Overview
Binder Jetting Additive Manufacturing is revolutionizing the way we think about manufacturing. This innovative technology, part of the 3D printing family, uses a liquid binding agent to fuse layers of powdered material to create a solid part. The versatility of Binder Jetting lies in its ability to work with various materials, including metals, ceramics, and polymers. It’s cost-effective, fast, and perfect for both prototyping and large-scale production. Let’s dive into the world of Binder Jetting and explore its intricacies, applications, and the specific metal powders used in this transformative process.
Types and Composition of Binder Jetting Additive Manufacturing
Binder Jetting technology can utilize different types of powders and binders. Here’s a detailed look:
Material Type | Composition | Properties | Characteristics |
---|---|---|---|
Metal Powders | Iron, steel, bronze, titanium, nickel | High strength, durability | Excellent for functional parts, high thermal and electrical conductivity |
Ceramic Powders | Alumina, zirconia, silicon carbide | High hardness, heat resistance | Suitable for high-temperature applications, wear-resistant parts |
Polymer Powders | Polyamide, polypropylene | Lightweight, flexible | Ideal for complex geometries, less durable compared to metals |
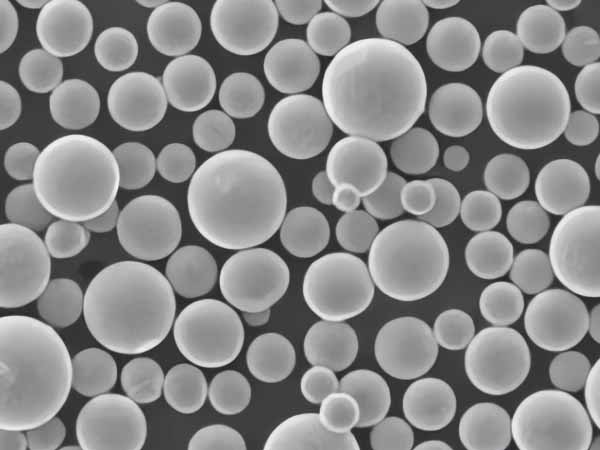
Applications of Binder Jetting Additive Manufacturing
The versatility of Binder Jetting makes it suitable for a wide range of applications:
Industry | Application |
---|---|
Aerospace | Lightweight structural components |
Automotive | Engine parts, prototypes |
Medical | Custom implants, surgical tools |
Consumer Goods | Jewelry, bespoke items |
Industrial Manufacturing | Tooling, molds |
Art and Design | Sculptures, art pieces |
Specifications, Sizes, Grades, and Standards
When selecting powders and binders for Binder Jetting, it’s crucial to consider specifications, sizes, grades, and standards:
Material | Specification | Size Range (microns) | Grade | Standards |
---|---|---|---|---|
Stainless Steel | ASTM A240 | 10-100 | 316L | ISO/ASTM 52900 |
Titanium | ASTM F2924 | 15-45 | Ti6Al4V | ISO 5832-3 |
Aluminum | ASTM B209 | 20-60 | 6061 | AMS 4027 |
Nickel Alloy | ASTM B444 | 20-50 | Inconel 718 | AMS 5662 |
Specific Metal Powder Models
Here are some of the commonly used metal powder models in Binder Jetting:
- 316L Stainless Steel
- Composition: Iron, Chromium, Nickel, Molybdenum
- Properties: Corrosion-resistant, good strength
- Applications: Medical instruments, aerospace components
- 17-4 PH Stainless Steel
- Composition: Iron, Chromium, Nickel, Copper, Niobium
- Properties: High strength, good corrosion resistance
- Applications: Valves, gears, surgical tools
- Inconel 625
- Composition: Nickel, Chromium, Molybdenum, Niobium
- Properties: High-temperature strength, oxidation resistance
- Applications: Turbine blades, aerospace components
- Inconel 718
- Composition: Nickel, Chromium, Iron, Niobium, Molybdenum
- Properties: High tensile strength, excellent creep resistance
- Applications: Jet engine parts, nuclear reactors
- Ti6Al4V (Titanium Alloy)
- Composition: Titanium, Aluminum, Vanadium
- Properties: High strength-to-weight ratio, corrosion resistance
- Applications: Aerospace components, medical implants
- Copper
- Composition: Pure Copper
- Properties: Excellent thermal and electrical conductivity
- Applications: Electrical components, heat exchangers
- Aluminum 6061
- Composition: Aluminum, Magnesium, Silicon
- Properties: Good mechanical properties, corrosion resistance
- Applications: Automotive parts, structural components
- Cobalt-Chrome
- Composition: Cobalt, Chromium, Molybdenum
- Properties: High wear resistance, biocompatibility
- Applications: Dental implants, orthopedic implants
- Hastelloy X
- Composition: Nickel, Chromium, Iron, Molybdenum, Cobalt
- Properties: High-temperature strength, oxidation resistance
- Applications: Gas turbine components, petrochemical industry
- Bronze
- Composition: Copper, Tin
- Properties: Low friction, high wear resistance
- Applications: Bearings, bushings
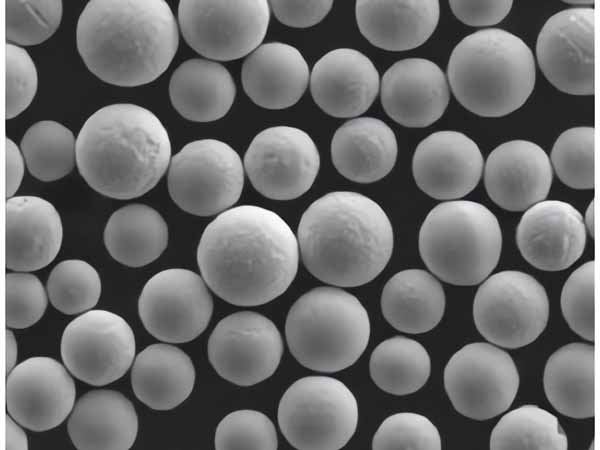
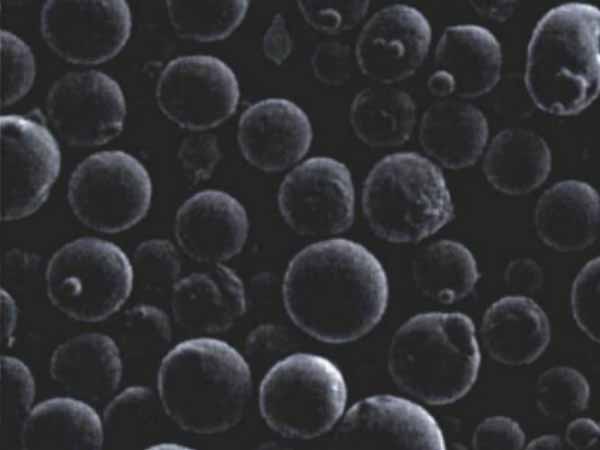
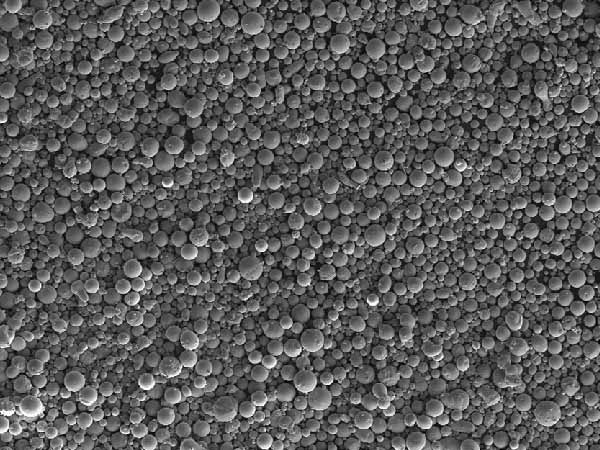
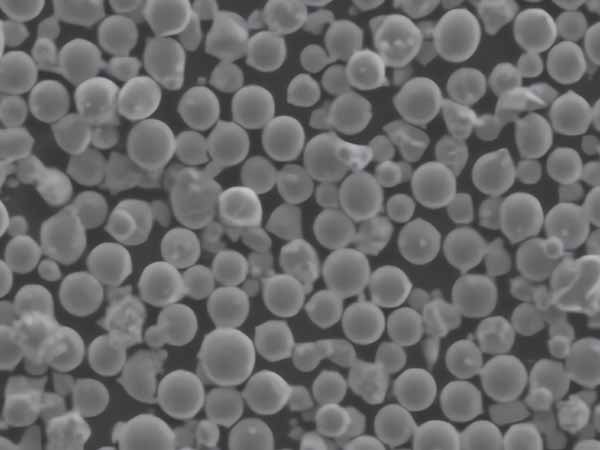
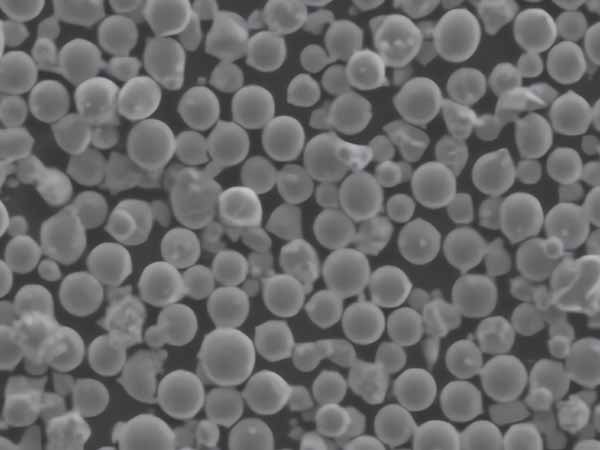
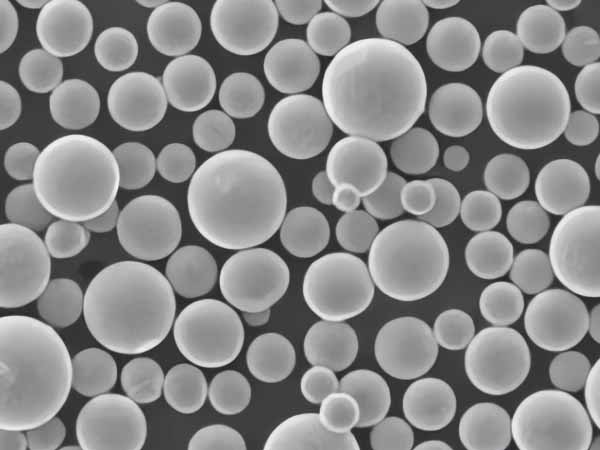
Suppliers and Pricing Details
Understanding the market and suppliers is crucial for implementing Binder Jetting technology effectively:
Supplier | Material | Price Range ($/kg) | Contact |
---|---|---|---|
GKN Powder Metallurgy | Stainless Steel, Titanium | 50-150 | www.gknpm.com |
Carpenter Technology | Inconel, Titanium | 100-300 | www.cartech.com |
Sandvik Osprey | Stainless Steel, Aluminum | 40-120 | www.materials.sandvik |
Praxair Surface Technologies | Nickel Alloys, Cobalt-Chrome | 80-250 | www.praxairsurfacetechnologies.com |
Höganäs | Iron, Bronze | 20-100 | www.hoganas.com |
Pros and Cons of Binder Jetting Additive Manufacturing
Evaluating the advantages and limitations of Binder Jetting can help determine its suitability for specific applications:
Pros | Cons |
---|---|
Cost-effective for large production | Limited material options |
High production speed | Lower mechanical properties |
No need for support structures | Post-processing often required |
Ability to produce complex geometries | Powder management challenges |
Wide range of material options | Potential for high porosity |
Characteristics of Binder Jetting Additive Manufacturing
Binder Jetting offers unique characteristics that distinguish it from other additive manufacturing techniques:
- Speed and Efficiency
- Compared to other 3D printing methods like SLS (Selective Laser Sintering) or DMLS (Direct Metal Laser Sintering), Binder Jetting is significantly faster. It’s akin to comparing a high-speed train to a regular passenger train; one is designed for rapid travel, the other for everyday convenience.
- Cost-Effectiveness
- Since Binder Jetting doesn’t require lasers or other expensive equipment, the initial setup costs and ongoing operational expenses are lower. Think of it as the difference between cooking at home and dining out; both provide a meal, but one is much more budget-friendly.
- Material Versatility
- This method can work with a broad spectrum of materials, from metals and ceramics to polymers. It’s like a Swiss Army knife of manufacturing – versatile and capable of handling various tasks.
- Complex Geometry
- Binder Jetting can produce intricate designs and internal structures without the need for support material. Imagine building a complex model ship in a bottle – Binder Jetting makes it feasible without breaking the bottle.
- Environmental Impact
- The process can be more environmentally friendly compared to traditional manufacturing methods, due to less material waste and the potential use of recycled powders. It’s like using every part of an apple when making a pie – efficient and waste-free.
Advantages of Binder Jetting Additive Manufacturing
Binder Jetting offers several advantages over traditional manufacturing methods and other additive manufacturing technologies:
- Design Freedom
- The ability to create complex, intricate designs without the need for support structures opens up endless possibilities for engineers and designers. It’s like having an artist’s complete palette of colors versus a few basic shades.
- Scalability
- Binder Jetting is well-suited for both small-scale and large-scale production. Whether you’re crafting a unique prototype or mass-producing parts, Binder Jetting can scale to meet your needs. Think of it as a versatile chef who can whip up a meal for one or cater a banquet.
- Cost Efficiency
- For large production runs, Binder Jetting can be more cost-effective than other additive manufacturing methods. Lower material waste and faster production times translate to savings. It’s akin to buying in bulk at the grocery store – the more you make, the less each unit costs.
- Material Range
- The technology can work with a wide range of materials, from metals and ceramics to polymers. This versatility makes it suitable for various industries and applications. It’s like having a toolkit with every possible tool, ready for any job.
- Rapid Prototyping
- The speed of Binder Jetting makes it ideal for rapid prototyping, allowing for quick iterations and faster time-to-market. Imagine being able to sketch an idea and see it come to life within hours – that’s the power of Binder Jetting.
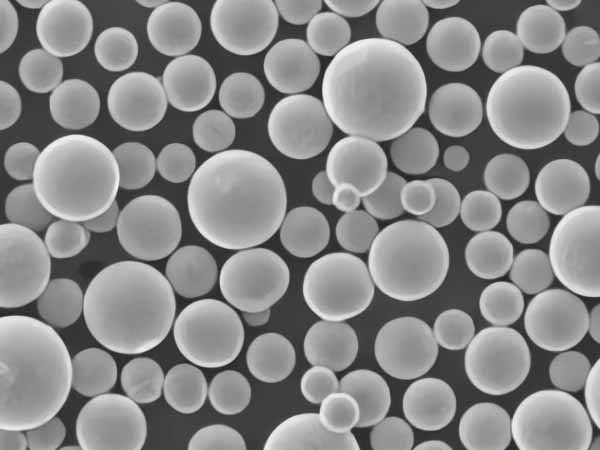
FAQ
Question | Answer |
---|---|
What is Binder Jetting? | Binder Jetting is an additive manufacturing process that uses a liquid binding agent to bond layers of powdered material, creating a solid part. |
What materials can be used in Binder Jetting? | A wide range of materials including metals (like stainless steel, titanium, and Inconel), ceramics, and polymers can be used in Binder Jetting. |
How does Binder Jetting compare to other 3D printing methods? | Binder Jetting is generally faster and more cost-effective than methods like SLS and DMLS, but may require more post-processing to achieve desired surface finish and strength. |
What are the main applications of Binder Jetting? | Binder Jetting is used in various industries such as aerospace, automotive, medical, consumer goods, and industrial manufacturing for parts, prototypes, and complex designs. |
Is post-processing required for Binder Jetting parts? | Yes, parts produced via Binder Jetting often require post-processing such as sintering, infiltration, or surface finishing to achieve desired properties and appearance. |
Can Binder Jetting produce functional parts? | Yes, especially when using metal powders, Binder Jetting can produce functional parts with adequate strength and durability for many applications. |
What are the advantages of Binder Jetting? | Advantages include high production speed, cost efficiency, material versatility, and the ability to create complex geometries without support structures. |
What are the limitations of Binder Jetting? | Limitations include the need for post-processing, potential for high porosity in parts, and limited mechanical properties compared to other methods. |
How environmentally friendly is Binder Jetting? | Binder Jetting can be more environmentally friendly due to reduced material waste and the potential use of recycled powders. |
What industries benefit most from Binder Jetting? | Industries such as aerospace, automotive, medical, consumer goods, and industrial manufacturing benefit greatly from the capabilities of Binder Jetting. |
Conclusion
Binder Jetting Additive Manufacturing is a powerful and versatile technology that is transforming the manufacturing landscape. Its ability to produce complex geometries, work with a wide range of materials, and do so cost-effectively makes it an attractive option for many industries. Whether you’re prototyping a new design or producing parts at scale, Binder Jetting offers a compelling solution that balances speed, cost, and quality. By understanding its strengths and limitations, you can leverage this technology to drive innovation and efficiency in your manufacturing processes.