the Powerhouse Material for Modern Manufacturing
Imagine a material that combines the exceptional strength of metal with the versatility of a powder. That’s the magic of aluminum-based alloy powders, a game-changer in the world of manufacturing. But what exactly are they, and how are they revolutionizing different industries? Dive into this comprehensive guide to unlock the secrets of this remarkable material.
What are Aluminum-Based Alloy Powders?
Aluminum-based alloy powders are finely-ground metallic particles, typically ranging between 10 and 150 micrometers in size. These powders are not just pure aluminum; they are alloyed with other elements like silicon, magnesium, copper, and zinc to enhance their properties, making them stronger, more corrosion-resistant, and lighter than pure aluminum.
Think of it like this: Imagine baking a cake. Pure aluminum is like the base flour, providing the foundation. But to create a cake with specific flavors and textures, you add ingredients like sugar, eggs, and flavorings. Similarly, alloying elements act as the “ingredients” that tailor the properties of the aluminum-based alloy powder for specific applications.
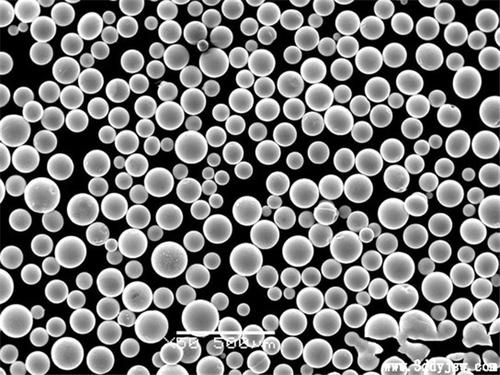
Production Method of Aluminum-Based Alloy Powder
The journey of aluminum-based alloy powder begins with alloying. Aluminum is melted in a furnace and combined with the desired elements in specific proportions. This molten mixture is then transformed into a powder using two main techniques:
- Gas Atomization: Molten metal is forced through a small nozzle at high pressure, breaking it into tiny droplets that solidify rapidly in a stream of inert gas (like nitrogen or argon) to form spherical powder particles.
- Water Atomization: Similar to gas atomization, but the molten metal is broken up into droplets using a high-pressure water jet. This method is typically used for less reactive metals and produces irregularly shaped particles.
The choice of method depends on the desired properties of the final powder. Gas atomization generally results in more spherical particles with better flowability and packing density, crucial for some additive manufacturing processes.
Key Factors Influencing Aluminum-Based Alloy Powder Properties
The performance of aluminum-based alloy powder mainly depends on its composition, particle size, shape, and surface state.
- Composition: The specific elements and their proportions significantly impact the strength, corrosion resistance, and other properties of the powder. For instance, adding copper increases strength but reduces corrosion resistance, while magnesium improves machinability.
- Particle Size: Smaller particles generally offer better surface area and packing density, making them suitable for specific additive manufacturing techniques like laser melting. However, very fine particles can be challenging to handle due to increased surface reactivity and potential agglomeration (clumping).
- Shape: Spherical particles typically offer better flowability and packing density compared to irregularly shaped ones. This is crucial for ensuring consistent material deposition in additive manufacturing processes.
- Surface State: The surface chemistry and presence of oxides or other contaminants can influence the wettability, bonding, and overall performance of the powder.
Understanding these factors allows manufacturers to tailor the powder properties for specific applications, achieving optimal performance in the final product.
Applications of Aluminum-Based Alloy Powders
Aluminum-based alloy powders are finding their way into a diverse range of industries due to their unique combination of lightweight properties, good strength, and excellent recyclability. Here are some of their key application areas:
Application Areas | Specific Examples |
---|---|
Aerospace: | Aircraft components, rocket parts, heat exchangers |
Automotive: | Engine components, wheels, body panels |
Electronics: | Heat sinks, electronic enclosures, electrical connectors |
Medical: | Prosthetic limbs, dental implants, surgical instruments |
Consumer Goods: | Sporting goods, bicycles, consumer electronics housings |
-
CM247LC Powder | Nickel Alloy Powder
-
0# Pure Nickel powder
-
NiCoCrAlY alloys powders
-
Rene 142 alloy-Rene Powder
-
Haynes 25 Haynes Powder
-
Best Hastelloy C-22 Powder-High temperature alloy Powder for 3D Printing
-
Best Hastelloy C-276 Powder-High temperature alloy Powder for 3D Printing
-
Best Hastelloy N Powder-High temperature alloy Powder for 3D Printing
-
Best Hastelloy B Powder丨High temperature alloy Powder for 3D Printing
the Diverse Landscape of Aluminum-Based Alloy Powders
The world of aluminum-based alloy powders is vast, with different options catering to specific needs. Here’s a glimpse into some popular models and their characteristics:
Model | Composition (wt%) | Particle Size (µm) | Shape | Applications |
---|---|---|---|---|
AA2024 | Cu 4.5, Mg 1.5, Mn 0.6 | 15-45 | Spherical | Aerospace components, high-strength applications |
AA6061 | Mg 0.5 – 1.0, Si 0.25 – 0.6, Cu 0.15 – 0.4 | 15-45 | Spherical | General-purpose applications, building & construction, automotive parts |
AA7075 | Zn 5.6, Mg 2.5, Cu 1.6 | 15-45 | Spherical | Aerospace components, high-strength applications |
AlSi10Mg | Si 9 – 11, Mg 0.3 – 0.6 | 15-45 | Irregular | Engine components, pistons, cylinder heads |
AlSi7Mg0.3 | Si 6.5 – 7.5, Mg 0.2 – 0.3 | 15-45 | Irregular | Automotive parts, wheels, engine blocks |
AlSi12 | Si 11 – 13 | 15-45 | Irregular | Foundry applications, cast components |
IN625 | Ni 2.2, Cr 0.15, Fe 0.15, Si 0.1 | 20-50 | Spherical | Medical implants, aerospace components |
Scalmalloy | Sc 4.02, Mg 0.7, Zr 0.18 | 15-45 | Spherical | High-performance aerospace components, demanding applications |
A20X | Cu 9 – 11, Si 0.5 – 1.2 | 15-45 | Spherical | Additive manufacturing components, heat exchangers |
AlSiCuMg | Si 7 – 9, Cu 1 – 2, Mg 0.3 – 0.5 | 15-45 | Irregular | Automotive parts, wear-resistant components |
the Pros and Cons of Aluminum-Based Alloy Powders
While aluminum-based alloy powders offer numerous advantages, it’s essential to consider their limitations to make informed decisions.
Pros:
Lightweight: Compared to traditional materials like steel, aluminum-based alloy powders offer significant weight savings, making them ideal for applications like aerospace and transportation where weight reduction is crucial.
Good Strength: Alloying elements enhance the strength of aluminum, making the powders suitable for various structural applications.
Excellent Recyclability: Aluminum is one of the most recyclable metals, and aluminum-based alloy powders can be recycled multiple times, minimizing environmental impact.
Design Flexibility: Additive manufacturing techniques utilizing aluminum-based alloy powders enable the creation of complex geometries and intricate designs, previously impossible with traditional manufacturing methods.
Cons:
Higher Cost: Compared to traditional manufacturing methods like casting or machining, the production of aluminum-based alloy powders can be more expensive.
Powder Handling Challenges: Fine powders can be challenging to handle due to their increased surface area and potential for agglomeration. This necessitates specialized equipment and handling procedures to ensure consistent quality and safety.
Surface Quality: The surface quality of the powder can impact the final product’s properties. Careful selection and handling are crucial to minimize the presence of oxides or other contaminants that could affect performance.
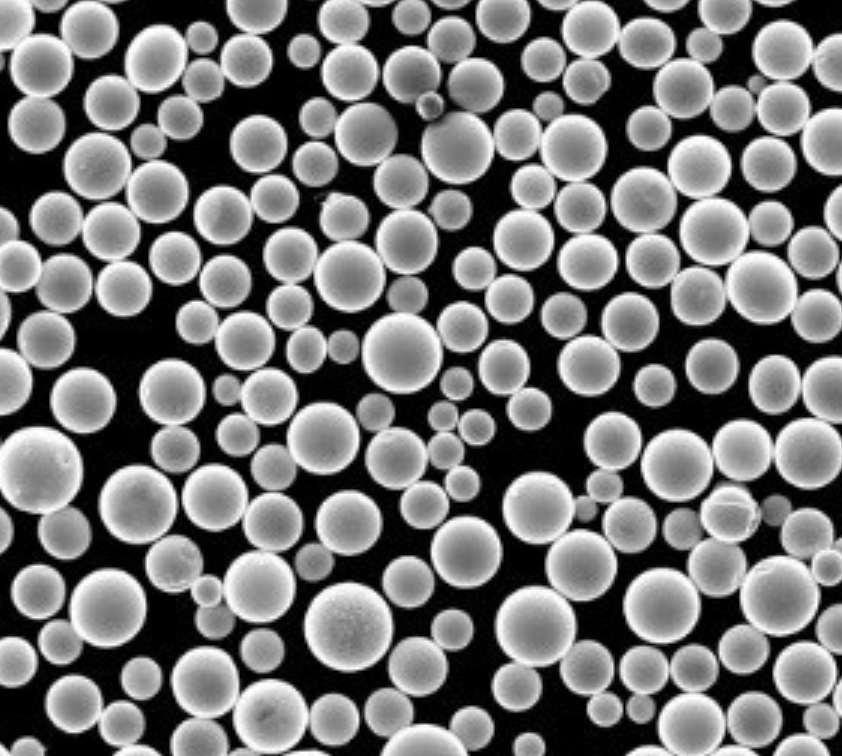
FAQ
1. What are the different shapes of aluminum-based alloy powders?
Aluminum-based alloy powders can have various shapes, including:
- Spherical: These are the most common type, offering good flowability and packing density, crucial for additive manufacturing processes.
- Irregular: These have less consistent shapes but can be more cost-effective to produce and are suitable for some applications like casting.
2. How are aluminum-based alloy powders stored?
To maintain their quality and prevent degradation, aluminum-based alloy powders are typically stored in sealed containers under inert gas (like nitrogen or argon) to minimize moisture and oxidation.
3. Are there any safety precautions to consider when handling aluminum-based alloy powders?
Fine powders can pose inhalation risks. It’s essential to follow proper safety protocols, including wearing personal protective equipment (PPE) like masks and gloves when handling aluminum-based alloy powders. Additionally, proper ventilation is crucial to prevent.
Additional Considerations and Future Outlook
Environmental Impact: While aluminum itself is highly recyclable, the production process of aluminum-based alloy powders can have an environmental impact. It’s important to consider the energy consumption and potential emissions associated with the production process. However, ongoing research and development are focused on minimizing this impact, making the production process more sustainable.
Advancements in Technology: The field of aluminum-based alloy powders is constantly evolving. New alloy compositions are being developed to offer improved properties like even higher strength, better corrosion resistance, and enhanced printability for additive manufacturing. Additionally, advancements in powder production techniques are leading to more efficient and cost-effective methods, making these powders even more accessible for various applications.
Conclusion
Aluminum-based alloy powders represent a revolutionary material with the potential to transform various industries. Their unique combination of lightweight properties, good strength, and design flexibility makes them a compelling choice for applications where weight reduction, performance optimization, and complex geometries are crucial. As technology continues to advance, we can expect to see even more innovative applications for this versatile material, shaping the future of manufacturing and design.