The world of metallurgy and material processing is one that demands precision, efficiency, and advanced technology. One of the key components in the metallurgical process, particularly in induction melting, is the crucible. But not just any crucible—ceramic-lined induction crucibles stand out as the gold standard for various metal melting applications. If you’re curious about why they are so crucial, their composition, benefits, and the various types available, you’ve come to the right place.
In this detailed guide, we’ll delve into everything you need to know about ceramic-lined induction crucibles, from their intricate properties to the specific metal powders they can handle. Whether you’re a seasoned engineer, a supplier, or just someone keen on learning more about metallurgy, this article is crafted just for you.
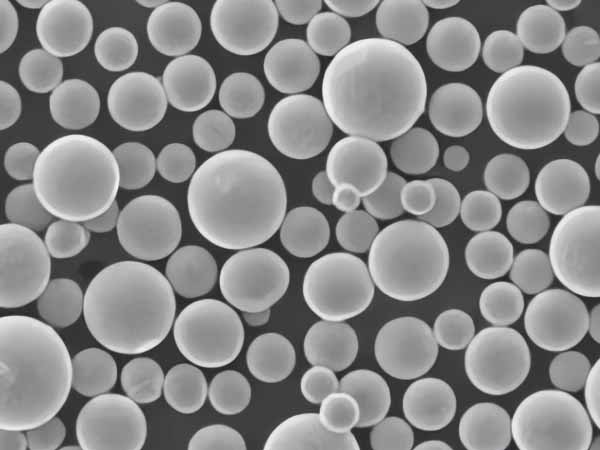
Overview of Ceramic-Lined Induction Crucibles
Ceramic-lined induction crucibles are specialized containers used in the process of melting metals via induction heating. The lining is composed of high-grade ceramic materials that can withstand extremely high temperatures, resist corrosion, and offer thermal insulation. These crucibles are indispensable in industries that require the melting of metals such as steel, aluminum, copper, and their alloys.
Key Features:
- High Thermal Resistance: Capable of withstanding temperatures exceeding 1600°C.
- Corrosion Resistance: Ideal for working with reactive metals and alloys.
- Electrical Insulation: Perfect for induction heating applications, as they don’t interfere with the electromagnetic field.
- Durability: Extended life even under harsh working conditions.
Applications:
- Metal casting
- Alloy production
- Precious metal refining
- Powder metallurgy
Composition of Ceramic-Lined Induction Crucibles
Understanding the composition of ceramic-lined induction crucibles is vital for selecting the right one for your specific application. These crucibles are composed of advanced ceramic materials, typically featuring alumina (Al2O3), zirconia (ZrO2), or silicon carbide (SiC). The choice of ceramic material largely depends on the metal to be melted and the specific process conditions.
Material | Composition | Properties | Application |
---|---|---|---|
Alumina (Al2O3) | 99.5% pure alumina | High thermal conductivity, corrosion resistance | Ideal for non-ferrous metals and alloys |
Zirconia (ZrO2) | ZrO2 + MgO | Exceptional thermal shock resistance, low thermal conductivity | Best for melting reactive metals like titanium |
Silicon Carbide (SiC) | SiC + bonding agents | High thermal conductivity, wear resistance | Suitable for high-temperature melting processes |
Why Does Composition Matter?
The composition of a crucible impacts its thermal stability, electrical properties, and durability. For instance, alumina crucibles are excellent for non-ferrous metals due to their high melting point, while zirconia crucibles are chosen for their ability to withstand thermal shocks, making them ideal for metals like titanium, which require rapid temperature changes.
Characteristics of Ceramic-Lined Induction Crucibles
Now that we’ve covered the composition, let’s explore the characteristics that make ceramic-lined induction crucibles so sought after in industrial applications.
Thermal Conductivity
The thermal conductivity of ceramic-lined induction crucibles is pivotal in ensuring efficient heat transfer to the metal, while also protecting the crucible from excessive heat buildup.
Material | Thermal Conductivity (W/mK) | Optimal Temperature Range |
---|---|---|
Alumina (Al2O3) | 30 | Up to 1600°C |
Zirconia (ZrO2) | 2.5 | Up to 2400°C |
Silicon Carbide (SiC) | 120 | Up to 2000°C |
Corrosion Resistance
Corrosion resistance is a crucial characteristic, especially when dealing with reactive metals. The ceramic lining serves as a barrier, protecting the crucible from the corrosive effects of molten metal and slag.
Electrical Insulation
Since these crucibles are used in induction heating, their electrical insulation properties are vital. The ceramic lining prevents interference with the electromagnetic field, ensuring efficient and uniform heating.
Durability and Longevity
Ceramic-lined crucibles are designed to withstand the rigorous conditions of high-temperature metal melting. Their resistance to wear and thermal shock significantly extends their service life, reducing the need for frequent replacements.
Characteristics of Common Ceramics in Crucibles
Characteristic | Alumina (Al2O3) | Zirconia (ZrO2) | Silicon Carbide (SiC) |
---|---|---|---|
Thermal Stability | Excellent | Superior | High |
Corrosion Resistance | High | Moderate | High |
Electrical Insulation | High | High | Moderate |
Durability | High | Superior | High |
Advantages of Ceramic-Lined Induction Crucibles
Why should you opt for a ceramic-lined induction crucible over other types? The advantages are numerous and compelling.
Enhanced Thermal Performance
Ceramic-lined crucibles offer superior thermal management. They retain heat better, which means faster melting times and lower energy consumption.
Improved Durability
The ceramic lining is not just for show—it dramatically increases the lifespan of the crucible, making it a cost-effective choice in the long run.
Corrosion Resistance
These crucibles are particularly resistant to corrosive environments, which is crucial when working with reactive or aggressive metal alloys.
Safety
With high thermal shock resistance and electrical insulation, ceramic-lined crucibles reduce the risk of accidents during metal melting processes.
Types of Ceramic-Lined Induction Crucibles
Different applications require different types of ceramic-lined crucibles. Below is a detailed look at the various types available on the market.
Alumina Ceramic-Lined Crucibles
Alumina-based crucibles are ideal for non-ferrous metals like aluminum and copper. They offer high thermal conductivity and are highly resistant to corrosion.
Zirconia Ceramic-Lined Crucibles
Zirconia crucibles are best suited for reactive metals such as titanium and zirconium. They are known for their exceptional thermal shock resistance and low thermal conductivity.
Silicon Carbide Ceramic-Lined Crucibles
Silicon carbide crucibles are perfect for high-temperature applications, where durability and thermal conductivity are crucial.
Graphite Ceramic-Lined Crucibles
Graphite-lined crucibles offer excellent thermal conductivity and are often used for melting precious metals like gold and silver.
Specific Metal Powder Models for Ceramic-Lined Crucibles
When it comes to melting metal powders, choosing the right crucible is essential. Here are ten specific metal powder models that work exceptionally well with ceramic-lined induction crucibles:
Metal Powder | Description | Recommended Crucible Type | Melting Point (°C) |
---|---|---|---|
Aluminum (Al) | Lightweight, high conductivity | Alumina Crucible | 660 |
Copper (Cu) | Excellent electrical conductivity | Alumina Crucible | 1085 |
Titanium (Ti) | High strength, corrosion resistant | Zirconia Crucible | 1668 |
Nickel (Ni) | High melting point, corrosion resistant | Silicon Carbide Crucible | 1455 |
Zirconium (Zr) | Resistant to heat and corrosion | Zirconia Crucible | 1855 |
Cobalt (Co) | Magnetic properties, high strength | Silicon Carbide Crucible | 1495 |
Gold (Au) | High conductivity, resistant to oxidation | Graphite Crucible | 1064 |
Silver (Ag) | Excellent thermal and electrical conductivity | Graphite Crucible | 961 |
Platinum (Pt) | High melting point, corrosion resistant | Silicon Carbide Crucible | 1768 |
Iron (Fe) | High strength, used in steelmaking | Silicon Carbide Crucible | 1538 |
Each metal powder has unique properties that make it suitable for specific applications. For instance, aluminum is often used in lightweight structures, while titanium is preferred for aerospace applications due to its strength and corrosion resistance.
Applications of Ceramic-Lined Induction Crucibles
Ceramic-lined induction crucibles are versatile and find applications across various industries. Let’s break down their usage based on different sectors.
Industry | Application | Preferred Crucible Type |
---|---|---|
Aerospace | Melting of titanium alloys | Zirconia Crucible |
Automotive | Production of aluminum parts | Alumina Crucible |
Jewelry | Melting of precious metals | Graphite Crucible |
Electronics | Copper wire production | Alumina Crucible |
Steelmaking | Iron and steel alloy production | Silicon Carbide Crucible |
Powder Metallurgy | Melting of metal powders | Silicon Carbide Crucible |
Foundries | Casting of non-ferrous alloys | Alumina Crucible |
Medical Devices | Production of cobalt-chrome alloys | Silicon Carbide Crucible |
Key Takeaways:
- Aerospace: Zirconia crucibles are favored for their ability to handle high-temperature, reactive metals.
- Automotive: Alumina crucibles are widely used for melting lightweight aluminum parts.
- Jewelry: Graphite crucibles are the go-to choice for melting gold and silver.
Specifications, Sizes, Grades, and Standards
When selecting a ceramic-lined crucible, it’s important to consider specifications, sizes, grades, and standards to ensure you’re getting the right product for your needs.
Specifications of Common Ceramic-Lined Crucibles
Specification | Alumina Crucible | Zirconia Crucible | Silicon Carbide Crucible |
---|---|---|---|
Purity (%) | 99.5 | 95 | 98 |
Temperature Range (°C) | 1000-1600 | 1400-2400 | 1400-2000 |
Size Range (mm) | 10-300 | 10-300 | 10-300 |
Wall Thickness (mm) | 3-10 | 3-10 | 3-10 |
Grades and Standards
Material | Grade | Standard |
---|---|---|
Alumina (Al2O3) | High Purity | ASTM C1674 |
Zirconia (ZrO2) | MgO Stabilized | ASTM C1326 |
Silicon Carbide (SiC) | Sintered | ASTM C863 |
Suppliers and Pricing Details
Finding the right supplier is crucial for obtaining high-quality ceramic-lined crucibles. Below is a table listing some of the top suppliers along with their pricing details.
Supplier | Location | Material | Price Range (USD) |
---|---|---|---|
Morgan Advanced Materials | USA | Alumina, Zirconia | $50-$500 |
CeramTec | Germany | Alumina, Silicon Carbide | $60-$600 |
CoorsTek | USA | Alumina, Zirconia | $70-$700 |
SGL Group | Germany | Graphite | $80-$800 |
Saint-Gobain | France | Silicon Carbide | $90-$900 |
Pros and Cons of Ceramic-Lined Induction Crucibles
Every material has its advantages and limitations. Here’s a comparison of the pros and cons of ceramic-lined induction crucibles.
Advantages:
Feature | Benefit |
---|---|
High Thermal Stability | Can withstand extreme temperatures without deforming. |
Corrosion Resistance | Suitable for reactive and aggressive metal alloys. |
Electrical Insulation | Prevents interference with induction heating processes. |
Durability | Long service life, reducing replacement costs. |
Disadvantages:
Feature | Limitation |
---|---|
Brittleness | Ceramics can crack under mechanical stress. |
Cost | Higher initial cost compared to other crucibles. |
Complex Manufacturing | Requires precise control over the manufacturing process. |
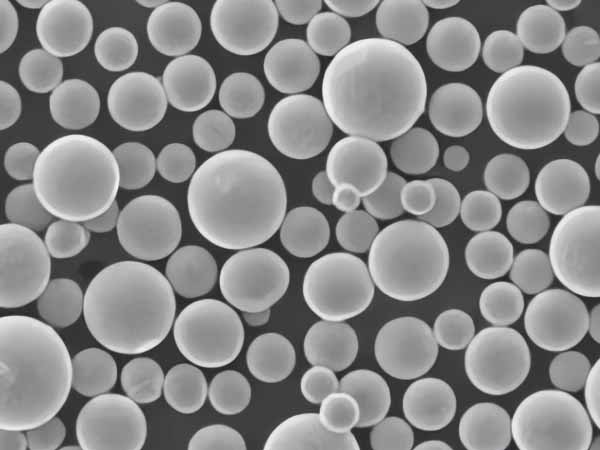
FAQ
To wrap things up, let’s answer some of the most frequently asked questions about ceramic-lined induction crucibles.
Question | Answer |
---|---|
What is the primary use of ceramic-lined induction crucibles? | They are primarily used for melting metals in induction furnaces, offering high thermal resistance and durability. |
Which metal powders can be melted in ceramic-lined crucibles? | Metal powders like aluminum, copper, titanium, and gold can be efficiently melted in these crucibles. |
How do I choose the right ceramic-lined crucible? | Consider factors such as the type of metal you’re melting, the operating temperature, and the required thermal properties. |
Are ceramic-lined crucibles expensive? | They can be more expensive initially, but their durability and efficiency make them cost-effective in the long run. |
Can ceramic-lined crucibles handle thermal shock? | Yes, especially zirconia-based crucibles, which are known for their exceptional thermal shock resistance. |
What sizes are available for ceramic-lined crucibles? | They come in a variety of sizes, typically ranging from 10 mm to 300 mm in diameter. |
How long do ceramic-lined crucibles last? | With proper care, they can last for several years, even in high-temperature environments. |
Can they be used for melting precious metals? | Absolutely, graphite-lined ceramic crucibles are especially good for this purpose. |
Are there any limitations to using ceramic-lined crucibles? | They are brittle and can crack under mechanical stress, and they are also relatively more expensive. |
Where can I buy high-quality ceramic-lined crucibles? | Suppliers like Morgan Advanced Materials, CeramTec, and CoorsTek offer high-quality options. |
Conclusion
Ceramic-lined induction crucibles are a critical component in modern metallurgy, offering a blend of durability, thermal efficiency, and corrosion resistance. Whether you’re working with lightweight aluminum alloys or high-strength titanium, choosing the right crucible can make all the difference in your process.
By understanding their composition, characteristics, and the specific metal powders they are best suited for, you can optimize your melting processes, reduce costs, and improve product quality. Remember, while the initial investment may be higher, the long-term benefits of using ceramic-lined induction crucibles far outweigh the costs.
In the ever-evolving world of metallurgy, staying informed about the tools and materials at your disposal is key. So, whether you’re refining precious metals or casting aerospace components, ceramic-lined induction crucibles are an investment worth considering.