Binder jet 3D printing is a fascinating technology that’s rapidly gaining popularity in the manufacturing world. If you’ve ever wondered about how this technology works, what materials it uses, and where it’s applied, you’re in the right place. Let’s dive deep into the world of binder jet 3D printing, breaking down its complexities and highlighting its unique advantages and limitations.
Overview of Binder Jet 3D Printing
Binder jet 3D printing, often referred to simply as binder jetting, is an additive manufacturing process. Unlike traditional 3D printing methods that use heat to fuse materials together, binder jetting involves the selective deposition of a liquid binding agent onto a powder bed. The binding agent glues the powder particles together, layer by layer, to form a solid part.
How Does Binder Jet 3D Printing Work?
Think of binder jetting like building a sandcastle. Imagine layering wet sand to create intricate shapes – binder jetting follows a similar principle. Here’s a step-by-step look at the process:
- Powder Spreading: A thin layer of powder (metal, ceramic, or plastic) is spread over the build platform.
- Binder Deposition: Print heads selectively deposit the binding agent onto the powder bed according to the digital model.
- Layering: This process is repeated layer by layer until the part is fully formed.
- Curing: The printed part is then cured to solidify the binder.
- Post-Processing: The final steps include depowdering, sintering, and any additional finishing processes needed to achieve the desired properties.
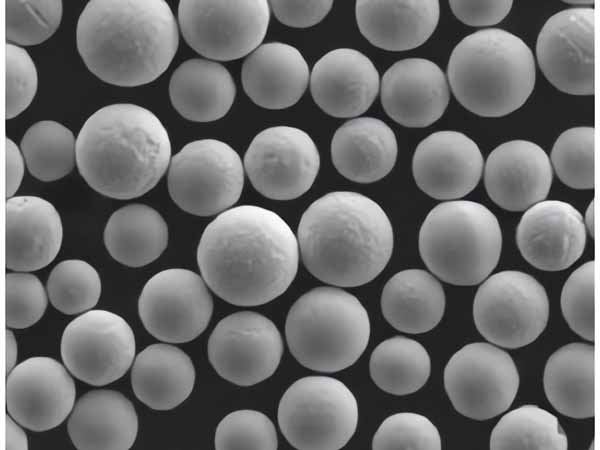
Types of Metal Powders Used in Binder Jet 3D Printing
In binder jet 3D printing, the choice of metal powder is crucial. Here are some commonly used metal powders:
Metal Powder | Description |
---|---|
Stainless Steel 316L | Highly resistant to corrosion, commonly used in medical devices, automotive, and aerospace applications. |
Inconel 625 | Known for its high strength and resistance to oxidation and corrosion, often used in high-temperature environments like gas turbines. |
Inconel 718 | Offers excellent mechanical properties at high temperatures, widely used in the aerospace industry. |
Copper | Excellent thermal and electrical conductivity, ideal for electrical components and heat exchangers. |
Tool Steel (H13) | High hardness and wear resistance, suitable for manufacturing tools and dies. |
Aluminum Alloy 6061 | Lightweight with good mechanical properties, used in automotive and aerospace industries. |
Titanium Alloy (Ti6Al4V) | High strength-to-weight ratio, corrosion-resistant, extensively used in aerospace, medical implants, and high-performance applications. |
Nickel Alloy 625 | Combines high strength, outstanding fatigue, and thermal-fatigue resistance, oxidation, and corrosion resistance, used in marine and chemical industries. |
Cobalt-Chrome | High wear resistance and biocompatibility, often used for medical implants and dental applications. |
Bronze | Good conductivity and historical value, used in art and decorative items, as well as bushings and bearings. |
Composition of Binder Jet 3D Printing Materials
Understanding the composition of the materials used in binder jetting is essential. Here’s a closer look at some of the key components and their properties:
Material | Composition | Properties |
---|---|---|
Stainless Steel 316L | Iron, Chromium, Nickel, Molybdenum | Corrosion-resistant, high tensile strength |
Inconel 625 | Nickel, Chromium, Molybdenum, Niobium | High strength, oxidation and corrosion-resistant |
Inconel 718 | Nickel, Chromium, Iron, Niobium, Molybdenum | Excellent mechanical properties at high temperatures |
Copper | Pure Copper | Excellent thermal and electrical conductivity |
Tool Steel (H13) | Iron, Chromium, Molybdenum, Vanadium | High hardness, wear resistance |
Aluminum Alloy 6061 | Aluminum, Magnesium, Silicon | Lightweight, good mechanical properties |
Titanium Alloy (Ti6Al4V) | Titanium, Aluminum, Vanadium | High strength-to-weight ratio, corrosion-resistant |
Nickel Alloy 625 | Nickel, Chromium, Molybdenum, Niobium | High strength, corrosion-resistant |
Cobalt-Chrome | Cobalt, Chromium, Molybdenum | High wear resistance, biocompatibility |
Bronze | Copper, Tin | Good conductivity, high historical value |
Characteristics of Binder Jet 3D Printing
Binder jetting stands out from other additive manufacturing technologies due to its unique characteristics:
- Speed: Binder jetting is faster compared to other 3D printing methods because it doesn’t require a thermal process during printing.
- Material Versatility: Can use a wide range of materials, including metals, ceramics, and even sand.
- No Supports Needed: Unlike other 3D printing methods, binder jetting does not require support structures.
- Lower Cost: Generally more cost-effective, especially for large parts and high-volume production.
Applications of Binder Jet 3D Printing
Binder jetting is versatile and used across various industries. Here are some common applications:
Industry | Application |
---|---|
Automotive | Prototyping, production of complex metal parts |
Aerospace | Lightweight components, turbine blades |
Medical | Customized implants, dental prosthetics |
Art & Jewelry | Intricate designs, customized pieces |
Industrial | Tooling, functional prototypes |
Consumer Goods | Customized products, functional prototypes |
Specifications, Sizes, Grades, and Standards
When it comes to binder jet 3D printing, knowing the specifications, sizes, grades, and standards is crucial for achieving the desired results. Here’s a comprehensive table:
Parameter | Details |
---|---|
Powder Particle Size | 15-45 microns for metals |
Layer Thickness | 50-200 microns |
Build Volume | Up to 800 x 500 x 400 mm |
Tolerance | +/- 0.1 mm (depends on the material) |
Density | 60-95% (depends on post-processing) |
Standards | ASTM, ISO |
Suppliers and Pricing Details
Understanding the market landscape is essential. Here’s a look at some key suppliers and an idea of the pricing:
Supplier | Material | Price Range (per kg) |
---|---|---|
ExOne | Stainless Steel 316L | $80 – $120 |
Desktop Metal | Inconel 625 | $100 – $150 |
Höganäs | Copper | $50 – $80 |
3DEO | Tool Steel (H13) | $90 – $130 |
GE Additive | Titanium Alloy (Ti6Al4V) | $300 – $400 |
HP 3D Printing | Aluminum Alloy 6061 | $60 – $100 |
Voxeljet | Bronze | $70 – $110 |
Pros and Cons of Binder Jet 3D Printing
Here’s a detailed comparison of the advantages and limitations of binder jet 3D printing:
Aspect | Advantages | Limitations |
---|---|---|
Speed | Faster printing process | Post-processing required |
Cost | Lower cost per part, especially for large volumes | Initial setup cost can be high |
Material Variety | Wide range of materials | Not all materials are equally available |
Complexity | Can produce highly complex geometries without supports | Mechanical properties may be inferior to other methods |
Finish | Good surface finish with post-processing | Sintering can cause shrinkage and warping |
Comparing Binder Jet 3D Printing to Other 3D Printing Methods
Let’s compare binder jetting with other popular 3D printing technologies like SLM (Selective Laser Melting) and SLS (Selective Laser Sintering):
Aspect | Binder Jetting | SLM | SLS |
---|---|---|---|
Speed | Faster | Slower due to layer-by-layer melting | Moderate |
Cost | Generally lower | Higher | Moderate |
Material Range | Broad (metals, ceramics, sand) | Mostly metals | Plastics, some metals |
Surface Finish | Good with post-processing | Excellent | Good with post-processing |
Strength | Lower compared to SLM | High | Moderate |
Heat Requirement | No heat during printing | High heat required | Moderate heat required |
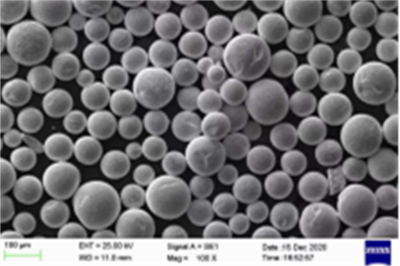
FAQs
Here are some frequently asked questions about binder jet 3D printing to help clear up any remaining queries:
Question | Answer |
---|---|
What is binder jet 3D printing? | It’s an additive manufacturing process where a liquid binder is deposited onto a powder bed to create parts. |
What materials can be used? | Metals, ceramics, and even sand can be used in binder jetting. |
How fast is binder jetting? | It’s generally faster than other 3D printing methods because it doesn’t use heat during printing. |
What are the main applications? | Automotive, aerospace, medical, art, and industrial applications are common. |
Is post-processing necessary? | Yes, post-processing like curing, depowdering, and sintering is often required. |
What are the benefits? | Speed, cost-effectiveness, and the ability to produce complex geometries without supports. |
What are the limitations? | Mechanical properties might be lower compared to other methods, and post-processing is needed. |
How does it compare to SLM and SLS? | Binder jetting is faster and more cost-effective but may offer lower strength compared to SLM. |
What is the cost of materials? | Material costs vary widely, from $50 per kg for copper to $400 per kg for titanium alloys. |
Who are the key suppliers? | ExOne, Desktop Metal, Höganäs, and GE Additive are some notable suppliers. |
Conclusion
Binder jet 3D printing is a powerful and versatile technology that opens up numerous possibilities in manufacturing. With its ability to quickly produce complex parts from a wide range of materials, it’s no wonder this technology is gaining traction across various industries. Whether you’re in automotive, aerospace, or even art and jewelry, binder jetting offers unique advantages that can revolutionize the way you approach production. So, why not dive into this fascinating world and see how it can benefit your next project?