Al 3003 powder, a champion among aluminum alloy powders, has become a cornerstone of metal additive manufacturing (MAM). Imagine crafting intricate objects layer by layer, not from molten metal but from a fine, metallic dust. This is the magic of MAM, and Al 3003 powder plays a starring role due to its unique blend of properties. But before we delve deeper, let’s establish a solid foundation.
Understanding Metal Powders and Al 3003’s Place
Metal powders are the building blocks of MAM. These tiny, granular particles, typically ranging from 10 to 100 microns in diameter (that’s about the width of a human hair!), are meticulously crafted from various metals and alloys. During the MAM process, the chosen powder is selectively deposited and fused together, layer by layer, to create a three-dimensional object based on a digital design.
Al 3003 powder stands out for its versatility. It’s a workhorse material, well-suited for a wide range of applications due to its:
- Excellent weldability: The particles readily fuse together during MAM, creating strong and reliable bonds.
- Good formability: Al 3003 powder allows for the creation of complex shapes with intricate details.
- High corrosion resistance: The aluminum-manganese composition provides good resistance to rust and degradation.
- Machinability: Parts printed with Al 3003 powder can be easily machined for additional finishing or functionality.
- Cost-effectiveness: Compared to other metal powders, Al 3003 is relatively affordable, making it an attractive choice for various projects.
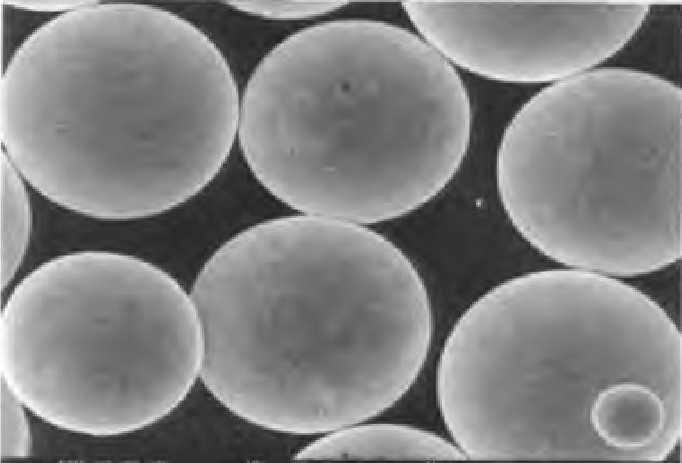
Composition, Properties, and Characteristics of Al 3003 Powder
Composition | Typical Percentage (wt%) | Key Property Influence |
---|---|---|
Aluminum (Al) | Min. 97.0 | Base metal, providing overall structure and machinability |
Manganese (Mn) | 1.0 – 1.5 | Improves strength, corrosion resistance, and weldability |
Copper (Cu) | Max. 0.2 | Minor influence on mechanical properties |
Iron (Fe) | Max. 0.7 | May affect strength and weldability in higher concentrations |
Silicon (Si) | Max. 0.6 | Can impact castability and weldability |
Other (combined) | Max. 0.15 | Trace elements with minimal influence |
Applications of Al 3003 Powder
Al 3003 powder’s versatility shines through in its diverse applications across various industries. Here are some prominent examples:
Application Area | Examples | Key Considerations |
---|---|---|
Automotive: | Lightweight components like brackets, housings, and prototypes | Excellent strength-to-weight ratio and good machinability for post-processing |
Aerospace: | Non-critical structural parts, heat shields, and fluid handling components | Corrosion resistance and good weldability for reliable performance |
Consumer Goods: | Sporting equipment components, customized enclosures, and decorative items | Formability for intricate shapes and aesthetics alongside machinability for finishing touches |
Building and Construction: | Architectural panels, lightweight cladding materials, and custom-designed brackets | Corrosion resistance for outdoor applications and good strength for structural integrity |
Medical and Dental: | Prosthetics, implants (non-load-bearing), and customized medical devices | Biocompatible properties (depending on specific processing) and good formability for complex geometries |
Different Metal Powders
While Al 3003 powder reigns supreme for its versatility, the world of metal powders offers a vast selection for specific needs. Here’s a glimpse into some popular contenders:
- 316L Stainless Steel: Known for its exceptional corrosion resistance, making it ideal for applications in harsh environments like marine settings or medical implants.
- Inconel 625: A champion in high-temperature applications, offering impressive strength and resistance to oxidation at elevated temperatures. Used in aerospace and energy sectors.
- Titanium 6Al-4V: The go-to choice for applications requiring a perfect blend of strength, low weight, and biocompatibility. Widely used in aerospace, medical implants, and sporting goods.
- Aluminum SiC Composite Powder: This unique blend combines the lightweight nature of aluminum with the exceptional strength and wear resistance of silicon carbide. Ideal for components requiring high abrasion resistance.
- Copper: A conductor’s dream, copper powder offers excellent electrical conductivity, making it perfect for creating electrical components, heat exchangers, and electromagnetic shielding applications.
- Nickel: Often used in electroplating applications due to its excellent corrosion resistance and good formability. Can also be used for creating pure nickel components for specific electrical or magnetic properties.
- Tool Steel: Various tool steel grades exist in powder form, offering exceptional hardness and wear resistance. Ideal for creating cutting tools, molds, and dies used in manufacturing processes.
- Inconel 718: A close cousin of Inconel 625, offering similar high-temperature performance but with even greater strength. Used in demanding aerospace applications requiring exceptional mechanical properties at elevated temperatures.
- Cobalt Chrome: Another biocompatible metal powder, often used in conjunction with 3D printing for creating custom-designed prosthetics and implants. Offers good strength and wear resistance.
- Niobium: This lesser-known metal powder offers a unique combination of high melting point, good superconductivity, and excellent corrosion resistance. Finding niche applications in superconductor technologies and specific aerospace components.
Choosing the Right Powder: A Balancing Act
As you can see, the selection of metal powders is vast, each offering a distinct set of properties ideal for specific applications. Choosing the right powder involves a careful balancing act, considering factors like:
- Required mechanical properties: Strength, ductility, fatigue resistance, and wear resistance are all crucial considerations depending on the application’s demands.
- Thermal properties: For high-temperature applications, consider powders like Inconel or Titanium Al-4V that can withstand extreme heat without compromising performance.
- Corrosion resistance: If the component will be exposed to harsh environments, a powder like 316L stainless steel might be necessary for optimal longevity.
- Formability: The ability to create intricate shapes is vital for certain applications. Al 3003 and some titanium powders excel in this aspect.
- Machinability: If post-processing is required, consider powders that can be easily machined for final finishing or dimensional adjustments.
- Cost: Metal powders can vary significantly in price. Al 3003 sits on the affordable side, while exotic materials like Niobium might be more expensive.
Specifications, Sizes, Grades, and Standards
Here’s a breakdown of Al 3003 powder specifications to provide a clearer picture:
Property | Description |
---|---|
Particle Size Distribution | Typically ranges from 15 to 45 microns, ensuring good flowability and packing density during the MAM process. |
Apparent Density | Around 2.7 g/cm³, which influences the amount of powder required to build a specific volume in the final part. |
Sphericity | Ideally, particles should be as spherical as possible for optimal packing and flow characteristics. |
Powder Flow | Free-flowing powders ensure smooth operation within the MAM equipment. |
Moisture Content | Low moisture content is crucial to prevent issues like spatter or inconsistent bonding during MAM. |
Oxygen Content | Minimizing oxygen content helps maintain good weldability and mechanical properties. |
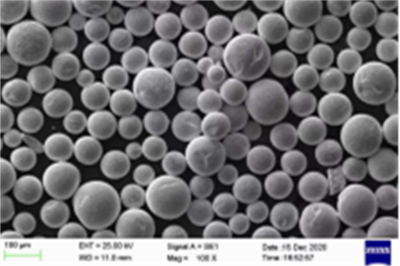
Standards and Regulations
Several standards govern the production and use of metal powders for MAM. Here are some prominent examples:
- ASTM International: Develops and publishes technical standards for various materials, including metal powders. Standards like ASTM B294 for aluminum alloy powders provide guidelines for composition, particle size, and other properties.
- American Welding Society (AWS): Focuses on welding standards and procedures. AWS A5.9 / A5.9M covers specifications for shielding gases and electrodes used in welding aluminum alloys, which can be relevant to MAM processes involving Al 3003 powder.
- Manufacturer’s Specifications: Individual metal powder suppliers often have their own specifications that detail the unique characteristics of their powders. It’s crucial to consult the specific product datasheet for precise details.
Al 3003 Powder: A Cost-Benefit Analysis
Pros:
- Affordable: Compared to other metal powders, Al 3003 is a budget-friendly option.
- Versatile: Its well-rounded properties make it suitable for a wide range of applications.
- Good weldability: Ensures strong and reliable bonds between particles during MAM.
- Machinable: Allows for post-processing and finishing of printed parts.
- Relatively lightweight: Aluminum’s inherent lightness contributes to the final weight of the printed component.
Cons:
- Moderate strength: Compared to some other metal powders like Titanium 6Al-4V, Al 3003 offers a lower level of strength.
- Not ideal for high temperatures: While it performs well in general applications, Al 3003 isn’t the best choice for parts exposed to extreme heat.
The Final Verdict: When to Choose Al 3003 Powder
Al 3003 powder shines in situations where a balance between affordability, versatility, and good overall properties is desired. Here are some ideal scenarios:
- Prototyping: Its cost-effectiveness makes it a great choice for creating functional prototypes to test form, fit, and functionality.
- Lightweight components: From brackets and housings to consumer goods, Al 3003’s lightweight nature is a plus.
- Non-critical structural parts: For applications where extreme strength isn’t paramount, Al 3003 can provide a good balance of functionality and affordability.
- Applications requiring machinability: If post-processing and finishing are part of the plan, Al 3003’s machinability makes it a suitable option.
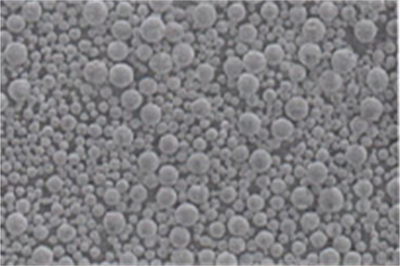
FAQ
Question | Answer |
---|---|
What is the shelf life of Al 3003 powder? | With proper storage in sealed containers under dry conditions, Al 3003 powder can maintain its properties for up to a year. However, it’s always recommended to consult the manufacturer’s specific storage recommendations. |
Can Al 3003 powder be recycled? | Yes! Aluminum is a highly recyclable material, and Al 303 powder scrap can be collected and reprocessed for use in future MAM projects. |
Are there any safety hazards associated with Al 3003 powder? | As with any metal powder, Al 3003 can be a respiratory irritant. Proper ventilation and the use of personal protective equipment like respirators are crucial when handling the powder. |
How does Al 3003 powder compare to aluminum alloy ingots for traditional manufacturing? | MAM using Al 3003 powder offers several advantages. It allows for the creation of complex geometries that might be difficult or impossible with traditional machining from solid ingots. Additionally, MAM can reduce waste material and offer greater design freedom. |
What are the future prospects for Al 3003 powder? | As MAM technology continues to evolve, Al 3003 powder is expected to remain a popular choice due to its affordability and versatility. Advancements in powder production techniques might lead to even better flow characteristics and improved mechanical properties for printed parts. |
In Conclusion: Al 3003 Powder – A Reliable Workhorse for Metal Additive Manufacturing
Al 3003 powder has earned its reputation as a dependable material in the world of MAM. Its affordability, versatility, and good overall properties make it a go-to choice for a wide range of applications. As MAM technology continues to develop, Al 3003 powder is certain to remain a key player in shaping the future of metal manufacturing.