Batch-based debinded sinter equipment represents a significant advancement in the manufacturing and processing of metal powders. This industry is at the forefront of producing high-quality, precise metal components for various applications. Let’s delve into the details, uncovering the intricacies and advantages of this technology.
Overview of Batch-Based Debinded Sinter Equipment Industry
Batch-based debinded sinter equipment is crucial in the metal powder industry. This technology is designed to debind and sinter metal powders in controlled, repeatable batches, ensuring consistent quality and performance. Key details include the types of metal powders used, the processes involved, and the applications of the finished products.
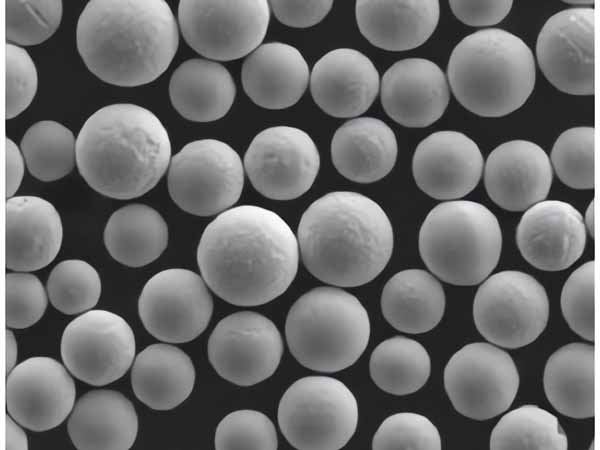
Types and Characteristics of Metal Powders
Metal powders used in batch-based debinded sinter equipment vary widely in their composition and properties. Here’s a detailed table summarizing some common metal powders:
Metal Powder | Composition | Properties | Characteristics |
---|---|---|---|
Stainless Steel 316 | Fe, Cr, Ni, Mo | High corrosion resistance, strength | Widely used in medical and food industry |
Titanium Ti-6Al-4V | Ti, Al, V | High strength-to-weight ratio | Aerospace, biomedical applications |
Copper C11000 | Cu | Excellent electrical conductivity | Electrical components |
Nickel Alloy 625 | Ni, Cr, Mo, Nb | Excellent corrosion and oxidation resistance | Marine and chemical processing |
Aluminum 6061 | Al, Mg, Si | Lightweight, good mechanical properties | Automotive, aerospace |
Iron Fe-PM | Fe, C | High strength, good machinability | Automotive parts |
Cobalt-Chrome (CoCr) | Co, Cr, Mo | High wear resistance, biocompatibility | Medical implants, dental applications |
Tungsten Carbide (WC-Co) | W, C, Co | Extremely hard, wear resistant | Cutting tools, abrasives |
Bronze (Cu-Sn) | Cu, Sn | Good wear resistance, machinability | Bearings, bushings |
Magnesium AZ91D | Mg, Al, Zn | Lightweight, good strength | Aerospace, automotive |
Applications of Batch-Based Debinded Sinter Equipment
The applications of batch-based debinded sinter equipment are vast and varied. Here’s a table showcasing where these metal powders are used:
Application | Description |
---|---|
Aerospace | Lightweight, strong components such as turbine blades, structural parts |
Medical | Biocompatible implants, surgical instruments, dental prosthetics |
Automotive | Engine components, gears, bearings, brake parts |
Electronics | Conductive components, connectors, heat sinks |
Industrial Machinery | Wear-resistant parts, cutting tools, molds |
Energy | Components for turbines, oil and gas equipment |
Consumer Goods | High-strength, corrosion-resistant products like kitchen utensils |
Marine | Corrosion-resistant parts for marine environments |
Defense | Strong, durable parts for military equipment |
Chemical Processing | Corrosion-resistant equipment for handling chemicals |
Specifications, Sizes, Grades, and Standards
When dealing with batch-based debinded sinter equipment, it’s essential to understand the specifications, sizes, grades, and standards. Here’s a detailed table:
Metal Powder | Sizes (µm) | Grades | Standards |
---|---|---|---|
Stainless Steel 316 | 5-45 | A, B, C | ASTM F138, ISO 5832-1 |
Titanium Ti-6Al-4V | 15-45 | Grade 5 | ASTM B348, ISO 5832-3 |
Copper C11000 | 10-75 | 110, 122 | ASTM B170, C10100 |
Nickel Alloy 625 | 15-45 | NA625 | ASTM B443, AMS 5599 |
Aluminum 6061 | 10-45 | T6 | ASTM B211, B221 |
Iron Fe-PM | 45-150 | Various | MPIF Standard 35 |
Cobalt-Chrome (CoCr) | 15-45 | F75 | ASTM F75, ISO 5832-4 |
Tungsten Carbide (WC-Co) | 0.4-30 | Various | ISO 3878, ASTM B777 |
Bronze (Cu-Sn) | 20-150 | Various | ASTM B22 |
Magnesium AZ91D | 45-150 | AZ91D | ASTM B93, B94 |
Suppliers and Pricing Details
Finding reliable suppliers and understanding pricing is crucial in the batch-based debinded sinter equipment industry. Here’s a table with some prominent suppliers and approximate pricing:
Supplier | Metal Powder | Pricing (USD/kg) | Notes |
---|---|---|---|
Carpenter Technology | Stainless Steel 316, Titanium Ti-6Al-4V | $50 – $150 | High-quality medical and aerospace powders |
Höganäs AB | Iron Fe-PM, Bronze (Cu-Sn) | $10 – $50 | Wide range of industrial applications |
Sandvik Materials Technology | Nickel Alloy 625, CoCr | $100 – $300 | Specialized in high-performance alloys |
Praxair Surface Technologies | Aluminum 6061, Tungsten Carbide (WC-Co) | $20 – $200 | Excellent for aerospace and cutting tools |
Advanced Powder Products | Copper C11000, Magnesium AZ91D | $15 – $100 | Electrical and automotive applications |
Advantages and Limitations of Batch-Based Debinded Sinter Equipment
Understanding the pros and cons of batch-based debinded sinter equipment can help in making informed decisions. Here’s a comparison:
Aspect | Advantages | Limitations |
---|---|---|
Quality Control | Consistent, high-quality output | Requires precise control and monitoring |
Versatility | Can process a variety of metal powders | Limited by batch size |
Cost Efficiency | Lower operational costs compared to continuous processes | Initial investment can be high |
Complex Shapes | Capable of producing intricate geometries | Some shapes may require additional finishing |
Energy Consumption | Often more energy-efficient than other methods | Energy costs can still be significant |
Scalability | Easily scalable for different production volumes | Scale-up may require additional equipment |
Environmental Impact | Lower emissions and waste compared to traditional methods | Disposal of debinding materials can be challenging |
Technical Parameters and Performance Metrics
Here’s a table summarizing some technical parameters and performance metrics for batch-based debinded sinter equipment:
Parameter | Value | Notes |
---|---|---|
Temperature Range | 1200°C – 1400°C | Varies based on material being processed |
Atmosphere Control | Argon, Nitrogen, Hydrogen | Inert or reducing atmospheres |
Cycle Time | 10 – 24 hours | Depends on batch size and material |
Batch Size | 1 – 100 kg | Adjustable based on equipment capacity |
Heating Rate | 1 – 10°C/min | Controlled to prevent defects |
Cooling Rate | 1 – 5°C/min | Controlled to ensure material properties |
Debinding Time | 2 – 8 hours | Depends on binder type and amount |
Sintering Time | 4 – 12 hours | Based on material and desired properties |
Power Consumption | 10 – 50 kW | Varies with equipment size and process |
Yield | 95% – 99% | High yield rates with proper control |
Comparing Batch-Based Debinded Sinter Equipment to Other Methods
Batch-based debinded sinter equipment has several advantages compared to other methods. Here’s a comparative analysis:
Method | Advantages | Disadvantages |
---|---|---|
Batch-Based Debinded Sintering | Consistent quality, energy-efficient, versatile | High initial investment, limited batch size |
Continuous Sintering | High throughput, suitable for large-scale production | Less control over individual batches, higher energy costs |
Additive Manufacturing | Complex geometries, minimal waste, rapid prototyping | Slower production rates, high material costs |
Traditional Powder Metallurgy | Established technology, wide material range | Higher emissions, less precise control |
Hot Isostatic Pressing (HIP) | Superior material properties, high density | Very high costs, limited to certain applications |
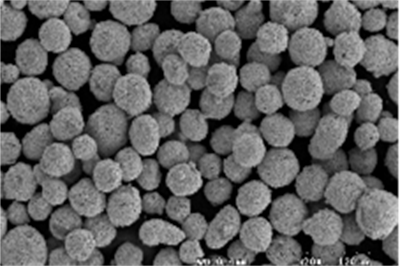
FAQ
Question | Answer |
---|---|
What is batch-based debinded sinter equipment? | It is a type of equipment used to process metal powders by debinding and sintering them in controlled batches. |
What metals can be processed? | Various metals like stainless steel, titanium, copper, nickel alloys, aluminum, iron, cobalt-chrome, tungsten carbide, bronze, and magnesium. |
What are the key benefits? | Consistent quality, versatility, cost efficiency, ability to produce complex shapes, and lower environmental impact. |
What are the limitations? | Requires precise control, high initial investment, and disposal challenges for debinding materials. |
How does it compare to other methods? | It offers better quality control and versatility but has limitations in batch size and initial costs compared to continuous methods and additive manufacturing. |
Who are some prominent suppliers? | Suppliers include Carpenter Technology, Höganäs AB, Sandvik Materials Technology, Praxair Surface Technologies, and Advanced Powder Products. |
Conclusion
The batch-based debinded sinter equipment industry represents a vital segment of the modern manufacturing landscape, offering numerous advantages in producing high-quality, precise metal components. By understanding the types of metal powders, their applications, specifications, and the comparative benefits of this technology, stakeholders can make informed decisions to leverage its full potential. This industry continues to evolve, promising further advancements and broader applications in the future.