Overview
Gas turbines are the workhorses of power generation, providing energy in various sectors from aviation to industrial applications. A crucial component within this system is the atomizing air system, which plays a significant role in enhancing combustion efficiency. But what exactly is this system, how does it work, and why is it so vital?
In this comprehensive guide, we’ll dive deep into the world of gas turbine atomizing air systems, exploring everything from their fundamental workings to their specific components, benefits, and the various metal powder models used. By the end of this article, you’ll have a clear understanding of why these systems are critical for modern energy production and how to select the right components for your specific needs.
What is a Gas Turbine Atomizing Air System?
The atomizing air system in a gas turbine is a specialized mechanism designed to enhance the combustion process by finely dispersing fuel into the combustion chamber. This ensures that the fuel mixes thoroughly with air, resulting in more efficient and complete combustion. Without an effective atomizing air system, a gas turbine could suffer from incomplete combustion, leading to reduced efficiency and increased emissions.
How Does the Gas Turbine Atomizing Air System Work?
The system works by introducing compressed air into the fuel stream at high velocities. This process breaks the fuel into tiny droplets, creating a fine mist that mixes evenly with the incoming air. The result is a homogeneous mixture that burns more efficiently, producing more energy and fewer pollutants.
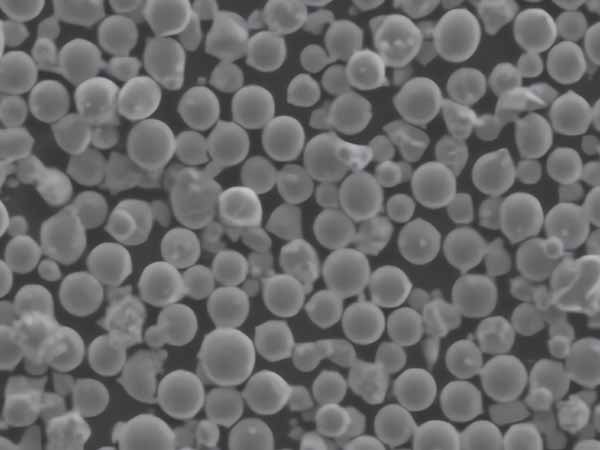
Composition of Gas Turbine Atomizing Air System
The atomizing air system is made up of several critical components, each playing a vital role in the overall functionality of the gas turbine. These include:
- Air Compressor: This component compresses the air before it enters the combustion chamber.
- Nozzles: These are responsible for dispersing the compressed air and fuel into fine droplets.
- Piping and Valves: These direct the flow of air and fuel to ensure proper mixing.
- Control Systems: These systems monitor and adjust the air-fuel ratio to optimize combustion efficiency.
Key Components of Gas Turbine Atomizing Air System
Component | Function | Material Composition | Durability | Maintenance Requirements |
---|---|---|---|---|
Air Compressor | Compresses air for fuel atomization | High-strength alloys | High | Regular inspection |
Nozzles | Disperse fuel and air into fine droplets | Stainless steel, ceramic coatings | Moderate | Periodic cleaning |
Piping and Valves | Directs flow of air and fuel | Alloy steel, nickel alloys | High | Regular inspection |
Control Systems | Monitors and adjusts air-fuel ratio | Electronic components | High | Software updates, calibration |
Characteristics of Gas Turbine Atomizing Air System
When it comes to the characteristics of an atomizing air system, several key factors define its performance:
- Efficiency: A good atomizing air system maximizes fuel combustion, leading to higher overall efficiency.
- Durability: The components must withstand high temperatures and pressures without degrading.
- Precision: The system needs to maintain a precise air-fuel mixture to ensure optimal combustion.
- Maintenance: While robust, the system should be easy to maintain, with accessible components and straightforward procedures.
Key Characteristics of Gas Turbine Atomizing Air System
Characteristic | Description | Impact on Performance |
---|---|---|
Efficiency | Ability to maximize fuel combustion | Higher efficiency, lower emissions |
Durability | Resistance to wear and tear at high temperatures | Longer lifespan, reduced downtime |
Precision | Accuracy in maintaining air-fuel mixture | Stable operation, consistent output |
Maintenance | Ease of maintenance and component access | Lower operational costs, less downtime |
Advantages of Gas Turbine Atomizing Air System
Gas turbine atomizing air systems offer numerous advantages that make them indispensable in various industrial applications:
- Enhanced Efficiency: By ensuring complete combustion, these systems reduce fuel consumption and emissions.
- Lower Emissions: More complete combustion leads to fewer pollutants being released into the environment.
- Improved Durability: High-quality materials and robust design mean these systems last longer, reducing the need for frequent replacements.
- Cost-Effective: Although the initial investment might be high, the long-term savings from improved efficiency and reduced maintenance make it a cost-effective solution.
Advantages of Gas Turbine Atomizing Air System
Advantage | Description | Benefit |
---|---|---|
Enhanced Efficiency | Complete combustion reduces fuel consumption | Cost savings, environmental benefits |
Lower Emissions | Fewer pollutants are produced | Compliance with regulations |
Improved Durability | High-quality materials increase the system’s lifespan | Reduced replacement costs |
Cost-Effective | Long-term savings outweigh initial investment | Higher ROI |
Specific Metal Powder Models for Gas Turbine Atomizing Air System
The atomizing air system’s efficiency largely depends on the materials used in its construction. Metal powders play a crucial role in the manufacturing of key components, such as nozzles and piping, due to their unique properties.
Here are 10 specific metal powder models commonly used in gas turbine atomizing air systems:
- Inconel 718: A nickel-chromium alloy known for its high strength and corrosion resistance at elevated temperatures.
- Hastelloy X: A nickel-molybdenum alloy with excellent oxidation resistance and weldability.
- Stellite 6: A cobalt-based alloy renowned for its wear resistance and hardness.
- Ti-6Al-4V (Titanium Alloy): Lightweight and strong, this alloy is often used in aerospace applications.
- Haynes 282: An age-hardenable nickel superalloy that offers a balance of creep strength and weldability.
- Rene 41: A nickel-based superalloy that maintains its strength at high temperatures.
- Cobalt Chrome (CoCr): An alloy with high wear resistance and biocompatibility, making it ideal for high-stress components.
- Maraging Steel: A high-strength steel alloy known for its toughness and malleability.
- Aluminum Oxide (Al2O3): Used as a coating for components to improve wear and corrosion resistance.
- Tungsten Carbide: Extremely hard and wear-resistant, used for nozzles and other critical components.
Specific Metal Powder Models for Gas Turbine Atomizing Air System
Metal Powder Model | Composition | Properties | Applications | Advantages |
---|---|---|---|---|
Inconel 718 | Nickel-Chromium | High strength, corrosion resistance | Nozzles, piping | High durability, temperature resistance |
Hastelloy X | Nickel-Molybdenum | Oxidation resistance, weldability | Combustion chambers, piping | Excellent weldability, corrosion resistance |
Stellite 6 | Cobalt-based | Wear resistance, hardness | Valve seats, nozzles | High wear resistance, durability |
Ti-6Al-4V | Titanium, Aluminum, Vanadium | Lightweight, high strength | Aerospace components, nozzles | Strong, lightweight |
Haynes 282 | Nickel-based | Creep strength, weldability | High-temperature components | Good balance of properties |
Rene 41 | Nickel-based | High strength at high temperatures | Turbine blades, combustion parts | High temperature stability |
Cobalt Chrome (CoCr) | Cobalt, Chromium | Wear resistance, biocompatibility | High-stress components, nozzles | High strength, biocompatible |
Maraging Steel | Iron-Nickel | High strength, malleability | Shafts, gears | Tough, easy to machine |
Aluminum Oxide (Al2O3) | Aluminum, Oxygen | Hard, wear-resistant | Coatings, protective layers | High hardness, corrosion resistance |
Tungsten Carbide | Tungsten, Carbon | Extremely hard, wear-resistant | Nozzles, cutting tools | High wear resistance, hardness |
Applications of Gas Turbine Atomizing Air Systems
Gas turbine atomizing air systems find applications across a wide range of industries due to their efficiency and reliability. Here’s a look at some of the most common applications:
- Power Generation: In power plants, atomizing air systems are essential for ensuring efficient combustion in gas turbines, leading to more power output and reduced emissions.
- Aerospace: Aircraft engines use atomizing air systems to ensure the fuel burns efficiently, providing the necessary thrust while minimizing fuel consumption.
- Oil and Gas Industry: These systems are used in the extraction and processing of oil and gas, where efficient fuel combustion is crucial for operational efficiency.
- Industrial Manufacturing:Atomizing air systems are also employed in various manufacturing processes where precise fuel combustion is required.
- Marine Propulsion: In marine engines, these systems help improve fuel efficiency and reduce emissions, which is crucial for meeting environmental regulations.
Applications of Gas Turbine Atomizing Air Systems
Industry | Application | Benefits |
---|---|---|
Power Generation | Enhances combustion efficiency in power plants | More power, reduced emissions |
Aerospace | Ensures efficient fuel combustion in aircraft | Improved fuel efficiency, lower costs |
Oil and Gas | Used in extraction and processing operations | Increased operational efficiency |
Industrial Manufacturing | Precise fuel combustion in manufacturing | Better product quality, energy savings |
Marine Propulsion | Improves fuel efficiency in marine engines | Compliance with environmental regulations |
Specifications, Sizes, Grades, and Standards
When selecting components for a gas turbine atomizing air system, it’s crucial to consider the specifications, sizes, grades, and standards that apply to your particular application. These factors determine the performance, compatibility, and longevity of the system.
Table: Specifications, Sizes, Grades, and Standards for Gas Turbine Atomizing Air System Components
Component | Specification | Size Range | Grade | Standard |
---|---|---|---|---|
Air Compressor | ASME B31.3 | 1″ to 12″ | AISI 316 | ASME, ANSI, ISO |
Nozzles | API 614 | Custom sizes | Inconel 718 | ASTM, API, ISO |
Piping | ASME B36.10 | 1/2″ to 48″ | ASTM A106 Gr.B | ASME, ANSI, API |
Valves | API 600 | 1/2″ to 24″ | Stainless Steel | API, ANSI, DIN |
Control Systems | IEC 61508 | Custom sizes | – | IEC, IEEE, ISO |
Suppliers and Pricing Details
The selection of the right supplier is critical to ensuring the quality and reliability of the gas turbine atomizing air system. Below is a comparison of various suppliers, along with estimated pricing details for different components.
Table: Suppliers and Pricing Details for Gas Turbine Atomizing Air Systems
Supplier | Location | Component Offered | Pricing | Reputation |
---|---|---|---|---|
ABC Compressors | USA | Air Compressors | $10,000 – $50,000 | High |
XYZ Nozzles | Germany | Fuel Nozzles | $5,000 – $20,000 | Very High |
PQR Valves | Japan | Piping and Valves | $2,000 – $10,000 | High |
LMN Controls | South Korea | Control Systems | $8,000 – $25,000 | High |
GHI Metal Powders | China | Metal Powders | $100 – $1,000 per kg | Medium |
Pros and Cons: Gas Turbine Atomizing Air System
Every system has its advantages and disadvantages, and the gas turbine atomizing air system is no exception. Here’s a closer look at the pros and cons:
Table: Pros and Cons of Gas Turbine Atomizing Air System
Aspect | Pros | Cons |
---|---|---|
Efficiency | High fuel combustion efficiency | Requires regular maintenance to sustain performance |
Durability | Components are highly durable | High initial investment |
Emissions | Lower emissions due to complete combustion | Complex system, requiring skilled operators |
Cost | Cost-effective over the long term | Expensive to install |
Comparing Metal Powder Models: Which One is Right for You?
Choosing the right metal powder model for your gas turbine atomizing air system depends on various factors such as temperature, pressure, and specific application requirements. Here’s a comparison to help you make an informed decision:
Table: Comparison of Metal Powder Models for Gas Turbine Atomizing Air System
Metal Powder Model | Best For | Not Suitable For | Why Choose It? |
---|---|---|---|
Inconel 718 | High-temperature applications | Low-budget projects | Superior strength and corrosion resistance |
Hastelloy X | Corrosive environments | Non-weldable applications | Excellent weldability and oxidation resistance |
Stellite 6 | High-wear environments | Applications requiring high ductility | Outstanding wear resistance |
Ti-6Al-4V | Lightweight, strong components | High-temperature applications | Combines strength with lightweight properties |
Haynes 282 | Creep-resistant components | Applications requiring quick fabrication | Balance of creep strength and weldability |
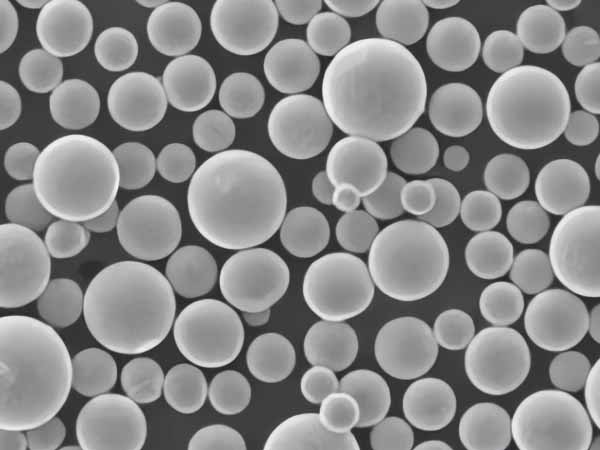
FAQ
Below are some frequently asked questions about gas turbine atomizing air systems, aimed at helping you better understand the topic.
Question | Answer |
---|---|
What is the primary function of the atomizing air system in a gas turbine? | It enhances combustion efficiency by finely dispersing fuel into the combustion chamber. |
What materials are commonly used for manufacturing atomizing air systems? | High-strength alloys like Inconel 718, Hastelloy X, and Stellite 6 are commonly used. |
How does an atomizing air system improve gas turbine efficiency? | By ensuring complete combustion, it reduces fuel consumption and emissions. |
What are the maintenance requirements for these systems? | Regular inspection and cleaning of components like nozzles and air compressors are necessary. |
Can atomizing air systems be used in all types of gas turbines? | Yes, but the specific design and materials may vary depending on the turbine’s application. |
Conclusion
The gas turbine atomizing air system is a crucial component in modern power generation and industrial processes. Its ability to enhance combustion efficiency while reducing emissions makes it an indispensable part of gas turbines. By understanding the components, characteristics, and specific metal powder models, you can ensure that your system operates at peak performance, delivering both economic and environmental benefits.
Incorporating the right materials and regularly maintaining the system will prolong its lifespan and keep your operations running smoothly. Whether you’re in power generation, aerospace, or industrial manufacturing, investing in a high-quality gas turbine atomizing air system is a decision that pays off in the long run.