When it comes to specialized materials in the engineering and industrial sectors, Pure Mo Powder (Molybdenum powder) is often mentioned in the same breath as titanium, tungsten, or chromium. It’s a material with incredible properties—known for its resilience, high melting point, and superb electrical conductivity.
This article dives deep into the world of Pure Mo Powder, covering everything from its characteristics, applications, and grades to its comparison against other metal powders. Whether you’re an engineer, researcher, or simply curious about high-performance materials, this guide will leave no stone unturned.
Overview of Pure Mo Powder
Molybdenum (Mo) is a refractory metal with excellent properties that make it a top choice in high-temperature applications. Mo powder, in its pure form, is made by reducing molybdenum trioxide or ammonium molybdate using hydrogen at elevated temperatures. This pure powder can then be processed and shaped for various uses, from electronics to aerospace components.
Key Properties of Pure Mo Powder:
- Melting Point: 2,623°C (4,753°F)
- Density: 10.2 g/cm³
- Thermal Conductivity: 138 W/m·K
- Corrosion Resistance: High in non-oxidizing acids
- Electrical Conductivity: Excellent
Pure Mo Powder’s unique combination of properties, particularly its high melting point, makes it a crucial material in industries that require strength and durability under extreme conditions.
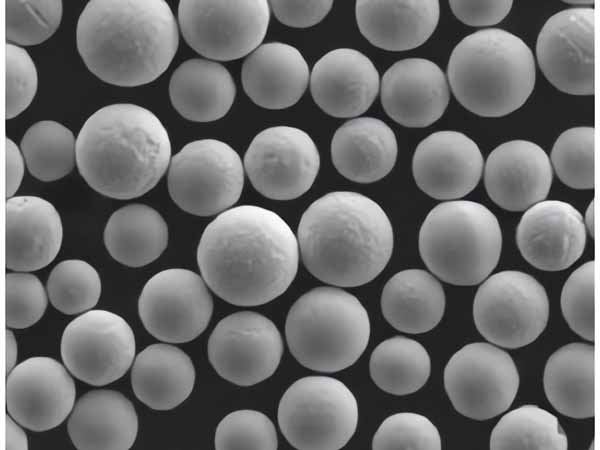
Types and Specifications of Pure Mo Powder
There are several types of Pure Mo Powder, each with its own specifications based on size, grade, and intended application. Below is a table that outlines some of the most popular variants and their characteristics.
Type | Particle Size | Purity | Applications | Description |
---|---|---|---|---|
Mo-Pure 99.95% | 1-5 µm | 99.95% | Semiconductor components, medical devices | Ultra-high purity molybdenum powder, used for sensitive applications requiring minimal contaminants. Ideal for microelectronics. |
Mo-Pure Fine | <1 µm | 99.9% | Thin films, coatings, research labs | This fine powder is optimized for thin-film deposition and research uses due to its ability to disperse uniformly across surfaces. |
Mo-HP Grade | 3-10 µm | 99.5% | Aerospace, defense, high-temperature parts | Known as high-performance grade molybdenum powder, it’s designed for high-stress environments like turbine blades or missile components. |
Mo-Spherical | 10-20 µm | 99.5% | 3D printing, additive manufacturing | Spherical particles provide superior flow characteristics, making it ideal for 3D printing applications where precision and smoothness are key. |
Mo-Coarse | 40-60 µm | 99.0% | Thermal spray coatings, heavy machinery | Coarser particles meant for bulk manufacturing and high-load applications. Frequently used in heavy industrial coatings for machinery parts. |
Mo-Nano | <100 nm | 99.95% | Nanoelectronics, catalysis, energy storage | Nano-sized particles open up new possibilities in nanotechnology fields like catalysis and advanced energy systems, thanks to their large surface area. |
Mo-Electronic | 5-15 µm | 99.8% | Circuit boards, integrated circuits (ICs) | Electronic grade molybdenum is designed for electrical conductivity and used widely in circuits and semiconductor devices. |
Mo-Dense | 20-50 µm | 99.6% | Aerospace, defense | Dense powder used in applications that require high density and durability under stress, such as in rocket nozzles and protective coatings. |
Mo-Spraying Grade | 30-70 µm | 99.0% | Plasma spraying, thermal barrier coatings | Used in thermal spray coating applications where molybdenum’s high melting point makes it effective as a thermal barrier material. |
Mo-Alloy Powder | 15-40 µm | 99.7% | Alloy production, corrosion resistance | Designed for blending into alloys, especially those meant to resist corrosion or wear in extreme environments, such as oil drilling equipment. |
Applications of Pure Mo Powder
Given its unique properties, Pure Mo Powder finds its way into several high-performance applications. Let’s break down some of the industries and use cases where this material is irreplaceable.
Application | Description | Common Types Used |
---|---|---|
Electronics | Molybdenum’s excellent electrical conductivity makes it ideal for use in semiconductor devices, thin-film transistors, and integrated circuits. | Mo-Electronic, Mo-Pure Fine |
Aerospace & Defense | The high melting point and strength of Mo make it a critical material in aerospace parts, such as rocket nozzles, turbine blades, and protective coatings. | Mo-HP Grade, Mo-Dense |
Additive Manufacturing | With 3D printing growing, spherical molybdenum powders are crucial for creating precise, high-strength parts in aerospace, medical, and automotive industries. | Mo-Spherical, Mo-Nano |
Thermal Spray Coatings | Used for producing wear-resistant, thermal barrier coatings in power generation and heavy machinery due to its heat tolerance and durability. | Mo-Spraying Grade, Mo-Coarse |
Medical Devices | Its biocompatibility allows it to be used in medical implants and devices, where reliability and non-reactivity with human tissues are essential. | Mo-Pure 99.95%, Mo-Nano |
Nanotechnology | Nano-sized molybdenum particles play a significant role in advanced fields like energy storage, catalysis, and nanoelectronics, thanks to their large surface area. | Mo-Nano, Mo-Alloy Powder |
Corrosion-Resistant Alloys | Molybdenum is often blended with other metals to create alloys that are exceptionally resistant to corrosion, especially in harsh chemical environments. | Mo-Alloy Powder, Mo-Coarse |
Specifications and Standards of Pure Mo Powder
Understanding the technical specifications is essential for anyone looking to use Pure Mo Powder in an industrial or research setting. The following table highlights key standards and sizing details.
Grade | Particle Size Range | Purity | Applicable Standards |
---|---|---|---|
Mo-Pure 99.95% | 1-5 µm | 99.95% | ASTM B386, ISO 4289 |
Mo-HP Grade | 3-10 µm | 99.5% | ASTM F15, AMS 7902 |
Mo-Spherical | 10-20 µm | 99.5% | ISO 9001, ASTM B662 |
Mo-Coarse | 40-60 µm | 99.0% | DIN 32513, AMS 7837 |
Mo-Nano | <100 nm | 99.95% | ISO 3290, MIL-PRF-13830B |
Mo-Spraying | 30-70 µm | 99.0% | ASTM B214, ISO 4499 |
Mo-Alloy Powder | 15-40 µm | 99.7% | SAE J470, AMS 6414 |
Advantages of Pure Mo Powder
1. High Melting Point
Molybdenum boasts an incredibly high melting point of over 2,600°C. Compared to materials like aluminum or even steel, Mo stands tall under extreme temperatures, making it ideal for high-heat applications.
2. Superior Electrical Conductivity
Electronics benefit from Mo’s conductivity. Pure Mo Powder is often used in semiconductors, printed circuit boards, and thin-film applications where precision is key.
3. Excellent Corrosion Resistance
One of molybdenum’s hidden strengths is its resistance to corrosion, especially in non-oxidizing acids. Compared to other metals like steel or nickel, Mo is less likely to degrade in harsh environments, making it valuable in chemical processing equipment.
4. High Density and Strength
In aerospace or defense applications, where materials need to withstand high stress without failure, Mo provides unmatched strength without adding excessive weight.
5. Versatility in Alloy Production
Molybdenum’s ability to blend well with other metals makes it an essential ingredient in high-strength alloys. Alloys made from Mo powders are often used to produce equipment designed for heavy-duty or corrosive environments.
Pure Mo Powder Compared to Other Metal Powders
Comparing Pure Mo Powder to other commonly used metal powders—such as tungsten, titanium, and aluminum—helps illustrate why molybdenum is chosen in specific applications.
Pure Mo Powder vs. Tungsten Powder
While tungsten has a higher melting point, molybdenum powder is more cost-effective and easier to work with. Tungsten is also significantly denser, making molybdenum a better option in weight-sensitive applications like aerospace.
Pure Mo Powder vs. Titanium Powder
Titanium shines in areas where lightweight strength is paramount, such as in medical devices. However, molybdenum is the go-to material in high-heat environments, thanks to its higher melting point and better performance under sustained stress.
Suppliers and Pricing of Pure Mo Powder
Several companies supply Pure Mo Powder globally, each offering different grades and specifications. Below is a summary of major suppliers, their typical offerings, and price ranges.
Supplier | Location | Available Grades | Price Range (USD/kg) |
---|---|---|---|
American Elements | United States | Mo-Pure 99.95%, Mo-Spherical | $300 – $500 |
Plansee Group | Austria | Mo-HP, Mo-Spraying Grade | $400 – $600 |
H.C. Starck | Germany | Mo-Nano, Mo-Coarse | $350 – $550 |
MolyWorks Materials | United States | Mo-Alloy, Mo-Dense | $280 – $480 |
Treibacher Industrie | Austria | Mo-Fine, Mo-Electronic | $320 – $520 |
Pros and Cons of Using Pure Mo Powder
Advantages | Disadvantages |
---|---|
High melting point suitable for extreme conditions | Expensive compared to more common materials |
Superior electrical and thermal conductivity | Difficult to machine or shape without proper tools |
Excellent corrosion resistance | Limited suppliers lead to higher procurement costs |
Versatility in alloy formation | Requires specialized handling due to high density |
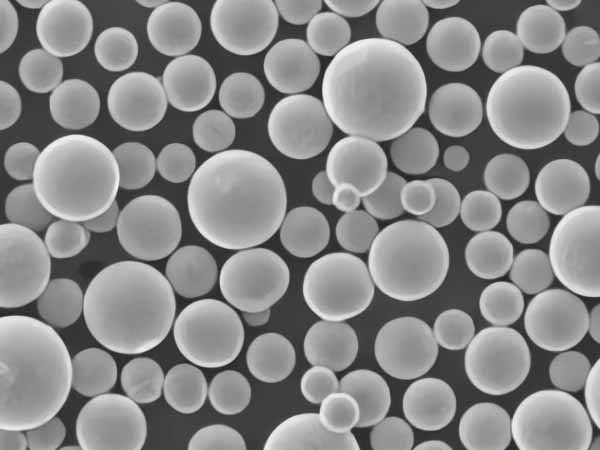
FAQs
Question | Answer |
---|---|
What is the primary use of Pure Mo Powder? | Pure Mo Powder is primarily used in high-temperature applications and electronic devices. |
How is Pure Mo Powder made? | It’s produced by reducing molybdenum trioxide or ammonium molybdate with hydrogen. |
Is molybdenum powder safe to handle? | Yes, but like all fine powders, it requires protective measures such as masks to avoid inhalation. |
Can molybdenum powder be alloyed with other metals? | Yes, molybdenum is often alloyed with nickel, iron, and other metals to enhance corrosion resistance. |
What is the typical cost of Pure Mo Powder? | The price ranges from $300 to $600 per kilogram, depending on the purity and supplier. |
Conclusion
Pure Mo Powder stands as a critical material for industries requiring extreme performance—whether it’s handling high temperatures in aerospace, providing corrosion resistance in chemical processing, or delivering electrical conductivity in electronics. Its versatility, though paired with higher costs, ensures that molybdenum will continue to be a material of choice for cutting-edge applications. As technology advances, we can only expect its uses to expand, pushing the boundaries of what’s possible with high-performance powders.
Whether you’re considering its use in advanced electronics or thermal barrier coatings, the unique properties of Pure Mo Powder make it an invaluable tool in the modern industrial arsenal.