Gas atomized prealloyed spherical Ti-6Al-4V is not just a mouthful to say—it’s a material with impressive versatility and a staple in industries where strength, lightness, and biocompatibility are key. Whether you’re into aerospace, medical devices, or even 3D printing, Ti-6Al-4V is probably on your radar. But what makes it so special? Why is it the go-to choice for high-performance applications? In this article, we’ll dive deep into what makes gas atomized prealloyed spherical Ti-6Al-4V tick, and why it’s worth the hype.
Overview of Gas Atomized Prealloyed Spherical Ti-6Al-4V
Let’s start with the basics. Ti-6Al-4V, also known as Grade 5 Titanium, is an alloy consisting of 6% aluminum, 4% vanadium, and the rest primarily titanium. This combination results in a material with a unique blend of high strength, low density, and excellent corrosion resistance. The gas atomization process ensures that the particles of this alloy are spherical, which makes it perfect for applications like additive manufacturing (3D printing) and powder metallurgy.
Key Details:
- Composition: Titanium (90%), Aluminum (6%), Vanadium (4%)
- Common Applications: Aerospace, biomedical implants, automotive components, 3D printing
- Advantages: High strength-to-weight ratio, corrosion resistance, biocompatibility
Composition of Gas Atomized Prealloyed Spherical Ti-6Al-4V
Understanding the composition of Ti-6Al-4V is crucial to appreciating why it’s such a powerhouse material. The specific percentages of aluminum and vanadium aren’t just arbitrary—they each serve a purpose.
Element | Percentage (%) | Role in Alloy |
---|---|---|
Titanium | 90% | Base metal, provides strength, and corrosion resistance |
Aluminum | 6% | Increases strength by stabilizing the alpha phase, improves hardness |
Vanadium | 4% | Promotes ductility and toughness by stabilizing the beta phase |
Why This Composition Works:
- Aluminum: By stabilizing the alpha phase, aluminum increases the overall strength and hardness of the alloy, making it suitable for high-stress environments like aircraft structures.
- Vanadium: Vanadium’s role in stabilizing the beta phase ensures that the material remains ductile, meaning it can withstand deformation without cracking—an essential trait for materials used in critical applications.
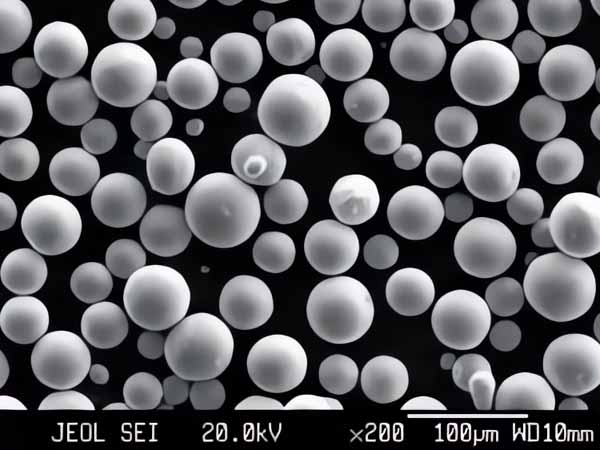
Characteristics of Gas Atomized Prealloyed Spherical Ti-6Al-4V
The unique blend of aluminum and vanadium gives Ti-6Al-4V a set of characteristics that make it stand out in the crowd of materials available for high-performance applications.
Physical Properties
Property | Value |
---|---|
Density | 4.43 g/cm³ |
Melting Point | 1,660°C |
Elastic Modulus | 114 GPa |
Thermal Conductivity | 6.7 W/m·K |
Coefficient of Thermal Expansion | 8.6 µm/m·°C |
Mechanical Properties
Property | Value |
---|---|
Ultimate Tensile Strength | 1,000 MPa |
Yield Strength | 880 MPa |
Elongation at Break | 14-16% |
Hardness (Rockwell C) | 36-40 HRC |
Why These Properties Matter:
- Strength: The tensile strength of Ti-6Al-4V is remarkable, particularly given its low density. This means you get a material that’s strong yet light—a crucial factor in aerospace applications where every gram counts.
- Corrosion Resistance: Titanium’s natural oxide layer protects it from corrosion in harsh environments, from salty seawater to human body fluids, making it ideal for medical implants.
- Biocompatibility: Ti-6Al-4V doesn’t just resist corrosion—it’s also highly biocompatible, meaning it’s not toxic to living tissue. That’s why it’s often used in medical implants like hip replacements and dental screws.
Advantages of Gas Atomized Prealloyed Spherical Ti-6Al-4V
When you’re picking a material for a project, you want to know what makes it the best choice. Ti-6Al-4V offers a range of benefits that make it a top contender.
High Strength-to-Weight Ratio
In industries like aerospace and automotive, where weight reduction is crucial for efficiency, Ti-6Al-4V’s high strength-to-weight ratio is a game-changer. Compared to other metals like steel or even aluminum alloys, Ti-6Al-4V delivers similar strength at a fraction of the weight.
Corrosion Resistance
Whether it’s exposure to seawater or the inside of the human body, Ti-6Al-4V can handle it. Its corrosion resistance is one of the reasons it’s widely used in marine and biomedical applications.
Versatility in Manufacturing
The gas atomized prealloyed spherical form of Ti-6Al-4V makes it particularly well-suited for additive manufacturing. The spherical particles flow easily, allowing for the precise layering needed in 3D printing. This property also benefits powder metallurgy processes, where consistent particle shape and size are essential.
Disadvantages and Limitations
Of course, no material is perfect. Ti-6Al-4V does have its drawbacks, and it’s important to consider these when choosing a material for your application.
Cost
Titanium alloys, including Ti-6Al-4V, are expensive. The cost of raw materials and the complexity of processing make this alloy pricier than other options like aluminum or steel.
Difficult to Machine
Ti-6Al-4V is tough, but that toughness comes at a price—it’s difficult to machine. The material’s hardness means it can wear down tools quickly, leading to higher production costs.
Applications of Gas Atomized Prealloyed Spherical Ti-6Al-4V
The versatility of Ti-6Al-4V means it finds applications in a wide range of industries. Here’s a look at where you’ll most commonly find this alloy in use.
Industry | Application | Why Ti-6Al-4V? |
---|---|---|
Aerospace | Aircraft components, landing gears | High strength, low weight, corrosion resistance |
Medical | Implants, surgical instruments | Biocompatibility, corrosion resistance |
Automotive | High-performance engine parts | Weight reduction, high strength |
Marine | Propellers, deep-sea submersibles | Corrosion resistance in seawater |
Additive Manufacturing | 3D printed components | Consistent particle shape, flowability |
Specifications, Sizes, Grades, and Standards
When it comes to buying gas atomized prealloyed spherical Ti-6Al-4V, you’ll need to know the specifics. This includes the different sizes, grades, and standards that the material adheres to.
Specification | Details |
---|---|
Sizes Available | Particle sizes typically range from 15 µm to 150 µm |
Grades | Grade 5 (Ti-6Al-4V) is the most common |
Standards | ASTM F136 (Medical), ASTM B348 (Industrial) |
Forms Available | Powder, bar, plate, sheet |
Specific Metal Powder Models: Top 10 Examples
When selecting Ti-6Al-4V powder for a specific application, there are various models you can choose from, each optimized for different uses. Here are ten of the most prominent models:
- Argon Plasma Atomized Ti-6Al-4V
- Particle Size: 15-45 µm
- Applications: Ideal for additive manufacturing (3D printing) due to its fine particle size.
- Hydrogenated Titanium Alloy Powder (Ti-6Al-4V-H2)
- Particle Size: 50-150 µm
- Applications: Used in powder metallurgy and cold isostatic pressing.
- Gas Atomized Ti-6Al-4V (Grade 5)
- Particle Size: 20-63 µm
- Applications: Widely used in aerospace for the production of lightweight, strong components.
- Spherical Ti-6Al-4V for L-PBF (Laser Powder Bed Fusion)
- Particle Size: 15-45 µm
- Applications: Specialized for laser-based 3D printing technologies.
- Ti-6Al-4V Grade 23 Powder
- Particle Size: 45-106 µm
- Applications: Preferred in medical applications due to its higher purity and better biocompatibility.
- Ti-6Al-4V ELI (Extra Low Interstitial) Powder
- Particle Size: 20-90 µm
- Applications: Used in critical medical implants, providing superior toughness and fatigue resistance.
- Plasma Rotating Electrode Process (PREP) Ti-6Al-4V
- Particle Size: 75-150 µm
- Applications: Employed in powder bed fusion and direct energy deposition methods.
- High Purity Ti-6Al-4V Spherical Powder
- Particle Size: 15-63 µm
- Applications: Essential for producing high-quality aerospace components with minimal impurities.
- Water Atomized Ti-6Al-4V
- Particle Size: 45-105 µm
- Applications: Suitable for less demanding applications, such as manufacturing non-critical components.
- Micronized Ti-6Al-4V Powder
- Particle Size: 10-25 µm
- Applications: Utilized in the production of fine, intricate components requiring detailed precision.
Suppliers and Pricing Details
When it comes to acquiring gas atomized prealloyed spherical Ti-6Al-4V, knowing your suppliers and the expected pricing is crucial.
Supplier | Pricing Range | Notes |
---|---|---|
Praxair Surface Technologies | $500 – $700 per kg | High-quality powders for aerospace |
Carpenter Technology | $450 – $650 per kg | Offers various grades, including ELI |
ATI Metals | $600 – $800 per kg | Specializes in medical-grade powders |
AP&C (A GE Additive Company) | $550 – $750 per kg | Focuses on powders for 3D printing |
Sandvik Osprey | $500 – $700 per kg | Wide range of particle sizes |
Advantages and Limitations Compared
When you’re weighing up materials, it’s essential to consider both the pros and cons. Here’s how Ti-6Al-4V stacks up compared to other materials.
Property | Ti-6Al-4V | Aluminum Alloys | Stainless Steel |
---|---|---|---|
Strength-to-Weight Ratio | High | Moderate | Low |
Corrosion Resistance | Excellent | Moderate | Excellent |
Machinability | Difficult | Easy | Moderate |
Cost | High | Low | Moderate |
Biocompatibility | Excellent | Low | Moderate |
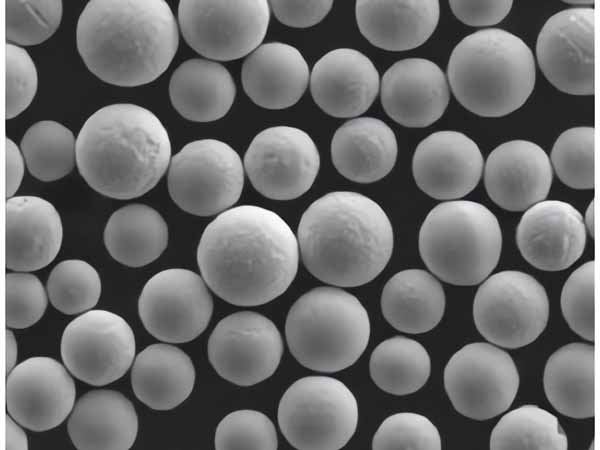
FAQs
Question | Answer |
---|---|
What is gas atomization? | Gas atomization is a process where molten metal is dispersed into fine droplets using a high-velocity gas stream. |
Why is spherical powder important? | Spherical powder ensures better flowability and packing density, crucial for additive manufacturing and powder metallurgy. |
Is Ti-6Al-4V suitable for medical implants? | Yes, especially the ELI (Extra Low Interstitial) grade, which offers superior biocompatibility. |
What are the main industries using Ti-6Al-4V? | Aerospace, medical, automotive, marine, and additive manufacturing industries heavily rely on this alloy. |
How does Ti-6Al-4V compare to stainless steel? | Ti-6Al-4V offers a higher strength-to-weight ratio and better biocompatibility, but it’s more expensive and harder to machine. |
Conclusion
Gas atomized prealloyed spherical Ti-6Al-4V is a powerhouse alloy with applications that span from the skies in aerospace to inside the human body in medical implants. Its unique composition and the properties it provides—strength, corrosion resistance, and biocompatibility—make it a material of choice for industries that demand nothing short of the best. While it comes with some challenges, like higher costs and machining difficulties, the benefits often outweigh these drawbacks, particularly in high-performance environments. Whether you’re in aerospace, medical fields, or additive manufacturing, understanding the ins and outs of Ti-6Al-4V will help you make informed decisions for your next big project.