Overview
Al 7075 is an aluminum alloy that contains zinc as its primary alloying element. It is widely used in applications that require high strength-to-weight ratio, such as aircraft structures, gears and shafts, fasteners, missile parts, and marine fittings and structures.
Al 7075 powder is produced by gas atomization process. In this process, molten Al 7075 alloy is broken into fine droplets by high velocity inert gas. The droplets rapidly solidify into spherical powders. Al 7075 powder has wide applications in powder metallurgy, metal injection molding and additive manufacturing.
Some key properties of Al 7075 powder:
- High strength and hardness
- Lightweight
- Good corrosion resistance
- Excellent workability
- High thermal conductivity
- Non-magnetic
Al 7075 powder is available in various size ranges from 10 microns to 150 microns. The powder size distribution and morphology influences compactability, sinterability and performance of final part. Spherical powders with narrow size range offer optimal properties.
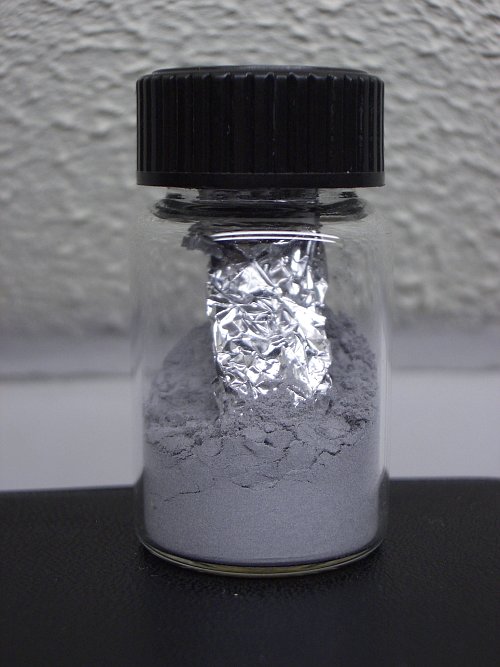
Types of Al 7075 Powder
Gas Atomized Al 7075 Powder
Gas atomized Al 7075 powder has spherical morphology and smooth surface. It exhibits excellent flowability and can be compacted to high densities. Gas atomization allows control over particle size distribution. Desired fractions can be sieved to obtain powder fractions suitable for specific applications.
Typical size range: 10 – 150 microns
Common size fractions:
- -150 +100 micron
- -100 +75 micron
- -75 +45 micron
- -45 +10 micron
Applications: Metal injection molding, additive manufacturing, powder metallurgy
Water Atomized Al 7075 Powder
Water atomized Al 7075 powder has irregular morphology with satellite structures. It has wider particle size distribution compared to gas atomized powder. The irregular structure results in lower flowability. But it has higher tap density which is suitable for press and sinter application.
Typical size range: 10 – 150 microns
Applications: Press and sinter powder metallurgy
Alloyed Al 7075 Powder
Alloyed Al 7075 powders have elemental additions like Scandium which enhance mechanical properties of final part. Scandium increases strength and hardness significantly.
Applications: High performance additive manufacturing, high strength P/M parts
Nanocrystalline Al 7075 Powder
Nanocrystalline Al 7075 powder has very fine grain size, typically less than 100 nm. The process control during inert gas atomization allows achieving nanocrystalline structure. The fine grains enhance mechanical properties through Hall-Petch relationship.
Typical size range: 10 – 45 microns
Applications: Additive manufacturing, sintering
Characteristics of Al 7075 Powder
Particle Size Distribution
- Narrow distribution improves powder flow and compactability
- Wide distribution suits press-and-sinter method
- Gas atomization gives narrow distribution
- Water atomization gives wide distribution
- Sieving classifies powder into desired fractions
Morphology
- Spherical morphology from gas atomization improves flow and packing
- Irregular morphology from water atomization reduces flow
Powder Flow
- Flowable powder required for uniform die filling in MIM and AM
- Hausner ratio indicates flowability
- Lower Hausner ratio = better flow
- Gas atomized powder has better flow
Apparent Density
- Density of powder mass indicating compactability
- Higher apparent density improves compactability
- Gas atomized = 2.7-3.1 g/cc
- Water atomized = 2.8-3.2 g/cc
Tap Density
- Packing density under tapping/vibration
- Higher tap density suitable for press-and-sinter method
- Gas atomized = 3.2-3.6 g/cc
- Water atomized = 3.5-3.8 g/cc
Applications and Uses of Al 7075 Powder
Metal Injection Molding (MIM)
MIM combines plastic injection molding method with powder metallurgy. Feedstock of metal powder and binder is injection molded and then sintered. Al 7075 MIM offers:
- High strength parts in complex shapes
- Near net shape capability
- Automated scalable production
- Low machining requirements
- Components with thin walls and hidden voids
Typical size fraction: -45 +10 μm
Applications: Aerospace components, automotive parts, consumer products
Additive Manufacturing
Al 7075 powder is processed using selective laser melting, electron beam melting and binder jetting additive manufacturing. Benefits are:
- Customized, complex geometries are possible
- Reduced weight by optimized design
- Elimination of assemblies by printed integrated parts
- Reduced lead time and tooling cost
Typical size fraction: 15-45 μm
Applications: Aerospace brackets, stiffeners, connectors, automotive, industrial
Powder Metallurgy
Al 7075 powder is compacted and sintered using conventional and microwave sintering. Advantages over wrought alloy:
- Isotropic properties from powder format
- Ability to alloy elements immiscible in ingot metallurgy
- Near net shape fabrication
Typical size fraction: -150 +45 μm
Applications: P/M connecting rods, gears, marine components
Thermal Spray Coatings
Al 7075 powder is deposited using flame spray, plasma spray, HVOF, cold spray etc. Benefits:
- Wear and corrosion protection
- Dimensional restoration of worn components
- Insulation and thermal barriers
Typical size fraction: -45 +15 μm
Applications: Repair and refurbishment of molds, turbine blades, bearings, shafts
Aluminum Matrix Composites
Al 7075 reinforced with ceramic particulates produces composites with very high strength and stiffness. Manufacturing methods are powder metallurgy, stir casting, squeeze casting etc.
Typical size fraction: -150 +45 μm
Applications: Aerospace and defense components, automotive parts, sporting goods
Explosive Welding
Al 7075 and other metals are joined by explosive bonding using thin sheet of Al 7075 powder between them. Cladding improves corrosion resistance.
Typical size fraction: -325 mesh
Applications: Bimetal sheets of Al-steel, Al-Cu, Al-Ti etc.
Specifications and Standards of Al 7075 Powder
Size range: 10 μm to 150 μm
Morphology: Spherical, granular, irregular shape
Apparent density: 2.7-3.2 g/cc
Tap density: 3.2-3.8 g/cc
Hausner ratio: 1.1-1.3
Flow rate: 25-35 s/50g
Composition:
Element | Zn | Mg | Cu | Fe | Si | Mn | Cr | Ti | Al |
---|---|---|---|---|---|---|---|---|---|
Wt % | 5.1-6.1 | 2.1-2.9 | 1.2-2.0 | 0.5 max | 0.4 max | 0.3 max | 0.28 max | 0.2 max | Balance |
Standards:
- ASTM B213: Standard for Aluminum Powders and Powder Metallurgy Products
- ASTM E740: Standard Guide for Characterizing Particulate Matter in Metal Powders and Powder Metallurgy Compacts
- MPIF Standard 46: Determination of Apparent Density of Non-Free-Flowing Metal Powders
- AMS 4200: Aluminum Alloy Powders
- MIL-DTL-5637: General Specification for Aluminum Alloy Powders for Use in Metal Injection Molding Processes
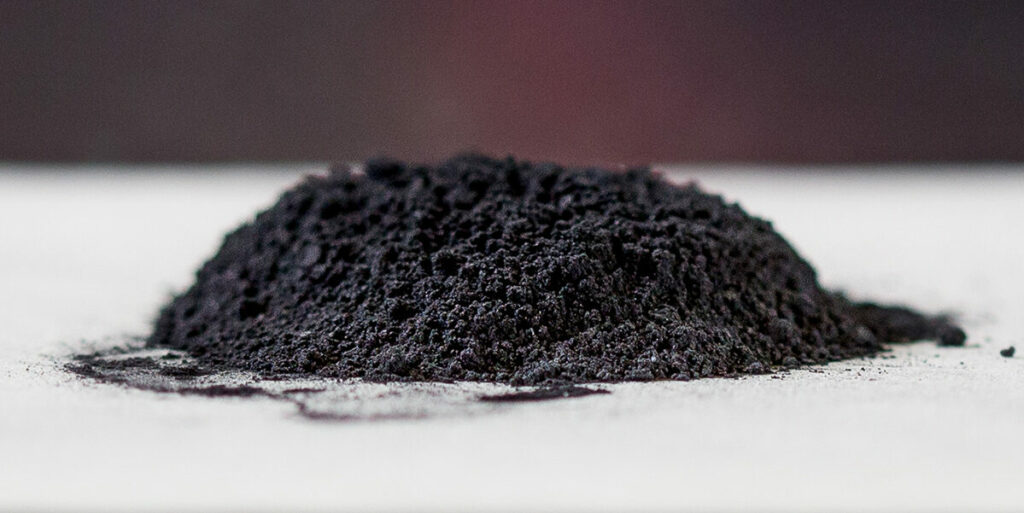
Design Considerations for Al 7075 Powder Parts
Wall thickness: Minimum 0.4 mm, maximum 5 mm
Surface finish: As sintered = 0.8-3.0 μm Ra; Machined = 0.1-0.5 μm Ra
Dimensional tolerance: ±0.5% nominal dimension
Minimum feature size:
- Holes: ≥ 1 mm diameter, ≥ 2 mm depth
- Slots: 1 mm width
- Pins: 1 mm diameter
Draft angles: ≥ 3° draft on vertical walls
Fillet radii: ≥ 0.5 mm at internal corners
Suppliers and Pricing of Al 7075 Powder
Here are some of the leading global suppliers of Al 7075 powder:
Supplier | Location | Size Range | Price Range |
---|---|---|---|
Hoganas | Sweden | 10-150 μm | $50-70/kg |
GKN | UK | 15-63 μm | $45-65/kg |
Sandvik | Sweden | 10-150 μm | $55-75/kg |
LPW Technology | UK | 10-45 μm | $60-80/kg |
Advanced Powders | Canada | 10-45 μm | $55-70/kg |
The price varies based on:
- Purity levels
- Powder size range and distribution
- Morphology (gas vs water atomized)
- Quantity of purchase
- Additional processing like mechanical/thermal treatment
Installation, Operation, and Maintenance of Al 7075 Powder Parts
Installation
- Clean contact surfaces thoroughly to remove dirt, grease and oxides
- Apply anti-seize compound on threads and interfaces if galling is a concern
- Use suitable fasteners – avoid overtightening
- Ensure good fit between components – minimize gaps
Operation
- Operate powder metallurgy parts within design envelope to avoid failure
- Limit peak stresses during service by following recommended procedures
- Consider effects of harsh environments like temperature, chemicals if present
- Periodically inspect for signs of wear, cracks, corrosion etc.
Maintenance
- Lubricate moving assemblies per OEM guidelines
- Check and tighten fasteners when needed
- Identify and mitigate sources of contamination or corrosion
- Repair or replace damaged components before reassembly
- Refinish surfaces as needed to maintain tolerances and clearances
Choosing a Al 7075 Powder Supplier
Here are key factors to consider when choosing a Al 7075 powder supplier:
- Technical expertise: Experience working with Al 7075, knowledgeable about processing methods and parameters optimization
- Quality systems: ISO 9001 certification, strict process controls, quality testing as per ASTM standards
- Consistency: Proven ability to produce powder to tight specifications batch after batch
- R&D capabilities: Invests in developing new powder varieties, sizes, emerging applications
- Customer service: Responsive application engineering and technical support team
- Customization: Capability to tailor powder characteristics and size ranges to your requirements
- Value adds: Services like toll processing, prototyping, testing and characterization
- Logistics: Ability to ship and store powder while maintaining quality
- Pricing: Balance of quality and competitive pricing for desired grade and quantity
- Reputation and references: Positive reputation based on customer experiences
Comparing Gas Atomized vs Water Atomized Al 7075 Powder
Parameter | Gas Atomized | Water Atomized |
---|---|---|
Morphology | Spherical, smooth surface | Irregular shape with satellites |
Particle size distribution | Narrower distribution | Wider distribution |
Flowability | Excellent | Moderate |
Apparent density | 2.7 – 3.1 g/cc | 2.8 – 3.2 g/cc |
Tap density | 3.2 – 3.6 g/cc | 3.5 – 3.8 g/cc |
Compactability | Very good due to morphology | Good |
Sintered density | Higher | Lower |
Mechanical properties | Better overall | Good |
Surface finish | Smoother | Rougher |
Cost | Higher | Lower |
Applications | MIM, AM | Press and sinter |
Advantages and Limitations of Al 7075 Powder
Advantages
- High strength-to-weight ratio
- Good ductility and toughness
- Excellent corrosion resistance
- High thermal conductivity
- Non-toxicity
- Non-pyrophoric compared to some reactive metals
- Near net shape capability in P/M and AM
- Wide range of achievable properties
Limitations
- Relatively low maximum service temperature (120°C)
- Susceptibility to stress corrosion cracking with surface damage
- Post-processing may be required to achieve final tolerances
- Lower ductility and toughness in P/M products vs wrought
- Limited recyclability of powders after use
- Higher cost than some ferrous powders

FAQ
Q: What is the main composition of Al 7075 powder?
A: The main alloying elements in Al 7075 powder are zinc (5.1-6.1 wt%), magnesium (2.1-2.9 wt%), and copper (1.2-2.0 wt%). The balance is aluminum.
Q: What are the typical uses of Al 7075 powder?
A: Major applications include metal injection molding, additive manufacturing, powder metallurgy, thermal spray coatings, aluminum matrix composites, and explosive welding.
Q: What powder size is best for metal injection molding?
A: For MIM, powder size range of 10-45 microns is typically used, with the fraction -45+10 microns most common.
Q: Does Al 7075 powder require special storage conditions?
A: Al 7075 powder should be stored in cool, dry environment in sealed containers. Extended exposure to moisture can result in oxidation.
Q: What are the effects of zinc in Al 7075 alloy?
A: Zinc significantly increases the strength and hardness of Al 7075 through solid solution strengthening and precipitation hardening heat treatments.
Q: What is the difference between gas atomized and water atomized Al 7075 powder?
A: Gas atomized powder has spherical morphology for better flow and compactability. Water atomized powder has irregular shape with wider particle distribution suited for press-and-sinter method.
Q: Does Al 7075 powder require sintering in inert atmosphere?
A: Yes, sintering in vacuum or inert gas atmosphere like argon is necessary to prevent oxidation of the powder. Nitrogen can also be used.
Q: What causes the dark staining of Al 7075 powder during storage?
A: Dark discoloration over time is generally superficial oxidation of the particle surfaces. It can be removed through proper rinsing, cleaning and handling before use.
Q: What post processing is used for Al 7075 P/M parts?
A: Post sintering operations like heat treatment, machining, grinding, drilling and finishing are used to achieve final dimensions, surface finish, dimensional tolerances and desired mechanical properties.
Q: Is Al 7075 powder flammable or explosive?
A: No, Al 7075 powder is not flammable or explosive under normal handling conditions. It is not classified as a hazardous material for transportation.