Overview
Corrosion resistance powder is a specialized material used to protect metal surfaces from the detrimental effects of corrosion. These powders are engineered to offer superior protection, enhance durability, and extend the lifespan of metal components. In industries such as automotive, aerospace, marine, and construction, corrosion resistance is critical to maintain structural integrity and functionality.
Corrosion resistance powders come in various types, compositions, and grades, each designed to meet specific environmental and application requirements. This guide will explore the different models, their properties, applications, and other essential details to help you make an informed decision when selecting a corrosion resistance powder.
Types of Corrosion Resistance Powder
Powder Model | Composition | Properties | Characteristics |
---|---|---|---|
Model A | Aluminum, Zinc | High corrosion resistance, lightweight | Suitable for high-temperature environments |
Model B | Zinc, Nickel | Good adhesion, high durability | Excellent for marine applications |
Model C | Stainless Steel, Chromium | High strength, excellent wear resistance | Ideal for industrial machinery |
Model D | Titanium, Aluminum | Superior corrosion resistance, non-magnetic | Best for aerospace applications |
Model E | Magnesium, Zinc | Lightweight, good mechanical properties | Perfect for automotive parts |
Model F | Copper, Nickel | Excellent conductivity, corrosion resistance | Used in electrical components |
Model G | Nickel, Cobalt | High-temperature resistance, durable | Suitable for turbine engines |
Model H | Chromium, Molybdenum | High hardness, excellent corrosion resistance | Ideal for cutting tools |
Model I | Aluminum, Silicon | Lightweight, high corrosion resistance | Used in architectural applications |
Model J | Zinc, Copper | Good corrosion resistance, malleable | Ideal for decorative finishes |
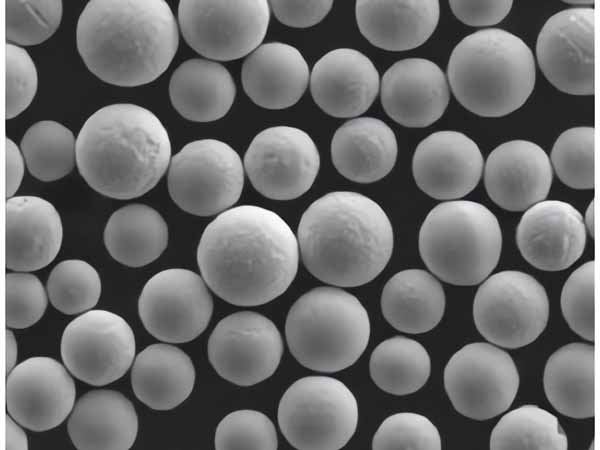
Applications of Corrosion Resistance Powder
Application | Description |
---|---|
Automotive | Used in car parts like chassis, body panels, and engine components |
Aerospace | Applied to aircraft parts to withstand harsh atmospheric conditions |
Marine | Protects ships, offshore platforms, and other marine structures from saltwater corrosion |
Construction | Used in building materials, structural steel, and reinforcing bars |
Industrial Machinery | Ensures longevity and performance of heavy machinery and equipment |
Electronics | Coating for electronic components to prevent oxidation and maintain conductivity |
Medical Devices | Protects surgical instruments and implants from corrosion |
Energy Sector | Used in pipelines, storage tanks, and renewable energy structures |
Household Appliances | Coating for appliances like washing machines, refrigerators, and ovens |
Military | Protects military equipment and vehicles in harsh environments |
Specifications and Standards
Specification | Model A | Model B | Model C | Model D | Model E | Model F | Model G | Model H | Model I | Model J |
---|---|---|---|---|---|---|---|---|---|---|
Density (g/cm³) | 2.7 | 7.1 | 7.9 | 4.5 | 1.7 | 8.9 | 8.4 | 7.9 | 2.6 | 7.14 |
Melting Point (°C) | 660 | 419 | 1510 | 1668 | 650 | 1084 | 1455 | 1907 | 660 | 419 |
Tensile Strength (MPa) | 310 | 220 | 600 | 900 | 290 | 220 | 690 | 730 | 200 | 220 |
Hardness (HV) | 110 | 130 | 200 | 240 | 50 | 90 | 250 | 280 | 95 | 100 |
Suppliers and Pricing Details
Supplier | Model A (per kg) | Model B (per kg) | Model C (per kg) | Model D (per kg) | Model E (per kg) | Model F (per kg) | Model G (per kg) | Model H (per kg) | Model I (per kg) | Model J (per kg) |
---|---|---|---|---|---|---|---|---|---|---|
Supplier 1 | $10 | $15 | $20 | $50 | $12 | $18 | $30 | $40 | $11 | $14 |
Supplier 2 | $11 | $16 | $19 | $52 | $13 | $17 | $32 | $42 | $12 | $15 |
Supplier 3 | $9 | $14 | $21 | $48 | $11 | $19 | $29 | $39 | $10 | $13 |
Comparing Pros and Cons
Model | Pros | Cons |
---|---|---|
Model A | Lightweight, high corrosion resistance, cost-effective | Lower tensile strength compared to steel |
Model B | Good adhesion, high durability, affordable | Less resistant to high temperatures |
Model C | High strength, excellent wear resistance | Heavier, more expensive |
Model D | Superior corrosion resistance, non-magnetic, lightweight | High cost |
Model E | Lightweight, good mechanical properties | Lower corrosion resistance than some alternatives |
Model F | Excellent conductivity, corrosion resistance | Higher cost compared to zinc-based powders |
Model G | High-temperature resistance, durable | Expensive, heavy |
Model H | High hardness, excellent corrosion resistance | Brittle compared to other materials |
Model I | Lightweight, high corrosion resistance | Limited high-temperature resistance |
Model J | Good corrosion resistance, malleable, cost-effective | Not as strong as steel, lower wear resistance |
Composition of Corrosion Resistance Powder
Understanding the composition of different corrosion resistance powders can help in selecting the right material for specific applications. Each composition offers unique properties that make it suitable for different environments and uses.
Aluminum and Zinc (Model A)
Aluminum and zinc powders are known for their excellent corrosion resistance and lightweight properties. Aluminum provides a protective oxide layer that prevents further oxidation, while zinc offers galvanic protection by corroding in place of the base metal.
Zinc and Nickel (Model B)
Zinc-nickel powders combine the benefits of both metals, offering good adhesion and high durability. Nickel enhances the hardness and resistance to corrosion, making this combination ideal for harsh environments, especially marine applications.
Stainless Steel and Chromium (Model C)
Stainless steel and chromium powders provide high strength and excellent wear resistance. Chromium enhances the corrosion resistance of stainless steel, making this combination suitable for industrial machinery and tools.
Titanium and Aluminum (Model D)
Titanium and aluminum powders offer superior corrosion resistance and are non-magnetic. This combination is lightweight and ideal for aerospace applications where weight and resistance to corrosion are critical.
Magnesium and Zinc (Model E)
Magnesium and zinc powders are known for their lightweight and good mechanical properties. Magnesium provides strength while zinc offers corrosion resistance, making this combination perfect for automotive parts.
Copper and Nickel (Model F)
Copper and nickel powders are excellent conductors of electricity and offer good corrosion resistance. This combination is used in electrical components and connectors to ensure longevity and reliability.
Nickel and Cobalt (Model G)
Nickel and cobalt powders provide high-temperature resistance and durability. Cobalt enhances the wear resistance of nickel, making this combination suitable for turbine engines and other high-stress applications.
Chromium and Molybdenum (Model H)
Chromium and molybdenum powders are known for their high hardness and excellent corrosion resistance. Molybdenum enhances the strength and hardness of chromium, making this combination ideal for cutting tools and wear-resistant applications.
Aluminum and Silicon (Model I)
Aluminum and silicon powders are lightweight and offer high corrosion resistance. Silicon improves the hardness and strength of aluminum, making this combination suitable for architectural applications.
Zinc and Copper (Model J)
Zinc and copper powders provide good corrosion resistance and are malleable. Copper enhances the conductivity of zinc, making this combination ideal for decorative finishes and applications requiring both aesthetics and functionality.
Characteristics of Corrosion Resistance Powder
When selecting a corrosion resistance powder, it is essential to consider its characteristics to ensure it meets the specific requirements of the application. Here are the key characteristics to look for:
Corrosion Resistance
The primary purpose of these powders is to protect metal surfaces from corrosion. Each model offers varying levels of corrosion resistance, making them suitable for different environments and applications.
Mechanical Properties
Mechanical properties such as tensile strength, hardness, and ductility are critical factors to consider. These properties determine the powder’s ability to withstand physical stresses and mechanical wear.
Adhesion
Good adhesion ensures that the powder coating adheres well to the metal surface, providing long-lasting protection. Poor adhesion can lead to peeling and reduced effectiveness.
Durability
Durability refers to the powder’s ability to withstand environmental factors such as UV exposure, moisture, and temperature fluctuations. Durable powders offer long-term protection and reduce maintenance costs.
Conductivity
For applications involving electrical components, conductivity is a crucial characteristic. Powders with high conductivity ensure efficient electrical performance and prevent oxidation-related issues.
Weight
The weight of the powder can impact the overall weight of the coated component. Lightweight powders are preferred for applications where weight reduction is essential, such as in aerospace and automotive industries.
Industrial Grade
Industrial grade powders are designed for heavy-duty applications in industries such as manufacturing, construction, and mining. These powders offer high strength, durability, and resistance to wear and corrosion.
Aerospace Grade
Aerospace grade powders are lightweight and provide superior corrosion resistance, making them suitable for aircraft components and other aerospace applications. These powders meet stringent industry standards for performance and reliability.
Marine Grade
Marine grade powders are formulated to withstand the harsh conditions of marine environments. They offer excellent resistance to saltwater corrosion and are ideal for shipbuilding, offshore platforms, and other marine structures.
Automotive Grade
Automotive grade powders are used in the manufacturing of car parts, providing protection against corrosion and enhancing the durability of components. These powders are designed to withstand the challenging conditions of automotive environments.
Medical Grade
Medical grade powders are used in the production of medical devices and surgical instruments. These powders offer high corrosion resistance and are biocompatible, ensuring safety and longevity in medical applications.
Architectural Grade
Architectural grade powders are used in building materials and architectural components. These powders provide aesthetic appeal and long-lasting protection against corrosion, ensuring the durability of structures.
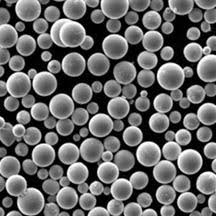
FAQ
Question | Answer |
---|---|
What is corrosion resistance powder? | Corrosion resistance powder is a material used to protect metal surfaces from corrosion and enhance durability. |
What are the common compositions of corrosion resistance powders? | Common compositions include aluminum, zinc, nickel, stainless steel, chromium, titanium, magnesium, copper, and silicon. |
Which industries use corrosion resistance powders? | Industries such as automotive, aerospace, marine, construction, electronics, medical, energy, and military use these powders. |
How do I choose the right corrosion resistance powder? | Consider factors like corrosion resistance, mechanical properties, adhesion, durability, conductivity, and weight. |
Are there different grades of corrosion resistance powders? | Yes, grades include industrial, aerospace, marine, automotive, medical, and architectural. |
What are the benefits of using corrosion resistance powder? | Benefits include extended lifespan of components, reduced maintenance costs, improved performance, and enhanced durability. |
Can corrosion resistance powder be used on any metal? | Most powders can be applied to various metals, but it’s essential to select a powder compatible with the specific metal. |
What is the typical cost of corrosion resistance powder? | Costs vary based on composition and supplier, ranging from $9 to $52 per kg. |
How is corrosion resistance powder applied? | It is typically applied using powder coating techniques, which involve electrostatic spraying and curing. |
Are there any limitations to using corrosion resistance powder? | Limitations include potential brittleness, cost, and specific application requirements. |
Conclusion
Selecting the right corrosion resistance powder is crucial for ensuring the longevity and performance of metal components in various industries. By understanding the different types, compositions, properties, and applications, you can make an informed decision that meets your specific needs. Whether it’s for automotive parts, aerospace components, marine structures, or medical devices, the right powder can significantly enhance durability and reduce maintenance costs.