Effect of Ni on CuAl10 Laser Cladding Properties
Effect of Ni Addition on Microstructure and Properties of Laser Cladding CuAl10 Copper Alloy
In the fields of marine engineering, chemical equipment, etc., copper alloys are widely used due to their excellent thermal conductivity and corrosion resistance, but their insufficient surface hardness and wear resistance often limit their service life. Alloy composition design of laser cladding copper alloys can improve performance through surface modification.
Recent studies have found that the addition of Ni elements can optimize the laser cladding coating of CuAl10 copper alloy. Its microstructure, mechanical properties and corrosion resistance can be significantly improved. This article will deeply analyze the mechanism of optimization by the addition of Ni element.
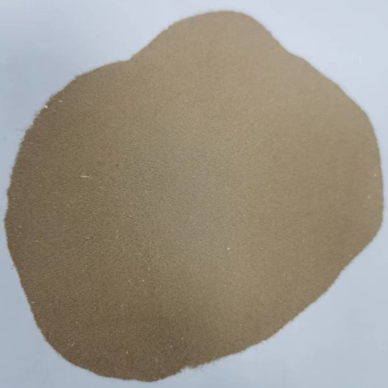
Microstructre evolution of coating of CuAl10 after adding Ni
Microstructure of cladding coating with different Ni wt%0% (b) 1.5% (c) 3.0% (d) 4.5% |

In the CuAl10 cladding layer without Ni addition, the second phase is randomly distributed in a dendritic or spherical form, resulting in an uneven structure. After adding 1.5%~6.0% Ni, Ni acts as a “diffusion catalyst” to promote the solid dissolution of elements in the α-Cu matrix and inhibit the precipitation of second phase. When the Ni content reaches 4.5%, the surface of the cladding layer has almost no particle defects and presents a continuous and smooth microstructure.
Microhardness evolution of coating of CuAl10 after adding Ni
Hardness curves of cladding coating with different Ni wt%0#: 0%, 1#: 1.5%, 3#: 4.5% |
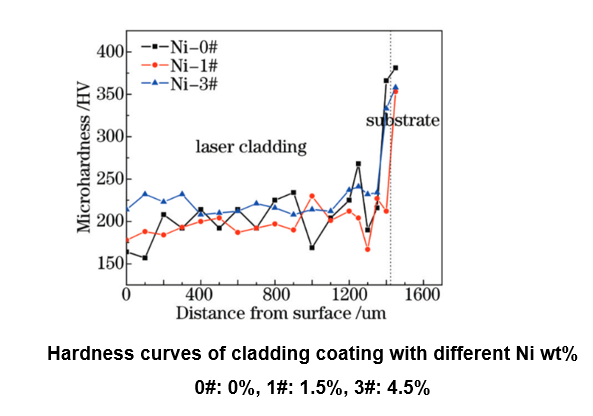
Microhardness jumps from “fluctuation” to “uniform” with the addition of Ni. The hardness of the coating without Ni fluctuates violently (157~268 HV) due to the uneven distribution of second phase, which causes local stress concentration. After adding Ni, the solid solution strengthening effect is significant, and the uniformity of hardness distribution is improved.
Conclusion
The introduction of Ni element, through the dual mechanisms of solid solution strengthening and electrochemical passivation, has made a qualitative leap in the performance of laser cladding CuAl10 coating.
In the future, the addition of multiple elements (such as Ni+Cr+Mo) and the optimization of process parameters on laser cladding CuAl10 coating will be expected to further break through the performance limit.
Other Laser Cladding Powders produced by TRUER:
Copper based: CuSn10, CuSn15, CuSn12Ni2, CuAl10, CuAl10Fe1, Cu-1, Cu-2, CuAlNiFe
Nickel based: C22, C276, Monel 400, Monel K500, Inconel 600, Inconel 625, Inconel 825, Hastelloy C, Hastelloy B, NiCr 80/20, NiCrAlY, Ni60A, Ni60B, Ni40
Cobalt based: Stellite 1, Stellite 3, Stellite 6, Stellite 12, Stellite 21, Stellite 25, Stellite 31, Triboloy T400, T800, T900
Iron based: D2, H13, M2, T15, T15M, 18Ni300, M35, M42, S390, M390
Tungsten based: WC-12Co, WC-10Ni, WC-65Ni60, WC-10Co-4Cr