Iron based alloy powders refer to powder metallurgy materials composed primarily of iron with the addition of alloying elements like nickel, molybdenum, copper and cobalt. They exhibit superior properties compared to plain iron powders and are widely used across industrial applications requiring high strength, wear resistance, magnetism etc.
Overview of Iron Based Alloy Powder
Iron based alloy powder is a versatile material with properties tailored as per composition and manufacturing process. Key traits of iron alloy powder include:
- High strength and hardness
- Good ductility and toughness
- Wear and abrasion resistance
- Magnetic properties
- Controlled thermal expansion
- Resistance to oxidation and corrosion
- Cost effectiveness
With the right alloying elements, iron powders can be customized to meet the needs of various end-use applications in automotive components, filtration systems, magnets, cutting tools, ball bearings and several other industries.
Types of Iron Based Alloy Powder
There are several alloying elements used with iron powder to produce powders with specific properties required for different applications.
Common alloy powders include:
Alloy Powder | Alloying Elements | Key Properties |
---|---|---|
Iron-Nickel | Nickel (Up to 50%) | High permeability, low coercivity – used in magnetic applications |
Iron-Copper | Copper (Up to 10%) | High strength, thermal and electrical conductivity |
Iron-Molybdenum | Molybdenum (Up to 8%) | Strength, wear resistance, high temperature strength |
Iron-Phosphorus | Phosphorus (Up to 1%) | Good machinability, self-lubricating properties |
Iron-Silicon | Silicon (Up to 6%) | High hardness and wear resistance |
Stainless steel | Chromium, Nickel | Corrosion and oxidation resistance |
Characteristics of Iron Based Alloy Powders
Iron alloy powders cover a wide spectrum of powder sizes, shapes, densities and microstructures. Key characteristics include:
- Particle size – Ranging from 10 microns to 200 microns depending on application
- Morphology – Irregular, spherical, annular and sponge shapes available
- Apparent density – 2 g/cc to 4 g/cc typical
- Flowability – Effects pressing and compacting behavior
- Compressibility – Determines final part density
- Pressability – Impacts formability into complex shapes
Proper selection of powder characteristics ensures optimal processing behavior during shaping operations like pressing and sintering.
Applications of Iron Based Alloy Powder
Thanks to their versatility, iron based alloy powders are consumed in large volumes across the following industries:
Automotive
- Engine parts like camshafts, gears
- Chassis and drivetrain components
- Brake pads, brake rotors
- Oil filters
Industrial
- Cutting tools, drill bits
- Bearings, bushings
- Machining parts
- Wear plates, guides
Electronics
- Ferrite magnet cores
- Inductor cores
- Electromagnetic shielding
Consumer goods
- Magnets, motors
- Locks, keys, handles
- Appliance parts
- Decorative hardware
Whether strength, wear resistance, magnetism, machinability or lubricity is required, there exists an iron alloy powder tailored to meet the needs.
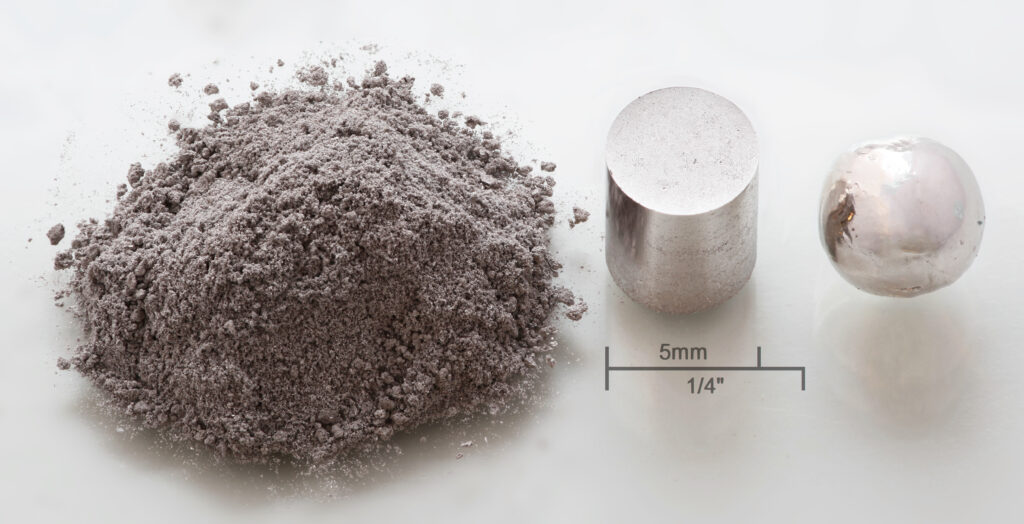
How Iron Alloy Powder Parts are Manufactured
Iron based alloy powder parts follow the conventional powder metallurgy route involving:
1. Compacting: Compression molding of the powder in a die cavity under pressures of 5-20 tons/sq. inch. The “green” compact now holds the shape.
2. Sintering: Heating the compact to just below melting point (1100-1300 deg C) to bond the particles metallurgically. This achieves final strength.
Optional steps like sizing, coining, machining, surface treatments etc. can further enhance the properties of the finished component.
The flexibility of powder metallurgy allows complex part geometries to be mass produced to tight dimensional tolerances. It is also a more material efficient process than machining.
Specifications and Design Standards
Iron alloy powder parts are designed as per the following guidelines and standards:
Density
- Green density: 6.0-7.2 g/cc
- Sintered density: 6.8-7.3 g/cc
Dimensional tolerances
- As per ISO 2768 standards for powder metallurgy parts
- +- 0.5% is achievable
Mechanical properties
- Tensile strength: up to 1000 MPa
- Hardness: up to 60 HRC
- Impact strength: up to 15 kJ/m2
Magnetic properties (for magnetic alloys)
- Saturation induction: Up to 2.4 Tesla
- Coercivity: 2-10 Oersted
- Permeability: Up to 600 u
Design and performance standards
- ISO 4902:2000 for structural PM parts
- ASTM standards for chemistry, microstructure, density
- Application specific standards
By selecting the right powder composition and process parameters, the alloy powder part can be tailored to meet the design specs.
Alloy Powder Manufacturers and Suppliers
Leading global suppliers of iron based alloy powder include:
Company | Key Products | Production Capacity |
---|---|---|
Höganäs AB | Iron, stainless, soft magnetic alloys | Over 500,000 tonnes |
GKN Sinter Metals | Pre-alloyed, diffusion bonded alloys | 40,000 tonnes |
AMES | Low alloy and stainless steel powder | 35,000 tonnes |
JFE Steel Corp | Iron-copper, iron-nickel alloys | 20,000 tonnes |
Rio Tinto Metal Powders | Nickel iron, iron powders | 75,000 tonnes |
Indicative Pricing
Alloy Powder | Price Range |
---|---|
Iron-nickel | $5-10 per kg |
Iron-copper | $15-25 per kg |
Stainless steel | $12-18 per kg |
Low alloy steel | $5-15 per kg |
Prices depend on order volumes, powder characteristics and base metal prices which fluctuate. Get latest price quotes from shortlisted suppliers.
How to Select an Alloy Powder Supplier
Choosing the right alloy powder supplier is crucial for part quality and performance. Below are key selection criteria:
- Powder range: Offers a wide range of alloy grades and powder sizes/shapes
- Quality standards: Powder production as per ISO 9001, ISO 14001 standards
- Technical expertise: Provides powder selection advice and technical support during trials
- Customization: Ability to customize powder composition and characteristics
- R&D capabilities: Invests in developing new powder grades and compositions
- Manufacturing facilities: Modern powder production technologies and metal analysis capabilities
- Delivery: Timely delivery of powders in desired packaging and quantities
- Pricing: Cost competitiveness, minimum order quantities and payment terms
- Post-sales support: Process and application troubleshooting assistance
Shortlist suppliers who meet the above prerequisites. Conduct trial orders before large volume commitments.
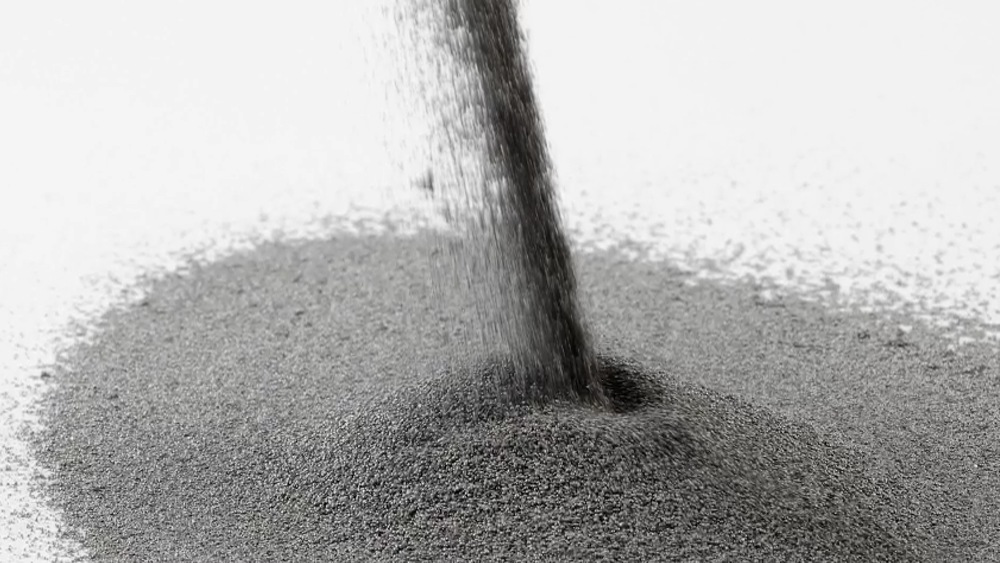
Pros and Cons of Iron Alloy Powder Parts
Advantages
- Wide range of alloy choices for tailored properties
- Higher strength relative to iron and steel
- Complex geometries can be mass produced
- Consistent quality and dimensional accuracy
- Low machining requirements and material waste
- Cost effective versus wrought counterparts
- Simplified manufacturing process
Limitations
- Limited size capabilities, typically under 2 kg
- Lower ductility than wrought alloys
- May require post-sintering operations
- Surface finish inferior to machined parts
- Porosity may be an issue in some grades
- Less thermally conductive than steel
- Requires specialized powder metallurgy equipment
The pros generally outweigh the cons for most applications of iron alloy powder metallurgy. Continued advances in alloys and processes further improve the capabilities.
Installation, Operation and Maintenance
For optimal performance, iron alloy powder parts must be handled, installed and maintained properly:
- Handle finished parts carefully to avoid damage
- Clean oil, dirt, or temporary coatings from parts before installation
- Ensure mating parts and housing areas are clean and free of burrs
- Apply lubrication if required especially during initial run-in period
- Tighten all assembly bolts and screws as per specified torque levels
- Operate within the recommended temperature range of the alloy grade
- Prevent excessive impacts which can cause cracks or fractures
- Use suitable corrosion inhibiting coatings if operated in wet conditions
- Periodically inspect parts for wear, cracks or damage and replace as needed
- Re-lubricate moving assemblies at appropriate service intervals
Adhering to the manufacturer’s instructions ensures reliable and consistent performance over the service life.
How to Choose an Iron Alloy Powder for Your Application
Selecting the optimal iron alloy powder depends on your production method and end-use requirements:
1. Determine required properties
Consider the strength, wear resistance, magnetic, thermal, electrical or other needs. This establishes the baseline.
2. Shortlist candidate alloys
Based on the required material properties, make a list of prospective iron alloy grades.
3. Evaluate feasibility of production method
Assess if your process (pressing, sintering etc.) is suitable for the shortlisted alloys.
4. Compare costs
Determine which alloy delivers the target properties at the lowest powder cost.
5. Confirm end-use suitability
Validate that the final chosen alloy meets the performance, life and reliability needs.
6. Conduct prototyping and testing
Make prototypes from the selected alloy and test them to confirm properties.
Choosing an application-specific alloy powder avoids over or under engineering and results in cost-optimized parts. Consult powder experts for guidance.
Iron Based Alloy Powder Parts – The Future
Iron alloy powder metallurgy has witnessed significant growth owing to rising demand combined with advances in powder production, equipment and process technologies.
Ongoing developments include:
- New pre-alloyed and diffusion bonded powders with enhanced properties
- Use of atomization methods for finer powders
- Innovation in powder pressing and tooling
- Faster sintering furnaces and techniques
- Post-sintering operations for higher precision and surface finish
- Software for simulation and modeling
- Customization of alloys tailored to customer needs
These improvements will expand the horizons of iron based alloy powder applications in the automotive, industrial, consumer goods and specialty industries going forward.
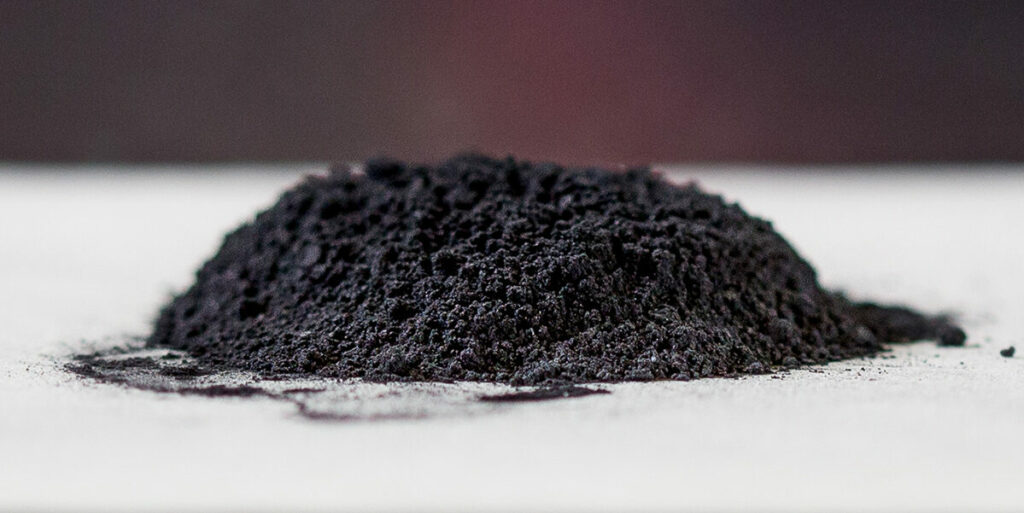
FAQ
Q: What are the main advantages of iron alloy powders over iron powders?
A: Iron alloy powders exhibit higher strength, wear resistance, magnetic properties, corrosion resistance and other enhanced properties from their alloying elements. This allows tailored materials as per the application.
Q: What effect does powder size have on the final part?
A: Finer powders below 30 microns fill the die cavity more densely during pressing. This results in higher final part density and mechanical properties. However, too fine powders have lower compressibility.
Q: How to improve strength of iron alloy PM parts?
A: Use finer powders, optimized pressing and sintering parameters. Secondary operations like sizing and coining further increase part density and strength. Also, choose alloys with higher hardenability.
Q: What is the benefit of pre-alloyed powders?
A: Pre-alloyed powders have uniform distribution of the alloying elements resulting in consistent properties throughout the part vs. blended elemental powders.
Q: How to minimize risk when adopting new iron alloy grades?
A: Work closely with your powder supplier during material selection stage as well as prototyping trials. Follow recommended pressing and sintering guidelines. Confirm all properties via testing.
Q: What causes dimensional growth in sintered iron alloy parts?
A: Excessive temperature or long sintering times can cause grain growth leading to swelling. Use recommended thermal cycles and keep sintering periods minimal.
Q: How to improve surface finish of pressed and sintered parts?
A: Secondary operations like coining, repressing or machining result in smoother surfaces. Complex powder shapes also increase density at the surface.
Q: What are common defects in iron alloy PM parts?
A: Lack of density, porosity, cracks, undersize, distortion, inclination and other defects can occur due to faulty powder, compaction issues or poor sintering practice.
Q: What is the benefit of iron-copper versus iron-nickel alloys?
A: Iron-copper gives higher strength while iron-nickel offers superior magnetic properties. Choose as per whether mechanical strength or magnetism is required.
Q: What alloy is suitable for automotive transmission gears?
A: Iron-copper alloys with up to 4% copper are ideal for gear applications needing a balance of strength, fatigue life and wear resistance.