Overview of WC-12Co Powder
When it comes to the world of metal powders and high-performance coatings, WC-12Co powder stands out as a key player. It combines tungsten carbide (WC) with cobalt (Co) in a 12% cobalt composition to deliver enhanced durability, hardness, and wear resistance, making it essential for industries where abrasion, erosion, and high-temperature resistance are critical. But what exactly makes WC-12Co powder so special? What are its various grades, and where is it used?
In this guide, we’ll cover everything from the basic composition and characteristics of WC-12Co powder to the specific models available on the market, how it compares to similar products, and its various applications. So, buckle up, because we’re about to dive deep into the world of tungsten carbide-cobalt powders!
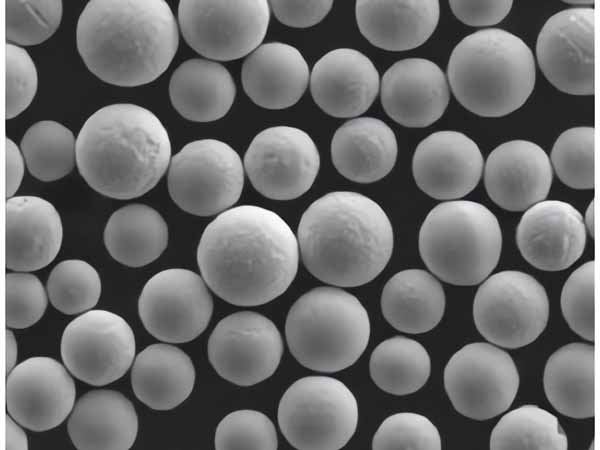
Composition of WC-12Co Powder
The “WC” stands for tungsten carbide, a compound known for its hardness and abrasion resistance, while “12Co” indicates that 12% of the powder’s composition is cobalt. Cobalt acts as a binder, enhancing the toughness of the compound. This perfect balance gives WC-12Co powder its edge, ensuring it can withstand mechanical stress and environmental factors like heat and corrosion.
Here’s a breakdown of its key components:
Component | Composition (%) | Role in the Powder |
---|---|---|
Tungsten Carbide (WC) | 88% | Provides hardness, wear resistance, and erosion resistance. |
Cobalt (Co) | 12% | Acts as a binder, improves toughness and durability. |
The fine balance between these two elements allows WC-12Co powder to excel in environments that demand exceptional resistance to wear and deformation.
Characteristics of WC-12Co Powder
Let’s be honest. If you’re considering using WC-12Co powder, you’re probably interested in how it performs under stress. The good news? It excels in almost every department you’d expect.
Hardness and Wear Resistance
The inclusion of tungsten carbide means that WC-12Co powder is incredibly hard—far harder than many other metals. This makes it ideal for applications where friction and erosion are a constant problem. Whether it’s cutting tools or surfaces exposed to heavy abrasion, WC-12Co powder handles the wear like a champ.
High-Temperature Performance
Compared to many other materials, WC-12Co powder retains its structural integrity even when things start to heat up. Thanks to the presence of cobalt, it holds its own at high temperatures, ensuring reliable performance where many other materials would fail.
Corrosion Resistance
If you think it’s all about wear resistance, think again. Cobalt in WC-12Co powder not only boosts its toughness but also lends it impressive corrosion resistance. This makes it suitable for harsh environments where exposure to moisture or chemicals is a concern.
Key Properties Table
Here’s a quick rundown of the technical properties of WC-12Co powder:
Property | Value | Explanation |
---|---|---|
Hardness | 1350-1800 HV | Extremely high hardness, ideal for abrasion resistance. |
Melting Point | 2870°C | Performs well in high-temperature applications. |
Density | 14.2-14.6 g/cm³ | Provides significant mass in coatings. |
Thermal Conductivity | 84-100 W/m·K | Efficient heat dissipation, preventing overheating. |
Compressive Strength | 4000-6000 MPa | Exceptional strength under mechanical stress. |
Corrosion Resistance | High | Suitable for harsh chemical environments. |
Types of WC-12Co Powder Models
Now that we’ve covered the composition and characteristics, let’s get into specific models. There are various WC-12Co powder variants, each tailored for different applications. Below are ten different models with their unique properties and optimal use cases:
Model | Description | Applications |
---|---|---|
WC-12Co-200 | Features fine particle size, excellent for thermal spraying applications that require smooth finishes. | Best for precision coatings, cutting tools, and wear-resistant machinery components. |
WC-12Co-300 | Medium particle size, provides balance between wear resistance and toughness. | Used in aerospace, automotive components, and manufacturing tools. |
WC-12Co-400 | Coarser particle size for applications that need high-density coatings. | Ideal for mining and oil & gas industry parts exposed to extreme conditions. |
WC-12Co-Spray | Specially designed for plasma spraying with optimized flowability and density. | Suitable for thermal spray coatings in gas turbines and aerospace components. |
WC-12Co-Submicron | Features submicron particles, offering enhanced hardness and finer coating layers. | Perfect for micro-tooling, electronics, and precision cutting tools. |
WC-12Co-HVAF | Developed for high-velocity air fuel (HVAF) spray processes, providing dense and smooth coatings. | Ideal for high-performance applications like industrial rolls and jet engines. |
WC-12Co-Plasma | Optimized for plasma transfer arc (PTA) welding, providing excellent adhesion to base metals. | Widely used in hard-facing components, repair, and refurbishment of metal parts. |
WC-12Co-HVOF | Tailored for high-velocity oxygen fuel (HVOF) spraying, ensuring strong, wear-resistant layers. | Common in turbine blades, automotive parts, and construction equipment. |
WC-12Co-Nano | Incorporates nanotechnology for enhanced toughness and fatigue resistance. | Best for advanced machinery, electronic components, and wear-resistant coatings in cutting-edge industries. |
WC-12Co-Coarse | Larger carbide grains, providing excellent shock absorption and toughness. | Suitable for heavy-duty industrial applications like mining, drilling, and oil exploration equipment. |
-
CM247LC Powder | Nickel Alloy Powder
-
0# Pure Nickel powder
-
NiCoCrAlY alloys powders
-
Rene 142 alloy-Rene Powder
-
Haynes 25 Haynes Powder
-
Best Hastelloy C-22 Powder-High temperature alloy Powder for 3D Printing
-
Best Hastelloy C-276 Powder-High temperature alloy Powder for 3D Printing
-
Best Hastelloy N Powder-High temperature alloy Powder for 3D Printing
-
Best Hastelloy B Powder丨High temperature alloy Powder for 3D Printing
Applications of WC-12Co Powder
WC-12Co powder’s versatility makes it the go-to material for a wide range of industries. Let’s look at where it really shines.
Application | Industry | Explanation |
---|---|---|
Thermal Spray Coatings | Aerospace, Power Generation | Protects turbine blades and components from wear, corrosion, and high temperatures. |
Cutting Tools | Manufacturing, Machining | Used to produce wear-resistant cutting and drilling tools. |
Mining Equipment | Mining, Drilling | Provides durable coatings for tools and machinery exposed to harsh environments. |
Automotive Components | Automotive Manufacturing | Enhances the longevity of engine components and other wear-prone parts. |
Wear Parts | Oil & Gas, Construction | Used in equipment exposed to abrasive materials like cement and sand. |
Precision Tools | Electronics, Medical Devices | Offers high-precision cutting tools for the production of electronics and medical devices. |
Advantages of WC-12Co Powder
So, why choose WC-12Co powder over other materials? Here are some key advantages:
- Superior Wear Resistance: With its high tungsten carbide content, WC-12Co powder is almost unmatched in terms of wear resistance. This makes it ideal for applications like cutting tools and coatings where longevity is crucial.
- High-Temperature Performance: When compared to other powders like WC-6Co or pure tungsten, WC-12Co can maintain performance at higher temperatures, thanks to its cobalt content.
- Corrosion Resistance: The inclusion of cobalt doesn’t just provide toughness, but it also significantly improves resistance to corrosion, making WC-12Co powder a top choice for environments where moisture or chemicals are a factor.
- Versatility: From aerospace to automotive, WC-12Co powder fits into numerous industries. Its adaptability across applications speaks to its strength, reliability, and versatility.
Advantages vs. Other Powders
Here’s a table comparing WC-12Co powder with other tungsten carbide powders:
Powder Type | Advantages | Disadvantages |
---|---|---|
WC-12Co | Best for wear resistance, high-temperature stability, corrosion protection. | More expensive due to cobalt content. |
WC-6Co | Lower cost, good hardness. | Less corrosion-resistant, reduced toughness. |
WC-10Ni | Great for chemical resistance and toughness. | Lower wear resistance than WC-12Co. |
WC-CrC-Ni | Excellent for high-corrosion environments. | Less hardness than WC-12Co. |
WC-Cu | Good conductivity, used in electrical contacts. | Lower wear resistance, softer than WC-12Co. |
Specifications, Sizes, and Grades
When it comes to choosing the right WC-12Co powder, it’s important to understand the various grades, sizes, and standards available. Different applications may require
different particle sizes or formulations, and knowing what to look for can save you a lot of headaches down the line.
Common Specifications
Specification | Range/Options |
---|---|
Particle Size | 5 µm – 45 µm |
Purity | ≥ 99% |
Coating Thickness | 50-500 µm |
Available Grades | Fine, Medium, Coarse |
Melting Point | 2700°C – 2900°C |
Suppliers and Pricing
Finding the right supplier for WC-12Co powder can be tricky, especially when prices can fluctuate based on market conditions, grade, and particle size. Here’s a list of reliable suppliers along with a general price range to help guide your purchasing decision.
Supplier | Location | Price (Per Kg) | Notes |
---|---|---|---|
Kennametal | USA | $120 – $150 | Offers a wide range of grades and particle sizes. |
H.C. Starck | Germany | $130 – $160 | Specializes in high-performance tungsten carbide powders. |
Sandvik | Sweden | $140 – $170 | Known for premium quality and customer service. |
Global Tungsten & Powders | USA | $125 – $155 | Offers extensive customization options. |
Treibacher Industrie AG | Austria | $135 – $165 | High-grade powder with great consistency. |
Pros and Cons of WC-12Co Powder
Before you decide on WC-12Co powder for your next project, it’s worth considering the pros and cons.
Pros
- High Wear Resistance: WC-12Co powder offers excellent durability, making it perfect for high-stress environments.
- Corrosion Resistance: The cobalt component provides significant protection against chemical wear.
- Versatility: Used across a wide range of industries, from aerospace to mining.
Cons
- Cost: WC-12Co can be more expensive than other powders due to the cobalt content.
- Brittleness: While tough, it can be slightly brittle under high-impact situations compared to some alternative powders.
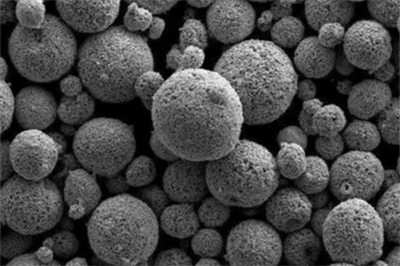
FAQ
Question | Answer |
---|---|
What is WC-12Co powder? | WC-12Co is a tungsten carbide powder with 12% cobalt, known for its extreme wear resistance and toughness. |
Where is WC-12Co used? | It’s used in industries like aerospace, mining, automotive, and manufacturing for cutting tools and coatings. |
How is WC-12Co powder made? | WC-12Co powder is produced through a sintering process where tungsten carbide and cobalt are fused together. |
Why is cobalt added to WC powder? | Cobalt acts as a binder, improving the toughness and corrosion resistance of the tungsten carbide particles. |
What’s the difference between WC-12Co and WC-6Co? | WC-12Co contains more cobalt, offering better toughness and corrosion resistance but at a higher cost. |
Can WC-12Co powder be used in thermal spraying? | Yes, it is widely used in thermal spray processes like HVOF and plasma spraying for protective coatings. |
Conclusion
WC-12Co powder is a top-tier material known for its exceptional hardness, wear resistance, and high-temperature performance. Whether you’re in aerospace, mining, or manufacturing, this powder offers unparalleled durability and reliability. While it may come with a higher price tag compared to other powders, its advantages far outweigh the costs in the long run. With various models, sizes, and grades available, WC-12Co powder is adaptable to nearly any demanding application.
If you’re looking to enhance the performance of your components or coatings, WC-12Co powder is a solid investment that will undoubtedly pay off in terms of longevity and efficiency.