If you’re diving into the world of metal powders, chances are you’ve come across MnS powder. Short for Manganese Sulfide powder, it has a vast range of applications across multiple industries. This article covers everything you need to know about MnS powder, including its characteristics, models, applications, advantages, and more.
Overview of MnS Powder
Manganese Sulfide (MnS) powder is a compound used primarily in metallurgy, specifically in steel production. It is commonly included to improve machinability, as it forms tiny inclusions that act as chip breakers during the machining process. However, its uses extend beyond steelmaking and into various other industries such as electronics and chemical manufacturing.
In this guide, we’ll explore not just the fundamentals but also provide detailed insights into the different models of MnS powder, its composition, characteristics, and how it compares to other similar materials.
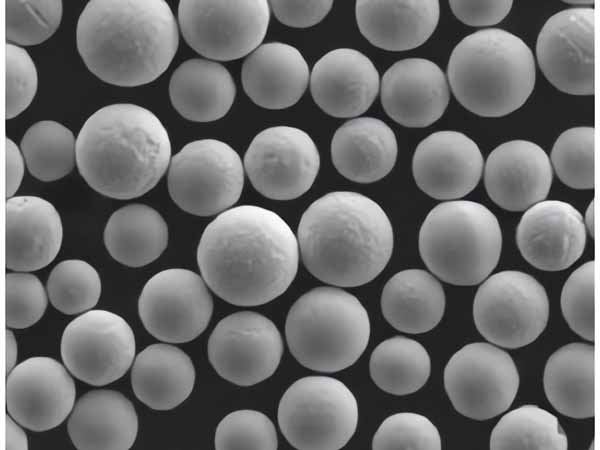
Composition and Characteristics of MnS Powder
MnS powder primarily consists of Manganese (Mn) and Sulfur (S), with trace elements depending on its specific grade. Its key characteristics include its ability to form inclusions that make machining easier, as well as high resistance to wear, corrosion, and temperature.
Composition | Typical Range |
---|---|
Manganese (Mn) | 62% – 65% |
Sulfur (S) | 30% – 33% |
Trace Elements (O, H, N) | Up to 1% |
The high levels of manganese in the powder improve both strength and durability, while sulfur contributes to the machinability factor.
Models of MnS Powder
There are various types of MnS powder available in the market. Here are 10 specific models commonly used in industries, each with its unique features and applications.
- MnS-65
- Composition: 65% Manganese, 33% Sulfur
- Use: Primarily used in high-performance steel alloys.
- Characteristics: Enhanced machinability, reduced tool wear.
- MnS-62
- Composition: 62% Manganese, 30% Sulfur
- Use: Ideal for stainless steel production.
- Characteristics: High corrosion resistance, suitable for acidic environments.
- MnS-60H
- Composition: 60% Manganese, 31% Sulfur, 1% Trace Elements
- Use: Heat-resistant steels.
- Characteristics: Suitable for applications involving high temperatures.
- MnS-58
- Composition: 58% Manganese, 30% Sulfur
- Use: Common in carbon steel production.
- Characteristics: Good for general-purpose machining.
- MnS-High Purity
- Composition: 99.9% pure MnS
- Use: High-end electronics and semiconductors.
- Characteristics: Ultra-low impurity levels, used for sensitive electrical components.
- MnS-72
- Composition: 72% Manganese, 27% Sulfur
- Use: Aerospace industry.
- Characteristics: Lightweight, high strength.
- MnS-65T
- Composition: 65% Manganese, 33% Sulfur, 2% Titanium
- Use: Specialty steels for tools.
- Characteristics: Titanium addition improves toughness.
- MnS-70
- Composition: 70% Manganese, 28% Sulfur
- Use: High-strength low-alloy steels.
- Characteristics: Good mechanical strength and toughness.
- MnS-Low Sulfur
- Composition: 60% Manganese, 20% Sulfur
- Use: Applications requiring minimal sulfur content.
- Characteristics: Reduced brittleness, better ductility.
- MnS-Nano
- Composition: Nanostructured MnS particles
- Use: Cutting-edge electronics and nano-applications.
- Characteristics: Ultra-fine particles for precision use.
Applications of MnS Powder
MnS powder is highly versatile and used across multiple industries. From improving machinability in steel to functioning as an important component in electronics, its utility knows no bounds.
Industry | Applications |
---|---|
Metallurgy | Used to improve machinability in steel and other alloys. |
Electronics | Used in the manufacture of semiconductors and sensors. |
Aerospace | Used in high-strength alloys for aircraft components. |
Chemical Manufacturing | Acts as a catalyst in various chemical reactions. |
Automotive | Included in the production of gears, axles, and engine parts for enhanced machinability. |
In metallurgy, MnS powder plays a vital role in producing steels that are easier to cut and form, reducing tool wear and increasing production efficiency. In electronics, its ultra-fine grades are used in manufacturing high-precision components such as sensors and semiconductors.
Advantages of MnS Powder
Let’s dive into the primary benefits of MnS powder, especially when compared to other materials.
- Improved Machinability
MnS forms inclusions in the metal that break the chips during machining, leading to faster production times and less tool wear. Compared to materials without MnS, the difference in machinability is striking. - Enhanced Corrosion Resistance
Sulfur in MnS helps improve the corrosion resistance of the final product, making it ideal for harsh environments. This sets MnS apart from other alloying materials that may not provide the same level of protection against corrosion. - Temperature Resistance
Certain models of MnS powder are specifically designed to withstand high temperatures, making them suitable for heat-resistant steels. This gives it an edge over many other alloying powders. - Cost Efficiency
Due to its properties, MnS reduces the cost of production by speeding up machining and reducing tool wear, which means fewer replacements and less downtime.
Pros | Cons |
---|---|
Enhanced machinability | Increased sulfur content may reduce ductility |
Corrosion resistance | Inclusions may lead to reduced tensile strength in some cases |
Temperature resistance | Not suitable for ultra-high strength applications |
Cost-effective | Requires careful handling in high purity forms |
Specifications, Sizes, Grades, and Standards
When choosing MnS powder, it’s crucial to pay attention to the specifications, sizes, and standards that apply to your specific industry. Below are some of the common grades and standards for MnS powder.
Grade | Manganese Content | Sulfur Content | Particle Size | Standard |
---|---|---|---|---|
MnS-65 | 65% | 33% | 10-20 microns | ASTM A581 |
MnS-62 | 62% | 30% | 5-15 microns | ISO 9001 |
MnS-72 | 72% | 27% | 2-10 microns | JIS G3321 |
MnS-High Purity | 99.9% | 0.01% | 1-5 microns | EN 10204 |
Particle size and composition will vary depending on the application, but most MnS powders follow industry-specific standards like ASTM and ISO.
Suppliers and Pricing of MnS Powder
Finding the right supplier for MnS powder is important, as it ensures consistent quality and availability. Prices for MnS powder vary based on purity, particle size, and grade. Here’s a breakdown of popular suppliers and their pricing.
Supplier | Model | Price per kg | Shipping |
---|---|---|---|
Powder Tech Solutions | MnS-65 | $20/kg | Free over 50kg orders |
MetalCorp | MnS-High Purity | $50/kg | $100 flat fee |
Industrial Powders Co. | MnS-72 | $25/kg | $150 worldwide |
Global Powders Inc. | MnS-Low Sulfur | $18/kg | Free over 100kg orders |
It’s essential to factor in shipping fees, especially if sourcing from international suppliers, as these can significantly increase overall costs.
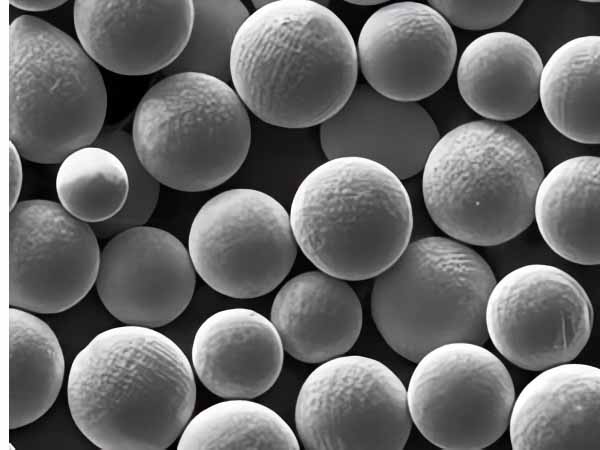
FAQ
Question | Answer |
---|---|
What is the primary use of MnS powder? | MnS powder is primarily used to improve machinability in steel and other metal alloys. |
How does MnS powder improve machinability? | MnS forms inclusions that break chips during machining, reducing tool wear and speeding up production. |
Can MnS powder be used in electronics? | Yes, high-purity forms of MnS powder are used in electronics for components like semiconductors and sensors. |
What are the drawbacks of using MnS powder in steel production? | While MnS improves machinability, it can reduce ductility and tensile strength in certain applications. |
How much does MnS powder cost? | Prices vary depending on grade and purity, typically ranging from $18 to $50 per kilogram. |
Conclusion
MnS powder is an essential material in a wide variety of industries, from metallurgy to electronics. Its ability to improve machinability, corrosion resistance, and temperature resistance makes it highly valuable, especially when producing high-performance steels. Understanding the different grades, characteristics, and applications of MnS powder can help you make informed decisions about its use in your industry.