Aluminum 6061 is one of the most versatile and widely used aluminum alloys. Al 6061 powder offers unique properties that make it suitable for diverse applications across many industries. This guide provides a detailed overview of Al 6061 powder, its key characteristics, processing methods, applications, suppliers, costs, installation, operation and maintenance.
Overview of Al 6061 Powder
Al 6061 is an aluminum alloy with magnesium and silicon as its major alloying elements. It is one of the most common alloys in the 6000 series. Here are the key details about Al 6061 powder:
- Composition: 1.0% Mg, 0.6% Si, 0.28% Cu, 0.2% Cr
- Excellent corrosion resistance and high strength-to-weight ratio
- Medium to high strength alloy with T4 and T6 tempers possible
- Good weldability and machinability compared to other aluminum alloys
- Melting point around 582°C
- Widely available in various forms including powder
- Al 6061 powder particle sizes range from 10-150 microns
- Spherical powder morphology allows excellent flowability
- Used for additive manufacturing, metal injection molding, and other powder metallurgy processes
Table 1: Overview of Key Properties of Al 6061 Powder
Properties | Details |
---|---|
Composition | 1.0% Mg, 0.6% Si, 0.28% Cu, 0.2% Cr |
Density | 2.7 g/cm3 |
Melting Point | Around 582°C |
Strength | Medium to high strength depending on temper |
Corrosion Resistance | Excellent due to protective oxide layer |
thermal conductivity | 167 W/m-K |
Electrical conductivity | 41% IACS |
Powder particle size range | 10-150 microns |
Powder morphology | Spherical |
Flowability | Excellent due to spherical shape |
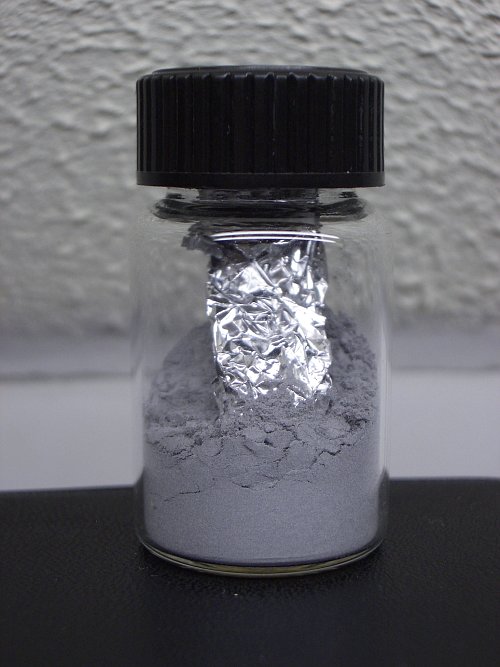
Applications and Uses of Al 6061 Powder
The combination of good mechanical properties, excellent corrosion resistance, machinability, and weldability make Al 6061 suitable for a wide range of applications. Here are some of the major uses of Al 6061 powder:
Table 2: Major Applications and Uses of Al 6061 Powder
Applications | Details |
---|---|
Additive manufacturing | Used in selective laser sintering, direct metal laser sintering, binder jetting |
Metal Injection Molding (MIM) | Highly suitable for MIM due to excellent flowability |
Welding wires and rods | Used to make Al 6061 filler metals |
Automotive parts | Engine blocks, wheels, frames, cylinders |
Aerospace components | Fuselage structures, aircraft fittings, wings |
Marine components | Hulls, masts, superstructures |
Construction and building | Doors, windows, locks, handles |
Heat exchangers and heat sinks | For electronic cooling and HVAC systems |
Bicycle frames | Lightweight alternative to steel or titanium |
The automotive sector utilizes Al 6061 extensively due to its high strength-to-weight ratio. The aerospace industry relies on Al 6061 for lightweight structural components. Additive manufacturing has opened up new possibilities for using Al 6061 powder in innovative part designs.
Specifications and Standards for Al 6061 Powder
Al 6061 powder products need to meet certain specifications outlined by various standards organizations. The key standards are:
Table 3: Specifications and Standards for Al 6061 Powder
Standard | Organization | Specification |
---|---|---|
ASTM B221 | ASTM International | Standard specification for aluminum and aluminum alloy extruded bars, rods, wires, profiles, and tubes |
AMS 4150 | SAE International | Details chemical composition limits of Al 6061 |
ISO 209:2007 | ISO | Specifies requirements for chemical composition of wrought Al-Mg-Si alloys |
DIN 1725-2 | DIN | German national standard for Al Mg1SiCu aluminium alloy profiles |
The ASTM B221 and related standards provide the acceptable chemical composition ranges, mechanical properties like tensile strength and hardness for various tempers, sampling procedures, inspection criteria, etc. for Al 6061 products including powder.
Manufacturers must certify their Al 6061 powder materials meet the required chemistry and property limits as per the applicable standard. Customers should review the mill certificates to ensure compliance.
Al 6061 Powder Properties
The unique combination of properties of Al 6061 powder stems from its alloy composition and processing methods. Here are some of the key powder characteristics:
Table 4: Properties of Al 6061 Powder
Property | Details |
---|---|
Particle size distribution | Typically 10-150 microns |
Morphology | Spherical powder shape |
Flow rate | >25 s/50 g, indicating excellent flowability |
Apparent density | Around 2.0 g/cc |
Tap density | Approximately 2.7 g/cc |
Residual oxygen content | <0.6% |
Residual moisture content | <0.2% |
The small particle size range, along with the spherical morphology, provides superior flow characteristics. This allows efficient processing through powder handling systems and dosing equipment with minimal hang-ups.
The tap density of Al 6061 powder approaches the theoretical density of solid Al 6061 alloy. This indicates high packing density and suitability for additive manufacturing and MIM.
Low residual oxygen and moisture content are essential for avoiding powder contamination and porosity in finished parts. Reputable suppliers control these impurity levels through high quality gas atomization and protective storage/handling.
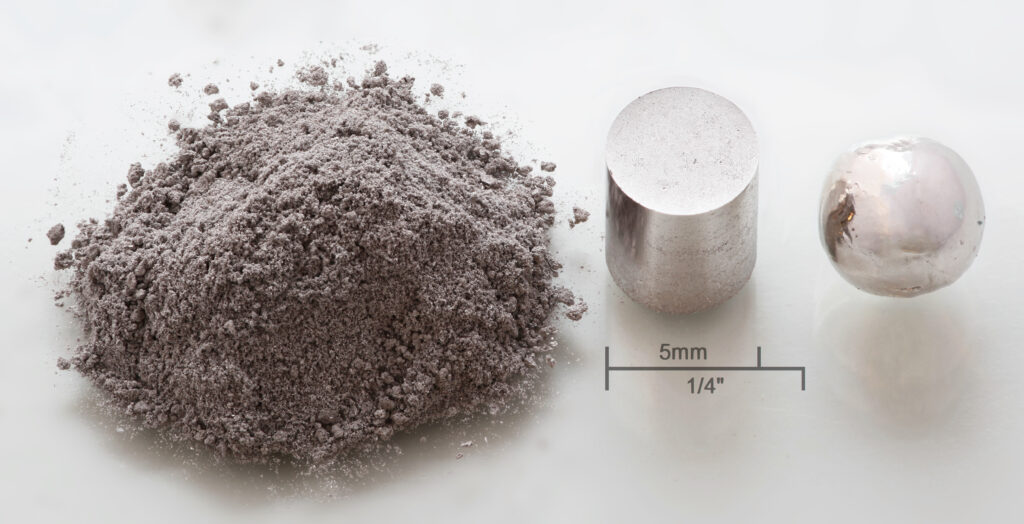
Production Methods for Al 6061 Powder
Al 6061 powder is mainly produced through the following methods:
Table 5: Key Production Methods for Al 6061 Powder
Method | Details |
---|---|
Gas atomization | High pressure inert gas disintegrates molten alloy stream into fine droplets that solidify into powder |
Plasma rotating electrode process (PREP) | Electrode rotation and plasma arc used to generate molten droplets flung off into powder |
Mechanical alloying | Ball milling of elemental/master alloy powders to synthesize Al 6061 alloy powder |
Gas atomization is the most common method allowing high purity, spherical powder ideal for AM and MIM. Mechanical alloying provides an alternative powder production route but can result in some contamination.
Atomization and PREP methods allow close control of powder chemistry, particle size distribution, morphology, oxygen pickup and other properties critical for high performance parts.
Al 6061 Powder Suppliers
There are several reputable suppliers that manufacture and distribute Al 6061 powder worldwide. Here are some of the major suppliers:
Table 6: Key Suppliers for Al 6061 Powder
Supplier | Location |
---|---|
Sandvik | Sweden |
Carpenter Additive | United States |
AP&C | Canada |
Praxair | United States |
Metal Powder Company | United States |
Makin Metal Powders | United Kingdom |
SCM Metal Products | United States |
These companies supply Al 6061 powder made through atomization as well as PREP techniques with precise control of chemistry, particle size distribution, morphology, density and other parameters.
High purity inert gas atomization by suppliers like AP&C and Praxair result in superior quality spherical Al 6061 powder ideal for critical applications. Custom alloys and particle size distributions are available.
Cost Analysis for Al 6061 Powder
Al 6061 powder can range in price from $5/kg to $150/kg depending on quality, particle size, order volume and other factors. Here are some typical price ranges:
Table 7: Cost Analysis for Al 6061 Powder
Particle Size | Price Range |
---|---|
10-50 microns | $20-100/kg |
15-45 microns | $15-75/kg |
45-150 microns | $5-25/kg |
Sub-micron powder | $100-150/kg |
Generally, smaller particle size distribution commands higher pricing due to increased production costs. High purity inert gas atomized powder with superior morphology and chemistry is more expensive than simple mechanical atomization.
Bulk orders above 1000 kg can negotiate discounts around 20% off regular pricing. Custom alloys tailored to specific applications can cost 20-50% more than standard Al 6061 compositions.
Installation and Operation of Al 6061 Powder-based Equipment
Working with Al 6061 powder requires proper installation and operation of powder handling systems and additive manufacturing equipment. Here are some key considerations:
Table 8: Installation and Operation Guidelines for Al 6061 Powder
Process | Installation and Operation Guidelines |
---|---|
Storage and handling | Store powder in sealed containers under inert gas, limited moisture exposure. Use gloves, respirators to avoid contact or inhalation. Have spill cleanup protocol. |
Blending/mixing | Ensure uniform blending if using powder blends. Check composition sampling. |
Dosing | Calibrate feeder equipment regularly. Control feed rate, verify activation. Check for clogs, bridging. |
Build chamber | Monitor oxygen levels below 100ppm for AM. Have purge cycles between builds. |
Post-processing | Use appropriate tools for powder removal – brushes, air blowers. Avoid direct contact. |
System maintenance | Schedule regular upkeep for powder handling and AM equipment per manufacturer. Proper cleaning between alloy changeover. |
Careful installation, calibration, operation, and maintenance of all powder equipment is essential for consistent, high quality results from Al 6061 powder. Proper training of personnel is also critical.
Maintenance of Al 6061 Powder-based Parts and Equipment
Regular maintenance is necessary for equipment and components using Al 6061 powder to ensure optimal performance. Here are some key maintenance guidelines:
Table 9: Maintenance Guidelines for Al 6061 Powder-based Components
Component | Maintenance Action | Frequency |
---|---|---|
Storage containers | Inspect for cracks, leaks. Replace damaged containers immediately. | Monthly |
Mixing/blending equipment | Check mixer barrel, blades for wear. Replace as needed. | 500 hours |
Feeder and dosing system | Inspect feed path for clogs and obstructions. Check actuator function. | 100 hours |
Additive manufacturing system | Clean build chamber. Inspect key modules – laser, optics, powder bed, recoater. | 500 hours |
Fabricated parts | Visual inspection for damage or wear. Schedule replacement as per application. | Ongoing |
Preventative maintenance schedules for storage containers, powder handling equipment, AM machines should be established and followed rigorously. This helps avoid costly downtime or loss of material.
In-service parts made using Al 6061 powder should also undergo scheduled inspections, cleaning, repair and replacement as dictated by the application.
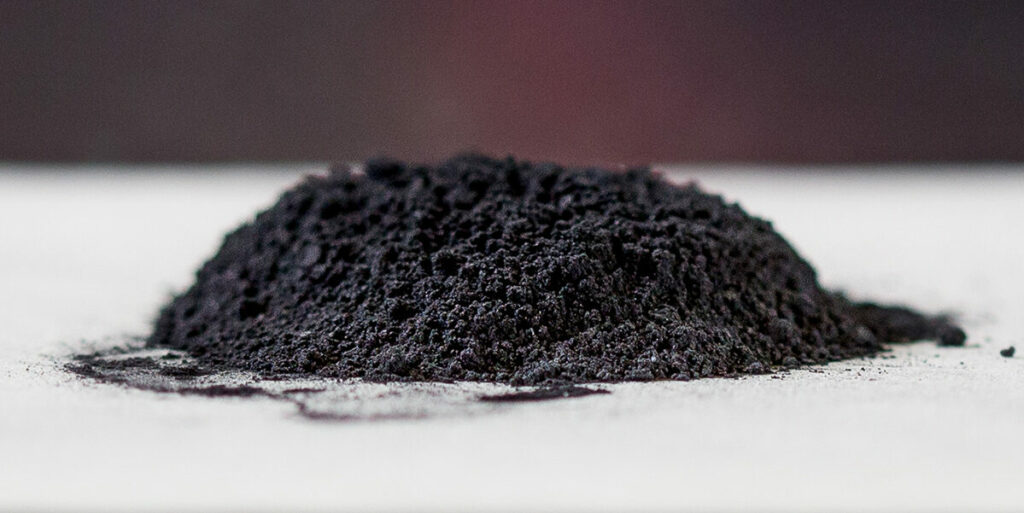
How to Select an Al 6061 Powder Supplier
Choosing a suitable Al 6061 powder supplier is critical for obtaining high quality powder. Here are key considerations for selection:
Table 10: Selection Criteria for Al 6061 Powder Supplier
Parameter | Guidelines |
---|---|
Production method | Prefer inert gas atomization for highest quality |
Production capacity | Match supplier output to application demand volume |
Powder quality | Chemistry, particle size, morphology, purity must meet specifications |
Certifications | ISO 9001, ISO 13485 – verify technical competence |
Testing capability | Supplier should test chemistry, powder properties for each batch |
Customer support | Technical expertise to assist with application development |
Delivery | On-time delivery of orders as per schedule |
Business stability | Established suppliers with solid financial position |
Cost | Balance cost vs performance based on application needs |
Review multiple suppliers based on the parameters above. Get powder samples for evaluation if possible. Start with small trial orders to verify supplier performance before large contracts.
Pros and Cons of Al 6061 Powder
Like any material, Al 6061 powder has both advantages and limitations to consider:
Table 11: Pros and Cons of Al 6061 Powder
Pros | Cons |
---|---|
High strength-to-weight ratio | Lower strength than steel, titanium alloys |
Excellent corrosion resistance | Susceptible to galvanic corrosion if contact dissimilar metals |
Good machinability and ductility | Not suitable for high temperature applications |
Cost-effective compared to titanium, nickel alloys | Powder production challenges compared to pure aluminum |
Widely available, established supply chain | High coefficient of thermal expansion |
Proven performance in aerospace, automotive | Needs surface protection in some usages |
Al 6061 provides a versatile combination of moderate strength, weldability, formability and corrosion resistance at relatively low cost. Limitations like lower strength or thermal expansion issues can be mitigated through design adjustments.
Applications Comparison Between Al 6061, Stainless Steel, and Titanium Powders
Al 6061 powder provides unique benefits but how does it compare against stainless steel and titanium powders for major applications?
Table 12: Comparison of Al 6061, Stainless Steel and Titanium Powders
Parameter | Al 6061 | Stainless Steel | Titanium |
---|---|---|---|
Strength | Medium | Higher | Highest |
Cost | Low | Moderate | High |
Corrosion resistance | Excellent | Good | Excellent |
Thermal conductivity | Good | Lower | Lowest |
Density | Low | Higher | High |
Processability | Excellent | Moderate | Fair |
Aerospace structural use | High | Limited | High |
Automotive components | High | Medium | Low |
Medical implants | Medium | High | Highest |
Food/chemical contact | High | High | Limited |
For applications like aerospace structures and automotive parts, Al 6061 offers the best balance of strength, lightweight, corrosion resistance and cost. For implants requiring strength and biocompatibility, titanium prevails despite higher cost. Stainless steel occupies a middle ground with moderate cost and corrosion resistance.
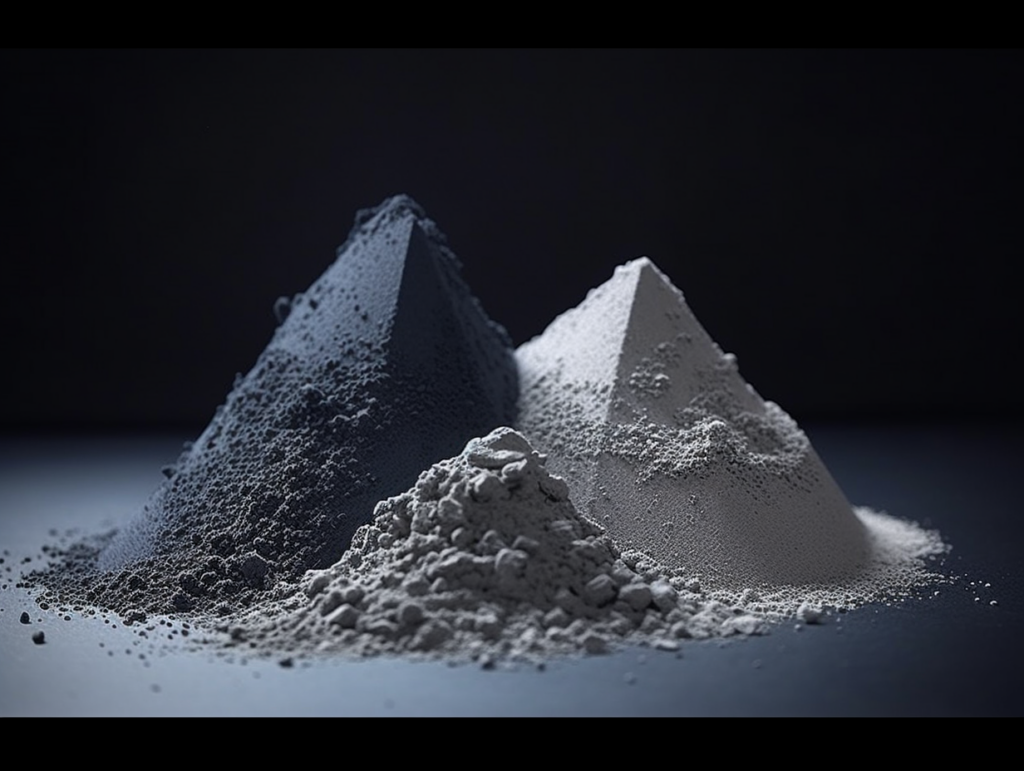
FAQ
Q: What are the common tempers available for Al 6061 powder?
A: The most common tempers for Al 6061 powder are T4 (solution heat treated and naturally aged to slight hardening) and T6 (solution heat treated and artificially aged to peak hardening). T0 (fully annealed) and T651 are also used sometimes.
Q: Does Al 6061 powder require special handling compared to other aluminum alloys?
A: No, the handling, storage and safety precautions for Al 6061 powder are similar to other common aluminum alloy powders like AlSi10Mg and AlSi7Mg. Moisture control and oxidation prevention are critical as with any aluminum powder.
Q: What particle size range of Al 6061 powder is typical for metal injection molding?
A: For MIM applications, the Al 6061 powder particle size range is usually 10-45 microns. This allows high powder loading in the feedstock and good flow in molding. Larger particles around 40-45 microns improve powder flow performance.
Q: What are some recommended post-processing steps for Al 6061 AM parts?
A: Typical post-processing includes support removal, bead blasting, surface grinding/machining, T6 heat treatment, anodizing, passivation, powder coating, etc. This improves surface finish, achieves required mechanical properties, and provides corrosion protection.
Q: Is Al 6061 powder compatible with direct metal laser sintering processes?
A: Yes, Al 6061 is highly compatible with DMLS AM systems and offers easier processing compared to higher strength aluminum alloys like AlSi10Mg or Al 7075. The medium strength of Al 6061 is sufficient for many applications.
Q: What is the typical chemical composition of Al 6061 T6 powder?
A: The chemical composition limits per AMS 4150 for Al 6061 T6 powder are 0.8-1.2% Mg, 0.4-0.8% Si, 0.15-0.4% Cu, 0.04-0.35% Cr, max 0.7% Fe, max 0.15% Mn, remainder Aluminum.
Q: Does Al 6061 powder require special equipment or tools compared to steel powder?
A: Generally no, standard metal powder handling equipment and AM machines can process Al 6061 powder. Some adjustments like argon atmosphere vs nitrogen may be needed. Feeding parameters may require optimization due to differences in density/flow.
Q: What are some alternatives to Al 6061 powder for cost-sensitive applications?
A: For moderate strength needs where cost is critical, options like Al 1100, Al 3003, and Al 6063 can be considered. Composition adjustments to reduce alloying additions like silicon, magnesium and copper can lower Al 6061 powder cost.
Q: What type of shielding gas is recommended for laser welding Al 6061 powder deposits?
A: 100% argon is the most suitable shielding gas for welding Al 6061 parts made via DMLS or other powder-based AM processes. Helium or helium rich mixtures can also work but are more expensive. Nitrogen promotes porosity in aluminum welds.
Q: Does Al 6061 powder have minimum order quantity requirements from suppliers?
A: Many major Al 6061 suppliers will accommodate orders as low as 25-50kg. However, ideal order sizes are 200-500kg for reasonable pricing. Small lab trial orders under 10kg are possible but quite expensive on a per kilogram basis.
In summary, Al 6061 powder offers an optimal balance of properties like medium strength, excellent corrosion resistance, good weldability and machinability at relatively low cost. With innovations in powder production and additive manufacturing, Al 6061 continues finding expanded applications across aerospace, automotive, medical and other demanding industries.