Aluminium alloy powder refers to powder metallurgy forms of aluminium that have been alloyed with elements like silicon, magnesium, zinc, copper, manganese and nickel to create materials with enhanced mechanical and physical properties. By compressing and sintering aluminium alloy powders, engineers can manufacture high-performance components for demanding applications.
Types of Aluminium Alloy Powder
Various aluminium powder alloys are commercially available using different base metals and alloying strategies:
Alloy Type | Key Alloying Elements | Characteristics |
---|---|---|
Aluminium silicon alloy | Si: 5-20% | Excellent fluidity and corrosion resistance |
Al-Si-Mg | Si, Mg: 0.5-1.5% | High strength-to-weight ratio |
Al-Mg-Si | Mg: 1-10% + Si | Good ductility, formability and machinability |
Al-Zn-Mg-Cu (7xxx) | Zn, Mg, Cu up to 9% | Highest strength aluminium PM alloys |
Al-Ni-Co-Cd | Ni, Co, Cd | High elastic modulus |
Al-Fe-V-Si | Fe, V | Heat treatable – age hardening |
By balancing composition, powder metallurgy aluminium alloys can achieve combinations of strength, corrosion resistance, weldability, workability and cost effectiveness.
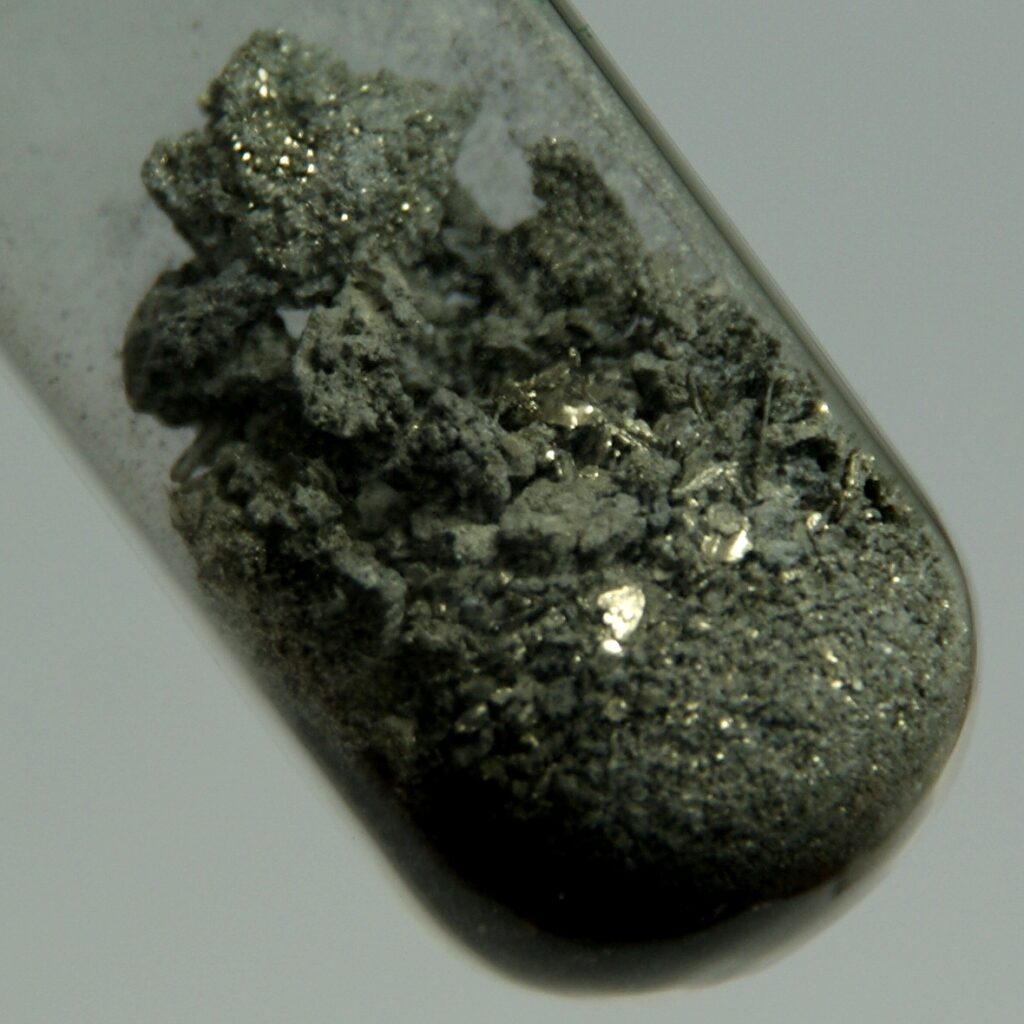
Properties and Characteristics
Key properties of aluminium alloy powder vary by exact composition but generally offer:
Property | Characteristics |
---|---|
Density | Low – 2.55 to 2.85 g/cm3 |
Melting point | 560 to 660°C depending on alloys |
Strength | 150 to 310 MPa tensile strength |
Elastic modulus | 65 to 80 GPa |
Thermal conductivity | 100 to 180 W/mK , high for metals |
Electrical conductivity | 20 to 38 MS/m |
Workability | Good ductility and formability in annealed state |
Corrosion resistance | Excellent due to self-passivating oxide film |
Recyclability | Fully reusable scrap value |
By blending in harder particles and annealing processes, engineers can tailor the material properties for targeted applications.
Applications and Uses
Aluminium alloy powders suit a variety of industrial uses:
Industry | Common Applications |
---|---|
Automotive | Pistons, transmission and engine parts |
Aerospace | Structural and satellite components |
Industrial | Gears, tooling fixtures, shafts |
Military | Ballistics, ordnance equipment |
Printing | 3D printed prototypes and products |
Sports equipment | Golf clubs, baseball bats, lacrosse sticks |
Aluminium powder alloys enable lightweight, high performance metal components thanks to their strength, workability and corrosion resistance.
Specifications and Grades
International standards classify aluminium alloy powder grades by:
Attribute | Measurement Details |
---|---|
Alloy designation | 4 digit system denoting composition (e.g. 6061) |
Temper | Denotes amount of cold working and annealing (F, T4, T6 etc) |
Size | Screen mesh size distributions (e.g -100/+325 mesh) |
Shape | Spherical, nodular, flakes, atomized forms |
Apparent density | Measured in g/cm3 based on packing effectiveness |
Flow rate | Time to flow 50g through Hall apparatus funnel |
Oxide content | Percent oxygen contamination from exposure |
Powder lots must meet certified chemistry assays and physical property tolerances to ensure performance.
Suppliers and Pricing
Aluminium Alloy Powder Suppliers | Price per kg |
---|---|
TLS Technik GmbH | $12-25 |
Avomet Advanced Materials | $15-40 |
Sandvik Osprey | $20-50 |
Aluminium Powder Company Ltd | $25-60 |
Valimet Inc. | $18-55 |
Prices vary based on alloy choice, particle shape, lot quantity and purity levels. Get competitive quotes based on quality needs and usage volumes.
Pros vs Cons
Advantages | Disadvantages |
---|---|
Lightweight strength | Lower shear strength than steel |
Excellent corrosion resistance | Sensitive to high temperature oxidation |
Good thermal/electrical conductivity | Must control for hydrogen embrittlement |
High scrap value, recyclability | Requires surface treatments in some uses |
Economical, available | Complex multistep workability process |
Within design constraints, aluminium alloy powder offers useful versatility across manufacturing industries.
Comparing Atomized vs Sinter-Forged Aluminium Powder
Property | Atomized | Sinter-Forged |
---|---|---|
Particle shape | Irregular flattened | Rounded compacted |
Typical size | Under 325 mesh | Larger 1mm aggregates |
Production method | Gas or water atomization | Compaction + sintering |
Common applications | MIM feedstock | Automotive parts |
Cost | Lower | Higher per-part cost |
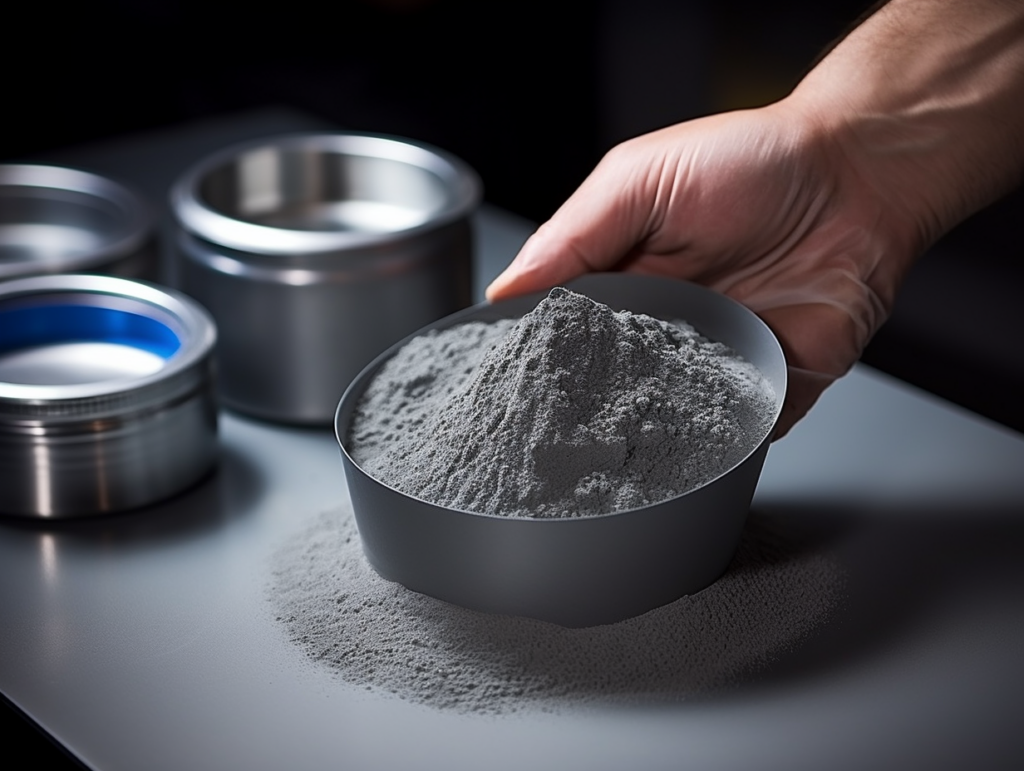
FAQs
What is aluminium alloy powder used for?
The most common applications are automotive parts like pistons, gears, structural aerospace components, additive manufacturing feedstock and consumer product molds or tooling.
What is the difference between aluminium powder and aluminium alloy powder?
Aluminium powders are pure elemental aluminium while alloy powders have other metals like silicon, magnesium, copper etc. added to enhance properties like strength and workability.
Is aluminium powder dangerous?
Pure aluminium powder should be handled with care given flammability concerns. Some alloy grades with magnesium or titanium can be sensitive to moisture creating hydrogen gas. Always take safety precautions working with metal powders.
What is the strongest aluminium alloy?
7xxx series alloys like 7068 and 7075 which contain zinc, magnesium and copper have the highest strength among aluminium alloys while retaining good workability.
Can you 3D print with aluminium powder?
Yes, aluminium alloy powder can be used in specialized 3D printers like DMLS systems along with rigorous parameter controls to successfully fabricate complex metal components through additive manufacturing.