The shape and surface texture of powder particles impact how they behave during welding.
Advantages of Metal Powder for Welding
- Enhanced Mechanical Properties: Metal powders can improve the strength, durability, and toughness of welded joints.
- Better Control: Allows for precise control over the composition and microstructure of the weld.
- Versatility: Suitable for various welding techniques, including MIG, TIG, and laser welding.
- Efficiency: Can reduce waste and improve the efficiency of the welding process.
Limitations of Metal Powder for Welding
- Cost: High-quality metal powders can be expensive.
- Complexity: Requires careful handling and storage to prevent contamination.
- Technical Expertise: Using metal powders effectively demands specialized knowledge and equipment.
Comparing Metal Powders for Different Welding Techniques
Welding Technique | Suitable Metal Powders | Advantages | Disadvantages |
---|---|---|---|
MIG Welding | Iron, Stainless Steel, Aluminum | High deposition rate, good control | Requires shielding gas, less portable |
TIG Welding | Iron, Titanium, Nickel | High precision, clean welds | Slower process, requires skill |
Laser Welding | Stainless Steel, Titanium, Nickel | High precision, minimal distortion | Expensive equipment, requires precise control |
Plasma Welding | Stainless Steel, Copper, Nickel | High quality, can weld thick materials | Complex setup, requires expertise |
FAQ
Question | Answer |
---|---|
What is metal powder for welding? | Metal powder for welding is finely powdered metal used to enhance the properties and efficiency of welding processes. |
Why use metal powder in welding? | It improves weld quality, mechanical properties, and allows for precise control over the welding process. |
Which metal powder is best for automotive welding? | Iron and aluminum powders are commonly used in automotive welding for their strength and lightweight properties. |
Can metal powder be used in all welding techniques? | While versatile, the suitability of metal powder depends on the specific welding technique and application. |
How is metal powder produced? | Metal powder is produced through various methods such as atomization, reduction, and electrolytic deposition. |
What are the storage requirements for metal powder? | Metal powder should be stored in a dry, contamination-free environment to maintain its quality. |
Is metal powder welding cost-effective? | Despite the higher initial cost, metal powder welding can be cost-effective in the long run due to improved efficiency and quality. |
What safety precautions are needed when handling metal powder? | Proper ventilation, protective clothing, and careful handling are essential to prevent inhalation and contamination. |
Are there environmental concerns with metal powder for welding? | Proper disposal and recycling of metal powder residues are necessary to minimize environmental impact. |
Can metal powders be customized for specific applications? | Yes, metal powders can be tailored to meet specific requirements for different applications and industries. |
Conclusion
Metal powder for welding is a dynamic and essential component in modern welding practices, offering numerous advantages from enhanced mechanical properties to improved efficiency. By understanding the various types, applications, and characteristics of metal powders, welders and engineers can make informed decisions to achieve superior welding results. Whether you’re in the automotive industry, aerospace, construction, or any other field that relies on high-quality welds, the right metal powder can make all the difference. So, next time you see a beautifully welded joint, remember the unsung hero – the metal powder that made it possible.