If you’re looking for a unique metal powder with a range of industrial applications, you’ve probably come across C103 powder. This exotic metal alloy has properties that make it incredibly valuable for niche sectors, particularly in aerospace and high-temperature environments. But why is it so special? What makes it stand out compared to other metal powders like titanium or aluminum alloys? This article breaks down everything you need to know about C103 powder, from its composition and characteristics to applications, models, and comparisons with other materials. Grab a coffee, sit back, and let’s dive into the world of C103 powder.
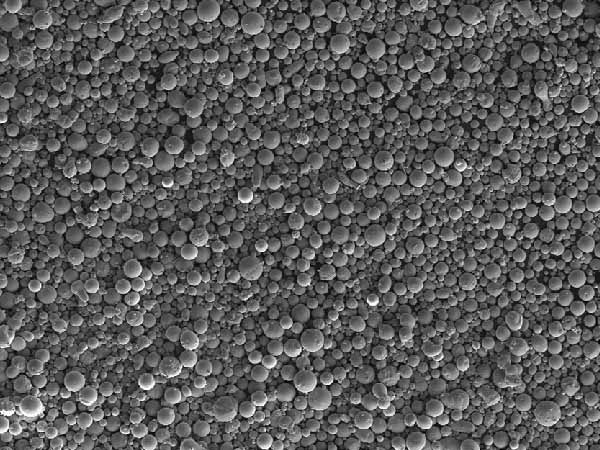
Overview of C103 Powder
C103 powder is a high-performance niobium-based alloy. Known for its remarkable heat resistance, strength, and adaptability, it is primarily used in the aerospace industry, especially in applications that demand materials capable of withstanding extreme temperatures and corrosive environments. Whether it’s space engines or nuclear reactors, C103 powder is a key player.
Here’s a quick snapshot of what C103 powder brings to the table:
Feature | Details |
---|---|
Primary Composition | Niobium (Nb) with small amounts of Hafnium (Hf), Titanium (Ti) |
Heat Resistance | Excellent; capable of withstanding temperatures exceeding 2400°F |
Corrosion Resistance | High; resistant to most corrosive environments |
Mechanical Strength | Superior tensile strength at high temperatures |
Common Applications | Aerospace, gas turbines, rocket engines, nuclear power systems |
What Exactly Is C103 Powder?
C103 powder is a niobium alloy that belongs to the Niobium-Hafnium-Titanium family. What does that mean for non-engineers? Essentially, it’s a powder made from a highly specialized mix of metals. While niobium is the dominant component, small amounts of hafnium and titanium are added to increase its durability and performance, particularly at high temperatures.
The result is an alloy that can withstand heat better than most other materials, making it a go-to choice for extreme applications like rocket nozzles and heat shields. Think of it as the sports car of metal powders—designed for speed, performance, and extreme conditions.
Composition of C103 Powder
C103 powder’s composition is key to its impressive performance. Understanding the blend of elements that make up this alloy will give you insights into why it’s chosen for highly demanding environments.
Element | Percentage | Purpose |
---|---|---|
Niobium (Nb) | 85–90% | Provides heat resistance and corrosion protection |
Hafnium (Hf) | 10% | Improves thermal stability and strengthens the alloy |
Titanium (Ti) | 5–7% | Enhances mechanical strength and reduces weight |
Tantalum (Ta) | Trace Amounts | Adds ductility and resistance to brittle fracture |
Why These Specific Elements?
Niobium is the star of the show in C103 powder. It provides the base structure, which gives the powder its high heat resistance. Adding hafnium further enhances this resistance, and titanium boosts strength while keeping the material relatively lightweight. These three elements work in perfect harmony, much like a well-tuned orchestra, each contributing something unique to the overall performance.
Characteristics of C103 Powder
When it comes to engineering materials, it’s not just about what they’re made of; it’s about what they can do. C103 powder has some outstanding characteristics that make it the material of choice for extreme applications. Let’s break down its key properties:
Characteristic | Details |
---|---|
Thermal Resistance | Handles temperatures above 2400°F without degradation |
Density | Around 8.6 g/cm³—denser than titanium but lighter than tungsten |
Corrosion Resistance | Highly resistant to oxidation and acidic environments |
Melting Point | Approximately 4310°F (2377°C) |
Ductility | High; can be formed into complex shapes without cracking |
Tensile Strength | Retains strength at elevated temperatures |
Oxidation Resistance | Excellent, especially in vacuum environments |
How Does C103 Powder Compare to Other Metal Powders?
Compared to titanium powder, C103 powder is stronger at high temperatures but heavier. On the other hand, when compared to tungsten powder, C103 is lighter and easier to work with but cannot match tungsten’s extreme heat resistance. It’s all about trade-offs, much like choosing between a high-powered truck and a sleek sports car—each has its pros and cons depending on what you’re looking for.
Top Models of C103 Powder
Not all C103 powders are created equal. Different manufacturers and suppliers offer variations in composition and particle size to meet specific industry needs. Here’s a breakdown of some popular models:
Model Name | Description | Special Features |
---|---|---|
C103-1 | General-purpose C103 powder; used in aerospace | Standard composition, ideal for high-heat applications |
C103-2 | Modified with additional hafnium | Enhanced heat and oxidation resistance |
C103-HT | High-temperature variant, withstands > 2600°F | Optimized for extreme thermal environments |
C103-Fine | Finer particle size for improved sintering | Better for 3D printing and powder metallurgy |
C103-SuperAlloy | Ultra-purified version for critical applications | Highly resistant to corrosion and oxidation |
C103-HF | High-Hafnium content for added thermal stability | Excellent for rocket nozzle and turbine applications |
C103-XT | Extended tensile strength variant | Designed for structural components |
C103-3DPrint | Specially formulated for additive manufacturing | Enhanced flowability for 3D printing |
C103-Nuclear | Specifically used in nuclear reactors | Engineered for radiation resistance |
C103-GT | Gas turbine optimized powder | Designed for high-stress, high-heat environments |
How to Choose the Right C103 Model
When choosing a C103 powder, it’s all about matching the material to your specific needs. For instance, if you’re working on a rocket nozzle, you’d likely want a model like C103-HT or C103-HF. On the other hand, for 3D printing applications, you’d opt for C103-Fine or C103-3DPrint due to their particle size and flow characteristics.
Applications of C103 Powder
C103 powder shines in environments where extreme heat, high stress, and corrosion are common. It’s no wonder it’s a favorite in the aerospace and defense industries. Below are some key applications of C103 powder:
Industry | Application | Why C103? |
---|---|---|
Aerospace | Rocket nozzles, heat shields, and engine components | Exceptional heat resistance and mechanical strength |
Defense | Missile components and thermal protection systems | High-temperature endurance and corrosion resistance |
Nuclear | Structural components in reactors | Resists radiation damage and extreme heat |
Power Generation | Gas turbines, power plant components | Can handle high operating temperatures and stress |
Automotive | High-performance engine parts | Superior strength-to-weight ratio under heat stress |
Additive Manufacturing | 3D printing complex aerospace components | High ductility and precise sintering properties |
Specifications and Standards of C103 Powder
Every industry has its standards, and C103 powder is no different. Various grades of the powder are manufactured to meet different specifications. Understanding these specifications ensures you’re using the right material for the right job.
Specification | Details |
---|---|
Grade | Multiple grades available based on purity levels |
Particle Size | Ranges from 15µm to 45µm for additive manufacturing |
Purity Level | 99.9% pure for critical aerospace applications |
ASTM Standards | ASTM B884 for powder metallurgy |
ISO Certification | ISO 9001:2008 for quality management |
Tolerance Levels | Varies by supplier; tighter tolerances for 3D printing applications |
Density | 8.57–8.60 g/cm³ |
Suppliers and Pricing Details of C103 Powder
Finding the right supplier is crucial for getting high-quality C103 powder. Below are some major suppliers and their average pricing:
Supplier | Average Price (per kg) | Specialization |
---|---|---|
ATI Metals | $1,500–$2,000 | High-performance alloys for aerospace and defense |
Metal Powder Solutions | $1,200–$1,800 | Additive manufacturing powders |
Advanced Powder Systems | $1,400–$2,100 | Powder metallurgy and custom alloy production |
Materion Corporation | $1,600–$2,300 | Specialty metal powders for nuclear and defense |
Höganäs AB | $1,500–$2,200 | Aerospace and 3D printing applications |
Factors Affecting Pricing
Prices can vary depending on factors such as:
- Purity Levels: Higher purity powders cost more but offer better performance.
- Particle Size: Fine powders suitable for 3D printing are more expensive than coarse powders.
- Supplier Specialization: Suppliers with ISO certifications or specialized manufacturing processes may charge premium rates.
Advantages and Limitations of C103 Powder
Like any material, C103 powder comes with its own set of pros and cons. Understanding these helps in determining whether it’s the right fit for your project.
Advantages | Limitations |
---|---|
High heat resistance | Expensive compared to other metal powders |
Exceptional corrosion resistance | Heavier than some alternative alloys |
Strong mechanical properties | Requires specialized handling |
Suitable for complex shapes and 3D printing | Limited availability due to specialized production |
Excellent ductility | Longer lead times for custom formulations |
Is C103 Powder Worth the Investment?
While C103 powder is not the cheapest option out there, its advantages in extreme environments make it invaluable. If you’re working on a high-stakes project where failure isn’t an option, the performance vs. cost trade-off leans heavily in favor of C103 powder.
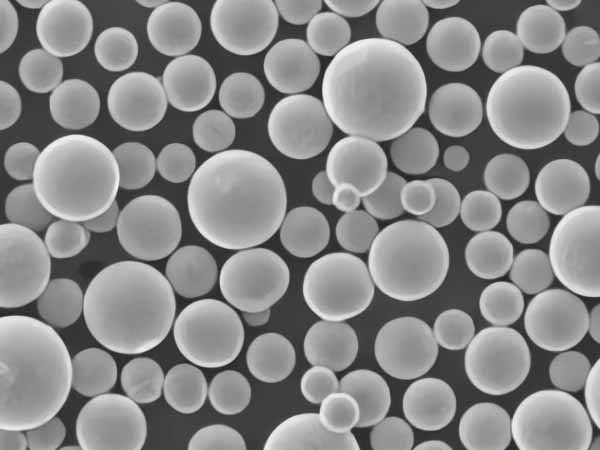
FAQ
Question | Answer |
---|---|
What is C103 powder made of? | C103 powder is primarily composed of niobium, hafnium, and titanium. |
What industries use C103 powder? | Aerospace, defense, nuclear, power generation, and additive manufacturing. |
How much does C103 powder cost? | Prices typically range from $1,200 to $2,300 per kilogram. |
Is C103 powder suitable for 3D printing? | Yes, specific models like C103-Fine and C103-3DPrint are optimized for 3D printing. |
What is the melting point of C103 powder? | Approximately 4310°F (2377°C). |
Why is C103 powder used in rocket nozzles? | Its high heat resistance and mechanical strength make it ideal for extreme temperature applications. |
Can C103 powder be recycled? | Yes, C103 powder can be recycled, though it requires specialized processes. |
What is the difference between C103 and titanium powders? | C103 offers better heat resistance but is heavier than titanium. |
How is C103 powder produced? | C103 powder is typically produced using atomization techniques for consistent particle size. |
Are there alternatives to C103 powder? | Alternatives include tungsten and titanium alloys, though each has its trade-offs. |
Conclusion
In a nutshell, C103 powder stands out because of its unique combination of heat resistance, strength, and corrosion resistance. While it may be pricier than other metal powders, its performance in critical applications like rocket engines and nuclear reactors makes it worth every penny. If your project demands the highest levels of performance, C103 powder should definitely be on your radar.
Now that you’re fully versed in the world of C103 powder, it’s time to take the next step in your engineering project with confidence!