Overview
The centrifugal atomization process is a fascinating method used primarily in the production of metal powders. This technique involves the disintegration of molten metal into fine droplets using centrifugal forces. The droplets then solidify into powder particles, which are essential in various industries, from aerospace to automotive. In this article, we will delve into the intricate details of the centrifugal atomization process, explore different metal powder models, and discuss their applications, properties, advantages, and limitations. By the end, you’ll have a thorough understanding of this remarkable process and its significance in modern manufacturing.
What is the Centrifugal Atomization Process?
Centrifugal atomization is a metal powder production technique that leverages centrifugal forces to fragment molten metal. The process typically involves a rotating disk or a rapidly spinning container, which throws the molten metal outward. As the metal travels away from the center, it breaks into fine droplets due to the centrifugal force and surface tension. These droplets then cool and solidify into fine metal powders.
Key Steps in the Centrifugal Atomization Process:
- Melting the Metal: The process starts with melting the metal or alloy.
- Rotating Disk/Container: The molten metal is fed onto a rapidly spinning disk or into a rotating container.
- Droplet Formation: Centrifugal forces cause the molten metal to disintegrate into droplets.
- Solidification: The droplets cool down and solidify into powder particles.
- Collection: The fine metal powders are collected for further processing or direct use.
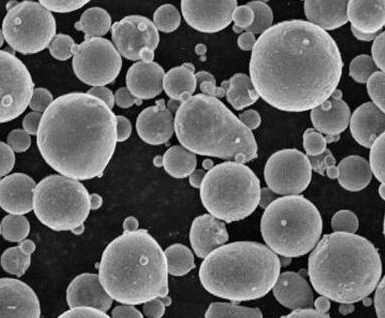
Specific Metal Powder Models
Let’s explore ten specific metal powder models produced through centrifugal atomization, detailing their composition, properties, and typical applications.
Metal Powder Model | Composition | Properties | Applications |
---|---|---|---|
Stainless Steel 316L | Fe, Cr, Ni, Mo | High corrosion resistance, good weldability, high ductility | Medical devices, aerospace components, marine hardware |
Aluminum 6061 | Al, Mg, Si | Lightweight, high strength, good corrosion resistance | Automotive parts, aerospace structures, marine equipment |
Titanium Ti-6Al-4V | Ti, Al, V | High strength-to-weight ratio, excellent corrosion resistance, biocompatibility | Aerospace, biomedical implants, marine applications |
Copper Cu-ETP | Cu, small amounts of O | High electrical conductivity, good thermal conductivity, excellent formability | Electrical components, heat exchangers, plumbing |
Nickel Alloy 718 | Ni, Cr, Fe, Nb, Mo, Ti, Al | High strength, excellent high-temperature performance, good corrosion resistance | Turbine blades, aerospace engines, nuclear reactors |
Cobalt-Chromium (CoCr) | Co, Cr, Mo | High wear resistance, good corrosion resistance, high strength | Medical implants, dental prosthetics, aerospace components |
Tool Steel D2 | Fe, Cr, Mo, V | High hardness, excellent wear resistance, good toughness | Cutting tools, dies, molds |
Inconel 625 | Ni, Cr, Mo, Nb | High strength, excellent fatigue and thermal fatigue resistance, good corrosion resistance | Aerospace engines, chemical processing, marine hardware |
Magnesium AZ31 | Mg, Al, Zn | Very lightweight, good strength, excellent machinability | Aerospace components, automotive parts, electronics |
Iron FE-PM | Fe, small amounts of C, Si, Mn | Good strength, excellent wear resistance, cost-effective | Automotive parts, machinery components, industrial tools |
Properties and Characteristics of Metal Powders
Stainless Steel 316L
- Composition: Iron (Fe), Chromium (Cr), Nickel (Ni), Molybdenum (Mo)
- Properties: Stainless Steel 316L offers high corrosion resistance, excellent weldability, and good ductility. It is often used in environments that require high resistance to pitting and crevice corrosion, such as marine applications.
- Applications: Commonly used in medical devices, aerospace components, and marine hardware.
Aluminum 6061
- Composition: Aluminum (Al), Magnesium (Mg), Silicon (Si)
- Properties: Known for its lightweight nature and high strength, Aluminum 6061 also provides good corrosion resistance. It is easily machinable and weldable.
- Applications: Widely used in automotive parts, aerospace structures, and marine equipment.
Titanium Ti-6Al-4V
- Composition: Titanium (Ti), Aluminum (Al), Vanadium (V)
- Properties: This alloy is renowned for its high strength-to-weight ratio, excellent corrosion resistance, and biocompatibility. It maintains its strength at high temperatures.
- Applications: Extensively used in aerospace, biomedical implants, and marine applications.
Copper Cu-ETP
- Composition: Copper (Cu), small amounts of Oxygen (O)
- Properties: Copper Cu-ETP is characterized by its high electrical and thermal conductivity, along with excellent formability.
- Applications: Primarily used in electrical components, heat exchangers, and plumbing systems.
Nickel Alloy 718
- Composition: Nickel (Ni), Chromium (Cr), Iron (Fe), Niobium (Nb), Molybdenum (Mo), Titanium (Ti), Aluminum (Al)
- Properties: Known for high strength, excellent performance at high temperatures, and good corrosion resistance.
- Applications: Used in turbine blades, aerospace engines, and nuclear reactors.
Cobalt-Chromium (CoCr)
- Composition: Cobalt (Co), Chromium (Cr), Molybdenum (Mo)
- Properties: This alloy offers high wear resistance, good corrosion resistance, and high strength.
- Applications: Commonly found in medical implants, dental prosthetics, and aerospace components.
Tool Steel D2
- Composition: Iron (Fe), Chromium (Cr), Molybdenum (Mo), Vanadium (V)
- Properties: Tool Steel D2 is known for its high hardness, excellent wear resistance, and good toughness.
- Applications: Used in cutting tools, dies, and molds.
Inconel 625
- Composition: Nickel (Ni), Chromium (Cr), Molybdenum (Mo), Niobium (Nb)
- Properties: Offers high strength, excellent fatigue and thermal fatigue resistance, and good corrosion resistance.
- Applications: Used in aerospace engines, chemical processing, and marine hardware.
Magnesium AZ31
- Composition: Magnesium (Mg), Aluminum (Al), Zinc (Zn)
- Properties: Magnesium AZ31 is very lightweight, with good strength and excellent machinability.
- Applications: Utilized in aerospace components, automotive parts, and electronics.
Iron FE-PM
- Composition: Iron (Fe), small amounts of Carbon (C), Silicon (Si), Manganese (Mn)
- Properties: Known for good strength, excellent wear resistance, and cost-effectiveness.
- Applications: Commonly used in automotive parts, machinery components, and industrial tools.
Applications of Centrifugal Atomization Process
The metal powders produced through the centrifugal atomization process have a wide range of applications across various industries. Let’s explore some of the key applications:
Application | Description |
---|---|
Aerospace | Used in manufacturing high-strength, lightweight components such as turbine blades and structural parts. |
Automotive | Utilized in producing durable, lightweight parts like gears, bearings, and engine components. |
Medical | Essential for creating biocompatible implants, surgical instruments, and dental prosthetics. |
Electronics | Employed in making high-conductivity components such as connectors, heat sinks, and circuit boards. |
Marine | Applied in crafting corrosion-resistant hardware and components exposed to harsh marine environments. |
Industrial Tools | Used in manufacturing high-wear-resistance tools like cutting instruments, dies, and molds. |
Energy | Important in producing high-performance components for turbines, nuclear reactors, and fuel cells. |
Specifications, Sizes, and Standards
To ensure the quality and consistency of metal powders, various specifications, sizes, and standards are adhered to during production.
Metal Powder | Particle Size Range (µm) | Purity (%) | Standards |
---|---|---|---|
Stainless Steel 316L | 10-45 | >99.5 | ASTM A276, ISO 5832-1 |
Aluminum 6061 | 20-60 | >99.8 | ASTM B211, AMS 4117 |
Titanium Ti-6Al-4V | 15-53 | >99.9 | ASTM F1472, ISO 5832-3 |
Copper Cu-ETP | 25-75 | >99.9 | ASTM B187, ISO 197-1 |
Nickel Alloy 718 | 10-45 | >99.5 | AMS 5662, ASTM B637 |
Cobalt-Chromium (CoCr) | 10-45 | >99.7 | ASTM F75, ISO 5832-4 |
Tool Steel D2 | 20-60 | >99.5 | ASTM A681, JIS G4404 |
Inconel 625 | 15-53 | >99.5 | AMS 5666, ASTM B443 |
Magnesium AZ31 | 25-75 | >99.8 | ASTM B107, AMS 4377 |
Iron FE-PM | 10-45 | >99.5 | MPIF 35, ASTM A681 |
Suppliers and Pricing Details
Here are some of the leading suppliers of metal powders produced via centrifugal atomization and their pricing details.
Supplier | Metal Powder | Price (USD/kg) | Location |
---|---|---|---|
Höganäs AB | Stainless Steel 316L | 50-70 | Sweden |
AP&C (a GE Additive company) | Titanium Ti-6Al-4V | 250-350 | Canada |
Sandvik | Nickel Alloy 718 | 150-200 | Sweden |
Praxair Surface Technologies | Inconel 625 | 180-250 | USA |
Carpenter Technology | Cobalt-Chromium (CoCr) | 200-300 | USA |
Valimet | Aluminum 6061 | 20-40 | USA |
Kennametal | Tool Steel D2 | 40-60 | USA |
Ames Laboratory | Iron FE-PM | 10-30 | USA |
Tekna Plasma Systems | Copper Cu-ETP | 50-70 | Canada |
Luxfer MEL Technologies | Magnesium AZ31 | 60-80 | USA |
Comparing Pros and Cons of Centrifugal Atomization Process
Advantages
- Uniform Particle Size: Centrifugal atomization produces powders with uniform particle size distribution, enhancing their performance in various applications.
- High Purity: The process results in high-purity metal powders, critical for applications requiring stringent material standards.
- Scalability: It is highly scalable, making it suitable for both small-scale and large-scale production.
- Versatility: Applicable to a wide range of metals and alloys, providing flexibility in material selection.
Disadvantages
- High Initial Cost: The equipment and setup costs for centrifugal atomization can be high, making it less accessible for smaller manufacturers.
- Energy Intensive: The process requires significant energy, especially for melting and atomizing high-melting-point metals.
- Complex Operation: Requires skilled operators and precise control to maintain product quality and consistency.
Application of Centrifugal Atomization Process
Centrifugal atomization finds applications in numerous industries due to its ability to produce high-quality metal powders. Here are some key applications:
Aerospace Industry
In the aerospace industry, the need for high-strength, lightweight components is paramount. Metal powders such as Titanium Ti-6Al-4V and Nickel Alloy 718 are used to manufacture turbine blades, engine components, and structural parts. These powders offer excellent mechanical properties and high-temperature performance, making them ideal for demanding aerospace applications.
Automotive Industry
The automotive industry benefits from metal powders like Aluminum 6061 and Tool Steel D2. Aluminum 6061 is utilized in producing lightweight yet strong parts, contributing to fuel efficiency and performance. Tool Steel D2 is employed in making durable, wear-resistant components such as gears, bearings, and cutting tools.
Medical Industry
Medical applications require materials that are biocompatible and corrosion-resistant. Stainless Steel 316L and Cobalt-Chromium (CoCr) powders are commonly used in medical implants, surgical instruments, and dental prosthetics. Their high strength and excellent corrosion resistance ensure longevity and reliability in the human body.
Electronics Industry
Copper Cu-ETP and Magnesium AZ31 are vital in the electronics industry. Copper’s high electrical and thermal conductivity makes it perfect for electrical components and heat exchangers. Magnesium AZ31, with its lightweight and good strength, is used in electronic housings and structural components.
Marine Industry
Marine environments demand materials with exceptional corrosion resistance. Stainless Steel 316L and Titanium Ti-6Al-4V powders are widely used in marine hardware, fasteners, and structural parts exposed to seawater. Their resistance to pitting and crevice corrosion ensures durability and longevity in harsh marine conditions.
Industrial Tools
Tool Steel D2 and Inconel 625 are essential in manufacturing high-performance industrial tools. Tool Steel D2 offers high hardness and wear resistance, making it ideal for cutting tools, dies, and molds. Inconel 625, with its excellent fatigue and thermal fatigue resistance, is used in tools exposed to extreme conditions.
Energy Sector
The energy sector relies on high-performance components for turbines, nuclear reactors, and fuel cells. Nickel Alloy 718 and Inconel 625 powders are used in these applications due to their high strength, excellent high-temperature performance, and good corrosion resistance.

FAQs
Question | Answer |
---|---|
What is centrifugal atomization? | Centrifugal atomization is a process that produces metal powders by disintegrating molten metal into fine droplets using centrifugal forces. |
What are the advantages of centrifugal atomization? | Advantages include uniform particle size, high purity, scalability, and versatility in material selection. |
What metals can be processed using centrifugal atomization? | A wide range of metals and alloys, including stainless steel, aluminum, titanium, copper, nickel alloys, cobalt-chromium, tool steel, and more. |
What industries use metal powders from centrifugal atomization? | Industries such as aerospace, automotive, medical, electronics, marine, industrial tools, and energy sectors. |
How does centrifugal atomization compare to other powder production methods? | It offers advantages like uniform particle size and high purity but can be more costly and energy-intensive compared to methods like gas atomization or water atomization. |
What are some common applications of metal powders produced by centrifugal atomization? | Applications include turbine blades, automotive parts, medical implants, electronic components, marine hardware, and industrial tools. |
Are there any limitations to the centrifugal atomization process? | Yes, limitations include high initial costs, energy-intensive operations, and the need for skilled operators and precise control. |
How is the quality of metal powders ensured in centrifugal atomization? | Quality is ensured through strict control of particle size distribution, purity levels, and adherence to industry standards. |
Can centrifugal atomization be used for both ferrous and non-ferrous metals? | Yes, it is suitable for both ferrous and non-ferrous metals. |
What are some key considerations when selecting a supplier for metal powders? | Considerations include the supplier’s reputation, quality control processes, material specifications, pricing, and location. |
Conclusion
The centrifugal atomization process is a highly effective method for producing high-quality metal powders. These powders are crucial in various industries, offering unique properties and advantages that enhance the performance of end products. By understanding the intricacies of the process, the properties of different metal powders, and their applications, manufacturers can make informed decisions to optimize their production and achieve superior results. Whether you’re in aerospace, automotive, medical, or any other industry, the centrifugal atomization process provides the precision and reliability needed for modern manufacturing.