Aluminum silicon alloy powder is a metal powder composed of aluminum and silicon that is used for various applications such as additive manufacturing, brazing, welding, and thermal spraying. This lightweight material offers high strength, wear resistance, and thermal conductivity properties.
Aluminum Silicon Alloy Powder Composition
Aluminum silicon alloys contain silicon as the main alloying element. Other alloying elements like magnesium and copper may also be present in small quantities.
The amount of silicon ranges from 5% to 20%, with common compositions between 10-15% Si. The aluminum makes up the balance composition along with minor elements.
Higher silicon content imparts more strength, whereas more ductility comes from higher aluminum levels. Specific compositions are tailored based on the desired material properties and manufacturing method.
Element | Composition Range |
---|---|
Silicon (Si) | 5-20% |
Aluminum (Al) | Balance |
Magnesium (Mg) | 0-5% |
Copper (Cu) | 0-5% |
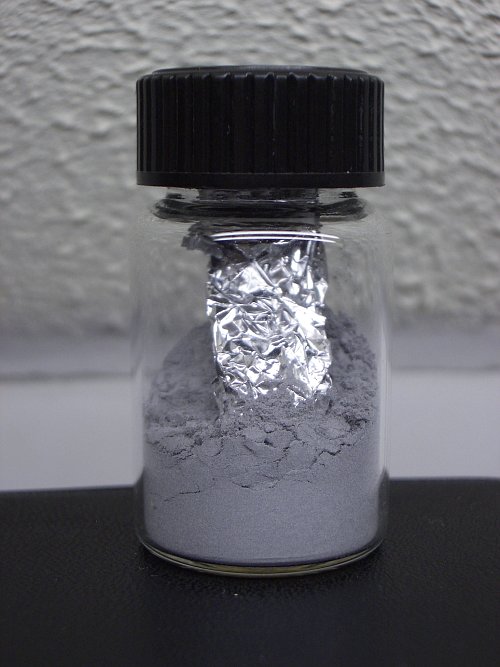
Aluminum Silicon Alloy Powder Characteristics
Aluminum silicon alloy powder has unique characteristics that make it suitable for specialty applications:
- High strength-to-weight ratio
- Good corrosion resistance
- Excellent thermal conductivity
- Low coefficient of thermal expansion
- Good dimensional stability at elevated temperatures
- Higher melting point than pure aluminum
- Can be strengthened through heat treatment
- Flowability allows usage in additive manufacturing
Controlling particle size distribution and morphology during atomization results in powder suitable for specific processes. Common size ranges are 15-150 microns. Irregular, spherical, and satellite particle shapes occur.
Property | Description |
---|---|
Particle shape | Irregular, spherical, satellite |
Particle size (μm) | 15-150 |
Apparent density (g/cc) | 1.5-3.5 |
Flowability | Excellent |
Melting point (°C) | 570-650 |
Aluminum Silicon Alloy Powder Manufacturing
Aluminum silicon alloy powder is manufactured using atomization processes where the molten metal is broken into droplets that solidify into fine spherical powder particles.
Gas atomization uses high-pressure inert gas to atomize the liquid metal stream into a spray of metal droplets. Gas atomized powder has a spherical morphology ideal for AM.
Water atomization breaks up the molten stream by high-velocity water jets. This produces an irregular, non-spherical powder appropriate for thermal spray.
The liquid metal composition, atomization parameters, and cooling rate determines the final powder characteristics. Post-process sieving and classification ensures powder meets specifications.
Process | Description | Typical Powder Characteristics |
---|---|---|
Gas atomization | Uses an inert gas like nitrogen or argon | Spherical morphology, 15-150 μm size |
Water atomization | Employs high-speed water jets | Irregular shape, 15-150 μm size |
Aluminum Silicon Alloy Powder Applications
The lightweight strength and thermal properties of aluminum silicon alloys make their powders useful across the following applications:
Additive manufacturing – Used in powder bed fusion and directed energy deposition processes to fabricate complex, lightweight components with good properties.
Welding and brazing – Offer excellent flow and capillary properties in welding, while providing stamped braze-filler metal preforms.
Thermal spraying – Sprayed as coatings to provide wear resistance, thermal barriers, and corrosion protection with low weight.
Metal injection molding – Allows intricate net-shape small parts production through powder metallurgy approach.
Application | Benefits | Example Industries |
---|---|---|
Additive manufacturing | Complex, lightweight parts | Aerospace, automotive |
Welding and brazing | Excellent flow properties | Automotive, construction |
Thermal spraying | Wear and corrosion resistant coatings | Industrial equipment, oil and gas |
Metal injection molding | Intricate, net-shape parts | Electronics, consumer products |
-
CM247LC Powder | Nickel Alloy Powder
-
0# Pure Nickel powder
-
NiCoCrAlY alloys powders
-
Rene 142 alloy-Rene Powder
-
Haynes 25 Haynes Powder
-
Best Hastelloy C-22 Powder-High temperature alloy Powder for 3D Printing
-
Best Hastelloy C-276 Powder-High temperature alloy Powder for 3D Printing
-
Best Hastelloy N Powder-High temperature alloy Powder for 3D Printing
-
Best Hastelloy B Powder丨High temperature alloy Powder for 3D Printing
Aluminum Silicon Alloy Powder Specifications
Aluminum silicon alloy powders are available under various standard grades and proprietary manufacturer designations. Common aluminum grades contain 10-15% silicon such as:
- 4032, 4045, 4145 – 10-13% Si alloys with medium strength
- 4047, A357 – 11-13% Si casting alloys
- 2319, 6061 – Medium-high Si aerospace alloys
Exact alloy composition conforms to designated specifications that list permissible elemental ranges, powder characteristics, manufacturing method, quality checks, and packaging requirements.
International standards organizations like ASTM International provide recognized aluminum alloy powder specifications:
Standard | Title | Application |
---|---|---|
ASTM B841 | Standard Specification for Aluminum-Silicon Alloy Powder and Powder Metallurgy Products | Additive manufacturing, MIM |
AWS A5.10 | Welding Consumables – Wire Filler Metals and Rods | Welding and brazing |
AWS C3.4M/C3.4 | Aluminum Brazing Flux | Brazing fillers and fluxes |
Aluminum Silicon Alloy Powder Suppliers
Many large manufacturers and specialized metal powder producers offer various aluminum silicon alloy powder products. Their in-depth materials expertise and sophisticated powder plants enable tailored alloys and consistent quality.
Both toll processing service as well as standard inventory grades are available to purchase. Some leading global suppliers are:
- Sandvik Osprey
- Höganäs
- Carpenter Additive
- Linde Gas
- Rio Tinto Metal Powders
- AP&C Powder Metallurgy
- Praxair
Pricing ranges from $50-150 USD per kg based on factors like order volume, alloy composition, powder quality and size distribution, packaging type (cans, drums etc.), and lead time.
Supplier | Typical Pricing | Standard Package Size | Lead Times |
---|---|---|---|
Sandvik, Höganäs | $100-150 per kg | 15-25 kg containers | 8-10 weeks |
Carpenter Additive, Linde | $75-125 per kg | 10-50 kg drums/boxes | 4-8 weeks |
AP&C, Rio Tinto | $50-100 per kg | 500-1,000 kg bulk bags | 6-12 weeks |
Comparison of Aluminum Alloys for Metal AM
Aluminum alloy options like AlSi10Mg, Scalmalloy, and 6061 offer different mechanical properties. Using wire-feed based DED or powder bed fusion methods enables lightweight, high-performance parts.
Key factors when selecting an alloy powder include buildability, anisotropic behavior, need for heat treatments, surface finish, and application requirements.
Alloy | Description | Buildability | Mechanical Properties | Post-Processing Needs |
---|---|---|---|---|
AlSi10Mg | Common cast alloy with good fluidity and 10% Si | Very good | Tensile strength 330-420 MPa, hardness 75-90 HB | May need hot isostatic pressing (HIP), heat treatment |
Scalmalloy | Al-Mg-Sc alloy designed for AM, scandium refine grains | Excellent | Yield strength over 460 MPa, elongation 8% | Good as-built properties, minimal post-processing |
6061 | Heat treatable medium-high Si alloy, aerospace grade | Average, cracks can occur | Tensile strength 240-290 MPa, hardness 73-88 HB | Solution heat & aging treatments boost properties |
AlSi10Mg is a versatile option able to produce dense components with medium strength suited for automotive and industrial applications. HIP and T6 heat treatment can further enhance properties. Scalmalloy delivers the best right-out-of-the-printer strength due to fine microstructure. 6061 requires heat treatment to achieve its full properties and is preferred for aerospace applications after conditioning.
Advantages and Limitations of Al-Si Alloys
Aluminum silicon alloys offer several benefits but also pose some challenges in additive manufacturing:
Advantages
- Higher strength than aluminum but lower density than steels
- Excellent fluidity allows complex geometries in casting and AM
- Good corrosion resistance and weldability
- Alloys like AlSi10Mg easy to print without cracks
- Less residual stresses compared to other materials
- Mostly good dimensional accuracy and surface finish
Limitations
- Lower maximal temperature capability than nickel or titanium alloys
- High thermal conductivity makes controlled heating difficult
- High reflectivity challenges some AM laser processes
- High thermal expansion coefficient requires supports
- Powder can be explosive when very fine or oxidized
- Limited number of validated alloy grades for AM
Overall, aluminum silicon powders enable lightweight and thermally performing components across automotive, aerospace, industrial, and consumer applications with ongoing expansions in printable materials.
Frequently Asked Questions
Q: What is aluminum silicon alloy powder used for? | A: Aluminum silicon alloy powder has applications in additive manufacturing, welding, brazing, thermal spraying, and metal injection molding to create lightweight, high-strength components and protective coatings with good thermal properties across the automotive, aerospace, oil and gas, and consumer product industries. The silicon content imparts strength and castability while the aluminum provides ductility and corrosion resistance. |
---|---|
Q: Is aluminum silicon alloy powder safe to handle? | A: Like any fine metal powder, aluminum silicon powders can pose dust explosion hazards under certain conditions of powder concentration, oxygen levels, moisture, etc. Proper protective equipment for handling powders safely along with measures like inert gas blanketing and safety ventilation helps mitigate any risks and allows safe powder operations. |
Q: Does aluminum silicon alloy powder require heat treatment? | A: Certain aluminum silicon alloys like 6061 rely on heat treatment like solution annealing and aging to achieve optimal mechanical properties. Other alloys such as AlSi10Mg obtain decent right-out-of-printer properties with minimal post-processing whereas Scalmalloy is designed for high strength without heat treatments. The specific alloy composition and intended application guides the need for any thermal conditioning. |
Q: What particle size is best suited for aluminum silicon alloy powder AM? | A: For powder bed fusion methods in metal additive manufacturing, the typical aluminum silicon alloy powder size range is 15-100 microns. Finer particles below around 10 microns can be challenging to process and may pose dust hazards whereas larger particles above 150 microns negatively impact resolution, surface finish and deposit porosity. Within 15-100 microns, particle size distribution tailored to the machine and intended application optimizes AM processing. |
Q: Can aluminum silicon alloys be 3D printed? | A: Yes, common aluminum silicon alloys including AlSi10Mg, 6061, Scalmalloy, and A357 can be processed using major metal additive manufacturing methods such as laser powder bed fusion (LPBF), electron beam melting (EBM) and directed energy deposition (DED). Parameters are tailored for alloy compatibility with temperatures, atmospheres, heating/cooling rates, and post-processing specifically optimized for high-density components. |
Q: What is the hardness of aluminum silicon alloy? | A: The hardness of aluminum silicon alloys varies based on silicon content and heat treatment ranging between approximately 73-120 HB (Brinell hardness). As-built hardness values of some common compositions are 75-90 HB for AlSi10Mg, 85-105 HB for A357 cast alloy and 87-93 HB for 6061 alloy. Age hardening can further increase hardness over 100 HB. Higher silicon increases yield strength and hardness. |