Overview of Triballoy T800 Powder
Triballoy T800 powder, a high-performance metal alloy powder, is renowned for its excellent resistance to wear, corrosion, and high-temperature environments. Designed primarily for applications requiring extreme durability, Triballoy T800 is a standout choice in industries such as aerospace, automotive, and energy production. This article delves into every facet of Triballoy T800, examining its composition, properties, applications, and advantages compared to other metal powders on the market.
Triballoy T800 is part of a larger family of metal powders, each engineered with unique characteristics tailored to specific industrial needs. We’ll explore various other metal powder models, comparing their strengths, limitations, and cost-effectiveness to guide you in choosing the right material.
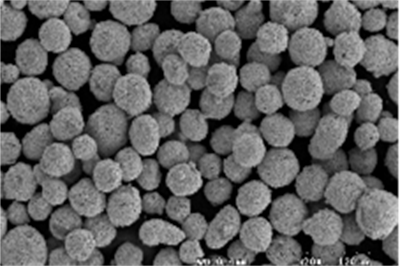
Metal Powder Models with Composition, Properties, and Characteristics
The following table provides an overview of different metal powder models, detailing their specific composition, core properties, and distinguishing characteristics:
Metal Powder Model | Composition | Properties | Characteristics |
---|---|---|---|
Triballoy T800 | Cobalt, Molybdenum, Chromium, Niobium | High wear resistance, corrosion-resistant, withstands high temperatures | Excellent for aerospace and industrial tools |
Triballoy T900 | Cobalt, Chromium, Nickel | Enhanced corrosion resistance, toughness | Suitable for marine and chemical environments |
Hastelloy X | Nickel, Molybdenum, Iron | Exceptional oxidation resistance, high strength | Ideal for gas turbine and petrochemical uses |
Stellite 6 | Cobalt, Chromium, Tungsten | Good hardness, impact resistance | Common in valve seats, saw tips, industrial wear parts |
Inconel 625 | Nickel, Chromium, Molybdenum | Outstanding tensile strength, fatigue-resistant | Highly applicable in jet engines, ocean equipment |
Haynes 282 | Nickel, Chromium, Molybdenum, Titanium | Creep-resistant at high temperatures | Widely used in gas turbines, aerospace structures |
Mar-M 509 | Cobalt, Chromium, Tungsten | High-temperature stability, excellent hardness | Perfect for hot section turbine components |
Rene 41 | Nickel, Chromium, Cobalt, Molybdenum | Strong under high stress, high-temperature use | Often used in aircraft parts, turbine blades |
Waspaloy | Nickel, Chromium, Molybdenum | Creep-resistant, oxidation-resistant | Aerospace and high-stress applications |
Haynes 188 | Cobalt, Chromium, Tungsten, Nickel | Great for high-temperature, high-stress conditions | Often used in jet engines, aerospace industries |
Composition of Triballoy T800 Powder
Triballoy T800 is a cobalt-based alloy primarily composed of cobalt, molybdenum, chromium, and niobium. Each element in Triballoy T800 plays a crucial role in its performance:
- Cobalt (Co): Provides high wear resistance and stability under extreme temperatures.
- Molybdenum (Mo): Enhances corrosion resistance and hardenability.
- Chromium (Cr): Adds a layer of oxidation resistance, ideal for high-temperature environments.
- Niobium (Nb): Increases hardness, ensuring prolonged durability in harsh conditions.
These elements combine to make Triballoy T800 suitable for environments where materials undergo abrasive wear and are subject to high-stress, high-temperature conditions.
Characteristics of Triballoy T800 Powder
Triballoy T800 powder is specifically engineered for demanding applications. Let’s examine its key characteristics:
- Wear Resistance: Due to the cobalt matrix and molybdenum-rich composition, Triballoy T800 offers unparalleled resistance to wear, even under extreme friction.
- Corrosion Resistance: The chromium in Triballoy T800 enables it to withstand corrosive environments, making it ideal for offshore, chemical, and petrochemical applications.
- High-Temperature Stability: Its unique blend of metals allows Triballoy T800 to maintain structural integrity and resist oxidation at elevated temperatures.
- Hardness: With a Rockwell hardness in the range of HRC 50-60, it is well-suited for industrial applications where surface durability is critical.
Applications of Triballoy T800 Powder
Application | Industry | Reason for Use |
---|---|---|
Gas Turbine Blades | Aerospace | High temperature and wear-resistant |
Valve Seats | Automotive | Excellent for durability under high stress |
Downhole Tools | Oil & Gas | Corrosion and wear resistance in harsh environments |
Extruder Screws | Manufacturing | Enhances lifespan under high-pressure operations |
Chemical Processing | Chemical Processing | Resistant to corrosive chemicals |
Pump Components | Water Treatment | Withstands constant wear and high moisture levels |
Bearings | Industrial Machinery | Durable under high load and friction |
Advantages of Triballoy T800 Powder Compared to Other Powders
Triballoy T800 has distinct advantages that set it apart from other metal powders, especially when compared to models like Stellite 6 or Inconel 625.
Feature | Triballoy T800 | Stellite 6 | Inconel 625 |
---|---|---|---|
Wear Resistance | Very high due to molybdenum content | Moderate | Low to moderate |
Corrosion Resistance | Excellent, especially against oxidizing agents | Good, especially in water-based environments | Exceptional, even in seawater |
High-Temperature Resistance | Up to 1,000°C | Up to 600°C | Up to 1,000°C |
Hardness | HRC 50-60 | HRC 40-50 | HRC 35-45 |
Cost | Relatively higher | Moderate | High |
Specifications of Triballoy T800 Powder
Specification | Triballoy T800 |
---|---|
Particle Size | 10-45 µm |
Density | 8.75 g/cm³ |
Melting Point | 1,270-1,360°C |
Hardness | HRC 50-60 |
Thermal Conductivity | 14 W/m·K |
Suppliers and Pricing for Triballoy T800 Powder
Supplier | Region | Approximate Price per kg |
---|---|---|
PowderTech Metals | North America | $150-$200 |
Metallurgic Industries | Europe | $180-$230 |
Advanced Metal Powders | Asia | $140-$190 |
AlloyWorld Solutions | Global | $170-$210 |
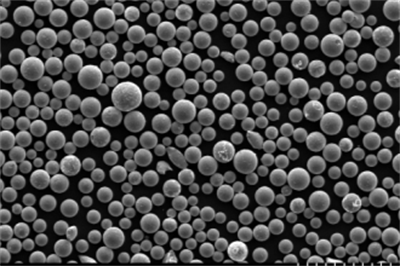
Triballoy T800 Powder vs Other Metal Powders
When it comes to choosing a metal powder for your specific application, here’s how Triballoy T800 stacks up against its competitors:
- Triballoy T800 vs Stellite 6: Triballoy T800 offers superior wear resistance due to its higher molybdenum content, making it ideal for high-friction environments, whereas Stellite 6 is often chosen for moderate wear applications at a lower cost.
- Triballoy T800 vs Inconel 625: Both are resistant to corrosion, but Inconel 625 is preferred in environments with continuous exposure to seawater, while Triballoy T800’s wear resistance makes it a better fit for high-abrasion settings.
FAQs
Question | Answer |
---|---|
What is Triballoy T800 powder made of? | Cobalt, Molybdenum, Chromium, and Niobium, specifically designed for high wear resistance. |
Can Triballoy T800 withstand high temperatures? | Yes, it performs well in temperatures up to 1,000°C. |
Is Triballoy T800 cost-effective? | While it has a higher price, its durability can result in long-term cost savings. |
Which industries use Triballoy T800? | Aerospace, automotive, oil & gas, chemical processing, and manufacturing. |
How does Triballoy T800 compare to Stellite 6? | Triballoy T800 is harder and more wear-resistant, though it may be pricier. |