Copper alloys powder is an important material with wide-ranging industrial applications. This comprehensive guide will examine key aspects of copper alloys powder technology to help readers understand its capabilities and limitations.
Overview of Copper Alloys Powder
Copper alloys powder refers to powder metallurgy forms of various copper-based alloys. These alloys contain copper as the base metal, along with alloying elements like tin, zinc, silicon, nickel, aluminium, manganese, and more.
Some major characteristics of copper alloys powder:
- High strength and hardness
- Excellent thermal and electrical conductivity
- Good corrosion resistance
- Low friction properties
- Range of alloy types for various applications
- Produced through atomisation and other powder production processes
The copper content ranges from 60% to 99% in different alloys. The remaining alloying elements enhance specific material properties needed for particular end-use applications.
Main applications of copper alloys powder include automotive components, machinery parts, bearings, gears, filters, brazing, diamond tools, welding, additive manufacturing, and more.
The global copper alloys powder market size was over USD XX million in 2022 and is projected to expand at a CAGR of XX% from 2023 to 2030. Key growth drivers are increasing usage in 3D printing and lightweight automotive parts.

Types of Copper Alloys Powder
Many alloy variants and grades of copper alloys powder exist which can be categorized into following major types:
Table 1: Major Types of Copper Alloys Powder
Alloy Type | Composition | Key Properties | Typical Applications |
---|---|---|---|
Brass | Copper + Zinc | High strength, machinability | Gears, decorative parts |
Bronze | Copper + Tin/Aluminium/Silicon | Wear resistance, electrical conductivity | Bearings, welding rods |
Copper-Nickel | Copper + Nickel | Corrosion resistance | Marine components, coinage |
Tool Alloy | Copper + Cobalt/Chromium | Extreme hardness, heat resistance | Cutting tools, molds |
Additionally, grades like phosphor bronze, silicon bronze, manganese bronze etc. are manufactured depending on exact properties needed. Grades differ based on exact percentages of alloying elements used.
Global capacity for brass powder is the highest among copper alloys, followed by bronze and nickel silver. Market share for tool alloy powder is expanding the fastest to meet tooling application demand.
Production Methods for Copper Alloys Powder
Following main methods are employed commercially for producing copper alloys powder depending on factors like cost, scale and final powder characteristics:
Table 2: Production Methods for Copper Alloys Powder
Method | Description | Typical Particle Size | Cost Factors |
---|---|---|---|
Atomisation | Molten alloy stream broken into droplets that solidify into powder | 5 – 250 microns | High purity, small batches |
Electrolysis | Anode dissolved leaving cathode deposit powder | Under 10 microns | Lower purity, high volume |
Ball Milling | Mechanical grinding of alloy chips/ingots | 10 – 250 microns | Reclaimed scrap usage |
Chemical Reduction | Metal salts reduced to powder form | Under 1 micron | Ultrafine special grades |
Atomisation is the most widely used method allowing good control over powder shape and size distribution. High productivity rotary atomisation is employed for common brass and bronze grades. Specialist grades use electrode induction gas atomisation or plasma atomisation.
Electrolytic copper powder has lower purity but very fine particle sizes. Ball milling utilizes scrap material and is lower cost but has size limitations. Chemical reduction uniquely produces nanopowder below 1 micron particle size.
Supply and quality factors
Most copper alloy powder supply comes from China, India, Germany, Italy and USA. Japanese and Korean manufacturers focus on high performance alloys. Buyers must evaluate factors like composition consistency, gas levels, particle shape/size distribution and lot-to-lot variability while sourcing.
Parameters and Specifications
Key parameters and specifications defined for copper alloys powder during product selection and quality control:
Table 3: Typical Specifications for Copper Alloys Powder
Parameter | Typical Range | Significance | Test Methods |
---|---|---|---|
Alloy Grade | CDA X, IS X, Custom | Defines properties | Spectrometry |
Particle Size | 10 – 150 microns | Handles consistency | Sieve Analysis |
Apparent Density | 2 – 5 g/cc | Pressability, handling | Hall Flowmeter |
Tap Density | 4 – 8 g/cc | Compactability | Jogging Volumeter |
Flow Rate | Under 50 s/50g | Mold filling ease | Hall Flowmeter |
Oxygen Content | Under 500 ppm | Purity, process control | Inert Gas Fusion |
Other tests like mesh size analysis, green strength checks, loss on ignition, microstructure examination etc. are also performed regularly. Customers must select powder based on not just alloy type but also particle size range and shape optimized for their fabrication process.
Applications and End-Use Sectors
Major application areas and end-use sectors using copper alloys powder are:
Table 4: End-Use Applications for Copper Alloys Powder
Sector | Applications | Used For | Alloy Grades |
---|---|---|---|
Automotive | Bushings, bearings, gears | Friction and thermal management | Bronzes, tool alloys |
Industrial | Filtration media, welding rods | Filtration efficiency, joint strength | Brasses, bronzes |
Additive Manufacturing | 3D printed components | Custom alloys, shapes | Tool alloys, bronzes |
Electronic | Contacts, coatings | Conductivity, anti-corrosion | Copper-tungsten, bronzes |
Diamond Tools | Tool bits, blades | Abrasion resistance | Chromium coppers |
Expanding usage areas are lightweight bronze bearings in EVs, manganese bronze architectural 3D printing, copper-chromium contact alloys in electronics etc. Market trends strongly support expanded uptake across transportation, energy, IT hardware and industrial machinery over the coming decade.
Among all industry sectors, transportation is the dominant end-user accounting for over 35% demand as per 2022 estimates. This includes substantial usage in two and four-wheelers for bushings, bushings and small gears. The fastest growth at over 8% CAGR is foreseen in industrial manufacturing like presses and compressors where replacing cast iron with copper alloy powder parts enables performance improvements. Multiple allied industries additionally utilize copper alloys powder directly or indirectly.
Pricing Factors and Breakup
Typical price range: USD XX to USD XX per kg
Prices vary based on:
- Alloy type – Specialist grades cost higher than standard brass
- Powder production method – Atomised is costlier than electrolytic
- Order volume – Bulk supply has lower per kg pricing
- Particle size – Finer is costlier owing to sieving/classification
- Quality requirements – Tighter control demands pricing premium
** Indicative composition based price stack-up** for 1 metric ton brass powder would be:
- Material – USD XX (base copper/zinc price)
- Processing – USD XX (atomization etc.)
- Quality Control – USD XX (composition/size/tests)
- Packing – USD XX (drums, storage/handling)
- Logistics – USD XX
- Consolidated Price = USD XX to USD XX per kg
Competitive options are available from China below USD XX/kg but quality variations can affect output. Indian suppliers offer good balance of quality and cost. Buyers must do pilot testing with short samples before bulk commitments.
Choosing the Right Copper Alloy Powder
Following key steps while selecting the optimum copper alloy powder:
Table 5: Copper Alloy Powder Selection Guidelines
Parameter | Guidelines | Benefit |
---|---|---|
Application | Match powder alloy to part functionality needed | Achieve target mechanical properties |
Composition | Specify composition tolerances needed | Control output variability |
Particle Size | Select based on consolidation process | Optimise pressability, handling |
Powder Shape | Spherical better than irregular for mold filling | Improve green strength, density |
Purity Standards | Establish process impurity limits | Control powder variability |
Sampling Testing | Do trial runs first before bulk orders | Confirm quality, process compatibility |
Proactively communicating product expectations, testing standards and batch sampling protocols is highly recommended while qualifying new copper alloy powder sources. This helps align supplier manufacturing to buyer needs through customisation options. Third party inspection services help relieve buyer quality control overheads.
Comparison Between Major Alloy Types
Table 6: How Key Alloy Grades Compare
Parameter | Brass Powder | Bronze Powder | Copper-Nickel Powder | Chromium Copper |
---|---|---|---|---|
Hardness | Medium | Medium-high | Medium | Very high |
Strength | High | Medium-High | High | Highest |
Wear Resistance | Medium | Highest | Low | Medium |
Corrosion Resistance | Medium | Medium | Maximum | Low |
Thermal Conductivity | High | Maximum | Medium | Medium |
Electrical Conductivity | Highest | Medium-high | Medium | Low |
Cost | Lowest | Medium | High | Very high |
Main Applications | Decorative fittings, gears | Bearings, welding | Marine components | Cutting tools |
Key takeaways:
- Bronzes optimized for wear performance, thermal conductivity
- Brasses provide best balance of cost, strength, conductivity
- Copper-nickels extremely corrosion resistant
- Chromium coppers used where extreme hardness needed
Align business needs to alloy grade strengths through informed material selection.
Installation, Operation and Maintenance
Table 7: Copper Alloy Powder Handling Guidelines
Stage | Instructions | Precautions |
---|---|---|
Unloading | Use dust masks, gloves ; Check drums | Avoid inhalation or contact |
Storage | Keep sealed drums in dry, indoor storage | Prevent moisture ingress or contamination |
Transfer | Use dedicated powder handling stations | Ensure adequate ventilation ; Control dust |
Processing | Set control limits for all make variables | Minimise process variations |
Maintenance | Schedule inspections of powder handling system | Keep all inserts clean; Replace as needed |
Critical aspects:
- Keep stored powder sealed and dry to prevent oxidation
- Employ fused pipes, leak-proof gaskets to avoid spills
- Program equipment to feed consistent powder volumes
- Watch particle size distribution and humidity in feedstock
- Implement rigorous maintenance schedules
Careful powder handling and process discipline for copper alloys pays great dividends in improving final part quality and consistency.
Troubleshooting Guide
Table 8: Copper Alloy Powder Troubleshooting Tips
Issue | Possible Causes | Action Items |
---|---|---|
Variability in green density | Irregular powder shape ; Powder segregation ; Incorrect particle size | Specify spherical powder ; Improve storage ; Review sieve analysis |
Low strength in sintered part | Off-spec powder composition ; Inadequate pressing parameters | Improve procurement quality control ; Adjust press settings |
Distortion or cracks | Rapid heating/cooling rates ; Excessive carbon pick-up | Optimize furnace program ; Check process environment |
Surface defects | Surface oxidation ; Contamination ingress | Use protective atmosphere ; Improve handling protocols |
Maintaining powder feedstock quality and an environmentcontrolled process are vital for minimizing copper alloy powder part defects. Continuously monitoring key parameters and taking corrective measures swiftly can dramatically improve yields over the long run.
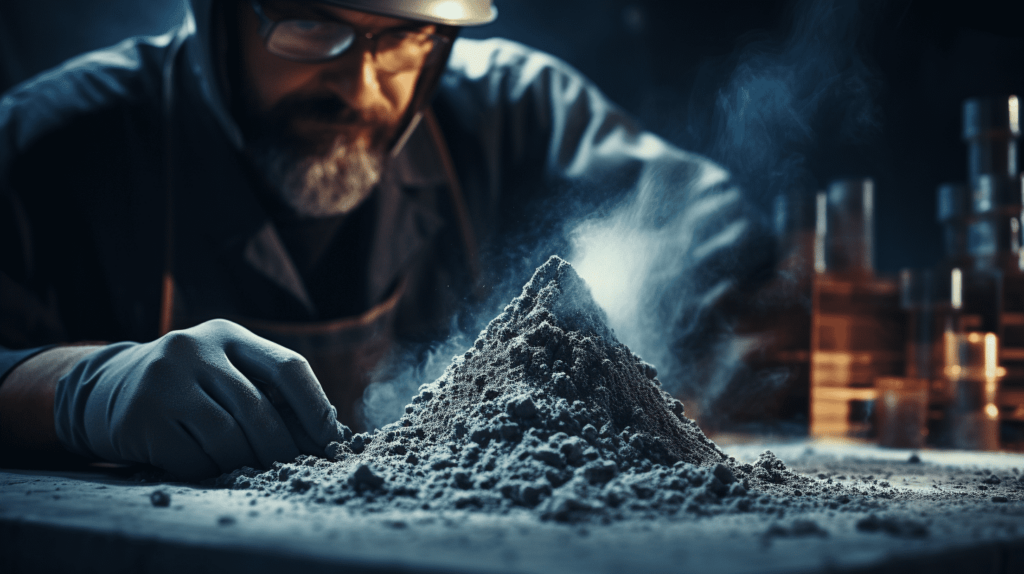
FAQ
Q: How to determine the right alloy grade for an application?
A: Consult supplier guides linking alloy properties to applications. Review technical literature for comparative data. Seek expert guidance to match mechanical, physical and cost needs.
Q: What is the effect of powder particle size on final part properties?
A: Finer powder below 25 microns improves density and strength but costs more and affects flowability. Coarser powder offers better liquid phase sintering response for higher ductility and impact energy.
Q: What is the influence of production method on copper alloy powder characteristics?
A: Water atomised powder has spherical particles ensuring best pressability and handleability. Air atomised powder has slightly more irregular shape but lower cost. Electrolytic powder has high oxygen so needs protective atmosphere when sintering.
Q: How to manage lot-to-lot variability in alloy powder chemistry?
A: Tighter supplier quality control on melt analysis and continuous production monitoring can minimise variation. Statistical process control tracking also helps identify subtle changes needing intervention.
Q: What causes distortion or cracks in final PM parts?
A: Non-uniform heating in furnaces, rapid cooling rates and inconsistent powder density contribute to these defects. Optimised thermal cycle and press program parameters are essential.