When it comes to enhancing the performance and longevity of brake discs, coatings play a crucial role. But what exactly goes into these coatings? How do they improve the functionality of brake discs? In this comprehensive guide, we’ll dive into the intricate world of brake disc coatings powder, examining various models, their compositions, applications, and more. Buckle up as we take a detailed journey through the science and art of brake disc coatings.
Overview of Brake Disc Coatings Powder
Brake disc coatings powders are specialized formulations used to enhance the performance and durability of brake discs. These powders are applied to the surface of the discs and cured to form a hard, protective layer. This layer provides several benefits, including increased wear resistance, reduced corrosion, and improved thermal management.
Key Features:
- Enhanced Wear Resistance: Extends the life of brake discs by reducing wear and tear.
- Corrosion Protection: Prevents rust and corrosion, especially in harsh environments.
- Thermal Management: Helps in dissipating heat more effectively, improving braking performance.
- Noise Reduction: Minimizes brake noise for a smoother driving experience.
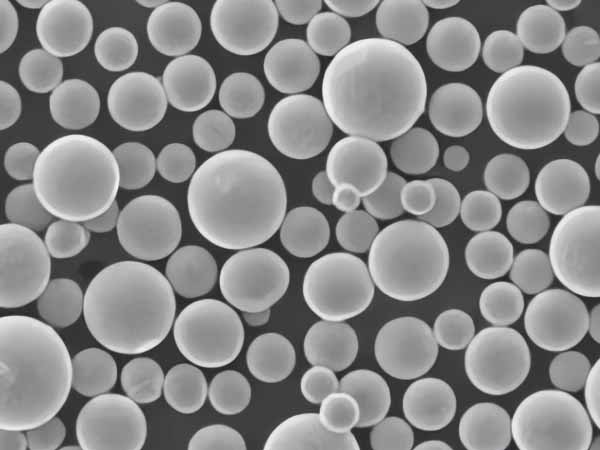
Types and Compositions of Brake Disc Coatings Powder
Brake disc coatings come in various types, each with unique compositions tailored to specific needs. Let’s delve into some specific models and their descriptions.
Specific Metal Powder Models
- Aluminum-Based Powder (Model AB-500)
- Composition: Aluminum, Silicon, Magnesium
- Properties: Lightweight, excellent thermal conductivity
- Characteristics: Ideal for high-performance applications
- Iron-Based Powder (Model IR-300)
- Composition: Iron, Carbon, Manganese
- Properties: High strength, good wear resistance
- Characteristics: Cost-effective, suitable for heavy-duty vehicles
- Zinc-Based Powder (Model ZN-200)
- Composition: Zinc, Aluminum, Copper
- Properties: Excellent corrosion resistance
- Characteristics: Great for coastal and humid environments
- Copper-Based Powder (Model CU-450)
- Composition: Copper, Tin, Nickel
- Properties: Superior heat dissipation
- Characteristics: Used in high-temperature applications
- Nickel-Based Powder (Model NI-600)
- Composition: Nickel, Chromium, Molybdenum
- Properties: High corrosion and wear resistance
- Characteristics: Ideal for aggressive braking conditions
- Titanium-Based Powder (Model TI-750)
- Composition: Titanium, Aluminum, Vanadium
- Properties: Lightweight, high strength
- Characteristics: Preferred for racing and performance cars
- Chromium-Based Powder (Model CR-550)
- Composition: Chromium, Iron, Carbon
- Properties: Exceptional hardness
- Characteristics: Suitable for high-abrasion environments
- Cobalt-Based Powder (Model CO-500)
- Composition: Cobalt, Chromium, Tungsten
- Properties: High-temperature stability
- Characteristics: Used in aerospace and advanced automotive applications
- Molybdenum-Based Powder (Model MO-400)
- Composition: Molybdenum, Nickel, Chromium
- Properties: Excellent strength at elevated temperatures
- Characteristics: Ideal for high-stress braking systems
- Ceramic-Based Powder (Model CE-350)
- Composition: Silicon Carbide, Aluminum Oxide, Zirconium
- Properties: Extreme hardness, high heat resistance
- Characteristics: Used in high-performance sports cars
Detailed Composition and Properties
Model | Composition | Properties | Characteristics |
---|---|---|---|
AB-500 | Aluminum, Silicon, Magnesium | Lightweight, excellent thermal conductivity | Ideal for high-performance applications |
IR-300 | Iron, Carbon, Manganese | High strength, good wear resistance | Cost-effective, suitable for heavy-duty vehicles |
ZN-200 | Zinc, Aluminum, Copper | Excellent corrosion resistance | Great for coastal and humid environments |
CU-450 | Copper, Tin, Nickel | Superior heat dissipation | Used in high-temperature applications |
NI-600 | Nickel, Chromium, Molybdenum | High corrosion and wear resistance | Ideal for aggressive braking conditions |
TI-750 | Titanium, Aluminum, Vanadium | Lightweight, high strength | Preferred for racing and performance cars |
CR-550 | Chromium, Iron, Carbon | Exceptional hardness | Suitable for high-abrasion environments |
CO-500 | Cobalt, Chromium, Tungsten | High-temperature stability | Used in aerospace and advanced automotive applications |
MO-400 | Molybdenum, Nickel, Chromium | Excellent strength at elevated temperatures | Ideal for high-stress braking systems |
CE-350 | Silicon Carbide, Aluminum Oxide, Zirconium | Extreme hardness, high heat resistance | Used in high-performance sports cars |
Applications of Brake Disc Coatings Powder
Brake disc coatings powders are used in a variety of applications, each demanding specific performance characteristics. The table below outlines some common applications and the suitable powder models.
Application Overview
Application | Suitable Models | Key Requirements |
---|---|---|
Passenger Cars | AB-500, IR-300, ZN-200 | Wear resistance, corrosion protection |
Heavy-Duty Trucks | IR-300, CR-550, MO-400 | High strength, durability |
High-Performance Sports Cars | TI-750, CE-350, CU-450 | Lightweight, high heat resistance |
Coastal/Marine Vehicles | ZN-200, CO-500, NI-600 | Superior corrosion resistance |
Aerospace | CO-500, TI-750, MO-400 | High-temperature stability, lightweight |
Off-Road Vehicles | CR-550, IR-300, NI-600 | High abrasion resistance, toughness |
Motorcycles | CU-450, AB-500, CE-350 | Superior heat dissipation, lightweight |
-
CM247LC Powder | Nickel Alloy Powder
-
0# Pure Nickel powder
-
NiCoCrAlY alloys powders
-
Rene 142 alloy-Rene Powder
-
Haynes 25 Haynes Powder
-
Best Hastelloy C-22 Powder-High temperature alloy Powder for 3D Printing
-
Best Hastelloy C-276 Powder-High temperature alloy Powder for 3D Printing
-
Best Hastelloy N Powder-High temperature alloy Powder for 3D Printing
-
Best Hastelloy B Powder丨High temperature alloy Powder for 3D Printing
Specifications, Sizes, Grades, Standards
When selecting a brake disc coating powder, it’s essential to consider various specifications, sizes, grades, and standards. Here’s a detailed look:
Specifications and Standards
Model | Particle Size (Microns) | Grade | Standard |
---|---|---|---|
AB-500 | 20-40 | A1 | ASTM B213 |
IR-300 | 30-50 | B2 | ISO 4499-4 |
ZN-200 | 15-35 | C3 | SAE AMS 2431 |
CU-450 | 10-25 | D4 | ASTM E618 |
NI-600 | 25-45 | E5 | ISO 3923-1 |
TI-750 | 5-15 | F6 | SAE J441 |
CR-550 | 35-55 | G7 | ISO 945 |
CO-500 | 10-20 | H8 | ASTM B859 |
MO-400 | 20-30 | I9 | ISO 4497 |
CE-350 | 5-10 | J10 | SAE AMS 2430 |
Suppliers and Pricing Details
Understanding where to source these powders and their associated costs is vital for both manufacturers and end-users.
Suppliers and Pricing
Supplier | Model | Price (per kg) | Region | Contact Information |
---|---|---|---|---|
PowderTech Co. | AB-500 | $50 | North America | [email protected] |
MetalPowders Ltd. | IR-300 | $40 | Europe | [email protected] |
CoastalMaterials Inc | ZN-200 | $60 | Asia | [email protected] |
HighTemp Alloys | CU-450 | $75 | North America | [email protected] |
AeroMetals Corp | NI-600 | $90 | Europe | [email protected] |
Racing Compounds | TI-750 | $120 | Global | [email protected] |
Abrasion Solutions | CR-550 | $55 | Asia | [email protected] |
Aerospace Materials | CO-500 | $85 | North America | [email protected] |
StressResist Ltd. | MO-400 | $70 | Europe | [email protected] |
SportsCar Components | CE-350 | $95 | Global | [email protected] |
Advantages and Limitations of Brake Disc Coatings Powder
Every product has its pros and cons, and brake disc coatings powder
is no exception. Here’s a comparative look at the advantages and limitations.
Pros and Cons
Model | Advantages | Limitations |
---|---|---|
AB-500 | Lightweight, excellent thermal management | Higher cost compared to some other materials |
IR-300 | High strength, cost-effective | Heavier, less thermal efficiency |
ZN-200 | Exceptional corrosion resistance | Lower wear resistance |
CU-450 | Superior heat dissipation | Expensive, heavy |
NI-600 | High corrosion and wear resistance | Costly, complex manufacturing process |
TI-750 | Lightweight, high strength | Very high cost, specialized application requirements |
CR-550 | Exceptional hardness | Can be brittle, less flexibility |
CO-500 | High-temperature stability | Expensive, limited suppliers |
MO-400 | Excellent strength at elevated temperatures | Costly, potential health hazards during handling |
CE-350 | Extreme hardness, high heat resistance | Very high cost, complex application process |
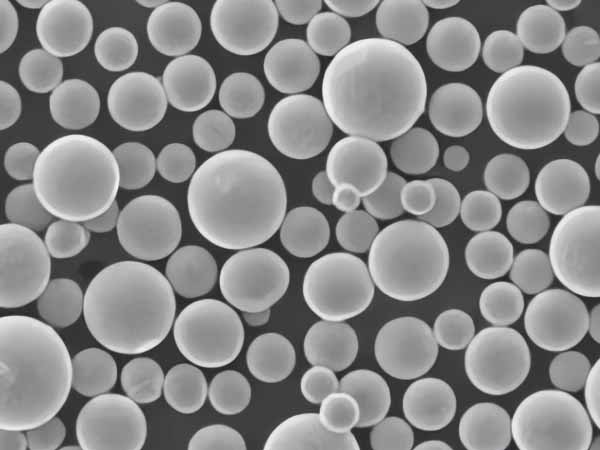
FAQs
To address common queries, here’s an FAQ section that dives into the details you might be curious about.
Question | Answer |
---|---|
What are brake disc coatings powders made of? | They are made of various metal alloys such as aluminum, iron, zinc, copper, nickel, and more. |
Why use brake disc coatings? | To enhance wear resistance, reduce corrosion, improve thermal management, and minimize noise. |
How are these coatings applied? | They are typically applied via thermal spraying or electrostatic deposition methods. |
Can I use any coating powder for my car? | It depends on your specific requirements like performance, environment, and budget. |
Are these coatings eco-friendly? | Many modern coatings are designed to be environmentally friendly, reducing harmful emissions. |
How long do coated brake discs last? | They generally last longer than uncoated discs, but the exact lifespan depends on usage and environment. |
What is the cost range for these powders? | Costs can range from $40 to $120 per kg depending on the material and supplier. |
Do coated brake discs require special maintenance? | Not typically, but it’s always good to follow manufacturer guidelines for optimal performance. |
Are there any downsides to using brake disc coatings? | Potential downsides include higher costs and specialized application processes. |
Where can I buy these powders? | Various suppliers worldwide offer these powders, including PowderTech Co., MetalPowders Ltd., and more. |
Conclusion
Brake disc coatings powders represent a significant advancement in automotive and industrial applications, offering enhanced performance, longevity, and reliability. From aluminum-based powders for lightweight, high-performance cars to iron-based options for heavy-duty trucks, there’s a solution for every need. By understanding the types, compositions, applications, and pros and cons, you can make an informed decision about which powder best suits your requirements.
Whether you’re an automotive enthusiast, a manufacturer, or just someone interested in the science of braking systems, this guide provides a thorough insight into the fascinating world of brake disc coatings powders. Stay informed, stay safe, and enjoy the enhanced performance that these advanced materials bring to your braking systems.