Al 3103 powder, a superhero in the world of metal additive manufacturing (MAM), might not have the flashiest name, but don’t let that fool you. This aluminum alloy powder boasts a unique blend of properties that make it a go-to choice for a wide range of applications. Imagine a material that’s strong, lightweight, corrosion-resistant, and easy to work with. That’s Al 3103 powder in a nutshell.
But before we dive into the nitty-gritty of this metal marvel, let’s take a step back. What exactly is metal additive manufacturing (MAM)? Picture this: Imagine building a three-dimensional object layer by layer, not by carving it out of a solid block, but by strategically adding material. That’s the magic of MAM. Al 3103 powder plays a starring role in this process, acting as the building block for creating complex and functional metal parts.
Understanding Al 3103 powder
Al 3103 powder belongs to the 3000 series of aluminum alloys, known for their excellent workability and formability. The key players in its composition are:
- Aluminum (Al): The main ingredient, forming the foundation of the material.
- Manganese (Mn): This element boosts strength and helps resist corrosion.
- Magnesium (Mg): Magnesium contributes to workability and weldability.
While these are the primary alloying elements, trace amounts of other elements like copper, iron, and silicon might also be present depending on the specific grade.
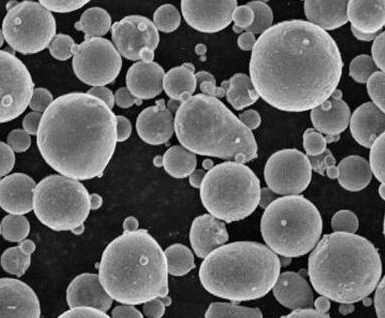
A Look at Different Metal Powders
The world of metal additive manufacturing offers a variety of powder choices, each with its own strengths and applications. Here’s a glimpse into some popular contenders alongside Al 3103 powder:
Metal Powder | Description | Applications |
---|---|---|
AlSi10Mg | A high-silicon content (around 10%) makes it excellent for casting applications due to its good fluidity and low crack sensitivity. | Automotive engine components, cylinder heads, pistons |
Al 6061 | A versatile option known for its good strength, weldability, and corrosion resistance. | Aerospace components, structural parts, electronic enclosures |
Al 7075 | This high-strength alloy offers outstanding mechanical properties but can be trickier to work with due to its lower weldability. | Aircraft parts, high-performance components, military applications |
Stainless Steel 316L | Offers excellent corrosion resistance, making it ideal for applications exposed to harsh environments. | Medical implants, chemical processing equipment, marine components |
Inconel 625 | A superalloy known for its exceptional high-temperature strength and resistance to oxidation and corrosion. | Gas turbine components, rocket engine parts, heat exchangers |
Titanium 6Al-4V (Ti64) | A biocompatible and high-strength option favored in the aerospace and medical industries. | Aerospace components, prosthetic limbs, dental implants |
Copper | Highly conductive, making it suitable for creating electrical components. | Heat sinks, electrical connectors, electrodes |
Nickel | Offers good corrosion resistance and can be used for electroplating or creating composite powders. | Electrical components, catalytic converters, additive manufacturing of functional surfaces |
Tool Steel | These alloy powders boast high hardness and wear resistance, making them ideal for creating molds and tools. | Cutting tools, dies, molds for plastic injection molding |
As you can see, each metal powder brings its own set of strengths and weaknesses to the table. The ideal choice depends on the specific needs of your application.
Properties and Characteristics of Al 3103 powder
Now, let’s delve deeper into what makes Al 3103 powder such a valuable player in the MAM arena. Here are some key characteristics that set it apart:
- Excellent Workability: Al 3044 powder boasts impressive formability, allowing for the creation of complex geometries with minimal issues.
- Good Strength: While not the strongest metal powder around, Al 3004 offers sufficient strength for a wide range of applications.
- Superior Corrosion Resistance: The presence of manganese enhances its resistance to corrosion, making it suitable for various environments.
- Weldability: (Continued) As mentioned earlier, Al 3103 powder can be readily welded, allowing for the creation of larger and more complex structures by joining multiple printed parts. This weldability makes it a versatile option for projects requiring intricate designs.
- Favorable Processing Characteristics: Al 3103 powder exhibits good flowability, meaning it moves smoothly within the MAM system, ensuring consistent and reliable printing. This characteristic minimizes printing defects and contributes to overall production efficiency.
- Cost-Effectiveness: Compared to some other metal powders, Al 3004 is a relatively affordable option. This cost advantage makes it an attractive choice for projects where budget is a major consideration.
The Applications of Al 3103 powder
With its well-rounded set of properties, Al 3103 powder finds application in a diverse range of industries. Here are some prominent examples:
- Automotive Industry: Al 3103 powder is used to create lightweight and corrosion-resistant components for automobiles, such as brackets, housings, and even some engine parts. Its workability allows for the production of complex shapes that can optimize vehicle performance.
- Aerospace Industry: While not the first choice for high-stress aircraft components, Al 3103 powder can be used to manufacture non-critical parts like interior panels, housings for electronics, and even certain drone components. Its affordability and good strength-to-weight ratio make it a suitable option for these applications.
- Consumer Goods: From camera housings to sporting good components, Al 3103 powder is finding its way into various consumer products. Its formability allows for the creation of intricate designs, while its corrosion resistance ensures these products can withstand everyday wear and tear.
- Medical Industry: Al 3103 powder shows promise in the creation of certain medical devices that don’t require exceptionally high strength. For instance, it can be used to manufacture prosthetic limbs components or housings for medical equipment. Here, biocompatibility and corrosion resistance are crucial factors, and Al 3103 powder delivers on both these aspects.
Al 3103 powder: Specifications, Sizes, and Grades
When it comes to selecting Al 3103 powder for your MAM project, several factors need consideration. Here’s a breakdown of key specifications:
- Particle Size Distribution: The size and distribution of the powder particles significantly impact the quality of the printed parts. Al 3103 powder typically comes in a range of particle sizes, from 15-45 micrometers, ensuring good flowability and minimal porosity in the final product.
- Powder Grades: Different grades of Al 3103 powder might contain slight variations in their chemical composition, tailored for specific applications. For instance, some grades might have tighter control over specific element concentrations to optimize certain properties.
- Standards: Reputable manufacturers ensure their Al 3103 powder adheres to industry standards, such as ASTM International (ASTM) or Aerospace Material Specifications (AMS). Meeting these standards guarantees consistent quality and reliable performance.
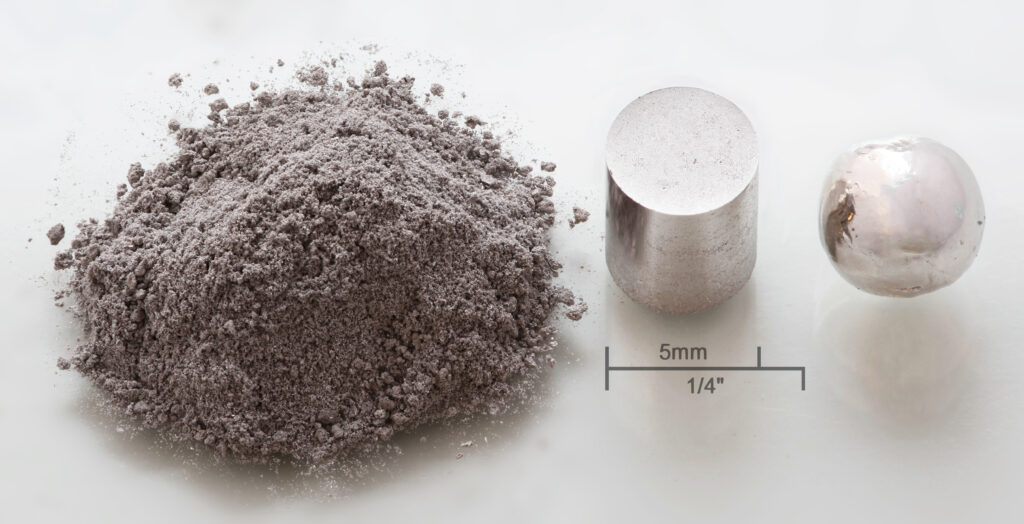
Suppliers and Pricing of Al 3103 powder
Several reputable suppliers offer Al 3103 powder for metal additive manufacturing applications. Pricing can vary depending on factors like:
- Quantity: Generally, larger quantities attract lower prices per unit weight.
- Particle size distribution: Powders with tighter particle size control might command a premium.
- Powder grade: High-purity or specialized grades might be more expensive.
Pros and Cons of Al 3103 powder
While Al 3103 powder boasts numerous advantages, it’s essential to consider its limitations as well. Here’s a balanced view:
Pros
- Excellent workability: Allows for the creation of complex geometries.
- Good strength: Sufficient for various applications.
- Superior corrosion resistance: Suitable for diverse environments.
- Weldability: Enables creation of larger structures.
- Favorable processing characteristics: Good flowability ensures consistent printing.
- Cost-effective: A relatively affordable metal powder option.
Cons
- Not the strongest metal powder: For high-stress applications, other options might be better suited.
- Lower melting point compared to some alloys: May not be ideal for extremely high-temperature environments.
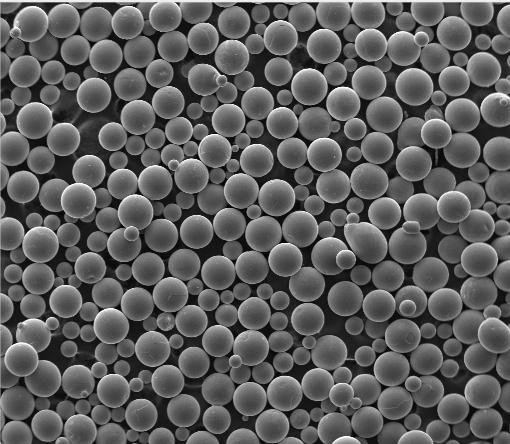
FAQ
Q: How does Al 3103 powder compare to Al 6061 powder?
Both Al 3004 and Al 6061 are popular aluminum alloy powders used in metal additive manufacturing. Here’s a breakdown of their key differences:
- Strength: Al 6061 offers superior strength compared to Al 3004. This makes it a better choice for applications requiring high structural integrity, such as aerospace components or load-bearing parts.
- Weldability: Both powders offer good weldability, allowing for the creation of larger and more complex structures. However, Al 6061 might require more specific welding techniques due to its higher magnesium content.
- Corrosion Resistance: Al 3004 exhibits slightly better corrosion resistance due to the presence of manganese. This makes it a preferable option for applications exposed to harsh environments or saltwater.
- Workability: Al 3004 reigns supreme in terms of workability. Its excellent formability allows for the creation of intricate designs that might be more challenging with Al 6061.
- Cost: Al 3004 is generally more affordable than Al 6061. This cost advantage can be a significant factor for projects with budget constraints.
In essence, the choice between Al 3004 and Al 6061 depends on your specific priorities. If superior strength is paramount, Al 6061 is the way to go. However, if excellent workability, good corrosion resistance, and cost-effectiveness are your primary concerns, then Al 3004 might be the better fit.
Q: Is Al 3103 powder safe to use?
Al 3103 powder itself is not inherently dangerous. However, as with any metal powder, certain safety precautions are crucial during handling and storage:
- Inhalation: Avoid inhaling the powder, as it can irritate the lungs. Wear a proper respirator when working with Al 3103 powder.
- Skin contact: Minimize skin contact with the powder to prevent irritation. Wear gloves and protective clothing when handling it.
- Fire hazards: Aluminum powder can be flammable under certain conditions. Store it away from heat sources and ignition points.
- Proper disposal: Al 3103 powder should not be disposed of in regular trash. Follow recommended guidelines for metal powder disposal to minimize environmental impact.
Q: What are some future trends for Al 3103 powder?
The future of Al 3103 powder looks promising. Here are some potential trends to watch:
- Development of even finer powder grades: This could lead to even more intricate and detailed parts being manufactured using Al 3004.
- Exploration of new applications: As metal additive manufacturing technology continues to evolve, Al 3103 powder might find its way into novel applications across various industries.
- Focus on sustainability: Manufacturers might explore greener methods for producing Al 3103 powder, minimizing its environmental footprint.
In conclusion, Al 3103 powder stands as a versatile and valuable player in the metal additive manufacturing world. Its well-rounded properties, affordability, and ease of use make it a compelling choice for a broad spectrum of applications. As technology progresses and new possibilities emerge, Al 3103 powder is certain to continue playing a vital role in shaping the future of metal additive manufacturing.