Gas atomization is an advanced and highly efficient process utilized in the production of metal powders. These powders are critical in various industries, including additive manufacturing, aerospace, automotive, and medical applications. This article dives deep into the world of gas atomization, exploring the technology behind it, the specific metal powders produced, their properties, and the advantages of using gas atomization compared to other methods. Whether you’re a seasoned industry professional or someone just curious about the process, this guide will walk you through everything you need to know.
Overview of Gas Atomization
Gas atomization is a process where molten metal is disintegrated into fine droplets by a high-velocity gas stream. These droplets then solidify into powder particles with controlled size and shape, making them ideal for various high-tech applications. Unlike other atomization methods, gas atomization offers superior control over powder morphology and particle size distribution, leading to high-quality metal powders.
The process involves the use of inert gases like nitrogen, argon, or helium to ensure that the metal does not oxidize during atomization, maintaining the purity of the powder. This process is particularly crucial for producing metal powders used in applications where material performance cannot be compromised.
Key Characteristics of Gas Atomization:
- High Purity: Due to the use of inert gases, the powders produced are of very high purity.
- Uniform Particle Size: The process allows for precise control over particle size distribution.
- Spherical Powder Shape: The powder particles produced are typically spherical, which is beneficial for flowability and packing density.
- Versatility: Capable of atomizing a wide range of metals and alloys.
- Scalability: Suitable for both small-scale laboratory production and large-scale industrial manufacturing.
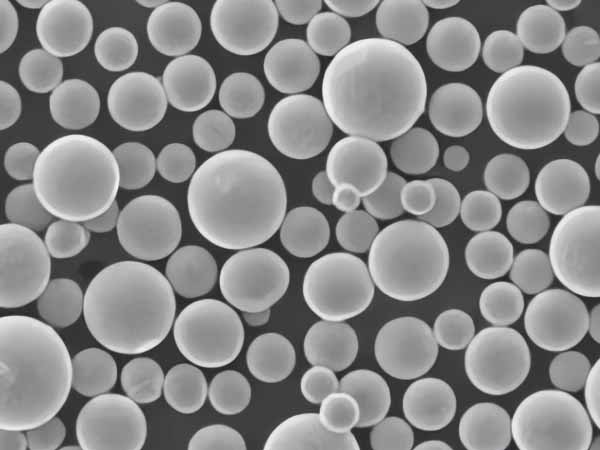
Understanding the Gas Atomization Process
How Does Gas Atomization Work?
The gas atomization process can be broken down into several key steps:
- Melting the Metal: The process begins with melting the metal or alloy in a controlled environment, typically using an induction furnace. The furnace temperature is carefully monitored to ensure complete melting.
- Atomization: Once the metal is molten, it is poured into a tundish, a type of intermediate holding container. From here, the molten metal flows through a small nozzle. As it exits the nozzle, it is immediately hit by a high-velocity gas stream. This gas stream breaks the molten metal into tiny droplets.
- Solidification: These droplets rapidly solidify as they travel away from the gas stream. The rapid cooling rate helps in forming fine, uniform powder particles.
- Collection: The solidified particles are then collected, classified, and sometimes sieved to ensure the desired particle size distribution is achieved.
Advantages of Gas Atomization Compared to Other Atomization Methods
Compared to other methods like water atomization, gas atomization offers distinct advantages:
- Better Control Over Particle Morphology: Gas atomization generally produces more spherical particles, which are preferred in many applications.
- Higher Purity Levels: Inert gas usage minimizes oxidation, which is a significant issue in water atomization.
- Superior Surface Finish: The powders produced have a smoother surface finish due to the absence of water contact.
Composition of Gas Atomized Powders
Different metals and alloys can be atomized using the gas atomization process. Below are some of the most commonly used materials:
Metal/Alloy | Composition | Key Properties | Applications |
---|---|---|---|
Stainless Steel (316L) | Fe, Cr, Ni, Mo | High corrosion resistance, good weldability | Medical implants, aerospace components |
Cobalt-Chrome (CoCr) | Co, Cr, Mo | Excellent wear and corrosion resistance | Dental implants, orthopedic devices |
Titanium (Ti-6Al-4V) | Ti, Al, V | High strength-to-weight ratio, excellent biocompatibility | Aerospace parts, biomedical devices |
Nickel Superalloys (Inconel 718) | Ni, Cr, Fe, Nb, Mo | High-temperature resistance, oxidation resistance | Turbine blades, aerospace components |
Aluminum Alloys (AlSi10Mg) | Al, Si, Mg | Lightweight, good thermal properties | Automotive parts, lightweight structures |
Copper Alloys (CuCrZr) | Cu, Cr, Zr | High electrical and thermal conductivity | Electrical components, heat exchangers |
Tool Steel (M2) | Fe, C, W, Mo | High hardness, wear resistance | Cutting tools, dies, molds |
Iron-Based Alloys (FeNiCo) | Fe, Ni, Co | High magnetic permeability, good mechanical properties | Soft magnetic components, aerospace applications |
Magnesium Alloys (AZ91D) | Mg, Al, Zn | Very lightweight, good strength | Automotive parts, aerospace components |
Precious Metals (Gold, Silver) | Au, Ag | Excellent conductivity, corrosion resistance | Electronics, jewelry, medical devices |
Applications of Gas Atomized Metal Powders
Gas atomized powders find use in a wide array of industries due to their superior properties. Below is a summary of applications:
Industry | Applications | Benefits |
---|---|---|
Additive Manufacturing | 3D printing of complex parts | High precision, minimal waste |
Aerospace | Turbine blades, structural components | High strength, lightweight |
Automotive | Lightweight structural parts, engine components | Improved fuel efficiency |
Medical | Implants, prosthetics, surgical tools | Biocompatibility, corrosion resistance |
Electronics | Conductive inks, solder pastes | High electrical conductivity |
Energy | Battery components, fuel cells | Enhanced performance, longevity |
Defense | Ammunition, armor-piercing projectiles | High density, excellent mechanical properties |
Jewelry | Intricate designs, custom pieces | High purity, customizable properties |
Comparing Gas Atomization to Other Atomization Techniques
When it comes to metal powder production, gas atomization is often compared to other methods like water atomization, centrifugal atomization, and plasma atomization. Here’s how gas atomization stacks up:
Parameter | Gas Atomization | Water Atomization | Centrifugal Atomization | Plasma Atomization |
---|---|---|---|---|
Particle Shape | Spherical | Irregular | Spherical | Spherical |
Purity | High | Moderate | High | Very High |
Oxidation Risk | Low (inert gases) | High | Low | Very Low |
Production Cost | Moderate | Low | High | Very High |
Control Over Particle Size | High | Moderate | Low | High |
Applications | Broad range, high-tech | Conventional, lower-cost | Specialty, high-tech | Specialty, ultra-high-tech |
Why Choose Gas Atomization?
Gas atomization offers a balance of purity, control, and cost-effectiveness, making it the preferred choice for producing metal powders used in critical applications. The spherical shape and uniform size distribution of gas atomized powders enhance the flowability and packing density, which are essential in processes like additive manufacturing and powder metallurgy.
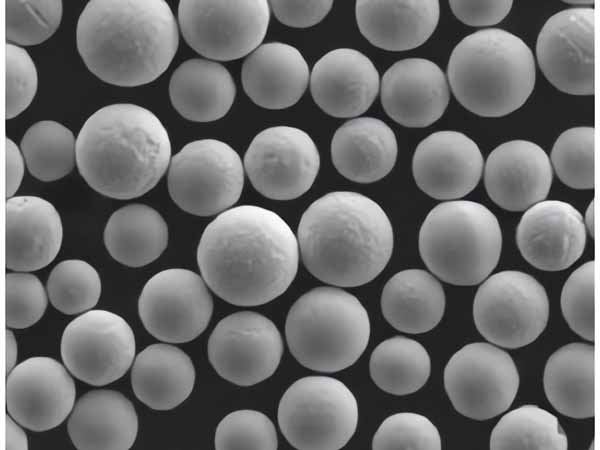
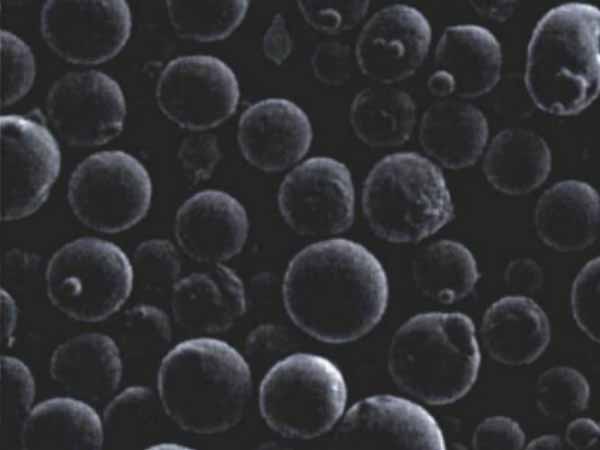
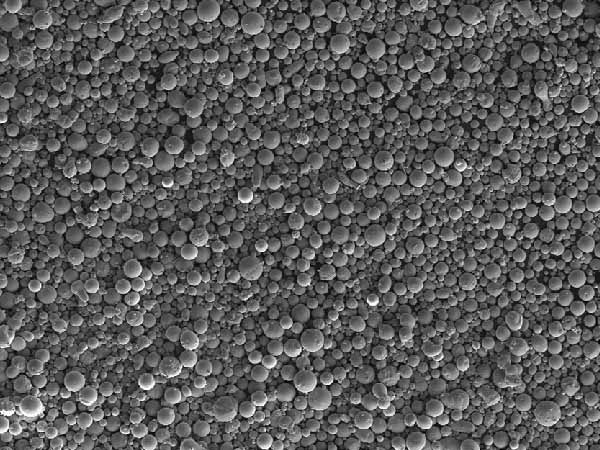
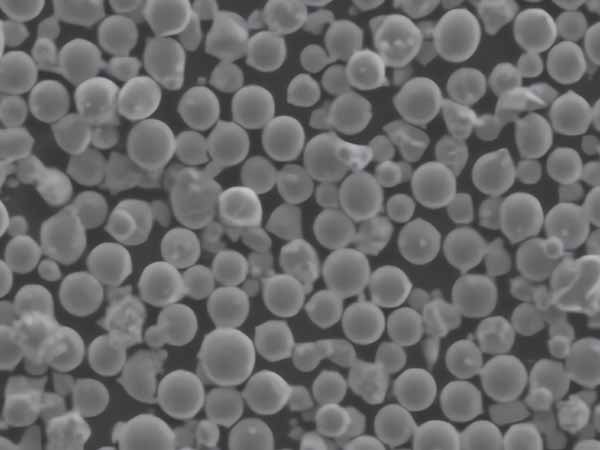
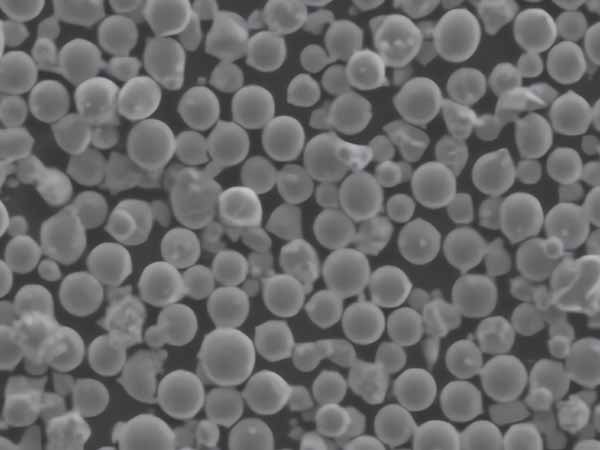
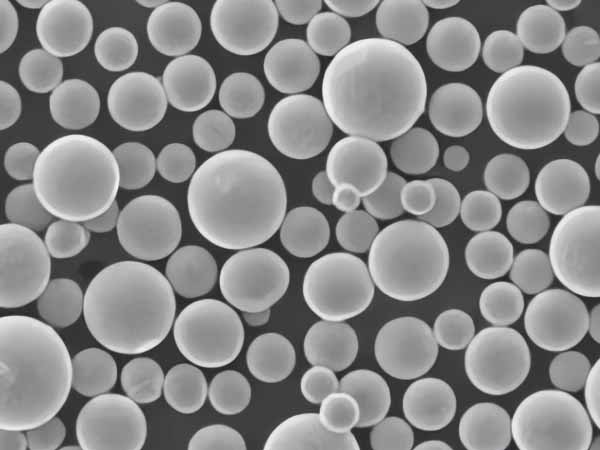
Suppliers and Pricing of Gas Atomized Powders
The market for gas atomized powders is diverse, with suppliers offering a range of materials tailored to specific applications. Below is a list of some key suppliers and an overview of pricing for various metal powders:
Supplier | Metal Powders Offered | Pricing (Approx.) | Specialty |
---|---|---|---|
Höganäs AB | Stainless Steel, Tool Steel, Copper Alloys | $25 – $100/kg | High volume, consistent quality |
Carpenter Technology | Nickel Superalloys, Titanium Alloys | $50 – $300/kg | Aerospace, medical applications |
GKN Powder Metallurgy | Iron-Based Alloys, Aluminum Alloys | $20 – $150/kg | Automotive, general engineering |
Sandvik | Titanium, Cobalt-Chrome, Stainless Steel | $40 – $250/kg | Additive manufacturing |
Tekna | Aluminum, Magnesium, Precious Metals | $30 – $400/kg | Electronics, specialty applications |
AP&C (Arcam) | Titanium, Nickel Superalloys | $60 – $350/kg | High precision, aerospace |
Oerlikon Metco | Copper Alloys, Tool Steels, Superalloys | $30 – $200/kg | Thermal spray, wear resistance |
AMETEK Specialty Metal Products | Stainless Steel, Nickel Alloys | $40 – $220/kg | High purity, specialty applications |
Praxair Surface Technologies | Inconel, Cobalt-Chrome, Titanium | $50 – $280/kg | Aerospace, medical |
Aubert & Duval | Superalloys, Tool Steels | $45 – $250/kg | High-performance applications |
Gas Atomized Powders: Pros, Cons, and Applications
Gas atomization, while highly advantageous, comes with its set of challenges. Below is a
detailed comparison of the pros and cons of using gas atomized powders:
Advantages | Disadvantages |
---|---|
High purity levels | Higher production cost compared to water atomization |
Spherical particles with excellent flowability | Requires specialized equipment |
Controlled particle size distribution | Limited to metals with high melting points |
Low oxidation risk | Not suitable for metals prone to gas absorption |
Versatility in material types | Higher energy consumption |
Scalability for industrial production | Potential need for post-processing |
When to Use Gas Atomized Powders?
Gas atomized powders are particularly beneficial in applications where material purity and particle morphology are critical. For instance, in additive manufacturing, the flowability of the powder can significantly impact the quality of the final product. Similarly, in aerospace and medical applications, the high purity and controlled composition of gas atomized powders ensure reliability and performance.
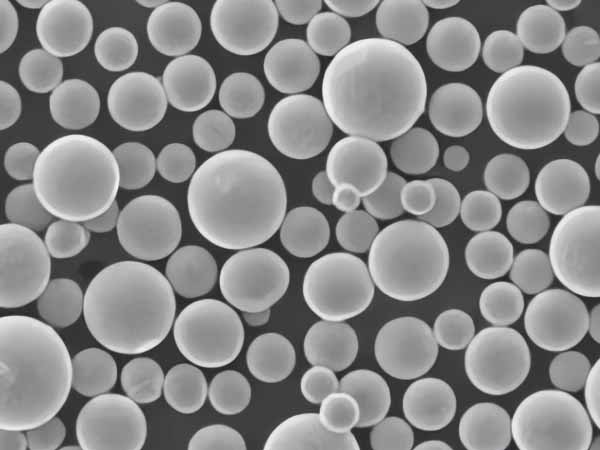
FAQs
Question | Answer |
---|---|
What is gas atomization used for? | Gas atomization is primarily used for producing metal powders that are employed in industries like aerospace, automotive, medical, and additive manufacturing. |
How does gas atomization differ from water atomization? | Gas atomization uses inert gases to break down molten metal into powder, resulting in higher purity and spherical particles, whereas water atomization often leads to irregular particles and higher oxidation levels. |
Can gas atomization be used for all metals? | While gas atomization is versatile, it is most effective for metals and alloys that do not easily absorb gases. Metals with very high melting points or those that react with gases may require different atomization techniques. |
What are the advantages of gas atomized powders in additive manufacturing? | The spherical shape and controlled size distribution of gas atomized powders enhance flowability and packing density, leading to higher quality in additive manufacturing processes. |
Is gas atomization environmentally friendly? | Gas atomization is relatively environmentally friendly, especially when compared to processes that generate more waste or require hazardous chemicals. The use of inert gases also minimizes oxidation and contamination. |
How is particle size controlled in gas atomization? | Particle size in gas atomization is controlled by adjusting the gas pressure, temperature, and the nozzle design. This allows for precise tuning to achieve the desired particle size distribution. |
What are the challenges in gas atomization? | Some challenges include the high cost of equipment, energy consumption, and the need for careful control of process parameters to avoid issues like gas absorption or improper particle formation. |
Who are the major suppliers of gas atomized powders? | Major suppliers include Höganäs AB, Carpenter Technology, GKN Powder Metallurgy, and Sandvik, among others, offering a wide range of metal powders tailored to various industrial needs. |
What are the future trends in gas atomization? | Future trends in gas atomization include the development of more energy-efficient processes, the ability to atomize a broader range of materials, and advancements in powder characterization techniques to further enhance the quality of the powders produced. |
How do gas atomized powders compare in cost to other powders? | Gas atomized powders tend to be more expensive than those produced by water atomization due to the higher production costs associated with the process. However, their superior properties often justify the cost in high-performance applications. |
Conclusion
Gas atomization stands as a cornerstone in the production of high-quality metal powders, which are essential in many cutting-edge industries. As technology continues to advance, the demand for these powders will only grow, driven by innovations in additive manufacturing, aerospace, and beyond. The balance of purity, control, and versatility offered by gas atomization ensures its place at the forefront of materials science for years to come.
The comprehensive control over particle morphology and size distribution, combined with the ability to produce powders from a wide range of metals and alloys, makes gas atomization a highly valued process. As industries continue to evolve, the role of gas atomized powders will undoubtedly expand, pushing the boundaries of what is possible in manufacturing and materials engineering.
Whether you’re looking to source the best metal powders for your next project or simply want to understand the process behind these advanced materials, gas atomization offers a fascinating glimpse into the future of manufacturing.