Al 7075 powder, also known as Aluminum 7075 alloy powder, is a revolutionary material rapidly transforming the landscape of additive manufacturing (3D printing) and various industrial applications. But what exactly is this wonder material, and why is it causing such a stir? Buckle up, because we’re diving deep into the world of Al 7075 powder, exploring its production methods, applications, unique properties, and the exciting possibilities it holds for the future.
Production Method of Al 7075 Powder
Imagine taking a superhero like Iron Man and shrinking him down to a microscopic level. That’s kind of what happens to bulk Al 7075 alloy, a popular high-strength aluminum alloy, when it’s transformed into Al 7075 powder. There are two primary methods for achieving this feat:
- Atomization: Picture a molten pot of Al 7075 alloy. In atomization, an inert gas like nitrogen or argon is blasted at the liquid metal, breaking it into tiny droplets that rapidly solidify into spherical particles. Think of it like a superpowered water sprayer creating a mist of metal droplets instead of water!
- Milling: This method involves taking pre-existing Al 7075 flakes or chips and grinding them down into a fine powder using high-energy mills. It’s like pulverizing a rock into dust, but with much more sophisticated machinery and precise control over the final particle size.
The chosen method significantly impacts the characteristics of the resulting Al 7075 powder. Atomization typically produces finer, more spherical particles with excellent flow properties, making them ideal for 3D printing applications. Milling, on the other hand, can result in slightly larger and more irregularly shaped particles, but it’s often a more cost-effective option for some industrial uses.
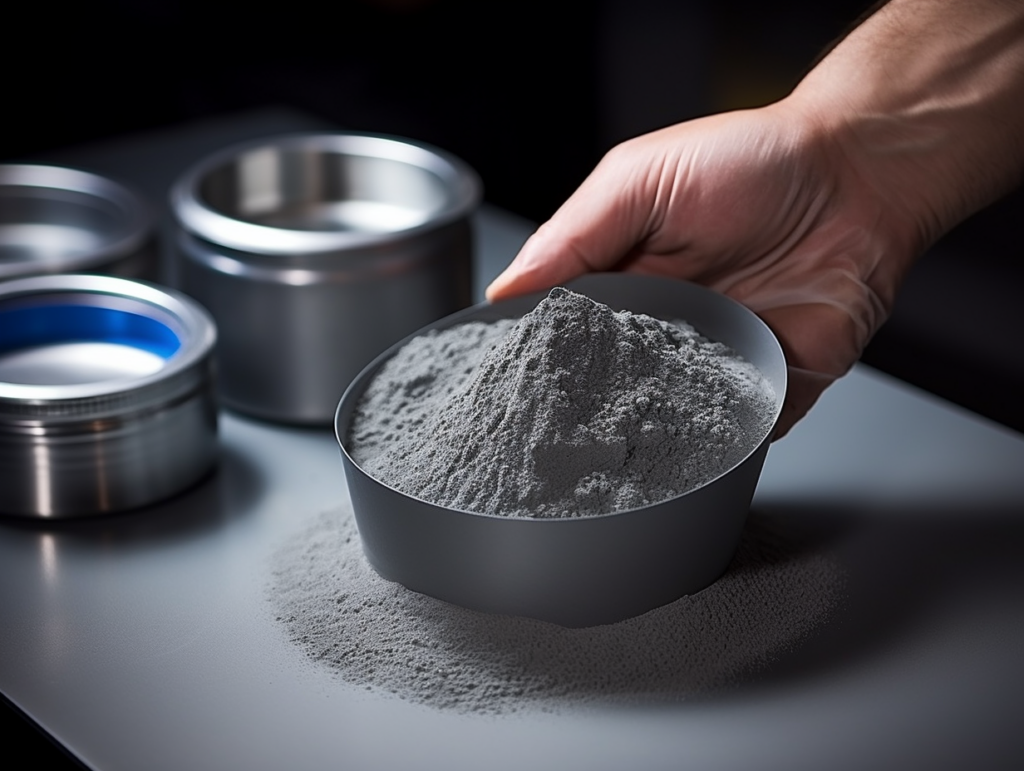
the Superpowers of Al 7075 Powder
Al 7075 powder isn’t just any metal dust; it boasts a unique combination of properties that make it a game-changer in various fields. Here’s a breakdown of its key strengths:
- High Strength: Remember why Iron Man uses such a tough material for his suit? Al 7075 powder inherits the exceptional strength of its bulk counterpart. This makes it perfect for creating lightweight yet incredibly strong components in aerospace, automotive, and other demanding applications.
- Excellent Machinability: Just because it’s strong doesn’t mean it’s difficult to work with. Al 7075 powder retains good machinability, allowing for precise post-processing and finishing of 3D printed parts. Imagine crafting intricate metal objects with relative ease!
- Corrosion Resistance: Al 7075 powder offers decent resistance to corrosion, making it suitable for applications where exposure to harsh environments is a concern. It’s not invincible, but it definitely holds its own compared to other metal powders.
- Lightweight: This is where the magic happens. Despite its strength, Al 70 powder boasts a lightweight nature, a crucial factor in applications like aerospace and transportation where every gram counts. Think of creating high-performance parts that won’t weigh down your project!
However, it’s important to acknowledge that Al 7075 powder also has some limitations:
- Higher Cost: Compared to some other metal powders, Al 7075 can be a bit more expensive. This is due to the complex production process and the inherent value of the alloy itself.
- Susceptibility to Hydrogen Embrittlement: Under specific conditions, Al 7075 can become brittle due to the presence of hydrogen. Careful post-processing techniques are needed to mitigate this risk.
Despite these limitations, the advantages of Al 7075 powder far outweigh the drawbacks for many applications.
Applications of Al 7075 Powder
Al 7075 powder is no longer confined to science fiction. It’s actively transforming various industries, with its applications growing rapidly. Here are some of the most exciting areas where this wonder powder is making its mark:
- Additive Manufacturing (3D Printing): This is arguably the most significant application of Al 7075 powder. Its combination of strength, machinability, and flowability makes it perfect for creating complex, high-performance parts through 3D printing. Imagine printing lightweight yet robust components for everything from aircraft to prosthetics!
- Aerospace: The weight-saving potential of Al 7075 powder is a dream come true for the aerospace industry. It’s being used to create stronger, lighter aircraft parts, leading to increased fuel efficiency and improved overall performance.
- Automotive: Not to be outdone by aerospace, the automotive industry is also embracing Al 7075 powder. It’s being used to manufacture lightweight yet durable components like wheels, suspension parts, and even engine blocks. This translates to better fuel economy, increased performance, and potentially even a sportier aesthetic for cars!
- Defense: The military is always looking for stronger, lighter materials to create advanced weaponry and protective gear. Al 7075 powder is being explored for applications like gun components, armor plating, and even components for drones and other unmanned aerial vehicles (UAVs).
- Medical and Dental: The biocompatible nature of certain variants of Al 7075 powder opens doors in the medical and dental fields. Imagine creating custom-made implants or prosthetics with excellent strength and weight characteristics, tailored to each patient’s specific needs!
- Consumer Goods: The potential applications of Al 7075 powder even extend to consumer goods. Think of high-end bicycles, sporting equipment, or even custom-designed phone cases made with this robust and lightweight material. The possibilities are truly endless!
It’s important to note that this is not an exhaustive list. As research and development continue, we can expect to see Al 7075 powder find its way into even more innovative applications across various industries.
Details of Al 7075 Powder Composition and Chemistry
So, what exactly makes Al 7075 powder tick? Let’s delve a little deeper into its composition and the science behind its properties. Here’s a breakdown of the key elements that contribute to its unique character:
- Aluminum (Al): As the name suggests, aluminum is the primary component, forming the base of the alloy. It provides the lightweight foundation and contributes to the material’s formability.
- Zinc (Zn): This element is the secret ingredient that unlocks the high strength of Al 7075. Zinc reacts with aluminum to form intermetallic compounds that significantly enhance the strength of the material. Imagine adding a special sauce to aluminum that makes it super strong!
- Magnesium (Mg): Magnesium plays a supporting role, contributing to the overall strength and corrosion resistance of the alloy. It’s like the reliable sidekick that helps zinc do its job effectively.
- Copper (Cu): A small amount of copper is often added to further enhance the strength of Al 7075. However, too much copper can have negative effects on corrosion resistance. It’s a delicate balancing act!
- Other trace elements: Depending on the specific application and desired properties, minute amounts of other elements like silicon or chromium might be added to the mix. These trace elements are like spices that can fine-tune the overall characteristics of the final product.
The exact proportions of these elements can vary slightly depending on the manufacturer and the desired properties of the final Al 7075 powder. Understanding this underlying chemistry is crucial for optimizing the production process and tailoring the powder for specific applications.
Al 7075 Powder vs. Other Metal Powders
Al 7075 powder isn’t the only player in the metal powder game. There are other options available, each with its own strengths and weaknesses. Here’s a comparison of Al 7075 powder with some of its most common competitors:
- Stainless Steel Powders: These powders offer excellent corrosion resistance but are generally denser and less strong than Al 7075. They’re a good choice for applications where corrosion resistance is paramount, even if some weight compromise is acceptable.
- Titanium Powders: Known for their exceptional strength-to-weight ratio, titanium powders are the ultimate lightweight champions. However, they are significantly more expensive than Al 7075 and require specialized printing techniques due to their higher melting point. Imagine a super strong and light material, but with a super high price tag!
- Nickel-based Alloy Powders: These powders offer incredible heat resistance, making them ideal for high-temperature applications like jet engines. However, they are even more expensive than titanium powders and can be challenging to work with. Think of a material that can withstand scorching temperatures, but be prepared to pay a hefty price!
The choice between Al 7075 powder and other options depends on the specific needs of the application. When a good balance of strength, weight, cost, and printability is required, Al 7075 powder often emerges as a compelling choice.
The Future of Al 7075 Powder
Here are some of the trends that are likely to shape the future of Al 7075 powder:
- Advancements in Powder Production: As research and development continue, we can expect to see even more efficient and cost-effective methods for producing Al 7075 powder. This will make it a more accessible material for a wider range of applications. Imagine a future where Al 7075 powder becomes as commonplace as other metal powders, opening doors for even more innovation!
- Improved Material Properties: Scientists are constantly working on improving the properties of Al 7075 powder. This could involve further enhancing its strength, reducing its susceptibility to hydrogen embrittlement, or even developing new variants with specialized functionalities. Imagine a future where Al 7075 powder boasts even better strength-to-weight ratios, increased corrosion resistance, or even unique properties like self-lubrication!
- Integration with Advanced Printing Technologies: The evolution of 3D printing technologies will go hand-in-hand with the development of Al 7075 powder. As printing techniques become more sophisticated and precise, Al 7075 powder will be optimized to take full advantage of these advancements. Imagine a future where 3D printers can create intricate and highly functional parts from Al 7075 powder with unparalleled precision and speed!
- Environmental Considerations: Sustainability is a growing concern in all industries, and the production of metal powders is no exception. We can expect to see a push towards more eco-friendly methods for producing Al 7075 powder, potentially involving recycled materials or energy-efficient processes. Imagine a future where Al 7075 powder production boasts a smaller environmental footprint, making it an even more attractive choice for environmentally conscious manufacturers!
Overall, the future of Al 7075 powder is bright. With ongoing advancements in production, material properties, printing technologies, and sustainability, this wonder material has the potential to revolutionize various industries and create a future filled with lighter, stronger, and more innovative products.
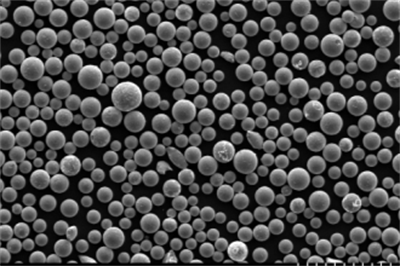
FAQ
Here are some frequently asked questions (FAQs) about Al 7075 powder:
Question | Answer |
---|---|
What is Al 7075 powder made of? | Al 7075 powder is primarily composed of aluminum (Al) with key elements like zinc (Zn) and magnesium (Mg) added for strength and corrosion resistance. Small amounts of copper (Cu) and other trace elements might also be present. |
Is Al 7075 powder safe? | In its raw powder form, Al 7075 powder can be an irritant if inhaled. However, once processed into a solid form through 3D printing or other techniques, it generally poses no safety risks. Always follow recommended safety precautions when handling metal powders. |
How much does Al 7075 powder cost? | The cost of Al 7075 powder can vary depending on the particle size, purity, and supplier. Generally, it is more expensive than some other metal powders but offers a good balance of cost and performance. |
What are some alternatives to Al 7075 powder? | Stainless steel powders offer better corrosion resistance, titanium powders boast exceptional strength-to-weight ratios, and nickel-based alloy powders excel in high-temperature applications. The choice depends on the specific needs of the project. |
What are the environmental impacts of Al 7075 powder production? | The production process can have some environmental impact. However, research is ongoing to develop more sustainable methods using recycled materials and energy-efficient processes. |
This FAQ section provides a quick overview of some key questions users might have about Al 7075 powder. By incorporating a table format, it allows for easy scanning and information retrieval, making the content more user-friendly.
I hope this comprehensive exploration of Al 7075 powder has been informative and engaging. With its unique combination of properties and vast potential applications, this wonder material is poised to play a significant role in shaping the future of manufacturing and beyond.