When it comes to high-performance metal powders, CoNiCr (Cobalt-Nickel-Chromium) stands out as a powerhouse material used in a wide range of industries, from aerospace to medical devices. But what exactly makes this alloy powder so special, and why should you care? If you’re looking to dive deep into the world of CoNiCr powder, you’re in the right place. In this comprehensive guide, we’ll explore the intricacies of this metal powder, from its composition to its applications, specifications, and much more. Let’s take the mystery out of this fascinating material and show you how it fits into the modern manufacturing world.
Overview of CoNiCr Powder
The CoNiCr powder, a combination of Cobalt (Co), Nickel (Ni), and Chromium (Cr), is a type of alloy powder used in high-temperature, high-strength applications. Known for its excellent corrosion resistance, high thermal stability, and superior wear resistance, it is commonly used in industries such as aerospace, automotive, medical devices, and gas turbines.
At its core, CoNiCr powder is a material designed for situations where high performance is non-negotiable. If you’re creating something that needs to endure extreme heat, resist corrosion, and still maintain structural integrity, CoNiCr powder might just be your best friend. But what does it offer that other metal powders don’t?
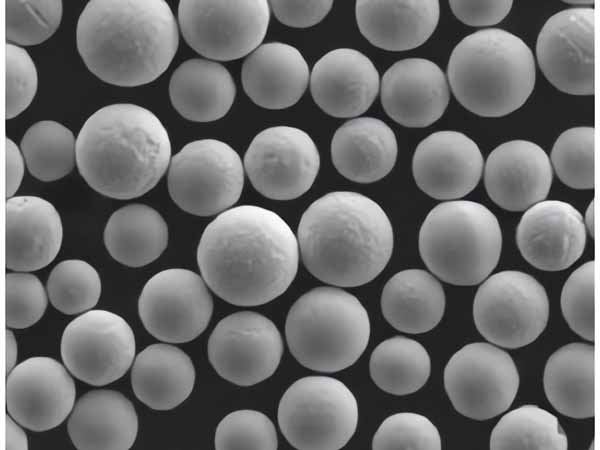
Composition of CoNiCr Powder
So, what exactly is CoNiCr powder made of? Let’s break it down. This alloy powder typically consists of varying percentages of cobalt, nickel, and chromium, with each metal contributing specific properties to the overall material.
Metal | Typical Percentage | Role |
---|---|---|
Cobalt (Co) | 35-60% | Provides corrosion resistance, thermal stability, and high strength. |
Nickel (Ni) | 20-40% | Enhances toughness and elasticity, especially at high temperatures. |
Chromium (Cr) | 10-30% | Adds significant corrosion resistance and improves wear properties. |
This combination creates a balanced alloy that excels in demanding environments, offering both structural stability and resistance to degradation under extreme conditions.
Characteristics of CoNiCr Powder
What are the standout characteristics that make CoNiCr powder so useful in critical applications? To get a better idea, let’s look at its key properties:
Property | Description |
---|---|
High Corrosion Resistance | Thanks to the high chromium content, CoNiCr alloys are extremely resistant to corrosion, making them ideal for use in harsh chemical environments. |
Thermal Stability | CoNiCr powder remains structurally stable even at extremely high temperatures, often reaching up to 1000°C or more without significant degradation. |
Wear Resistance | These alloys are resistant to wear and abrasion, making them perfect for applications involving moving parts or surfaces subject to constant friction. |
High Strength | With cobalt as the main component, CoNiCr powder retains a high strength-to-weight ratio, even in high-temperature environments. |
Magnetic Properties | The cobalt content provides magnetic properties, which can be advantageous in certain technical applications like electric motors or sensors. |
With these characteristics, CoNiCr powder is an excellent material for high-performance applications. But it’s not just about performance—this material offers a unique combination of durability and versatility that makes it stand out against the competition.
Common Types and Models of CoNiCr Powder
There are various types and models of CoNiCr powder, each designed for specific applications. Here’s a breakdown of some common models you might encounter:
Model | Composition (Typical) | Main Applications | Key Features |
---|---|---|---|
CoNiCr Model 1 | Co 50%, Ni 30%, Cr 20% | Aerospace components, turbine blades | High thermal stability and oxidation resistance |
CoNiCr Model 2 | Co 60%, Ni 25%, Cr 15% | Medical implants, orthopedic devices | Superior biocompatibility and wear resistance |
CoNiCr Model 3 | Co 40%, Ni 40%, Cr 20% | Gas turbine components, combustion chambers | Excellent mechanical properties at high temperatures |
CoNiCr Model 4 | Co 55%, Ni 35%, Cr 10% | Automotive exhaust systems | High corrosion resistance in acidic environments |
CoNiCr Model 5 | Co 45%, Ni 35%, Cr 20% | High-speed tools, cutting equipment | High wear resistance and toughness |
CoNiCr Model 6 | Co 50%, Ni 20%, Cr 30% | Chemical processing, marine applications | Exceptional corrosion and erosion resistance |
CoNiCr Model 7 | Co 35%, Ni 40%, Cr 25% | Heat exchangers, steam turbines | Enhanced thermal stability and oxidation resistance |
CoNiCr Model 8 | Co 48%, Ni 32%, Cr 20% | Jet engine components, nozzles | High fatigue strength and wear resistance |
CoNiCr Model 9 | Co 50%, Ni 40%, Cr 10% | Biomedical tools, dental implants | Excellent biocompatibility and precision manufacturing |
CoNiCr Model 10 | Co 52%, Ni 30%, Cr 18% | Power generation, turbine vanes | High-temperature performance and corrosion resistance |
Each of these models offers specific advantages for different industries and applications. Whether you’re looking for corrosion resistance, wear resistance, or thermal stability, there’s likely a CoNiCr powder variant that fits the bill.
-
CM247LC Powder | Nickel Alloy Powder
-
0# Pure Nickel powder
-
NiCoCrAlY alloys powders
-
Rene 142 alloy-Rene Powder
-
Haynes 25 Haynes Powder
-
Best Hastelloy C-22 Powder-High temperature alloy Powder for 3D Printing
-
Best Hastelloy C-276 Powder-High temperature alloy Powder for 3D Printing
-
Best Hastelloy N Powder-High temperature alloy Powder for 3D Printing
-
Best Hastelloy B Powder丨High temperature alloy Powder for 3D Printing
Applications of CoNiCr Powder
What can you actually do with CoNiCr powder? The range of potential uses is surprisingly broad. From manufacturing aerospace parts to creating medical devices, CoNiCr powder plays a crucial role in modern engineering.
Industry | Application | Advantages of CoNiCr in This Application |
---|---|---|
Aerospace | Turbine blades, engine components | Withstands high temperatures and corrosive environments. |
Medical | Orthopedic implants, dental implants | Biocompatible, wear-resistant, and long-lasting for medical devices. |
Automotive | Exhaust systems, turbochargers | Excellent resistance to heat and corrosion from engine environments. |
Chemical Processing | Pumps, valves, and piping | Resistant to corrosive chemicals, ensuring longevity in harsh conditions. |
Power Generation | Steam turbines, heat exchangers | Withstands high thermal stress and corrosion, crucial for efficient energy production. |
Marine | Propellers, pumps, underwater components | Excellent resistance to saltwater corrosion and erosion. |
In each of these industries, CoNiCr powder is chosen not only for its performance but also because it extends the life of critical components, reducing the need for frequent replacements and repairs.
Specifications and Grades of CoNiCr Powder
When choosing CoNiCr powder, understanding its specifications is crucial. Here’s a table summarizing the common grades, sizes, and standards you might encounter:
Grade | Particle Size (µm) | Standard | Applications |
---|---|---|---|
CoNiCr Grade A | 15-45 | ASTM F75 | Orthopedic implants, medical devices |
CoNiCr Grade B | 20-50 | AMS 5894 | Aerospace components, turbine blades |
CoNiCr Grade C | 10-40 | ISO 5832-4 | Dental implants, medical instruments |
CoNiCr Grade D | 25-60 | AMS 5844 | High-speed cutting tools, wear parts |
CoNiCr Grade E | 30-70 | ISO 9001 | Marine applications, corrosion-resistant components |
The particle size of CoNiCr powder affects how it behaves during manufacturing processes such as 3D printing or metal injection molding (MIM). Smaller particles offer greater surface area, improving bonding and melting characteristics in these processes.
Comparing CoNiCr Powder with Other Alloys
When you’re choosing between metal powders for a project, CoNiCr powder often goes up against alternatives like Inconel, Stellite, or even Titanium alloys. So how does it stack up?
Property | CoNiCr | Inconel | Stellite | Titanium Alloy |
---|---|---|---|---|
Corrosion Resistance | Excellent (especially in high heat) | Very good | Excellent | Moderate (not ideal in high heat) |
Thermal Stability | High (up to 1000°C or more) | Very high | High | Moderate |
Wear Resistance | Excellent | Good | Excellent | Moderate |
Biocompatibility | High (used in medical devices) | Moderate | High | High |
Cost | Moderate to high | High | High | High |
As you can see, CoNiCr powder offers a balanced mix of corrosion resistance, thermal stability, and wear resistance, often outperforming other metal powders in extreme environments. In medical applications, its biocompatibility is another major advantage over alloys like Inconel.
Advantages and Disadvantages of CoNiCr Powder
Before you rush to purchase CoNiCr powder, it’s important to weigh the pros and cons. Here’s a quick breakdown:
Advantages | Disadvantages |
---|---|
High thermal stability at elevated temperatures | Generally more expensive than standard alloys |
Excellent corrosion and wear resistance | Harder to machine due to its hardness |
Biocompatibility, making it ideal for medical use | Limited availability in some regions |
Magnetic properties, useful for certain applications | Requires specialized equipment for processing |
While CoNiCr powder offers many benefits, it’s not without its challenges. It’s typically more expensive and harder to machine than some alternative alloys, which can make it a less attractive option for projects on a tight budget.
Suppliers and Pricing of CoNiCr Powder
When sourcing CoNiCr powder, it’s crucial to find reputable suppliers. Prices can vary based on factors such as grade, quantity, and location.
Supplier | Price per kg (USD) | Notes |
---|---|---|
Sandvik Osprey | $150 – $200 | High-quality aerospace and medical grades |
Carpenter Additive | $180 – $250 | Specializes in additive manufacturing powders |
Höganäs AB | $140 – $210 | Known for advanced powder metallurgy |
Praxair Surface Technologies | $160 – $230 | Offers custom alloys and powder solutions |
Ametek Specialty Metal | $130 – $190 | Competitive pricing with bulk discounts |
CoNiCr powder prices generally range from $130 to $250 per kilogram, with fluctuations depending on the supplier and market demand. Prices for specialized grades, such as those used in medical or aerospace applications, tend to be on the higher end of the spectrum.
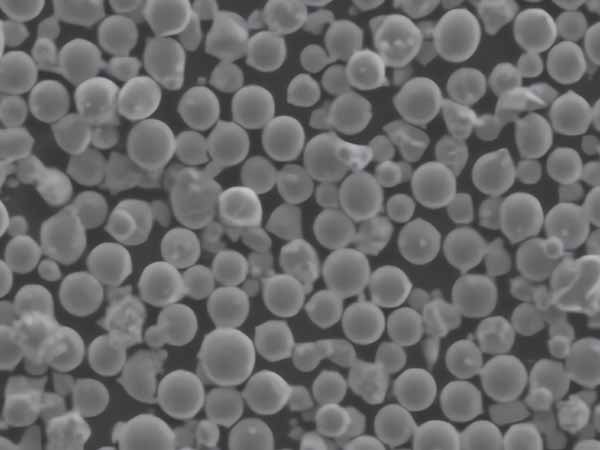
FAQ
Question | Answer |
---|---|
What is CoNiCr powder used for? | CoNiCr powder is primarily used in aerospace, medical devices, automotive components, and high-temperature industrial parts. |
How is CoNiCr powder made? | It’s produced through atomization processes, where molten metal is turned into fine particles. |
Can CoNiCr powder be used in 3D printing? | Yes, it’s widely used in additive manufacturing for producing high-performance parts. |
Is CoNiCr powder biocompatible? | Absolutely, which is why it’s often used in medical implants and tools. |
How much does CoNiCr powder cost? | Prices typically range from $130 to $250 per kg, depending on grade and supplier. |
Conclusion
In summary, CoNiCr powder is a versatile and high-performing alloy that shines in demanding environments. Whether you’re developing next-generation jet engines or crafting precise medical implants, this alloy delivers where others fall short. Its unique blend of cobalt, nickel, and chromium offers a material that resists wear, corrosion, and extreme temperatures, making it an excellent choice for industries that need top-tier performance.
If you’re ready to take your projects to the next level, consider integrating CoNiCr powder into your manufacturing processes. Its upfront cost may be higher, but in the long run, it’s an investment in durability, performance, and efficiency.