Introduction
In the world of materials science and engineering, high purity powders play a crucial role in various applications. These powders, often composed of metals, ceramics, or other advanced materials, are essential for producing components that require high levels of precision and performance. Whether you’re involved in manufacturing, research, or product development, understanding how to prepare high purity powders is fundamental.
But what exactly goes into the preparation of these powders? How do you ensure that the powders meet the stringent standards required for your application? In this article, we’ll dive deep into the topic of preparing high purity powders, discussing everything from the composition and characteristics to the advantages and challenges associated with different types of powders. We’ll also provide detailed comparisons of specific metal powder models, helping you make informed decisions.
Overview of High Purity Powders
High purity powders are finely divided solid materials, typically with particle sizes ranging from a few micrometers to nanometers. These powders are characterized by their chemical purity, which is often greater than 99.9%, making them suitable for high-performance applications. The preparation of high purity powders involves a series of complex processes designed to achieve the desired purity, particle size distribution, and morphology.
High purity powders are used in a wide range of industries, including aerospace, electronics, automotive, and medical devices. They are essential for producing components that require high strength, corrosion resistance, electrical conductivity, and other critical properties.
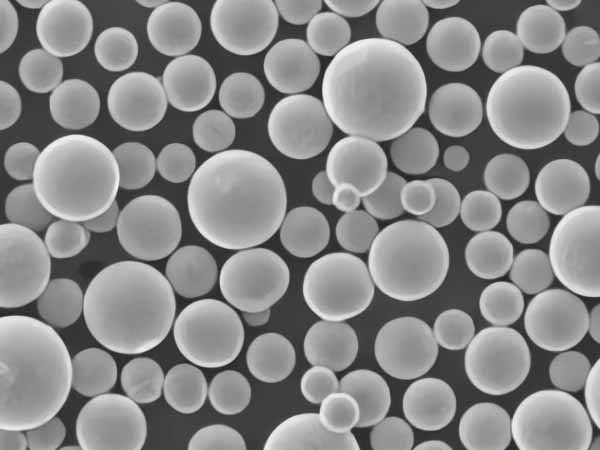
Composition of High Purity Powders
The composition of high purity powders can vary significantly depending on the intended application. Here, we’ll explore some of the most common types of high purity metal powders, their compositions, and their unique properties.
Metal Powder | Composition | Properties | Applications |
---|---|---|---|
Aluminum (Al) | Al > 99.9% | Lightweight, high strength, corrosion-resistant | Aerospace, automotive, electronics |
Copper (Cu) | Cu > 99.9% | High electrical conductivity, ductility, thermal conductivity | Electrical components, heat exchangers, semiconductors |
Titanium (Ti) | Ti > 99.9% | High strength-to-weight ratio, biocompatibility, corrosion resistance | Medical implants, aerospace components, sports equipment |
Nickel (Ni) | Ni > 99.9% | Corrosion resistance, high-temperature stability, magnetic properties | Turbine blades, batteries, electronics |
Cobalt (Co) | Co > 99.9% | Magnetic properties, high wear resistance, high-temperature performance | Magnets, superalloys, cutting tools |
Silver (Ag) | Ag > 99.9% | Highest electrical conductivity, antimicrobial properties, malleability | Electronics, jewelry, medical devices |
Gold (Au) | Au > 99.9% | Excellent corrosion resistance, electrical conductivity, malleability | Electronics, jewelry, dentistry |
Platinum (Pt) | Pt > 99.9% | High melting point, catalytic properties, corrosion resistance | Catalysts, medical devices, electronics |
Iron (Fe) | Fe > 99.9% | Magnetic properties, strength, versatility | Automotive components, construction, electronics |
Zinc (Zn) | Zn > 99.9% | Corrosion resistance, galvanizing properties, low melting point | Coatings, batteries, alloys |
Each of these metal powders has unique characteristics that make them suitable for specific applications. For example, aluminum is widely used in the aerospace industry due to its lightweight and high-strength properties, while copper is preferred in electrical applications for its excellent conductivity.
Characteristics of High Purity Powders
When selecting high purity powders for a particular application, several characteristics must be considered:
- Particle Size Distribution: The size of the particles can significantly impact the performance of the powder in various applications. Finer powders generally offer better sintering properties but may be more challenging to handle.
- Morphology: The shape of the particles, whether spherical, irregular, or flake-like, can influence the packing density, flowability, and surface area of the powder.
- Purity: The chemical purity of the powder is critical in applications where impurities can cause defects or degrade performance. High purity powders typically have impurities less than 0.1%.
- Surface Area: A higher surface area can enhance the reactivity of the powder, which is essential in applications like catalysis.
- Flowability: The ease with which the powder flows is crucial in manufacturing processes, especially in powder metallurgy and additive manufacturing.
- Density: The bulk and tap density of the powder can affect its packing behavior and the final properties of the sintered product.
Advantages of High Purity Powders
High purity powders offer several advantages that make them indispensable in advanced manufacturing and research:
- Enhanced Performance: The high chemical purity ensures that the final products have superior properties, such as higher strength, better conductivity, and improved corrosion resistance.
- Consistency: The controlled particle size distribution and morphology result in consistent performance across different batches, which is crucial for quality control.
- Versatility: High purity powders can be used in a wide range of applications, from aerospace components to medical implants, making them highly versatile materials.
- Improved Processability: The excellent flowability and density of high purity powders make them easier to process, reducing the likelihood of defects during manufacturing.
Challenges in Preparing High Purity Powders
While high purity powders offer numerous benefits, their preparation is not without challenges. Some of the key challenges include:
- Cost: The production of high purity powders often involves complex processes that can be expensive. This cost can be a significant barrier, especially for small-scale operations.
- Contamination: Maintaining high levels of purity requires strict control over the production environment to prevent contamination from external sources.
- Handling: Finer powders, which are often required for certain applications, can be challenging to handle due to their tendency to agglomerate or become airborne.
- Consistency: Achieving consistent particle size distribution and morphology across different batches can be difficult, particularly in large-scale production.
Processes for Preparing High Purity Powders
There are several methods for preparing high purity powders, each with its own advantages and limitations. Here, we’ll explore some of the most common processes:
1. Atomization
Atomization is one of the most widely used methods for producing metal powders. It involves breaking up a molten metal stream into fine droplets, which then solidify into powder particles. There are several types of atomization processes:
- Gas Atomization: In gas atomization, a high-pressure gas stream (such as nitrogen or argon) is used to atomize the molten metal. This process is known for producing spherical particles with a narrow size distribution.
- Water Atomization: Water atomization uses high-pressure water jets to break up the molten metal. This method is typically used for producing powders with irregular shapes.
- Plasma Atomization: Plasma atomization involves using a plasma torch to melt the metal, which is then atomized by a gas stream. This process is often used for producing high-purity powders with a controlled particle size.
2. Chemical Reduction
Chemical reduction is a process in which metal salts or oxides are reduced to pure metal powders using a reducing agent. This method is commonly used for producing powders of metals that are difficult to atomize, such as tungsten and molybdenum.
3. Mechanical Milling
Mechanical milling involves the use of high-energy ball mills to grind bulk metal into fine powder. This process is suitable for producing powders with a wide range of particle sizes, but it may introduce contamination from the milling media.
4. Electrolysis
Electrolysis is a process in which metal ions are reduced to their elemental form at the cathode of an electrolytic cell. This method is often used for producing high-purity powders of metals like copper and silver.
5. Sol-Gel Process
The sol-gel process is a chemical method for producing metal oxide powders. It involves the hydrolysis and condensation of metal alkoxides, followed by drying and calcination to form a fine powder. This method is commonly used for producing ceramic powders.
6. Precipitation
Precipitation involves the formation of a solid from a solution through a chemical reaction. The precipitate is then filtered, washed, and dried to obtain the powder. This process is often used for producing powders of metals like nickel and cobalt.
Applications of High Purity Powders
High purity powders are used in a wide range of applications across various industries. Below is a table summarizing some of the key applications:
Industry | Application | Powder Type | Benefits |
---|---|---|---|
Aerospace | Turbine blades, structural components | Nickel, titanium | High strength, corrosion resistance, high-temperature stability |
Automotive | Engine components, exhaust systems | Aluminum, iron | Lightweight, high strength, wear resistance |
Electronics | Conductive inks, semiconductors | Copper, silver | High electrical conductivity, thermal conductivity |
Medical | Implants, dental restorations | Titanium, cobalt | Biocompatibility, corrosion resistance, strength |
Energy | Fuel cells, batteries | Platinum, cobalt | Catalytic properties, high energy density |
Jewelry | Ornaments, watches | Gold, silver | Malleability, corrosion resistance, aesthetic appeal |
Construction | Coatings, structural elements | Zinc, iron | Corrosion resistance, durability, versatility |
Defense | Armor, ammunition | Tungsten, titanium | High density,strength, impact resistance |
Specifications, Sizes, Grades, and Standards
When selecting high purity powders for specific applications, it’s important to consider the specifications, sizes, grades, and standards that apply. Below is a table summarizing some of the key parameters:
Metal Powder | Particle Size (µm) | Purity (%) | Grade | Standard |
---|---|---|---|---|
Aluminum (Al) | 5-45 | > 99.9% | 5N | ASTM B928 |
Copper (Cu) | 10-50 | > 99.9% | 4N | ASTM B170 |
Titanium (Ti) | 15-45 | > 99.9% | 5N | ASTM B348 |
Nickel (Ni) | 10-63 | > 99.9% | 4N | ASTM B333 |
Cobalt (Co) | 20-50 | > 99.9% | 4N | ASTM F75 |
Silver (Ag) | 1-10 | > 99.9% | 5N | ASTM B328 |
Gold (Au) | 2-20 | > 99.9% | 5N | ASTM B488 |
Platinum (Pt) | 1-10 | > 99.9% | 5N | ASTM B600 |
Iron (Fe) | 10-50 | > 99.9% | 4N | ASTM B216 |
Zinc (Zn) | 5-25 | > 99.9% | 4N | ASTM B328 |
Suppliers and Pricing Details
The cost of high purity powders can vary depending on the metal, purity, and particle size. Below is a table summarizing some of the leading suppliers and pricing details:
Supplier | Metal Powder | Price (USD/kg) | Minimum Order Quantity (kg) | Location |
---|---|---|---|---|
Advanced Powders & Coatings | Aluminum | $150 | 1 | USA |
Höganäs AB | Copper | $200 | 5 | Sweden |
Tekna | Titanium | $500 | 1 | Canada |
American Elements | Nickel | $250 | 2 | USA |
Metal Powder Products | Cobalt | $300 | 3 | USA |
Sigma-Aldrich | Silver | $1000 | 0.5 | USA |
Goodfellow | Gold | $50,000 | 0.1 | UK |
Johnson Matthey | Platinum | $60,000 | 0.05 | UK |
Rio Tinto Metal Powders | Iron | $100 | 10 | Canada |
Umicore | Zinc | $150 | 2 | Belgium |
Comparing Pros and Cons of Different High Purity Powders
Selecting the right high purity powder for your application requires careful consideration of the pros and cons associated with each type. Below is a comparative analysis:
Metal Powder | Advantages | Disadvantages |
---|---|---|
Aluminum | Lightweight, high strength, corrosion resistance | High cost, reactivity with oxygen |
Copper | Excellent electrical conductivity, thermal conductivity | Prone to oxidation, relatively heavy |
Titanium | High strength-to-weight ratio, biocompatibility | Expensive, difficult to process |
Nickel | Corrosion resistance, high-temperature stability | High cost, potential health hazards |
Cobalt | High wear resistance, magnetic properties | Toxicity concerns, expensive |
Silver | Highest electrical conductivity, antimicrobial properties | High cost, tarnishes easily |
Gold | Excellent corrosion resistance, malleability | Extremely expensive, soft metal |
Platinum | High melting point, catalytic properties | Extremely expensive, limited supply |
Iron | Strength, versatility, low cost | Prone to rusting, heavy |
Zinc | Corrosion resistance, low melting point | Brittle, prone to cracking |
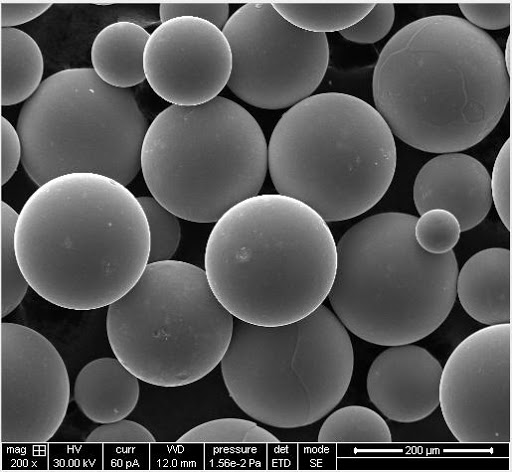
FAQ
Question | Answer |
---|---|
What are high purity powders? | High purity powders are finely divided materials with a chemical purity of greater than 99.9%, used in applications requiring precise material properties. |
How are high purity powders made? | High purity powders can be made using processes like atomization, chemical reduction, mechanical milling, electrolysis, sol-gel processes, and precipitation. |
What are the applications of high purity powders? | High purity powders are used in aerospace, automotive, electronics, medical devices, energy, jewelry, and construction industries. |
What are the challenges in preparing high purity powders? | Challenges include high production costs, contamination control, handling difficulties, and maintaining consistency. |
Which metals are commonly used in high purity powders? | Common metals include aluminum, copper, titanium, nickel, cobalt, silver, gold, platinum, iron, and zinc. |
What factors should I consider when selecting high purity powders? | Consider particle size distribution, morphology, purity, surface area, flowability, and density. |
Why are high purity powders expensive? | The high cost is due to the complex processes required to achieve the desired purity, consistency, and particle size. |
Can high purity powders be customized? | Yes, powders can be customized in terms of particle size, morphology, and purity to meet specific application requirements. |
Conclusion
The preparation of high purity powders is a complex process that requires careful consideration of various factors, including the type of metal, desired purity, particle size, and application requirements. By understanding the characteristics, advantages, and challenges associated with different types of high purity powders, you can make informed decisions that will help you achieve the best results for your specific needs.
Whether you’re working in aerospace, electronics, medical devices, or another high-tech industry, high purity powders offer the precision and performance needed to meet the most demanding specifications. With the right knowledge and resources, you can harness the full potential of these advanced materials to drive innovation and success in your field.