Corrosion is the natural enemy of metals, causing degradation that can lead to costly repairs or replacements. To combat this, corrosion resistance powders are often employed, especially in environments where exposure to corrosive agents like water, chemicals, or salt is prevalent. These powders are formulated with specific metal compositions to prevent or significantly slow down the corrosion process.
In this comprehensive guide, we’ll delve into the world of corrosion resistance powders, exploring their compositions, characteristics, applications, and much more. Whether you’re a materials engineer, a product designer, or someone interested in understanding how to protect metal surfaces, this article will provide you with the necessary insights.
Overview of Corrosion Resistance Powder
Corrosion resistance powders are finely milled particles of metals and alloys designed to offer a protective barrier against oxidation and corrosion. These powders can be applied via various methods such as thermal spraying, powder coating, and metal injection molding. They are used in a wide range of industries including automotive, aerospace, marine, and construction.
Here’s a quick overview of what we’ll cover in this guide:
- Types of Corrosion Resistance Powders: Different metals and alloys used.
- Compositions: Chemical makeup of these powders.
- Characteristics: Properties that make these powders effective against corrosion.
- Applications: Industries and scenarios where these powders are used.
- Specifications and Standards: Common grades, sizes, and industry standards.
- Suppliers and Pricing: Where to buy and what to expect cost-wise.
- Advantages and Disadvantages: Comparing the pros and cons of different powders.
- FAQs: Common questions about corrosion resistance powders.
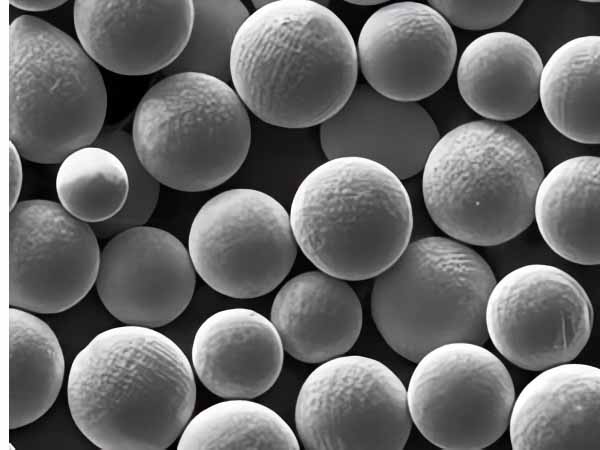
Types of Corrosion Resistance Powders
Corrosion resistance powders come in various types, each offering unique properties tailored to specific environments. Here’s a detailed look at some of the most commonly used powders:
Type | Composition | Properties | Best Suited For |
---|---|---|---|
Stainless Steel 316L | Iron, Chromium, Nickel, Molybdenum | Excellent corrosion resistance, high strength | Marine applications, chemical processing |
Inconel 625 | Nickel, Chromium, Molybdenum, Niobium | High-temperature resistance, superior corrosion protection | Aerospace, nuclear reactors |
Hastelloy C276 | Nickel, Molybdenum, Chromium, Tungsten | Exceptional corrosion resistance, especially to acids | Chemical processing, pollution control |
Aluminum 6061 | Aluminum, Magnesium, Silicon | Lightweight, good corrosion resistance | Automotive, construction |
Titanium Grade 5 | Titanium, Aluminum, Vanadium | High strength, excellent corrosion resistance | Aerospace, medical implants |
Zinc | Zinc | Sacrificial anode properties, good for galvanizing | Automotive, construction, electrical components |
Nickel 200 | Nickel | Outstanding resistance to caustic alkalies | Chemical manufacturing, food processing |
Copper-Nickel 90/10 | Copper, Nickel | Good seawater corrosion resistance | Marine, offshore oil and gas |
Cobalt-Chromium | Cobalt, Chromium | High wear resistance, excellent corrosion resistance | Medical implants, aerospace |
Magnesium AZ91D | Magnesium, Aluminum, Zinc | Lightweight, moderate corrosion resistance | Automotive, aerospace |
Composition of Corrosion Resistance Powder
Understanding the composition of corrosion resistance powders is crucial to selecting the right type for your application. Different elements in the composition bring unique benefits and challenges. Let’s break down the key components:
Stainless Steel 316L
- Iron (Fe): Base metal providing structural strength.
- Chromium (Cr): Offers corrosion resistance by forming a passive oxide layer.
- Nickel (Ni): Adds toughness and enhances corrosion resistance.
- Molybdenum (Mo): Improves resistance to pitting and crevice corrosion, especially in chloride environments.
Inconel 625
- Nickel (Ni): Base metal, providing excellent oxidation and corrosion resistance.
- Chromium (Cr): Enhances oxidation resistance at high temperatures.
- Molybdenum (Mo) and Niobium (Nb): Strengthen the alloy, improving its high-temperature stability.
Hastelloy C276
- Nickel (Ni): Provides exceptional corrosion resistance in a wide range of environments.
- Molybdenum (Mo) and Chromium (Cr): Offer resistance to pitting, crevice corrosion, and stress-corrosion cracking.
- Tungsten (W): Increases the alloy’s resistance to highly corrosive environments.
These compositions demonstrate how different elements work together to create powders with unique corrosion resistance properties. The choice of powder depends on the specific needs of the application, including environmental factors and the mechanical demands of the part or structure being protected.
Characteristics of Corrosion Resistance Powder
To truly understand the value of corrosion resistance powders, let’s take a closer look at their key characteristics:
- Corrosion Resistance: The primary function, these powders protect the substrate from oxidation and chemical reactions that cause deterioration.
- Adhesion: They bond well to the substrate, ensuring long-lasting protection without flaking or peeling.
- Wear Resistance: Many of these powders also provide excellent wear resistance, which is crucial in applications involving friction or abrasive conditions.
- Temperature Resistance: Powders like Inconel 625 and Hastelloy C276 can withstand extreme temperatures, making them suitable for high-heat environments.
- Mechanical Strength: Beyond just protecting against corrosion, these powders can add to the mechanical strength of the coated material.
- Chemical Compatibility: Different powders offer resistance to different types of chemicals, whether acidic, basic, or saline environments.
- Environmental Safety: With growing environmental concerns, many of these powders are designed to be environmentally friendly, with minimal hazardous components.
Applications of Corrosion Resistance Powder
Corrosion resistance powders find application across a variety of industries. Here’s how they’re used in some key sectors:
Industry | Application | Powder Type | Benefits |
---|---|---|---|
Marine | Ship hulls, offshore platforms | Copper-Nickel 90/10, Stainless Steel 316L | Protects against seawater corrosion |
Aerospace | Jet engines, structural components | Inconel 625, Titanium Grade 5 | Resists high-temperature corrosion, reduces weight |
Automotive | Exhaust systems, structural parts | Aluminum 6061, Zinc | Lightweight, protects against road salts |
Chemical Processing | Reactors, pipelines, storage tanks | Hastelloy C276, Nickel 200 | Resists acidic and caustic environments |
Construction | Bridges, buildings, reinforcement bars | Stainless Steel 316L, Zinc | Longevity in harsh outdoor conditions |
Medical | Implants, surgical tools | Cobalt-Chromium, Titanium Grade 5 | Biocompatibility, corrosion resistance in body fluids |
Oil & Gas | Downhole tools, pipelines, valves | Inconel 625, Copper-Nickel 90/10 | Corrosion resistance under high pressure and temperature |
Electronics | Connectors, PCBs, casings | Nickel 200, Zinc | Prevents corrosion in electrical contacts |
Power Generation | Turbine blades, heat exchangers | Hastelloy C276, Inconel 625 | Handles high heat and corrosive environments |
Food Processing | Machinery, piping | Stainless Steel 316L, Nickel 200 | Maintains hygiene, resists food acids |
Specifications, Sizes, and Standards
Selecting the right corrosion resistance powder involves understanding the specifications, sizes, and standards applicable to your needs. Here’s a breakdown:
Powder Type | Available Sizes (Microns) | Common Standards | Grades |
---|---|---|---|
Stainless Steel 316L | 15-45, 45-75 | ASTM A276, ISO 15156-3 | 316L, 316F |
Inconel 625 | 15-53, 53-150 | AMS 5666, ASTM B446 | UNS N06625 |
Hastelloy C276 | 15-45, 45-75 | ASTM B575, ASME SB-575 | UNS N10276 |
Aluminum 6061 | 20-60, 60-90 | ASTM B209, ISO 6362 | 6061-T6, 6061-T651 |
Titanium Grade 5 | 15-45, 45-75 | ASTM B348, ISO 5832-3 | Grade 5 (Ti-6Al-4V) |
Zinc | 20-50, 50-100 | ASTM B6, ISO 752 | SHG, HG |
Nickel 200 | 15-53, 53-150 | ASTM B160, ASME SB-160 | UNS N02200 |
Copper-Nickel 90/10 | 15-45, 45-75 | ASTM B122, ISO 6208 | C70600, CW352H |
Cobalt-Chromium | 10-45, 45-75 | ASTM F75, ISO 5832-4 | CoCrMo, L605 |
Magnesium AZ91D | 20-60, 60-90 | ASTM B93/B93M, ISO 16220 | AZ91D, AZ91E |
These standards and specifications ensure that the powders meet the necessary quality and performance criteria for their intended applications.
Suppliers and Pricing Details
When purchasing corrosion resistance powders, it’s essential to consider both the quality of the product and the reliability of the supplier. Here’s a list of some well-known suppliers along with a general idea of pricing:
Supplier | Location | Powder Types Offered | Price Range (USD/kg) |
---|---|---|---|
Höganäs AB | Sweden | Stainless Steel 316L, Inconel 625, Copper-Nickel 90/10 | $50 – $150 |
Carpenter Technology | USA | Titanium Grade 5, Cobalt-Chromium, Hastelloy C276 | $100 – $250 |
Sandvik Materials Technology | Sweden | Stainless Steel 316L, Inconel 625 | $60 – $200 |
Kennametal | USA | Cobalt-Chromium, Inconel 625, Nickel 200 | $80 – $220 |
Praxair Surface Technologies | USA | Hastelloy C276, Aluminum 6061, Zinc | $40 – $130 |
VSMPO-AVISMA | Russia | Titanium Grade 5, Aluminum 6061 | $120 – $300 |
AMETEK SMP Eighty Four | USA | Nickel 200, Copper-Nickel 90/10, Magnesium AZ91D | $70 – $180 |
Metco (Oerlikon) | Switzerland | Inconel 625, Hastelloy C276, Zinc | $90 – $240 |
Advanced Powder & Coatings | Canada | Stainless Steel 316L, Aluminum 6061 | $50 – $140 |
Tekna | Canada | Titanium Grade 5, Inconel 625, Magnesium AZ91D | $110 – $290 |
Prices can vary significantly depending on the specific powder type, quantity ordered, and supplier. It’s always advisable to request quotes and compare options before making a purchase.
Advantages and Disadvantages of Corrosion Resistance Powder
Every material has its strengths and weaknesses, and corrosion resistance powders are no exception. Here’s a comparison of the pros and cons of using these powders:
Advantage | Explanation |
---|---|
High Corrosion Resistance | Protects metal surfaces from a wide range of corrosive environments. |
Improved Mechanical Properties | Enhances the strength and durability of the coated material. |
Versatility | Suitable for a variety of applications across multiple industries. |
Temperature Resistance | Maintains integrity at high temperatures, ideal for aerospace and power generation. |
Cost-Effective Protection | Extends the lifespan of metal components, reducing the need for frequent replacements. |
Disadvantage | Explanation |
---|---|
Cost | Some powders, especially those made from rare or expensive materials, can be costly. |
Complex Application Process | Requires specialized equipment and expertise to apply properly. |
Limited Availability | Not all powder types are readily available, particularly specialized alloys. |
Environmental Concerns | Some powders may contain elements that are not environmentally friendly. |
Surface Preparation | Requires thorough cleaning and preparation of the substrate for optimal adhesion. |
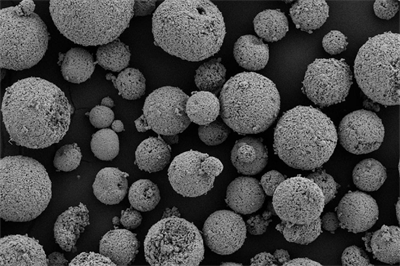
FAQs
Here’s a collection of frequently asked questions about corrosion resistance powders, designed to clear up any doubts you might have.
Question | Answer |
---|---|
What is corrosion resistance powder? | Corrosion resistance powder is a finely milled metal or alloy powder used to protect metal surfaces from corrosion. |
How is corrosion resistance powder applied? | It can be applied through methods like thermal spraying, powder coating, or metal injection molding. |
Which industries benefit the most from using these powders? | Industries such as aerospace, automotive, marine, and chemical processing benefit significantly from these powders. |
Are corrosion resistance powders environmentally friendly? | Many are designed to be environmentally friendly, though it depends on the specific powder type. |
How do I choose the right corrosion resistance powder? | Consider the environmental conditions, required properties, and compatibility with the substrate. |
Can corrosion resistance powders improve mechanical strength? | Yes, some powders enhance the mechanical strength of the coated material. |
What are the common standards for these powders? | Standards like ASTM, ISO, and AMS are commonly used to ensure quality and performance. |
Is there a significant cost difference between different powder types? | Yes, cost varies based on the material composition, availability, and application method. |
Can I apply corrosion resistance powder at home? | Application typically requires specialized equipment and expertise, so it’s usually done by professionals. |
What is the shelf life of corrosion resistance powder? | Most powders have a long shelf life if stored properly in a dry, cool environment. |
Conclusion
Corrosion resistance powders play a critical role in extending the life of metal components by providing a robust defense against the harsh effects of corrosion. By choosing the right type of powder, understanding its composition, and applying it correctly, you can protect your assets and ensure long-term durability.
Whether you’re working in aerospace, automotive, marine, or any other industry that requires metal protection, corrosion resistance powders offer a versatile and effective solution. The key is to select the right powder for your specific needs and to work with reputable suppliers to ensure you get the best product at the right price.
If you have any more questions, feel free to reach out, and don’t forget to explore the various powder types and their unique properties as you plan your next project.