Introduction to Triballoy T400 Powder
Triballoy T400 Powder is a high-performance, cobalt-based alloy powder known for its exceptional resistance to wear, corrosion, and high temperatures. This material is primarily utilized in industries where extreme conditions can degrade standard materials—think of oil rigs, aerospace components, or heavy-duty machinery. But what exactly makes Triballoy T400 stand out in such demanding environments? Its unique composition, boasting an array of robust elements like cobalt, molybdenum, and chromium, gives it properties that few other alloys can match.
With growing applications in industries where reliability and longevity are critical, Triballoy T400 Powder has gained a reputation as a go-to solution. But selecting the right alloy powder isn’t just about knowing its toughness. Factors like composition, properties, and industry standards all play a role in choosing the most effective material. This guide will walk you through everything you need to know about Triballoy T400 Powder, from its technical specifications to its industry applications and even how it stacks up against similar powders on the market.
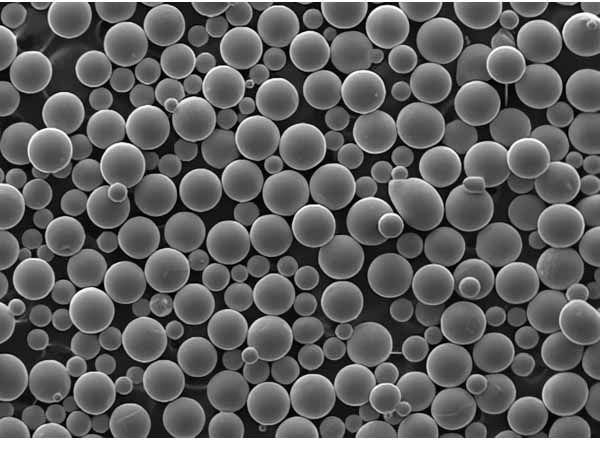
Composition of Triballoy T400 Powder
One of the key factors behind Triballoy T400 Powder’s remarkable properties is its composition. This cobalt-based alloy powder is enriched with elements like molybdenum, silicon, and chromium. Each element is selected to provide strength, corrosion resistance, and thermal stability.
Key Components of Triballoy T400 Powder
Element | Percentage Composition | Role in Alloy |
---|---|---|
Cobalt (Co) | 60-65% | Base metal; offers high-temperature resistance. |
Molybdenum (Mo) | 28-32% | Provides hardness and wear resistance. |
Silicon (Si) | 1-2% | Enhances oxidation resistance. |
Chromium (Cr) | 3-5% | Increases corrosion resistance. |
In this unique mix, cobalt serves as the core ingredient, providing a foundation of heat resistance, while molybdenum adds to its wear resistance. The silicon and chromium components further bolster its resistance to oxidation and corrosion, making Triballoy T400 a formidable material in environments where other alloys would struggle.
Characteristics and Properties of Triballoy T400 Powder
Triballoy T400 Powder is not just another metal powder; it’s a high-performance material engineered for extremes. Here’s a look at its primary characteristics:
Properties of Triballoy T400 Powder
Property | Value/Range | Explanation |
---|---|---|
Density | 8.4 g/cm³ | High density, contributing to its durability. |
Hardness | 55-60 HRC | Exceptional hardness, reducing wear in abrasive settings. |
Melting Point | Approx. 1350°C | High melting point allows usage in extreme heat. |
Corrosion Resistance | Excellent | Withstands harsh chemicals and corrosive environments. |
Wear Resistance | Superior | Ideal for applications involving high friction. |
Compared to other alloys, Triballoy T400 stands out for its wear resistance. Think of it like armor for your machinery—a shield that keeps surfaces from breaking down under stress. The alloy’s resistance to corrosion also makes it ideal for applications where it will face chemicals, salt, or other corrosive agents, such as marine environments.
Applications of Triballoy T400 Powder
Triballoy T400 Powder is used in a variety of industries. Its specific properties make it a prime choice for applications where wear, heat, and corrosion are constant challenges. Here are some of the primary applications:
Uses of Triballoy T400 Powder in Industry
Industry | Application | Benefits |
---|---|---|
Oil & Gas | Drill bits, valves, and pumps | Exceptional wear and corrosion resistance. |
Aerospace | Jet engine components | Can withstand high temperatures and friction. |
Manufacturing | Tooling parts, metal cutting machinery | Improves lifespan of tools subjected to constant abrasion. |
Automotive | Engine components, exhaust systems | Ideal for high-temperature areas prone to wear. |
Marine | Pump and valve coatings, propellers | Resists saltwater corrosion effectively. |
By providing extended durability and reducing maintenance needs, Triballoy T400 Powder helps companies improve efficiency and reduce downtime—a crucial factor in industries like aerospace and oil & gas, where time is money.
-
CM247LC Powder | Nickel Alloy Powder
-
0# Pure Nickel powder
-
NiCoCrAlY alloys powders
-
Rene 142 alloy-Rene Powder
-
Haynes 25 Haynes Powder
-
Best Hastelloy C-22 Powder-High temperature alloy Powder for 3D Printing
-
Best Hastelloy C-276 Powder-High temperature alloy Powder for 3D Printing
-
Best Hastelloy N Powder-High temperature alloy Powder for 3D Printing
-
Best Hastelloy B Powder丨High temperature alloy Powder for 3D Printing
Specifications and Standards for Triballoy T400 Powder
In technical applications, meeting specifications is essential. Triballoy T400 Powder is available in a variety of grades and sizes, which ensures that manufacturers can select the right specification for each project.
Available Sizes, Grades, and Standards for Triballoy T400
Specification | Available Sizes | Standards Met |
---|---|---|
Particle Size | 15-45 μm, 45-106 μm | ASTM, ISO standards for alloy powders |
Grade | Standard, High-purity | ASTM B 929 for cobalt-based alloys |
Density | 8.4 g/cm³ | Adheres to industry density standards |
Manufacturers rely on these standards to ensure quality, consistency, and safety. For example, ASTM B 929 is a widely recognized specification that covers the requirements for cobalt-based alloys in powder form, making it easier for companies to verify that their materials meet necessary performance benchmarks.
Popular Metal Powder Models Comparable to Triballoy T400
When it comes to wear-resistant and high-performance alloys, Triballoy T400 isn’t the only option on the market. Here are some alternatives that provide similar properties for various applications.
Comparison of Alternative Metal Powder Models
Powder Model | Primary Composition | Unique Properties |
---|---|---|
Tribaloy T800 | Cobalt, Chromium, Molybdenum | Higher hardness than T400, ideal for severe wear. |
Stellite 6 | Cobalt, Chromium | Excellent thermal shock resistance, used in turbines. |
Inconel 625 | Nickel, Chromium, Molybdenum | Corrosion resistance with higher flexibility. |
Haynes 25 | Cobalt, Nickel, Tungsten | High-temperature tolerance, useful in jet engines. |
MP35N | Nickel, Cobalt, Chromium | Combines strength and corrosion resistance. |
Ultimet | Cobalt, Chromium, Molybdenum | Balances wear and corrosion resistance for marine use. |
Hastelloy C276 | Nickel, Molybdenum, Chromium | Exceptional chemical resistance, used in chemical plants. |
Waspaloy | Nickel, Chromium | High tensile strength at elevated temperatures. |
Cobalt-Chrome Alloy | Cobalt, Chromium | Known for wear resistance, used in biomedical implants. |
Nimonic 80A | Nickel, Chromium | High creep resistance, used in power generation. |
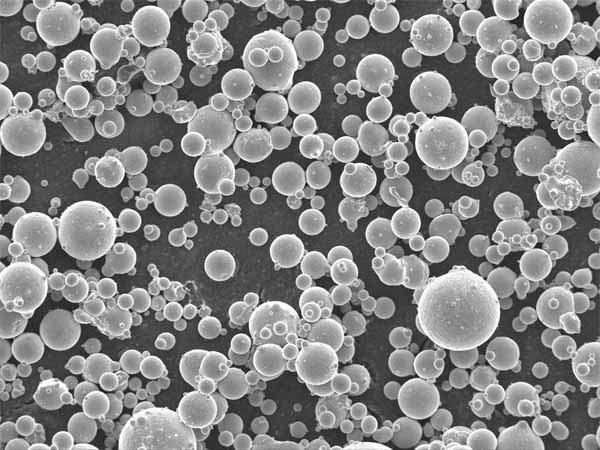
FAQs
Question | Answer |
---|---|
What is Triballoy T400 Powder used for? | Primarily in high-wear, high-temperature environments such as aerospace, oil & gas, and tooling. |
What makes it different from other alloys? | Its unique cobalt-based composition with high molybdenum content for superior wear resistance. |
Is it corrosion-resistant? | Yes, particularly against oxidation and corrosive agents. |
How is it priced compared to similar powders? | Slightly higher due to its specialized properties and applications. |