Aluminum based alloy powder have become a game-changer in various industries, from aerospace and automotive to biomedical and consumer electronics. Imagine crafting intricate components with complex geometries, pushing the boundaries of traditional manufacturing. That’s the power of these tiny, versatile wonders. But how exactly do these aluminum-based alchemists come into existence? Buckle up, because we’re diving deep into the fascinating world of aluminum alloy powder production methods!
Production of Aluminum Based Alloy Powder by Atomization Method
The Art of Disintegration: Atomization
Atomization, a process akin to creating a metallic confetti shower, reigns supreme in aluminum alloy powder production. Molten metal, heated to scorching temperatures, is broken down into fine droplets through various techniques. These droplets rapidly solidify in a controlled atmosphere, forming the coveted aluminum alloy powder. Let’s explore the two main atomization methods:
- Gas Atomization: Picture a high-pressure stream of inert gas (like nitrogen or argon) blasting a molten aluminum alloy stream. This forceful collision disintegrates the metal into a fine mist of droplets, which solidify as they fall through a cooling tower. Imagine a sculptor using a pressurized airbrush to create a metallic masterpiece, one tiny particle at a time. Gas atomization offers excellent control over particle size and morphology (shape), making it ideal for demanding applications like additive manufacturing.
- Water Atomization: Here, the molten metal meets a high-velocity stream of water. The forceful impact shatters the liquid metal into a finer, more irregular powder compared to gas atomization. Think of a high-powered water jet pulverizing a molten aluminum stream – that’s the essence of water atomization. This method is cost-effective and suitable for applications where precise particle size and shape are less critical, such as pyrotechnics or metal injection molding.

Aluminum Alloy Powders via Atomization
While atomization reigns supreme, it’s not without its considerations. Gas atomization, while offering superior control, comes at a higher cost compared to water atomization. Additionally, gas-atomized powders tend to be more spherical, while water-atomized powders have a more irregular shape. Choosing the right method depends on the specific application’s needs – a delicate balance between cost, particle characteristics, and desired properties.
Beyond the Big Two: Alternative Atomization Techniques
The realm of atomization extends beyond just gas and water. Here are some lesser-known, but equally intriguing, methods:
- Electrolytic Atomization: This method utilizes an electrolytic cell to break down molten metal into droplets. Imagine an electroplating process in reverse, where instead of building up metal, we’re breaking it down into fine particles. Electrolytic atomization offers exceptional control over particle size and purity, making it ideal for specialized applications.
- Rapid Solidification: Here, molten metal is exposed to a very high cooling rate, resulting in unique microstructures and potentially novel properties in the resulting powder. Imagine flash-freezing molten metal to capture its essence in a single instant. Rapid solidification holds promise for creating new and improved aluminum alloys with enhanced properties.
Aluminum Alloy Powder via Atomization
The beauty of atomization lies in its versatility. A wide range of aluminum alloys can be processed into powders using these methods. Here are ten specific examples, each with its own unique properties and applications:
- AA2024: This high-strength aluminum-copper alloy powder is known for its excellent machinability and is widely used in aerospace applications for components requiring a good balance of strength and weight savings.
- AA6061: A popular choice for general-purpose applications, AA6061 aluminum alloy powder offers good corrosion resistance and weldability. Think of it as the all-rounder in the aluminum alloy powder world.
- AA7075: Offering exceptional strength and hardness, AA7075 aluminum alloy powder finds its place in demanding aerospace and defense applications. Imagine a lightweight metal with the strength to withstand high stresses.
- AlSi10Mg: This silicon-magnesium alloy powder boasts excellent castability and is often used for producing complex, near-net-shape components through processes like metal injection molding.
- AlSi7Mg: A close cousin to AlSi10Mg, this alloy powder offers a good balance of castability and strength, making it suitable for various automotive and industrial applications.
- AM3004: This high-purity aluminum alloy powder is known for its excellent weldability and formability, making it ideal for applications requiring intricate shapes and good joining characteristics.
- Invar 42: This unique alloy powder, known for its minimal thermal expansion coefficient, finds its place in high-precision instruments and
Gas Explosion Method
Another method for crafting aluminum alloy powders is the gas explosion technique. Here, molten metal is injected into a chamber filled with an inert gas mixture. A precisely timed ignition source creates a sudden pressure increase, violently fragmenting the molten metal into a fine powder. Imagine a controlled explosion that breaks down liquid metal into a million tiny pieces.
The gas explosion method offers a high production rate compared to atomization techniques. However, the resulting powder particles tend to be more irregular in shape and size compared to gas or water atomization. This method is often used for applications where precise particle control is less critical, such as pyrotechnics or metal additive manufacturing processes that can accommodate a wider range of particle sizes.
Mechanical Crushing Method
The mechanical crushing method takes a more brute-force approach. Here, bulk aluminum alloy materials are shattered into a fine powder using various grinding techniques. Ball milling, where the metal is crushed by high-energy balls in a rotating chamber, is a common method. Think of a giant mortar and pestle pulverizing aluminum chunks into a fine dust.
While cost-effective and suitable for some applications, the mechanical crushing method generally produces a wider range of particle sizes and shapes compared to atomization techniques. Additionally, the crushing process can introduce impurities and potentially degrade the inherent properties of the aluminum alloy. This method is often used for applications where precise particle control is less critical, such as pyrotechnics or conductive fillers in composites.
the Aluminum Alloy Powder of Properties, Applications, and Beyond
Now that we’ve explored the production methods, let’s delve deeper into the world of aluminum alloy powders themselves.
Aluminum Alloy Powders: A Spectrum of Properties
The properties of aluminum alloy powders depend on the specific alloy composition, the chosen production method, and the processing parameters. Here’s a glimpse into some key characteristics:
- Particle Size and Distribution: Particle size significantly impacts the powder’s flowability, packing density, and suitability for different applications. For instance, finer powders offer better packing density but can be challenging to flow freely.
- Particle Morphology (Shape): The shape of the particles, whether spherical, irregular, or angular, influences factors like packing density, flowability, and surface area. Spherical particles tend to flow more easily and pack more densely, while irregular shapes can provide better mechanical interlocking in some applications.
- Flowability: This refers to the ease with which the powder flows. Good flowability is crucial for smooth operation in various powder handling and processing techniques, such as additive manufacturing.
- Apparent Density: This is the density of the powder in its loose, uncompacted state. It’s a critical factor for material handling and storage considerations.
- Chemical Composition: The specific alloying elements present in the aluminum powder influence its mechanical properties, corrosion resistance, and other characteristics.
the Applications of Aluminum Alloy Powders
The versatility of aluminum alloy powders makes them a valuable asset across various industries:
- Additive Manufacturing: Aluminum alloy powders are a popular choice for 3D printing techniques like selective laser melting (SLM) and binder jetting. These methods allow for the creation of complex, lightweight components with intricate geometries.
- Metal Injection Molding (MIM): This process utilizes aluminum alloy powders to produce near-net-shape components. The powder is mixed with a binder, molded into the desired shape, and then debindered and sintered to achieve the final product.
- Thermal Spraying: Aluminum alloy powders can be used to create coatings on various substrates to improve wear resistance, corrosion resistance, or electrical conductivity.
- Pyrotechnics: The irregular shapes and high surface area of aluminum alloy powders make them ideal for pyrotechnic applications, creating dazzling visual effects.
- Conductive Fillers: Aluminum alloy powders can be incorporated into composites or polymers to enhance their electrical conductivity.
Specifications, Sizes, Grades, and Standards
Choosing the right Aluminum Based Alloy Powder for a specific application requires careful consideration of various factors. Here’s a breakdown of some key aspects:
Factor | Description | Example |
---|---|---|
Alloy Composition | The specific combination of elements in the aluminum alloy | AA2024 (aluminum-copper alloy), AA6061 (aluminum-magnesium-silicon alloy) |
Particle Size Distribution | The range and distribution of particle sizes in the powder | D50 = 45 microns (median particle size is 45 microns) |
Particle Morphology (Shape) | The shape of the particles (spherical, irregular, angular) | Spherical, Irregular |
Flowability | The ease with which the powder flows | Excellent, Good |
Apparent Density | The density of the powder in its loose, uncompacted state | 2.5 g/cm³ |
Grade | The purity level and additional elements present | Commercial Grade (CG), High Purity (HP) |
Standards | Specifications set by organizations to ensure quality and consistency | ASTM B29 (aluminum alloy powder for additive manufacturing) |
Suppliers and Pricing
The world of Aluminum Based Alloy Powder suppliers is vast and ever-evolving. Here are some factors to consider when choosing a supplier:
- Product Portfolio: The variety of aluminum alloy powders offered, including different compositions, particle sizes, and grades.
- Production Capabilities: The supplier’s capacity to meet your volume requirements and ability to produce custom powder specifications.
- Quality Control: The supplier’s commitment to quality control measures to ensure consistent powder properties.
- Pricing: Powder prices can vary depending on the alloy composition, particle size, grade, and order quantity. It’s crucial to compare quotes from multiple suppliers to find the best value.
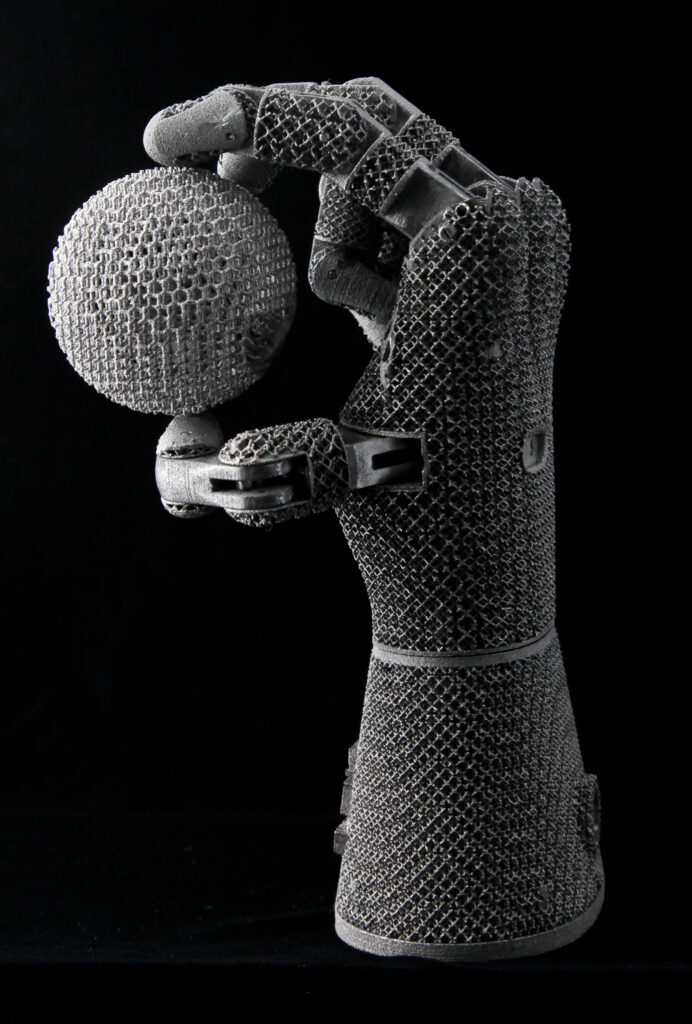
Pros and Cons of Aluminum Based Alloy Powder
Advantages:
- Lightweight: Aluminum Based Alloy Powder offer significant weight savings compared to traditional materials like steel.
- High Strength-to-Weight Ratio: These powders can achieve excellent strength while maintaining a low weight, making them ideal for aerospace and automotive applications.
- Design Flexibility: Additive manufacturing techniques utilizing aluminum alloy powders enable the creation of complex geometries and intricate components.
- Near-Net-Shape Manufacturing: Processes like metal injection molding allow for the production of components with minimal post-processing requirements.
- Diverse Applications: Aluminum alloy powders find uses in various industries, from additive manufacturing to pyrotechnics.
Disadvantages:
- Cost: Aluminum alloy powders can be more expensive than traditional manufacturing materials like bulk aluminum.
- Powder Handling: These powders require careful handling to prevent contamination and ensure consistent flow properties.
- Process Optimization: Additive manufacturing and other powder-based processes may require optimization for specific powder characteristics.
- Environmental Considerations: The production process for some aluminum alloy powders can have environmental implications.
FAQ
Q: What are the different types of aluminum alloy powders?
A: Aluminum alloy powders come in a wide variety, each with a unique combination of elements. Common types include AA2024 (high-strength), AA6061 (general-purpose), AA7075 (high-strength and hardness), AlSi10Mg (excellent castability), and AM3004 (good weldability and formability).
Q: What are the factors to consider when choosing an aluminum alloy powder?
A: Several factors are crucial, including the desired application, required properties (strength, weight, conductivity), particle size and morphology, flowability, and cost.
Q: How are aluminum alloy powders used in additive manufacturing?
A: These powders are a popular feedstock for 3D printing techniques like selective laser melting (SLM) and binder jetting. The powder is selectively melted or bonded layer-by-layer to create the desired component.
Q: What are the advantages of using aluminum alloy powders over bulk aluminum?
A: Aluminum alloy powders offer design flexibility, near-net-shape manufacturing capabilities, and the potential for lighter weight components compared to traditional machining from bulk aluminum.
Q: Are there any safety considerations when handling aluminum alloy powders?
A: Yes, aluminum alloy powders can be combustible and may pose inhalation risks. Proper handling procedures and personal protective equipment are essential.
Conclusion
Aluminum alloy powders are revolutionizing manufacturing processes across various industries. With continuous advancements in production methods, powder characteristics, and processing techniques, the future of aluminum alloy powders is bright. From creating lightweight components for aerospace applications to enabling complex geometries in consumer electronics, these versatile powders are poised to play a transformative role in the manufacturing landscape for years to come.