Multi-material structures represent the cutting edge of engineering, blending different materials to create components that benefit from the unique properties of each material. This approach allows engineers and designers to tailor the mechanical, thermal, and aesthetic properties of a product, leading to significant advancements in industries like aerospace, automotive, and consumer electronics.
In this article, we’ll dive deep into the world of multi-material structures. We’ll explore the different types of materials used, their composition, properties, and applications. We’ll also compare various multi-material structures, analyze their advantages and limitations, and provide insights into the future of this fascinating field.
Overview of Multi-Material Structures
Multi-material structures are an innovative approach that involves the integration of two or more materials within a single component. This concept leverages the strengths of each material, overcoming the limitations that might be present if only a single material were used.
For example, in the automotive industry, combining metals like aluminum with polymers can result in a structure that is both lightweight and strong, enhancing fuel efficiency and safety. In aerospace, the integration of carbon fiber with titanium can produce components that are both extremely strong and lightweight, crucial for high-performance aircraft.
Key Benefits of Multi-Material Structures
- Enhanced Performance: By combining materials, you can achieve superior mechanical and thermal properties.
- Weight Reduction: Multi-material structures often result in lighter components without sacrificing strength.
- Cost Efficiency: Using cheaper materials in less critical areas can reduce overall costs.
- Design Flexibility: Allows for innovative designs that wouldn’t be possible with single-material components.
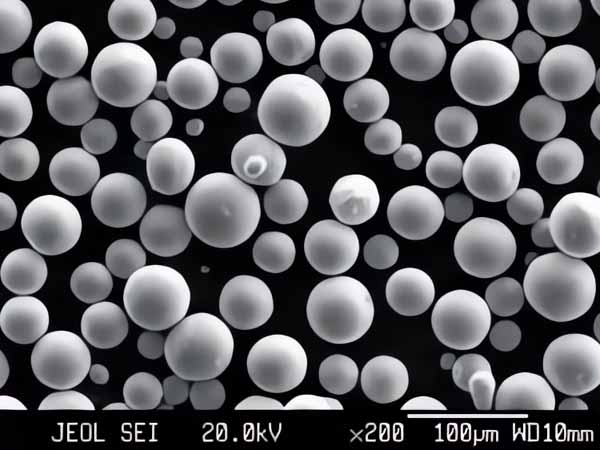
Composition of Multi-Material Structures
The composition of multi-material structures varies widely depending on the application and desired properties. Typically, these structures incorporate a combination of metals, polymers, ceramics, and composites.
Key Materials Used in Multi-Material Structures
Material | Type | Composition | Properties | Applications |
---|---|---|---|---|
Aluminum Alloys | Metal | Al + Mg, Si, Cu | Lightweight, corrosion-resistant, ductile | Automotive, aerospace |
Titanium Alloys | Metal | Ti + Al, V | High strength, lightweight, corrosion-resistant | Aerospace, medical implants |
Carbon Fiber | Composite | Carbon fibers + Resin | Extremely strong, lightweight | Aerospace, sporting goods, automotive |
Polymer Composites | Composite | Polymer matrix + Reinforcement (glass, carbon) | Versatile, lightweight, strong | Automotive, consumer electronics |
Ceramics | Non-metal | SiC, Al2O3 | Hard, brittle, high temperature resistance | Cutting tools, electronics, aerospace |
Stainless Steel | Metal | Fe + Cr, Ni | Strong, corrosion-resistant, durable | Construction, automotive, medical devices |
Copper Alloys | Metal | Cu + Zn, Sn | Excellent conductivity, corrosion-resistant | Electrical components, plumbing |
Nickel Alloys | Metal | Ni + Cr, Mo, Fe | High temperature resistance, corrosion-resistant | Aerospace, chemical processing |
Glass Fiber | Composite | Glass fibers + Polymer | Strong, insulating, lightweight | Construction, automotive, marine |
Magnesium Alloys | Metal | Mg + Al, Zn | Extremely lightweight, good machinability | Automotive, aerospace, electronics |
Properties and Characteristics of Multi-Material Structures
The properties of multi-material structures are highly dependent on the materials used and how they are combined. Below are some key characteristics to consider.
Key Characteristics of Multi-Material Structures
Property | Description | Influencing Factors |
---|---|---|
Mechanical Strength | The ability to withstand forces without breaking or deforming. | Material composition, bonding techniques, and structure design |
Thermal Conductivity | The ability to conduct heat efficiently. | Materials used, interface between materials |
Corrosion Resistance | The ability to resist degradation in harsh environments. | Material selection, protective coatings |
Weight | The mass of the structure, which is crucial in applications where weight reduction is essential. | Material density, design |
Fatigue Resistance | The ability to withstand repeated loading and unloading cycles without failure. | Material choice, bonding quality |
Impact Resistance | The ability to absorb and dissipate energy during sudden impacts. | Material toughness, composite layering |
Aesthetic Appeal | The visual and tactile qualities of the structure, which may influence consumer preference. | Surface finish, material combinations |
Electrical Conductivity | The ability to conduct electricity, important for electronic applications. | Type of metals and composites used |
Types of Multi-Material Structures
There are various types of multi-material structures, each designed to meet specific requirements in different industries. Some of the most common types include:
Hybrid Metal-Composite Structures
These structures combine metals like aluminum or steel with composite materials like carbon fiber. The result is a component that benefits from the strength of metals and the lightweight nature of composites. These are commonly used in the automotive and aerospace industries.
Metal-Polymer Structures
In this type, metals such as aluminum or magnesium are combined with polymers to create lightweight and corrosion-resistant components. These structures are often used in consumer electronics and automotive applications.
Multi-Metal Structures
Multi-metal structures involve the integration of different metals, such as aluminum and steel or copper and nickel. This type of structure is particularly beneficial in applications requiring a combination of high strength and thermal conductivity.
Ceramic-Metal Structures
Ceramic-metal structures combine the hardness and high-temperature resistance of ceramics with the toughness of metals. These are used in cutting tools, aerospace components, and electronics.
3D Printed Multi-Material Structures
Advancements in 3D printing have enabled the creation of complex multi-material structures with precise control over material distribution. This technology is revolutionizing industries like medical implants, aerospace, and prototyping.
-
CM247LC Powder | Nickel Alloy Powder
-
0# Pure Nickel powder
-
NiCoCrAlY alloys powders
-
Rene 142 alloy-Rene Powder
-
Haynes 25 Haynes Powder
-
Best Hastelloy C-22 Powder-High temperature alloy Powder for 3D Printing
-
Best Hastelloy C-276 Powder-High temperature alloy Powder for 3D Printing
-
Best Hastelloy N Powder-High temperature alloy Powder for 3D Printing
-
Best Hastelloy B Powder丨High temperature alloy Powder for 3D Printing
Applications of Multi-Material Structures
Multi-material structures have a wide range of applications across various industries. Below is a table highlighting some key applications.
Applications of Multi-Material Structures
Industry | Application | Materials Used | Benefits |
---|---|---|---|
Automotive | Body panels, chassis components, engine parts | Aluminum, carbon fiber, polymers | Weight reduction, improved fuel efficiency, safety |
Aerospace | Fuselage components, turbine blades, landing gear | Titanium alloys, carbon fiber, ceramics | Strength-to-weight ratio, high-temperature resistance |
Consumer Electronics | Smartphones, laptops, wearable devices | Magnesium alloys, polymers, glass fiber | Lightweight, durability, aesthetic appeal |
Medical Devices | Implants, surgical instruments | Titanium, stainless steel, polymers | Biocompatibility, strength, corrosion resistance |
Construction | Structural components, facade panels, insulating materials | Steel, glass fiber, polymers | Strength, durability, thermal insulation |
Marine | Hull components, propellers, deck structures | Aluminum, stainless steel, composites | Corrosion resistance, lightweight, strength |
Energy | Wind turbine blades, solar panel frames, pipeline components | Composites, stainless steel, ceramics | Durability, resistance to environmental factors |
Sports Equipment | Bicycle frames, golf clubs, helmets | Carbon fiber, aluminum, polymers | Lightweight, high performance, durability |
Chemical Processing | Reactors, piping, valves | Nickel alloys, ceramics, stainless steel | Corrosion resistance, high-temperature capability |
Defense | Armor plating, missile components, structural parts | Titanium alloys, composites, ceramics | Ballistic protection, lightweight, high strength |
Specifications, Sizes, Grades, and Standards
When selecting multi-material structures, it’s essential to consider the specifications, sizes, grades, and standards that apply. Below is a table summarizing some of the key aspects.
Specifications, Sizes, Grades, and Standards of Multi-Material Structures
Material | Specification | Sizes Available | Grades | Standards |
---|---|---|---|---|
Aluminum Alloys | ASTM B209, EN AW-2024, EN AW-7075 | Sheets, plates, extrusions, tubes | 2024, 7075, 6061 | ISO 9001, ASTM B211 |
Titanium Alloys | ASTM B265, Ti-6Al-4V | Sheets, bars, forgings | Ti-6Al-4V, Ti-6Al-4V ELI | AMS 4928, ASTM F136 |
Carbon Fiber | ASTM D3039, ISO 14129 | Rolls, prepregs, panels | T300, T700, M55J | ASTM D7264, ISO 13019 |
Polymer Composites | ASTM D5956, ISO 14693 | Sheets, rods, custom shapes | SMC, BMC, CFRP | ASTM D5766, ISO 75-2 |
Ceramics | ASTM C1161, ISO 6872 | Custom shapes, plates, rods | Al2O3, SiC, ZrO2 | ISO 6872, ASTM C1161 |
Stainless Steel | ASTM A240, ISO 15510 | Sheets, plates, pipes, bars | 304, 316, 17-4PH | ASME SA240, ASTM A312 |
Copper Alloys | ASTM B281, ASTM B622 | Tubes, sheets, rods | C11000, C70600 | ASTM B134, ISO 281 |
Nickel Alloys | ASTM B443, ASTM B564 | Bars, plates, sheets | Inconel 625, Monel 400 | ASTM B444, ISO 6265 |
Glass Fiber | ASTM D3808, ISO 13019 | Sheets, rods, woven fabrics | E-glass, S-glass | ASTM D3039, ISO 9001 |
Magnesium Alloys | ASTM B90, AMS 4375 | Sheets, bars, extrusions | AZ31B, ZK60 | ASTM B107, ISO 6892 |
Suppliers and Pricing of Multi-Material Structures
Finding reliable suppliers and understanding pricing for multi-material structures is crucial for making informed decisions. Here’s an overview of notable suppliers and typical pricing for various materials.
Suppliers and Pricing for Multi-Material Structures
Material | Supplier | Typical Pricing Range | Description |
---|---|---|---|
Aluminum Alloys | Kaiser Aluminum, Constellium | $2 – $6 per pound | Leading supplier of aluminum products |
Titanium Alloys | Timet, VSMPO-Avisma | $20 – $50 per pound | Major producer of titanium alloys |
Carbon Fiber | Hexcel, Toray | $30 – $80 per pound | Top manufacturers of carbon fiber |
Polymer Composites | Owens Corning, SGL Carbon | $10 – $50 per pound | Providers of various composite materials |
Ceramics | Saint-Gobain, Kyocera | $15 – $100 per pound | Renowned ceramic materials suppliers |
Stainless Steel | Outokumpu, Aperam | $3 – $10 per pound | Leading suppliers of stainless steel |
Copper Alloys | Wieland, Mueller Industries | $4 – $12 per pound | Prominent suppliers of copper alloys |
Nickel Alloys | Haynes International, Special Metals | $50 – $150 per pound | Specialized suppliers of nickel alloys |
Glass Fiber | Owens Corning, Jushi Group | $5 – $15 per pound | Major suppliers of glass fiber materials |
Magnesium Alloys | Magnesium Elektron, UACJ | $8 – $25 per pound | Key suppliers of magnesium alloys |
Advantages and Limitations of Multi-Material Structures
Multi-material structures offer numerous advantages, but they also come with certain limitations. Here’s a comparison to help understand their benefits and potential drawbacks.
Advantages and Limitations of Multi-Material Structures
Aspect | Advantages | Limitations |
---|---|---|
Strength-to-Weight Ratio | Combines materials for optimal performance, enhancing strength while reducing weight. | Complex manufacturing processes may increase costs. |
Design Flexibility | Enables innovative designs and tailored properties for specific applications. | Integration of different materials can complicate the design and assembly. |
Cost Efficiency | Allows for the use of cost-effective materials in less critical areas. | Initial setup costs for multi-material manufacturing can be high. |
Durability | Improved resistance to wear, corrosion, and other environmental factors. | Potential issues with material compatibility and bonding. |
Thermal and Electrical Properties | Offers tailored thermal and electrical characteristics by combining materials. | Requires precise control over material interfaces to achieve desired properties. |
Environmental Impact | Potential for reduced environmental impact through lightweight designs and efficiency. | The use of multiple materials can complicate recycling and disposal. |
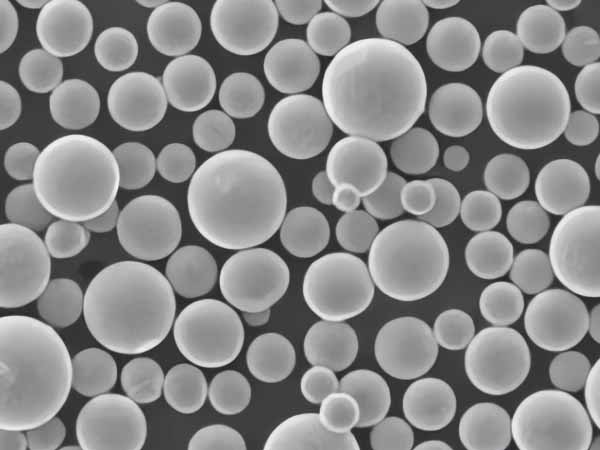
FAQs
Here’s a comprehensive FAQ section addressing common questions about multi-material structures.
Question | Answer |
---|---|
What are multi-material structures? | Multi-material structures combine two or more materials to take advantage of their individual properties, resulting in enhanced performance and efficiency. |
What are the benefits of using multi-material structures? | They offer improved performance, weight reduction, cost efficiency, and design flexibility compared to single-material components. |
Which industries use multi-material structures the most? | Industries such as aerospace, automotive, consumer electronics, medical devices, and construction commonly use multi-material structures. |
How do multi-material structures impact manufacturing? | They can complicate manufacturing processes due to the need for precise integration and bonding of different materials. |
Are multi-material structures more expensive than single-material ones? | While they can be more costly initially, the benefits of improved performance and reduced lifecycle costs can offset the higher upfront expense. |
Can multi-material structures be recycled? | Recycling can be challenging due to the combination of materials, but advances in recycling technologies are improving this aspect. |
Conclusion and Future Outlook
Multi-material structures represent a significant advancement in engineering and design. They offer unparalleled benefits in terms of performance, weight, and versatility, making them a preferred choice in various high-tech industries. However, they also present challenges in terms of manufacturing complexity and cost.
As technology progresses, we can expect continued innovation in multi-material design and manufacturing techniques. Emerging technologies, such as advanced 3D printing and new material composites, will likely enhance the capabilities and applications of multi-material structures.
The future of multi-material structures promises even more efficient, effective, and sustainable solutions across industries, driving further advancements in engineering and design.